連續澆鑄
連續澆鑄
同通常鋼錠澆鑄相比,具有增加金屬收得率,節約能源,提高鑄坯質量,改善勞動條件,便於實現機械化、自動化等優點。連鑄鎮靜鋼的鋼材綜合收得率比模鑄的約高10%。沸騰鋼連鑄比較困難,至今尚未成功。近年對沸騰鋼成分的鋼液進行真空“輕處理”,可以順利地進行連鑄。有色金屬的連鑄發展比鋼鐵連鑄為早。如在輥式連鑄機上,兼有凝固和塑性變形,則稱連續鑄軋。
由於連鑄簡化了鍊鋼鑄錠及軋鋼開坯加工工序,每噸鋼可節約能量(0.15~0.25)×106千卡,如進一步解決鑄坯和成材軋機的合理配合問題,熱送直接成材,還可進一步節約能源。
連鑄坯在結晶結構上的主要特點是:連鑄工藝使鋼水迅速而均勻地冷卻,因而迅速形成較厚微晶細粒的表面凝固層,沒有充分時間形成柱狀晶區;連鑄坯斷面較小,整罐鋼水的連鑄從開始到終了的冷卻凝固時間接近,連鑄坯縱向成分偏析差別可在10%以內,這是模鑄鋼錠無法與之比擬的;連鑄坯不像模鑄鋼錠那樣分單根澆鑄,所以可避免形成縮孔或空洞,使金屬收得率提高;在塑性加工中,為消除鑄態組織所需的壓縮比也可較小。
有色金屬(銅、鋁等)的連鑄在20世紀30年代已成功,至40年代,德國永漢斯(S.Junghans)、美國羅西 (I.Rossi)在連續鑄鋼方面取得工業規模的成功。到50年代,鋼水連鑄工藝比較成熟。由於對連鑄工藝的冶金理論認識加深、連鑄機設備結構和生產工藝不斷有所改進,使操作安全和鑄坯質量得到基本保證。連鑄機設備型式從半連續垂直式開始,經立彎連續式逐步降低了設備高度,到60年代成為現在通用的弧型連鑄機。1981年世界上51個國家裝有415台連鑄機,年產鋼13500萬噸,為當年鋼產量的20%;其中板坯機台數約為1/4,占連鑄坯產量的50%;主要產鋼國家連鑄坯產量占鋼產量約為38%。世界鋼產量和連鑄坯產量發展的趨勢見圖1。
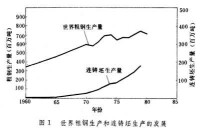
連續澆鑄
在大型連鑄機組上為快速調整鑄坯斷面的生產要求,通常將機組部件整體更換;從結晶器上口送入引錠桿,可減少通常從下口送進引錠桿的輔助作業時間;有的板坯鑄機將結晶器製成六段,可分別獨立交換改變斷面;在改變斷面時,只須停澆鋼水20秒鐘,便能繼續生產其他新斷面的產品。有些板坯機生產單一尺寸的寬板坯,然後縱切成所需寬度尺寸的窄坯。為了在一台連鑄機上增加品種和提高產量,發展出多流連鑄機。板坯機有的採用2~3流機組,方坯機可多至8~10流。
近年連鑄生產自動化技術迅速發展。在技術先進的鋼廠已經開始實現對鋼水成分、溫度、結晶器鋼液面、鑄速、二次水冷卻、鑄坯質量熱檢查、定尺切割等用計算機進行全面自動控制;生產過程中有質量不合格鑄坯時,實行自動切除;然後熱送連軋生產。中國於50年代開始進行半連鑄的工業試驗。1959和1960年間建成直立式方扁坯連鑄機。60年代中期建成弧形板坯連鑄機。同時還建有立彎式小方坯連鑄機。截至1981年,中國投產的連鑄機有26台,1981年生產連鑄坯254萬噸,佔全國鋼產量的7.65%。澆鑄的鋼種有普通碳鋼、低合金結構鋼、彈簧鋼、電工鋼等。連鑄坯的品種有120~200毫米方坯,700~2300毫米寬板坯。
連鑄機是從直立式裝置開始的。為了降低裝置的高度,擴大鑄坯品種和提高質量等目的,連鑄機發展出了多種結構形式。
立式連鑄機 全部設備直至切割器,都是垂直布置,切割后鋼坯放平運走(圖2)。
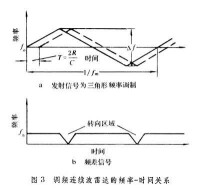
連續澆鑄
弧形連鑄機 通過結晶器使鑄坯表層凝固成形,隨即沿弧形曲線的二冷段向前移動,鑄坯凝固至一定程度后,再矯直成水平狀,切割后運出。這類連鑄機的二冷段有全弧形、橢圓形(多點橢圓軌跡)或帶二冷上部直線段。矯直段有鑄坯全凝固矯直方式或帶液相坯矯直方式。為了滿足高質量產品的要求,在結晶器或二冷上段外圍裝設低頻電磁攪拌裝置,以改善鑄坯結晶組織(圖3)。
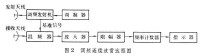
連續澆鑄
水平式連鑄機 鋼水由中間罐水口直接水平導入水冷結晶器,出結晶器后的鑄坯以時拉時停的間斷操作方式拉坯前進,以保證鑄坯表面質量不產生破裂(圖4)。
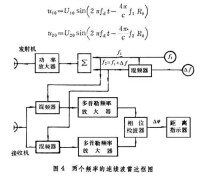
連續澆鑄
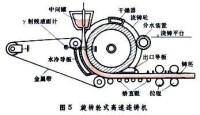
連續澆鑄
目前普遍使用的連鑄設備是弧形連鑄機。立式、立彎式、傾斜式三種型式是發展過程的產物,其中直立式仍在少數工廠使用,水平式、旋轉輪式、離心旋轉連鑄機尚處於試驗或小規模生產階段。
以通用的弧形連鑄機為例。
盛鋼桶和中間罐 盛鋼桶多用旋轉檯承托,便於調換盛鋼桶連續供鋼水。鋼水澆進結晶器之前先通過中間罐,調整鋼水靜壓力,保持鋼水流動平穩。中間罐可快速調換使用,以保證鋼流澆鑄不間斷並實現多爐連澆。在中間罐水口下設有事故溢流槽,使廢鋼流入垃圾罐。
結晶器 以純銅或銅合金材料作內壁,用鋼框架密封箍住。內壁和外框間留有冷卻水通路。結晶器內襯銅壁一般厚6~24毫米,長600~1100毫米,在結晶器旁側裝設槓桿機構的機械聯鎖振動機構,使結晶器沿弧形曲線上下振動。結晶器內壁的潤滑有兩種方法:對厚度150毫米以上鑄坯一般採用伸入式水口加保護渣粉澆鑄工藝,對小於150毫米鑄坯採用油潤滑。
二次冷卻裝置 結晶器出口至拉坯矯直機之間,沿弧形曲線以多組導輥作鑄坯前進的軌道,導輥中間穿插多組冷卻水噴嘴進行二次冷卻,加速鋼流凝固。
拉坯矯直機 在二冷區後段設有多支點拖輥,曳拉和矯直鑄坯前進。
切割裝置 用氧氣乙炔火焰或機械剪切割鑄坯,這項裝置和拉坯矯直機前進方向的速度應相互配合。
引錠桿 是許多金屬環節連接構成的可撓長桿。可與鑄坯一樣由拉坯矯直機夾持,沿導輥曲線移動。朝結晶器方向一端的引錠桿為凹形鎖頭,承接鋼水,牽拉鑄坯。
連續鑄鋼工藝 連鑄機必須與出鋼操作密切配合,鋼水開始澆入結晶器的同時,一面啟動結晶器振動,進行潤滑和開放冷卻水,一面啟動拉坯矯直機拖引錠桿運轉,鑄坯隨引錠桿拉曳前進,鑄坯過拉坯矯直機到一定位置后,脫卸並移開引錠桿,鑄坯本身由拉坯矯直機繼續拉曳。前進的鑄坯按定尺長度逐次切割(圖6),輸送、堆存,待全爐鋼水鑄完為止。在生產中應力爭多爐連鑄,以提高經濟效益。
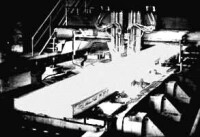
連續澆鑄
拉速控制 在保證鑄坯質量和安全生產的前提下,拉速主要受鑄坯凝固速度的制約。其關係式為:s=K堢。式中s為鋼凝固層厚度(毫米),s為凝固時間(分)。一定的s值應保證硬殼不破裂和安全生產,K值為23~32,視鋼種、斷面、鋼水溫度和拉速變化而定。拉速過快易發生漏鋼、斷接等;拉速慢則易發生鑄坯表面不光整、結疤等。高碳鋼和合金鋼的拉速應比低碳鋼慢。鑄坯斷面(厚度)大的拉速應比斷面小的慢。提高拉速須盡量保持低溫澆鑄,並對鋼液面採用60Co、紅外線或電磁檢測儀錶等控制手段。拉速範圍與鑄坯斷面品種有關,以普通碳鋼為例:板坯0.5~1.8米/分,大方坯0.6~1.5米/分,小方坯1.5~3.5米/分。
冷卻控制 連續鑄鋼的冷卻區集中在結晶器、二冷段和後部工序冷卻等三個部分。一般認為結晶器段占冷卻量的14~20%,二冷段佔23~30%。冷卻強度過大和拉速不適應時,會造成鑄坯內裂和外裂紋。冷卻強度過小和不均勻則易產生鑄坯鼓肚、漏鋼等現象。冷卻強度必須隨鋼種、鑄坯溫度和拉速快慢進行控制調節。每公斤鋼的冷卻水消耗量約1~2公斤。要求各斷面部位冷卻均勻,冷卻水要過濾凈化,使水質潔凈,導熱均勻。
提高連鑄機生產能力應降低鋼水澆鑄時的過熱溫度,提高拉速,擴大鑄坯斷面和採用多流連鑄。鑄坯斷面的選定和軋機軋製成材道次的綜合考慮也很重要。採用多爐連鑄可提高連鑄機作業率,但要力求澆鑄時間與冶鍊周期相互協調。
連鑄坯的缺陷 在澆鑄生產過程中,由於鋼水成分、溫度、澆鑄速度、冷卻水強度等控制不當,以及鑄機設備安裝不合規格等原因,可造成與模鑄相似的各種缺陷。與模鑄鋼錠的差別是裂紋缺陷比較多見。(見彩圖)。

連續澆鑄
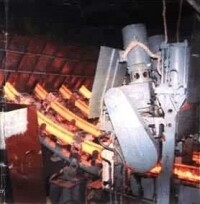
連續澆鑄
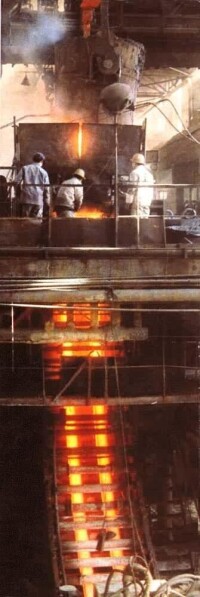
連續澆鑄
參考書目
魯捷斯等著,《連續鑄鋼原理》翻譯組譯:《連續鑄鋼原理》,上海人民出版社,上海,1977。