FMECA
用於找出單點故障的分析技術
FMECA是針對產品所有可能的故障,並根據對故障模式的分析,確定每種故障模式對產品工作的影響,找出單點故障,並按故障模式的嚴重度及其發生概率確定其危害性。所謂單點故障指的是引起產品故障的,且沒有冗餘或替代的工作程序作為補救的局部故障。FMECA包括故障模式及影響分析(FMEA)和危害性分析(CA)。
故障模式、影響和危害性分析(Failure Mode,Effects and Criticality Analysis,簡稱FMECA)是在工程實踐中總結出來的,以故障模式為基礎,以故障影響或後果為目標的分析技術。它通過逐一分析各組成部分的不同故障對系統工作的影響,全面識別設計中的薄弱環節和關鍵項目,並為評價和改進系統設計的可靠性提供基本信息。
實例
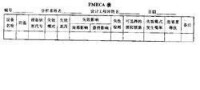
FMECA
1.明確分析對象
找出零部件所發生的故障與系統整體故障之間的因果關係是FMECA的工作思路,所以明確FMECA的分析對象,並針對其應有的功能,找出各部件可能存在的所有故障模式,是提高FMECA可靠性和有效性的前提條件。
2.時間性
FMEA、FMECA應與設計工作結合進行,在可靠性工程師的協助下,由產品的設計人員來完成,貫徹“誰設計、誰分析”的原則,並且分析人員必須有公正客觀的態度,包括客觀評價與自己有關的缺陷,理性分析缺陷的原因。同時FMEA必須與設計工作保持同步,尤其應在設計的早期階段就開始進行FMECA,這將有助於及時發現設計中的薄弱環節並為安排改進措施的先後順序提供依據。如果在產品已經設計完成並且已經投產以後再進行FMEA,其實對設計的指導意義不大。一旦分析出原因,就要迅速果斷地採取措施,使FMEA分析的成果落到實處,而不是流於形式。
3.層次性
進行FMECA時,合理的分析層次確定,特別是初始約定層次和最低約定層次能夠為分析提供明確的分析範圍和目標或程度。此外,初始約定層次的劃分直接影響到分析結果嚴酷度類別的確定。一般情況下,應按以下原則規定最低約定層次:。
(1)所有可獲得分析數據的產品中最低的產品層次;
(2)能導致災難的(I類)或致命的(II類)故障的產品所在的產品層次;
(3)定或預期需要維修的最低產品層次,這些產品可能導致臨界的(III類)或輕度的(IV類)故障。
4.FMECA團隊協作和經驗積累往往FMECA都採用個人形式進行分析的,但是單獨工作無法克服個人知識、思維缺陷或者缺乏客觀性。從相關領域選出具有代表性的個人,共同組成FMECA團隊。通過集體的智慧,達到相互啟發和信息共享,就能夠較完整和全面地進行FMECA分析,大大提高工作效率。
FMECA特彆強調程序化、文件化,並應對FMECA的結果進行跟蹤與分析,以驗證其正確性和改進措施的有效性,將好的經驗寫進企業的FMECA經驗反饋里,積少成多,形成一套完整的FMECA資料,使一次次FMECA改進的量變彙集成企業整體設計製造水平的質變,最終形成獨特的企業技術特色。
(1)掌握產品結構和功能的有關資料。
(2)掌握產品啟動、運行、操作、維修資料。
(3)掌握產品所處環境條件的資料。
(4)定義產品及其功能和最低工作要求。
(5)按照產品功能方框圖畫出其可靠性方框圖。
(6)根據所需要的結構和現有資料的多少來確定分析級別,即規定分析到的層次。
(7)找出故障模式,分析其原因及影響。
(8)找出故障的檢測方法。
(9)找出設計時可能的預防措施,以防止特別不希望發生的事件。
(10)確定各種故障模式對產品產生危害的嚴酷程度。
(11)確定各種故障模式的發生概率等級。
(12)填寫FMEA表,並繪製危害性矩陣,如果需要進行定量FMECA,則需填寫CA表。