摩擦材料
摩擦材料
摩擦材料:用粉末冶金方法製成的、具有高摩擦係數和高耐磨性能的金屬和非金屬複合材料。主要用於製造各種制動和傳動機件。
目錄
1930年美國韋爾曼 (S.K.Wellman)研製出油中使用的(濕式)銅基粉末冶金摩擦材料,並應用於工業生產。50年代出現了用於干摩擦的鐵基粉末冶金摩擦材料。同原來使用的金屬摩擦材料相比,這種材料的摩擦表面可承受的溫度由500~600℃提高到1000℃以上。中國粉末冶金摩擦材料的研究始於60年代,現已生產出十多種銅基和鐵基粉末冶金摩擦材料。
同非粉末冶金製作的摩擦材料(例如鑄鐵和鑄鋼,樹脂粘合石棉以及樹脂粘合的“金屬-非金屬”粉末混合料等)相比,粉末冶金摩擦材料的優點是:能很快吸收動能,制動、傳動速度快,磨損小;強度高,耐高溫高壓,導熱性好,即使在高溫高壓下也能保持較穩定的摩擦係數;不易與對摩材料發生咬合,耐腐蝕,摩擦係數受油脂、潮濕的影響小;雜訊低,壽命長等。現代機械向高速高負荷發展,對摩擦材料的綜合性能要求越來越高,因此粉末冶金摩擦材料日益重要。
材料構成 主要由基體金屬、潤滑組元、摩擦組元三部分構成。其結構特點是:具有特殊性能的各種微粒均勻地分佈在連續的金屬基體中,後者發揮導熱作用並承受機械應力,前者保證摩擦性能。各個組元所用材料大致如下:
基體金屬 銅基材料通常是加錫、鉛、鋅組成合金,導熱性好,耐腐蝕,耐摩擦性好,主要用於“濕式”離合器。鐵基材料有更高的摩擦係數和耐熱性,多用於乾式重負荷的制動器。
潤滑組元 通常是採用石墨和鉛,有時也選用硫化鉬、硫化銅、硫化鋇或氮化硼等固體潤滑劑。低熔點的鉛、錫等在高溫下會局部熔化,可以吸收摩擦熱並在摩擦面上形成一層薄膜,防止粘結、咬合和擦傷。
製造工藝 為了能承受或傳遞巨大的壓力或動能,摩擦材料大都燒結在鋼板上。製造工藝主要為製備粉末、配料、混合、壓製成形(見粉末冶金成形)和燒結。壓制通常有兩種形式:一種是先將混合均勻的粉末壓製成形,再加壓燒結在鋼板上;一種是將混合均勻的粉末直接壓制在鋼板上進行加壓燒結。燒結一方面是增加粉末層內部顆粒間的結合強度,另一方面藉助於高溫和壓力的作用,使粉末層和鋼板牢固地結合在一起。燒結一般在可以對樣品加壓的“鐘罩式”燒結爐內,在中性或還原性氣氛中進行。也有採用噴塗法和粉末軋製法製造摩擦片的。各種方法各有短長,要根據使用的要求選擇合適的材質和工藝。一般銅基和鐵基摩擦材料的主要性能見上表。
參考書目
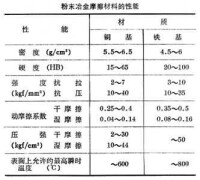
摩擦材料
松山芳冶等:《粉末セ金応用製品(Ⅲ)構成部品》,日刊工業新聞社,東京,1964。