鑄造焦
化鐵爐熔鐵的主要燃料
鑄造焦是化鐵爐熔鐵專用焦炭。是冶金焦的一種。因所熔鐵水供鑄造鐵件而得名。
因此,鑄造焦應具備塊度大、反應性低、氣孔率小、具有足夠的抗衝擊破碎強度、灰分和硫分低等特點。
鑄造焦是化鐵爐熔鐵的主要燃料。其作用是熔化爐料並使鐵水過熱,支撐料柱保持其良好的透氣性。
美國、英國等工業發達國家於20世紀初就開始進行鑄造焦的生產。
在中國,到1990年年底已形成年產近百萬噸鑄造焦的設備生產能力,而且在配料技術、鑄造焦質量、微觀結構的研究和鑄造型焦的研製方面都取得了進展。
鑄造焦是化鐵爐熔鐵的主要燃料。其作用是:
熔化爐料並使鐵水過熱,支撐料柱保證其良好的透氣性。因此,鑄造焦應具備塊度大、反應性低和氣孔率小的特點。
鑄造焦與高爐焦相比在外觀上具有塊度大裂紋少、密實程度高等特點。裝入化鐵爐內的鑄造焦分為底焦和層焦兩部分。
底焦的作用是燃燒產生熱量,熔化金屬並在鐵水通過它時使鐵水過熱。由於這部分焦炭處於化鐵爐的底部,它要承受整個料柱的靜壓力和加料時大塊鐵料的衝擊力,因此應具有一定的抗碎強度。
層焦由上部與金屬料層層相間加入爐內,用於補充底焦的消耗,每層加入量即為熔化一層鐵料所消耗的底焦量。
化鐵爐要求鑄造焦具有下列性質:
(1)塊度大而均勻。為了保證化鐵爐內料柱的良好透氣性能,使風能吹透中心,一般要求焦炭塊度在60mm以上。
鑄造焦塊度與化鐵爐內徑有關,生產能力大於10t/h的化鐵爐,要求鑄造焦塊度為化鐵爐內徑的1/10~1/12;中小型化鐵爐則要求焦炭塊度為其內徑的1/6~1/9。
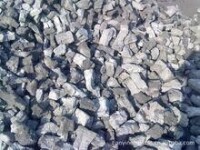
鑄造焦
(4)硫分低。鑄造焦硫含量約有30~70%進入熔化的鐵水,特別是爐料中廢鋼用量增加時,鐵水增硫更多,直接影響鑄件質量。化鐵爐一般用酸性爐襯,不能脫硫,因此要求焦炭含硫量低於0.8%。
(5)水分適宜且穩定。水分蒸發需要消耗熱量; 但水分過低,焦炭裝入化鐵爐時容易著火。為防止化鐵爐頂部著火,鑄造焦又須有一定量的水分並保持穩定。水分波動會使料批計量不準,影響化鐵爐操作。一般入爐焦水分控制在5%以下。
(6)揮發分不宜太高。揮發分高會影響鑄造焦使用時的強度,同時也會降低焦炭的固定碳含量。各國都訂有鑄造焦質量標準。塊度、灰分、硫分和機械強度指標是鑄造焦質量考核指標。若上述指標中任一項達不到規定的數值,即不符合該級別的合格品質量標準。轉鼓強度和落下強度為並用指標,當兩個指標值有矛盾時,以M見米庫姆轉鼓試驗)為準。水分、揮發分、顯氣孔率和碎焦率等則不作為主要質量驗收指標。
中國鑄造焦國家標準 | |||
---|---|---|---|
指 標 | 級 別 | ||
特級 | 一級 | 二級 | |
塊 度,mm | >80 80~60 >60 | ||
水分Mad,% | ≤5.0 | ||
灰分Ad,% | ≤8.00 | 8.01~10.00 | 10.01~12.00 |
揮發分Vdaf,% | ≤1.5 | ||
硫分St。d,% | ≤0.60 | ≤0.80 | ≤0.80 |
轉鼓強度M40,% | ≥85.0 | ≥81.0 | ≥77.0 |
落下強度SI504% | ≥92.0 | ≥88.0 | ≥84.0 |
顯氣孔率Ps,% | ≤40.0 | ≤45.0 | ≤45.0 |
碎焦率(<40mm), % | ≤4.0 |
一些國家的鑄造焦質量標準 | |||||||||
---|---|---|---|---|---|---|---|---|---|
國 家 | 灰分 % | 硫分 % | 揮發分 % | 轉鼓強度,% | 落下強度 % | 視密度 g/cm3 | 氣孔率 % | 塊 度 mm | |
M80 | M40 | ||||||||
美 國 | <7.0 | <0.6 | <1.0 | >95 | 0.85~1.1 | 45~50 | 76~230 | ||
英 國 | <7.0 | <0.7 | <1.0 | >80 | >90 | 0.95~1.4 | 45~50 | 76~150 | |
法 國 | 9~10 | <0.7 | <1.0 | 65~70 | 0.9~1.1 | 45~52 | 60~90 90~152 | ||
日 本 | 6~14 | <0.8 | <2.0 | 70.1~90.1 | >100 100~75 75~50 50~35 | ||||
德 國 | 7.5~8.5 | 0.8~0.95 | 60~75 | >100 >80 80~120 | |||||
蘇 聯 | 9.5~12.5 | 0.45~1.4 | <1.2 | 73~80 | 42 | >80、 >60 >40、 40~60 60~80 |
生產鑄造焦的最理想的原料是低灰、低硫、中等揮發分、中強粘結性焦煤。
當優質焦煤不足時,也可以以中、高揮發分和中、強粘結性煤為基礎煤,配入中、低揮發分或中、低粘結性煤以及石油延遲焦、焦粉或瀝青等配煤添加劑。
配入焦粉和石油延遲焦等惰性添加物,可減緩半焦生成后的收縮應力,減少裂紋的生成並改善氣孔結構,增大塊度。配入瀝青等添加物,可以補充配料中粘結組分的不足,並對煤料產生一定的改質作用。
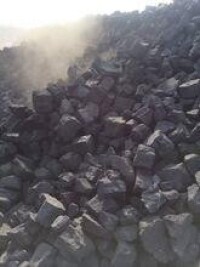
鑄造焦
石油延遲焦與煤的熔融組分結合良好,所得焦炭氣孔小,孔壁加厚。用低灰、低硫的高揮發分弱粘結性煤為主體配料時,通過選擇合適的配合煤種和添加物,並採用煤搗固工藝,也能生產出質量合乎要求的鑄造焦。為降低鑄造焦的灰分,根據原料煤的灰分及其可選性,在煤料預處理過程中常常設置適當的洗選工序。
在煤料粉碎方面可採用先粉碎后配合工藝或分組粉碎工藝,使裝爐煤中煤料的細度(指小於3mm的粒級)達到85~90%,石油延遲焦粉的細度達到90~96%,配加的焦粉則要求小於0. 5mm的粒級佔90%以上。為增大焦炭塊度,宜採用寬炭化室焦爐煉製,在煉焦工藝上,採用降低爐溫延長結焦時間,以延緩成焦過程中氣體析出速度,降低半焦收縮應力,減少焦炭裂紋。
國內外生產鑄造焦多數採用的是生產冶金焦的室式煉焦爐,為了生產出合格的鑄造焦,在生產中一般採取以下4種方式。
在配煤中加入瀝青和石油延遲焦
這樣生產的鑄造焦的常規分析可達到特級指標,但它的反應后強度極差,致使其價格降低。
從冶金焦中挑選大塊焦作為鑄造焦
大塊焦相對地講裂紋較多,受機械力的作用,首先沿裂紋碎裂,所以大塊焦是穩定性最差的焦炭。在冶金焦生產中,為了使焦炭強度提高,國內外一些企業都採取了穩定化(國內稱整粒)處理的設施。
以化產回收焦爐批量生產鑄造焦
一些化產回收焦爐憑藉資源優勢,可生產鑄造焦,但一般溫度要降至1100℃,這一溫度條件下不利於保護爐體,而且產量約減30%以上,所以這類廠只能生產有限的鑄造焦。
使用熱回收焦爐生產鑄造焦
最早用於鑄造焦生產的是20世紀80年代的東聚焦化廠採用的“七五”爐,該爐型是熱回收焦爐萌芽期的爐型,而鎮江焦化廠是我國最早開始採用化產回收焦爐生產鑄造焦的廠家之一。
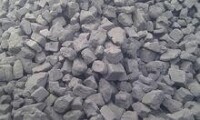
鑄造焦
1981年國家計委和冶金部要求鞍山熱能所協同鎮江焦化廠利用該廠生產石油焦的有利條件,儘快試製一級鑄造焦。經過共同努力,以肥煤、焦煤5 %、配以45 %的延遲焦、石油焦和瀝青, 並對原有的61 型和“型焦爐,通過降低爐溫和延長炭化時間的辦法,成功地研製出一級鑄造焦。後來通過“六五”科技攻關,對原料配比略加調整后,又試製成功特級鑄造焦。
十多年來, 我國的鑄造焦生產技術已有生產鑄造焦的鎮江、山西和寧夏要組了很大發展,對幾種主要生產流程基本掌握,但不足之處是,低運費原則適當分工合理定向供應,以低價年生產量尚不足30 萬t ,而且大多是由爐孔較窄的小型焦爐和改良型焦爐生產的,供國其它有條件的企業亦要適當生產部分鑄內自用的尚不足1/3,大多為生產出口鑄件和造焦以就地供應。