表面淬火
給鋼件表面快速加熱的工藝
目的 表面淬火的目的在於獲得高硬度,高耐磨性的表面,而心部仍然保持原有的良好韌性,常用於機床主軸,齒輪,發動機的曲軸等。
表面淬火是將鋼件的表面層淬透到一定的深度,而心部分仍保持未淬火狀態的一種局部淬火的方法。表面淬火時通過快速加熱,使鋼件表面很快到淬火的溫度,在熱量來不及穿到工件心部就立即冷卻,實現局部淬火。
表面淬火的目的在於獲得高硬度,高耐磨性的表面,而心部仍然保持原有的良好韌性,常用於機床主軸,齒輪,發動機的曲軸等。
表面淬火採用的快速加熱方法有多種,如電感應,火焰,電接觸,激光等,目前應用最廣的是電感應加熱法。
感應加熱表面淬火就是在一個感應線圈中通以一定頻率的交流電(有高頻,中頻。工頻三種),是感應圈周圍產生頻率相同的交變磁場,置於磁場之中的工件就會產生與感應線圈頻率相同,方向相反的感應電流,這個電流叫渦流。由於集膚效應,渦流主要集中在工件的表層。由渦流所產生的電阻熱使工件表層被迅速加熱到淬火溫度,隨即向工件噴水,將工件表層淬硬。
感應電流的頻率愈高,集膚效應也愈強烈,故高頻感應加熱用途最廣。高頻感應加熱常用頻率是200~300kHz,其加熱速度極快,通常只有幾秒鐘,淬硬層深度一般為0.5~2mm。主要用於要求淬硬層較薄的中,小型零件,如齒輪,軸等。
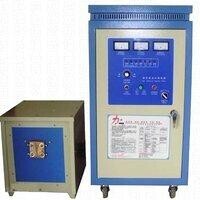
表面淬火
目前國內以IGBT發展勢頭較為強勁,尤其是以二代IGBT感應電源,三代IGBT感應電源為主導,頻率範圍覆蓋了中頻,超音頻,和高頻,最高頻率可達200KHz。IGBT以其性能穩定著稱。
表面淬火對於工件來說是至關重要的,是提高工件硬度及耐磨性的關鍵,因此,選擇合適的設備是很有必要的。
將工件表層快速加熱,在熱量尚未及時大量傳到內部的情況下,使表層達到淬火溫度,迅即淬冷,獲得預定淬火組織的淬火工藝。鋼的表面淬火多用於要求耐磨、抗扭轉、抗彎曲疲勞和接觸疲勞的零部件。鋼件表面淬火前一般經正火或調質處理。
加熱用的能源通常有電磁感應加熱,火焰加熱,電接觸加熱及在電解液中加熱;並可採用更高密度的能源,如電子束、激光、電弧等。能源提供的能量密度越高,則表面加熱和淬硬層越薄。
電磁感應加熱表面淬火
鐵磁性物質的工件處在交變磁場中時,會因感應而在內部產生電流。這種電流在微小區域內形成迴路,稱之為渦流。渦流電流強度與交變磁場磁通變化率和工件材質有關。渦流在工件中僅集中在表層,有所謂“集膚效應”。表面電流最大,向內逐漸降低。電流值保持表面電流I0的1/e以上的厚度稱為“電流透入深度”(e為自然對數的底)。鋼鐵材料在居里溫度(磁性轉變溫度,中碳鋼約為724℃)以上由於導磁率的突然變化,電流透入深度(△)急劇增大。當被加熱材料與感應器條件相同時,△值取決於感應器中交變電流的頻率(f),對於鋼鐵材料,△≌500/(mm)。因此要根據淬火層厚度的要求選擇電流頻率。常用的感加熱交流流電源有3種:(1)高頻。200~300kHz,採用電子管式高頻振蕩電源,淬硬層厚度一般為1~3mm。(2)中頻。500~800Hz,採用中頻發電機或可控硅變頻裝置電源,淬硬層厚度一般為6~8mm。(3)工頻。一般工業頻率50Hz,採用加熱變壓器電源,由工業電網供電,淬硬層厚度一般為10~20mm,其電流透入深度則可達50~70mm,適於大件的表面淬火。
如圖1所示,電磁感應加熱表面淬火通常是將工件置於一加熱感應圈內,感應圈通入交變電流以形成交變磁場。感應圈多用銅管製成,可以是單圈或多圈的,管內通入冷卻水防止工作時升溫。加熱和噴冷淬火可採用連續和斷續兩種方式,皆可在圖1機構上實現。噴水圈設在加熱器的下方,在連續式加熱-噴冷時,工件在自旋轉(使加熱均勻)的同時向下移動,表面各部位依次加熱和淬冷;在斷續式加熱-噴冷時,工件自旋轉時位置不變,待一定面積被加熱到淬火溫度時,迅速下降並噴水冷卻。
表面淬火時的加熱溫度取決於鋼的成分(臨界點)、原始組織和加熱速度。加熱速度一般在50~500℃/s之間,屬快速加熱。由於鋼在快速加熱時奧氏體形成的動力學的特點,在加熱速度、加熱溫度、鋼的原始組織和淬火后組織、性能幾方面之間具有如圖2所示的關係。Ⅱ區為最佳規範,既具有細晶粒,又具有高硬度。Ⅰ區加熱不足,晶粒雖細小,但加熱時奧氏體形成不充分,淬火硬度不足。因為加熱過度,晶粒長大,硬度也因殘留奧氏體較多而略有下降。
火焰加熱表面淬火
將工件置於氧-乙炔(也可用天然氣等)火焰中,表面快速加熱至淬火溫度后噴水淬冷。火焰溫度一般為3000℃左右。本法設備簡單,常用於小批、單件生產或零部件的維修。其他其他備包括:(1)噴嘴。氧-乙炔按一定比例混合,在相當高的壓力下從噴嘴小孔噴出並被點燃。噴嘴的布置,一般按工件表面製成方形狀。(2)淬火機床。固定工件和噴嘴位置,並可控制工件(或噴嘴)的旋轉和移動。(3)燃燒控制裝置。保證氧-乙炔氣有穩定的混合比和噴出的壓力。
電接觸加熱表面淬火
利用觸頭(銅或石墨材質)和工件的接觸電阻,低電壓、大電流,使觸點溫度迅速上升。將觸點以一定速度移過工件表面,即可將表層加熱至淬火溫度,並在工件自身的冷卻下淬硬。本法簡易可行,適於大件的局部表面淬火。
電解液加熱表面淬火
以工件作陰極,置於電解液中(常用5%~20%碳酸鈉水溶液),以電解槽為陽極,通入200~300V直流電。由於電解作用使陰極(工件)表面形成一層氫氣膜。氫氣膜具有大的電阻,溫度迅速升高,並將工件表面加熱到淬火溫度。停電后電解液將工件淬冷。本法適用於大批量生產工件的局部表面淬火。
各種表面淬火均採用快速加熱,基本上無保溫階段,表面到達預定溫度即噴冷。因而奧氏體形成時過熱度大,初生晶粒細,奧氏體成分不均勻。如果加熱和噴冷參數合適,則可在此種細晶狀態下淬冷,這是正確的表面淬火可以做到的;但如果加熱時間過長,溫升過高,則表層將處於過熱狀態。以上是表面淬火層與一般淬火組織性能差異的來源。
冷冷水冷水前,溫度由表面向心部逐漸降低,大致可分為三區,即高於Ac3區,Ac1~Ac3區和低於Ac1區。淬火后組織分別為:1—細針狀馬氏體(M),2—馬氏體加鐵素體(M+F),3—原始組織(珠光體加鐵素體(P+F)。45鋼高頻淬火后的組織和硬度沿縱深方向的分佈如圖3所示。靠近表面的1區,為細晶馬氏體區;在過渡的2區中,馬氏體量由外向內急劇減少,並可出現少量珠光體;在2~3區的交界處,未轉變的珠光體量急劇增加,過渡到原始組織。
高頻感應表面淬火的表層(細馬氏體區)硬度比一般淬火高出2~4HRC,這一強化作用是相當顯著的。除上述組織因素外,薄層噴冷冷卻效率高及淬火后表層的殘餘壓應力也是導致硬度增高的重要因素。表層殘餘壓應力的存在還可大幅度提高零部件的抗疲勞強度。