共找到2條詞條名為複合模的結果 展開
- 複合模
- 多頭沖模
複合模
複合模
複合模是指沖床在一次行程中,完成落料、沖孔等多個工序的一種模具結構。
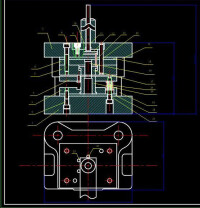
②成形類複合模如彎曲複合模、複合擠壓模等;
③沖裁與成形複合模如落料、拉深複合模;沖孔、翻邊複合模;拉深、切邊複合模;落料、拉深、沖孔、翻邊複合模等。
①生產批量複合模可以成倍地提高生產效率,生產批量越大,提高生產效率就越顯得重要。
②衝壓工件精度當衝壓工件的尺寸精度或同軸度、對稱度等位置精度要求較高時,應考慮採用複合模。
③複合工序的數量一般複合模的複合工序數量在四工序以下,更多的工序將導致模具結構過於複雜,同時模具的強度、剛度、可靠性也將隨之下降,製造和維修更加困難。
④模具結構的大小複合模的大小不同,其採用的結構和板塊會有繁簡的差異,而且脫料裝置也不一樣。
(1)複合模中必定有一個(或幾個)凸凹模,凸凹模是複合模的核心零件。沖件精度比單工序模衝出的精度高,一般沖裁件精度可達到IT10~IT11。
(2)複合模衝出的製件均由模具型口中推出,製件比較平整。
(3)複合模的沖件比較複雜,各種機構都圍繞模具工作部位設置,所以其閉合高度往往偏高,在設計時尤其要注意。
(4)複合模的成本偏高,製造周期長,一般適合生產較大批量的衝壓件。
(5)設計複合模時要確保凸凹模的自身強度,尤其要注意凸凹模的最小壁厚。為了增加凸凹模的強度和減少孔內廢料的脹力,可以採用對凸凹模有效刃口以下增加壁厚和將廢料反向頂出的辦法,如圖《增加凸凹模強度的方法》所示。
(6)複合模的推件裝置形式多種,在設計時應注意打板及推塊活動量要足夠,而且兩者的活動量應當一致,模具在開啟狀態推塊應露出凹模0.2~0.5mm。
(7)複合模中適用的模柄有多種形式,壓人式、旋入式、凸緣式、浮動式等均可選用,應保證模柄裝入模座后配合良好,有足夠穩定性,不能因為設置退料機構而降低模柄強度,或過大增大模具閉合高度。
相對其他冷衝壓模具結構而言,它具有以下一些優點:①工件同軸度較好,表面平直,尺寸精度較高;②生產效率高,且不受條料外形尺寸的精度限制,有時廢角料也可用以再生產。
它的缺點是:模具零部件加工製造比較困難,成本較高,並且凸凹模容易受到最小壁厚的限制,而使得一些內孔間距、內孔與邊緣間距較小的下件不宜採用。
由於複合模本身所具有的一些優點較明顯,故模具企業在條件允許的情況下,一般傾向於選擇複合模結構。
複合模結構由於其生產效率高,工件尺寸精度好受到客戶的歡迎;但同時也由於其凸凹模受到沖裁條件的限制而使得通常的加工工藝方法不盡如意。於是出現了一種新型的加工方法——腐蝕工藝,加工出來的棋具零部件完全符合技術要求。
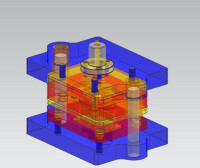
下料--車削(台階)--劃線--預打鋁絲孔--熱處理--精車--電加工(外形及內孔)--腐蝕(漏料孔)--清洗。
複合模零部件採取腐蝕工藝后,加工出的漏料孔壁光滑,尺寸一致,且最大限度地保證了刃口的強度。
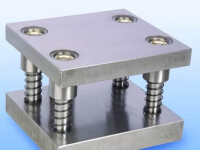
印痕(如殼飾)和殼內表印痕(如肌痕)的複合模。雙殼類、腕足類化石中常見有複合模。
①為節約用料可採用調頭沖的方式,此時兩支內導柱可只裝在同一側。
②沖凸位時,模具需要下死,可以在上夾板設計鑲件或在下墊板與外脫板之間做限位。內脫料力與外脫料力要大,且外脫板要高出凸模板用來壓料。切邊沖,大凸包沖需固定在夾板,凸包附近的沖孔沖頭要設計短一些,以保證材料拉動延展后再完成沖孔動作。
③設計對稱產品的複合落料模時,可在多餘邊料處預先設計后工序起防反作用的定位孔。
④為防止模具裝配反,導致衝壓時模具爆裂,導柱需設計防呆方式。