熱裂
熱裂
熱裂,石油煉製過程之一,是在熱的作用下(不用催化劑)使重質油發生裂化反應,轉變為裂化氣(煉廠氣的一種)、汽油、柴油的過程。
目錄
熱裂化原料通常為原油蒸餾過程得到的重質餾分油或渣油,或其他石油煉製過程副產的重質油。
沿革 1912年熱裂化已被證實具有工業化價值。1913年,美國印第安納標準油公司將W.M.伯頓熱裂化法實現工業化。1920~1940年,隨著高壓縮比汽車發動機的發展,高辛烷值汽油用量激增,熱裂化過程得到較大發展。第二次世界大戰期間及戰後,熱裂化為催化裂化所取代,雙爐熱裂化大都改造為重質渣油的減粘熱裂化。
化學反應 熱裂化反應很複雜。每當重質油加熱到450℃以上時,其大分子分裂為小分子。同時,還有少量疊合(見烯烴疊合)、縮合發生,使一部分分子轉變為較大的分子,熱裂化是按自由基反應機理進行的。在400~600℃,大分子烷烴分裂為小分子的烷烴和烯烴;環烷烴分裂為小分子或脫氫轉化成芳烴,其側鏈較易斷裂;芳烴的環很難分裂,主要發生側鏈斷裂。熱裂化氣體的特點是甲烷、乙烷-乙烯組分較多;而催化裂化氣體中丙烷-丙烯組分、丁烷-丁烯組分較多。
工藝過程 工業裝置類型主要有雙爐熱裂化和減粘熱裂化兩種。前者的原料轉化率(輕質油收率)較高,大於45%,目的是從各種重質油製取汽油、柴油;後者的轉化率較低(20%~25%),目的是降低減壓渣油的粘度和凝點,以提高燃料油質量,雙爐熱裂化汽油的辛烷值和安定性不如催化裂化汽油,目前已不發展;減粘熱裂化在石油煉廠中仍有較廣泛的應用。
雙爐熱裂化 所謂雙爐,是指在流程中設置兩台爐子以分別加熱反應塔的輕重進料(圖1),
操作時原料油直接進入分餾塔下部,與塔進料油氣換熱蒸出原料中所含少量輕質油和反應產物中的汽油、柴油后,在塔中部抽出輕循環油。塔底為重循環油。兩者分別送往輕油、重油加熱爐(為避免在爐管中結焦,故將輕、重循環油分別在兩爐中加熱到不同溫度),然後進入反應塔進行熱裂化反應。反應溫度為485~500℃,壓力1.8~2.0MPa;反應產物經閃蒸塔分出裂化渣油后,進入分餾塔分餾。汽油和柴油總產率約為60%~65%。所得柴油凝點-20℃以至-30℃、十六烷值(見柴油)約60(比催化裂化柴油高約20個單位);汽油辛烷值較低(馬達法辛烷值約55~60)且安定性差,熱裂化渣油是生產針狀焦(見石油焦)的良好原料。雙爐熱裂化的能耗約1900MJ/t原料(為催化裂化的65%~70%)。
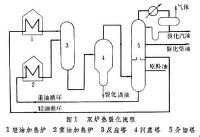
熱裂化