設備故障停機率
設備故障停機率
設備故障停機率是指設備故障停機時間與設備開動時間的比例,是考核設備技術狀態、故障強度、維修質量和效率的一個指標。
它是指設備故障停機時間與設備開動時間的比例。
故障停機率=故障停機台時/[故障停機台時+設備實際開動台時(設備應開動總台時)]×100%
公式是指故障停機時間與設備應開動時間的比,是考核設備技術狀態、故障強度、維修質量和效率一個指標。式中設備故障停機台時是指設備自發生故障損壞時起,至修復后重新投入生產上的實際時間。設備開動總台時=故障停機台時+實際開動台時。在其它條件不變的前提下,故障停機率越小,說明設備的可維修性能越好。
GZL=(Σ設備實際開動時間+Σ設備故障停機時間)×100%
(1)統計公式保持不變。注意子項和母項的計算公式。一個單位設備故障停機率過高均應引起關注,分析是否合理。但倘若一個單位故障停機率長期為零,可能未認真統計。
(2)一般要求綜合故障停機率GZL≤1%。
(3)設備故障停機率+設備有效利用率=100%。
設備故障停機率是設備運行好壞的主要指標,設備管理的其餘指標都是圍繞著該項指標的開展而確定的。如設備運行成本、TPM、PM的完成率等。設備故障停機率怎樣統計才能真實地反映設備運行的實際情況就成了一個重要話題。
(1)傳統設備故障停機時間的計算方法
設備故障率的高低與設備故障停機時間的定義、統計方法有著直接的關係,傳統的設備故障停機率是以平均故障率或最大故障率兩種方式來反映的。
方法一:平均故障率是將生產線所有設備故障率的平均值作為該生產線的故障率,即將生產線所有設備的故障時間累加作為分子,將每台設備計劃開動的時間累加作為分母,兩者所得的商則作為生產線的平均設備故障停機率。平均故障率計算公式如下:
生產線故障停機率=Σ每台設備故障停機時間/Σ每台設備計劃開動時間
方法二:最大故障率是將生產線停線時間最長的那台設備的故障率作為該生產線的故障率。最大故障率計算公式如下:
生產線故障停機率=MAX單台設備最大故障停機率
上述兩種方法都有一定的局限性,不能真實反映生產線的實際運行狀況:平均故障率掩蓋了很多有用的信息,如掩蓋了生產線上個別設備高故障率的現象,儘管平均故障率很低,但不能說明該生產線的開動效率一定高。
最大故障率確實能夠反映高故障率設備對整個生產線的影響,但忽視了低故障率設備對生產線的影響,最大故障率統計方法較平均故障率統計方法在反映故障率對設備開動率的影響方面有了改進,但如果低故障率的設備較多,該種故障率統計方法的缺陷也是明顯的。另外,在傳統採集做法中,故障數據都是由各維修班組進行統計,再由設備管理人員統一匯總,生成各類數據報表。環節多,周期長,易出錯,不利於對現場和客戶的快速響應。
(2)設備故障停機時間統計方法的改進
根據公司的要求,提出了以客戶為導向的“故障時間累加不重複”的科學統計方法,即以生產線為對象,以對象的最終影響為故障時間統計原則。所謂“故障時間累加不重複”是指將生產線作為一個整體,按故障對整個生產線的全局性影響的全部結果統計停機時間,且對產生同一影響的多個同步故障不重複統計。
①若每道工序都是由一台設備組成,則單台設備故障停機,視同整條線故障停線,不同時間段多台設備故障,停機時間要進行累加。但在同一時間多台設備故障時,故障停機時間只統計效率損失最大的一台設備故障停機時間,不再重複統計計算。另外,多台設備交叉重疊發生故障,在設備故障停機時間時需要減去重疊的設備故障時間。
②若同工序有多台設備組成,則某一台設備的故障停機對整條生產線的影響也會隨著設備數量的增加而相應地減少。如生產線某工序有2台設備,設備加工內容相同,若其中一台設備發生故障停機,該設備故障停機對整條生產線的影響為工序生產能力降低了一半,由產能折損折算到停機時間,則整線故障停機時間應該是單機故障停機時間的一半。
設備故障停機時間的定義和統計原則確定后,如何快速而準確地進行統計也是一個重要環節。
(1)利用EXCEL常用軟體,設置統計方法和計算公式
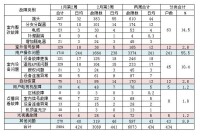
表1 每日故障時間統計表
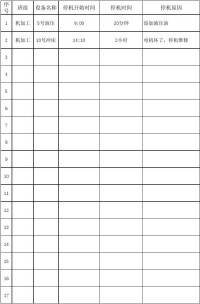
表2 單台設備和整條線故障停機時間
(2)故障統計操作流程
填寫表1(每日故障時間統計表)、自動生成表2(單台設備和整條線故障停機時間),方便算出當月整線設備故障率和單台故障率。
隨著科學技術的飛速發展,現代工業企業生產過程的機械化、自動化程度日益增高,結構日趨複雜,技術日益先進。設備在企業總投資中占的比重越來越大。可以說,一個企業生產能力的大小,取決於其擁有生產設備的品種、素質和擁有量;產品質量的好壞,一定程度上取決於裝備技術水平之高低;生產經營目標能否實現,取決於設備的能力、利用程度以及設備的管理水平。對於機械設備來說,在開動時間一定的前提下,發生故障停機時間越短,故障率就越小,設備的生產運行性能就越好。因此設備故障停機率是許多企業設備管理的重要考核指標。
通過以往的故障記錄,發現生產過程中設備故障停機時間長主要是由設備故障次數多以及故障修理時間長引起。導致設備故障次數多是因為大量的故障未能在檢修中被發現,而集中暴露在生產過程中,造成生產過程中頻繁停機;同時經過長期現場跟蹤,發現維修時間長並非由於維修工人技術水平不高,而是維修所需的備配件不足,在維修過程中加工、製造零件佔用了大量的時間,直接導致生產線長時間停機甚至停產。
國內很多企業都廣泛推行全員生產維護活動(TPM),但根據反饋,普遍認為TPM的理念確實好,就是大多落不到實處。維修人員和操作人員分屬不同車間,操作人員只關心使用設備,完成生產任務以及簡單的清潔保養工作。雖然他們能夠在第一時間感知設備運行狀態的好壞,但對設備的機構、原理卻缺乏了解,也不參與點檢工作。而維修人員對設備的使用狀態沒有切身體會,常規的例行檢查也就缺乏針對性。操作人員和維修人員各管一頭的局面在很大程度上導致了預防性維修工作的缺失。
對於點檢未能發現或者一些無法預防的突發故障,只能通過搶修來解決。在搶修過程中,除去必要的故障原因分析,以及維修過程實施外,經常由於備件的準備不足或者管理不善而耽誤時間。造成備件不能及時提供的主要原因有以下幾個方面:
(1)整條生產線設備流程長,安裝位置分散,所用零部件規格型號多,備件管理中部分帳物不符或不夠詳細,存放地點較混亂,尋找起來費時費力。
(2)大量備品配件都是進口的美製、美標零件,通用性不強,臨時緊急採購或定製周期長。比如:造型機各大型油缸所用的美標密封件,規格多、尺寸差異大,一旦損壞就需聯繫密封件廠家臨時測繪趕製,維修時間無法保證。
(3)備件質量達不到要求。考慮到維修成本,生產線所用的標準件儘可能使用國產件替代,有時會因為質量達不到要求,造成維修工作量增加或重複故障。
(4)機加工能力不足影響備件製作。備件中有許多零件需要根據磨損狀況測繪加工的,由於機加工工作量大,經常重視搶修急需的零件,而忽視了備件的加工準備。
為了使點檢工作不流於形式,使點檢工作取得應有效果,將點檢與定期維修相結合,從以下幾方面加強:
(1)制定嚴格的設備點檢規範。生產線由多台設備組成,而設備由很多零部件組成,但有的零部件不容易損壞,有的則容易損壞,有的零部件即便損壞也不影響設備開動。因此,對流水線故障進行統計分析,找出故障停機發生頻率高、故障停機時間長的設備,將點檢集中在其經常發生故障的部件上。
(2)推行中班點檢和維修結合。點檢工作與維修相結合,是點檢工作取得應有效果的有效方法。將維修人員分兩班,一班跟隨生產隨時解決突發故障,另一班則在生產結束后對設備進行點檢,並解決前一班生產中遺留下來的並沒有造成停機的故障或隱患。點檢的目的是防故障於未然。因此,利用中班時間點檢與維修相結合,既能更準確地檢查出設備的故障及隱患,又能更及時地處理檢查中發現的問題。
(3)加強基礎管理。完善點檢制度,增強中班點檢的監督和檢查。改變原有的設備管理和維修方式,提高對預防性維修的認識,同時提高人員素質,加強技術及現代設備管理理論的培訓。大力推行日常崗位點檢的規範化,定期檢查、定項修理的制度化、表格化和標準化。試行點檢及預防性維修的激勵機制。對於能夠在點檢或生產巡檢中發現重大設備故障隱患並及時加以解決的維修人員給予一定的經濟獎勵,反之對於所負責的區域和設備因點檢不仔細、不認真造成的設備停機事故給予相應處罰,以此激發維修員工的點檢工作熱情。
為防止企業發生片面追求降低設備維修費用、強制運行設備的短期行為,應將設備維修費用與設備利用率、完好率、設備故障停機率等技術指標捆在一起進行考核,使職工認識到重視設備經濟管理並不意味著輕視設備技術管理、實物管理,更不意味著在設備管理考核指標上厚此薄彼,促使基層單位千方百計提高設備綜合管理水平。