煉焦
化學產品的工藝過程
煉焦是指煉焦煤在隔絕空氣條件下加熱到1000℃左右(高溫乾餾),通過熱分解和結焦產生焦炭、焦爐煤氣和其他煉焦化學產品的工藝過程。冶金焦炭含碳量高,氣孔率高,強度大(特別是高溫強度),是高爐煉鐵的重要燃料和還原劑,也是整個高爐料柱的支撐劑和疏鬆劑。煉焦副產的焦爐煤氣發熱值高,是平爐和加熱爐的優良氣體燃料,在鋼鐵聯合企業中是重要的能源組分。煉焦化學產品是重要的化工原料。因此煉焦生產是現代鋼鐵工業的一個重要環節。
目錄
自20世紀80代以來,隨著我國經濟的快速發展,我國的煉焦產業也進入了一個快速發展期。
1991年,我國的焦炭產量躍居世界第一;1994年,我國焦炭年產量首度超過1億噸;到2000年,我國焦炭出口量佔到世界焦炭貿易量的60%,成為全球最大的焦炭生產國。
據《中國煉焦行業市場需求預測與投資戰略規劃分析報告前瞻》統計顯示,截至2011年末,我國煉焦產業規模以上企業有733家,資產總額達5982.22億元,同比增長24.32%。2011年,煉焦產業實現銷售收入6212.91億元,同比增長35.72%;實現利潤總額178.77億元,同比增長26.14%。從企業經濟類型來看,私營企業數量最多,其企業數量占行業的52.52%,資產占行業的33.11%。
隨著國內及世界鋼鐵工業迅猛發展,其對煉焦產品的需求急劇增長,投資日趨升溫,行業產能迅速擴張。但是煉焦產業資源消耗高,生產排放大,特別是排放物中有害物質多,造成嚴重的資源浪費和環境污染,對國民經濟健康可持續發展帶來巨大壓力,從而也阻礙了煉焦產業的快速發展。
為了加快調整煉焦產業結構,使焦化企業向規模化、現代化、環保型方向發展,國家制定了“焦化行業准入條件”標準。如企業的焦爐炭化室高4.3m以上(含4.3m),規模能力60萬噸以上,環比基本達到國家要求等,經省級環保部門核實推薦和專家組評議標準合格,可進入“焦化行業准入條件”行列,並由主管部門發布。
近幾年來,全國各煉焦大省也先後按照國家政策,加大了調整煉焦產業結構的力度。山西省在淘汰2600多萬噸的土焦、改良焦的基礎上,又淘汰了一批落後的小焦爐;內蒙古自治區關掉小焦爐20多座;河南省關掉落後焦爐生產企業20多家;貴州省關掉落後焦爐生產企業19家;黑龍江、山東、雲南等省淘汰落後焦爐都取得了較大的成績。
簡史
中國明代以前就已採用土窯煉焦,並用焦炭冶鐵。到20世紀初,經過發展的土窯有圓窯和長窯兩種,前者適用於地下水位不高、煤結焦性較好的地區;後者因爐底高於地面,操作受地下水的影響較小,結焦時間較短,適用於多雨而煤結焦性略差的地區。土窯的特點是結焦室和燃燒室不分開,煉焦熱源靠煤乾餾時產生的煤氣和部分煤料燃燒提供,因而成焦率低,焦炭灰分高,結焦時間長(約8~12晝夜),化學產品不能回收利用,對大氣污染嚴重。后經改進,出現一種帶固定拱頂的圓窯,稱為蜂窩式煉焦爐(圖1)。每孔爐的裝煤量5~7噸,結焦時間48~72小時。焦炭在爐內熄火,最初用人工出焦,後來改為機械化出焦。
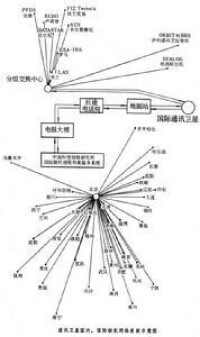
煉焦
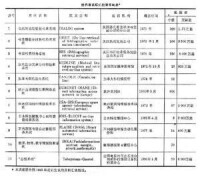
煉焦
結焦機理
煤的有機質基本結構單元,是以芳香族稠環為主體,周圍連接側鏈雜環和官能團的大分子。煤在結焦過程中受熱到350~480℃,大分子劇烈分解,斷裂后的側鏈繼續裂解,其中分子量小的呈氣態,分子量適中的呈液態,分子量大的和不熔組分呈固態,相互滲透的三相物組成膠質體。煤的粘結性強弱,取決於膠質體的數量以及流動性和熱穩定性。當溫度繼續升高到450~550℃時,液相產物進一步分解,其中一部分又呈氣態析出,剩餘部分逐漸變稠,與分散的固相顆粒融成一體,最後縮聚並固化,形成半焦。在這過程中,氣態產物通過膠質體逸出,產生膨脹壓力,使固體顆粒結合得更加牢固。聚積在膠質體中的氣態產物則形成氣孔。當溫度進一步升高到700~1000℃時,半焦主要析出氣體,碳網繼續縮聚,體積變小,焦質變硬,形成多孔的焦炭。這時,熱解產物已無液相出現。由於半焦的收縮,各點的溫度和升溫速度不同,使收縮量和收縮速度不均,產生焦炭裂紋。
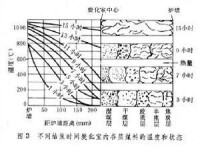
煉焦
有下述程序:
煉焦煤料的製備簡稱備煤,是將煤礦運來的各種精煤(或低灰分原煤)製備成配比準確、粒度適當、質量均一、符合煉焦要求的煤料。一般包括:卸煤、貯存和混勻、配合、粉碎和混合,並將製備好的煤料送到焦爐貯煤塔。嚴寒地區,還應有解凍庫和破凍塊設備。煉製優質焦炭,必須對備煤操作給予足夠的重視。把煤混勻好,提高配煤的準確度,使煤質波動最小,保證焦炭的化學成分和物理機械性能的穩定,以穩定焦炭質量。因此配煤設備必須準確地按給定值配煤;配煤槽要均勻連續下煤。煤中雜物要除凈,水分不能過高。煤料的合理粉碎,可以有效地提高焦炭的機械強度。必須根據具體情況對不同的煤料確定最適宜的粉碎粒度。
改進備煤流程,是擴大煉焦煤源和改善焦炭質量的途徑。目前,中國絕大多數焦化廠都採用先按規定比例配合的混合粉碎流程。這種流程不能根據各種煤的硬度差異分別進行處理,因此只適用於粘結性較好、煤質較均勻的煉焦煤料。較新的備煤流程有三種:①單獨粉碎流程,是將各種煤先單獨進行粉碎,然後按規定的比例配合,再進行混合;②分組粉碎流程,是先將硬度相近的各煤種,按比例配合成組,各組分別送往各自的粉碎機粉碎到要求的粒度,再進行混合;③選擇粉碎流程,是將粉碎到一定程度的煤過篩,將篩出的粗粒級組分進行再粉碎,這樣可使粘結性差、惰性物含量高的粗粒級組分粉碎得較細,避免粘結性好的岩相組分過度粉碎。
煉焦生產已經製備好的煤料從煤塔放入裝煤車,分別送至各個炭化室裝爐。乾餾產生的煤氣經集氣系統,送往化學產品回收車間加工處理。經過一個結焦周期(即從裝爐到推焦所需的時間,一般為14~18小時,視炭化室寬度而定),用推焦機將煉製成熟的焦炭經攔焦機推入熄焦車;熄焦后,將焦炭卸入涼焦台;然後篩分、貯藏。
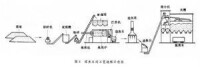
煉焦
焦炭處理
從煉焦爐出爐的高溫焦炭,需經熄焦、涼焦、篩焦、貯焦等一系列處理。為滿足煉鐵的要求,有的還需進行整粒。
熄焦有濕法熄焦和干法熄焦兩種方式。前者是用熄焦車將出爐的紅焦載往熄焦塔用水噴淋。後者是用180℃左右的惰性氣體逆流穿過紅焦層進行熱交換,焦炭被冷卻到約200℃,惰性氣體則升溫到800℃左右,並送入餘熱鍋爐,生產蒸汽。每噸焦發生蒸汽量約400~500公斤,干法熄焦可消除濕法熄焦對環境的污染,提高焦炭質量,同時回收大量熱能,但基建投資大,設備複雜,維修費用高。
涼焦將濕法熄焦后的焦炭,卸到傾斜的涼焦檯面上進行冷卻。焦炭在涼焦台上的停留時間一般要30分鐘左右,以蒸發水分,並對少數未熄滅的紅焦補行熄焦。
篩焦根據用戶要求將混合焦在篩焦樓進行篩分分級。中國鋼鐵聯合企業的焦化廠,一般將焦炭篩分成四級,即粒度大於40毫米為大塊焦,40~25毫米為中塊焦,25~10毫米為小塊焦,小於10毫米為粉焦。通常大、中塊焦供冶金用,小塊焦供化工部門用,粉焦用作燒結廠燃料。
貯焦將篩分處理后的各級焦炭,分別貯存在貯焦槽內,然後裝車外運,或由膠帶輸送機直接送給用戶。
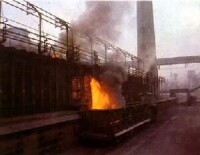
煉焦
整粒將大於80(或75)毫米級的焦炭預先篩出,經切焦機破碎后再過篩,得到粒度80~25(或75~25)毫米級焦炭用於煉鐵。這樣可以提高焦炭粒度的均勻性,並避免大塊焦炭沿固有的裂紋在高爐內碎裂,從而提高焦炭的機械強度,有利於煉鐵生產。