機械粘砂
機械粘砂
機械粘砂又稱為金屬液滲透粘砂,是由液態金屬或金屬氧化物通過毛細管滲透或氣相滲透方式鑽入型腔表面砂粒間隙,在鑄件表面形成的金屬和砂粒機械混合的粘附層。清鏟粘砂層時可見金屬光澤。機械粘砂表面呈海綿狀,牢固地粘附在鑄件表面,多發生在砂型和砂芯表面受熱作用強烈及砂型緊實度低的部位,如澆冒口附近,鑄件厚大截面、內角和凹槽處。
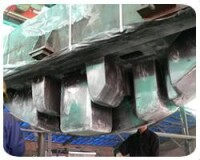
機械粘砂
消失模鑄件一般噸位大,結構複雜,存在較多的橫向或縱向減重孔。在造型過程中,要求混砂設備出砂量較大,這樣常會有個別減重孔舂砂不到位或漏舂,在塗料與型砂之間留下大的孔隙(如圖1所示),從而導致該部位機械粘砂,這種粘砂形態暴露在外表面,大多呈斜坡狀。
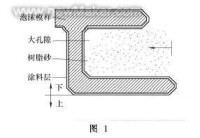
機械粘砂
肉眼外觀檢查。機械粘砂可發生在各種砂型中,表面呈海綿狀,可用噴、拋丸法清理,有時也要進行打磨。樹脂砂型粘砂通常為機械粘砂。
造成第一類缺陷的原因有兩個方面:首先是模樣設計者為了保證鑄件壁厚的均勻性,在模樣上設計出不易舂砂或無法舂砂的結構,甚至在模樣上出現特別狹窄的孔腔。如圖2a、圖2b類結構分別影響右下側和右上側死角部位型砂的緊實,圖3類結構中,A孔往往設在比較深的減重孔下側壁根部,嚴重影響孔內上圓弧處型砂的緊實。造型工在操作時雖然特別關注這些部位,其結果還是出現粘砂;其次是造型工的疏忽大意。
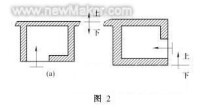
機械粘砂
1.型砂和芯砂粒度太粗。2.砂型和砂芯的緊實度低或不均勻。3.型、芯的塗料質量差,塗層厚度不均勻,塗料剝落。4.澆注溫度和澆注高度太高,金屬液動壓力大。5.上箱或澆口杯高度太高,金屬液靜壓力大。6.型砂和芯砂中含粘土、粘結劑或易熔性附加物過多,耐火度低,導熱性差。7.型、芯砂中含回用砂太多,回用砂中細碎砂粒、粉塵、死燒粘土、鐵包砂太多,型砂燒結溫度低。8.鑄件開箱落砂太晚,形成固態熱粘砂,尤其是厚大鑄件和高熔點合金鑄件。9.金屬液流動性好、表面張力低。例如,銅合金中磷、鉛含量過高,鑄鋼中磷、硅、錳含量過高。10.樹脂砂型、芯表面未刷塗料或塗料質量差,塗層厚薄不均,澆注時砂粒間樹脂膜氣化,形成毛細通道,在金屬液靜壓力、蒸氣壓和表面張力作用下,金屬液或金屬蒸氣滲入毛細通道,形成機械粘砂。11.金屬液中的氧化物和低熔點化合物與型砂發生造渣反應,生成硅酸亞鐵、鐵橄欖石等低熔點化合物,降低金屬液表面張力並提高其流動性,使低熔點化合物和金屬液通過毛細管作用機制,滲入砂粒間隙,並在滲透過程中,不斷消蝕砂粒,使砂粒間隙擴大,導致機械粘砂。12.澆注系統和冒口設置不當,造成鑄型和鑄件局部過熱。
通過以上分析,我們主要採取了如下預防措施:
(1)嚴格審核模樣結構鑄造工程師在模樣結構審核時,必須認真分析模樣結構是否合理,對於影響塗料塗刷和防礙型砂緊實的不合理結構要徹底消除,以方便工人作業。對於圖2a類結構,可在上部開孔(如圖4所示);對於圖2b類結構,應改為圖5a、5b或5c結構;圖3類結構應採取在孔棱邊上倒15mm×15mm×45°大斜角,以利死角部位型砂的緊實。
具體為:
1.使用耐火度高的細粒原砂。2.採用再生砂時,去除過細的砂粒、死燒粘土、灰分、金屬氧化物、廢金屬、鐵包砂及其他有害雜質,提高再生砂質量。定期補充適量新砂。3.水是強烈氧化劑,應嚴格控制濕型砂水分,加入適量煤粉、瀝青、碳氫化合物等含碳材料,在砂型中形成還原性氣氛。但高壓造型時應減少含碳材料加入量,以減少發氣量。4.採用優質膨潤土,減少粘土砂的粘土含量。5.型砂中粘結劑含量要適當,不宜過高。提高混砂質量,保證砂粒均勻裹覆粘結劑膜,並有適度的透氣性。避免型砂中夾有團塊。6.提高砂型的緊實度和緊實均勻性。7.澆注系統和冒口設置應避免使鑄件和鑄型局部過熱。內澆道應避免直衝型壁。8.採用防粘砂塗料,均勻塗覆,在易產生粘砂部位適當增加塗層厚度。塗料中不得含有易產生氣體、氧化及能與金屬液和型砂發生反應的成分。盡量不採用通過反應可在鑄件-鑄型界面形成易剝離的玻璃狀粘砂層的塗料或面砂來解決粘砂問題(例如在鑄鐵件型砂和芯砂中加入赤鐵礦粉等)。9.適當降低澆注溫度、澆注速度和澆注高度,降低上型高度和澆口杯高度,以減小金屬液動壓力、靜壓力及對鑄型的熱衝擊。10.加強對鑄鋼等高熔點合金的精鍊,凈化金屬液,降低合金液的氧化程度和吸氣量,減少低熔點相形成元素(如鑄鋼、鑄鐵中的硫、磷,青銅中的磷、鉛)的含量,控制會降低金屬液表面張力、提高金屬液蒸氣壓的元素(如鑄鋼、鑄鐵中的錳和硅,青銅中的鉛)的含量。11.對於大型厚壁鑄件,適當提早開箱,加快鑄件冷卻,以防止固態粘砂。12.採用表面光潔的模樣和芯盒。
(2)加強對造型舂砂質量的監控配備專職人員對工序質量進行管理,並對舂砂質量實行全程跟蹤,全程監督檢查。
(3)嚴把塗料配製和塗刷質量關尤其是對塗料層厚度的監控,要因料、因件、因時進行嚴格又靈活的作業,確保塗層滿足工藝要求。
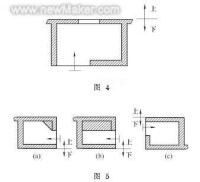
機械粘砂
(5)採用激勵機制按照缺陷嚴重程度及數量進行量化,給予相關責任人一定的經濟處罰。
1.噴、拋丸清砂。2.打磨。3.電化學清砂,尤其適用於清除鑄件深腔和精密鑄件的嚴重粘砂。
蒸氣壓粘結劑打磨孔腔造型工激勵機制塗料芯盒樹脂砂硅酸亞鐵漏舂碳氫化合物碳當量液態金屬凹槽片狀黑色石墨粉粘附層鑄造工藝鑄件金屬氧化物模鑄件鑄件深腔澆注塑料泡沫模樣
[1]佳工機電網 http://mw.newmaker.com/art_27695.html
[2]中華機械網 http://baike.machine365.com/doc-view-22317.html