熔塊釉
熔塊釉
熔塊釉,用熔塊配製的釉。將熔塊和呈色劑按比例放在一起熔融,使呈色劑均勻分佈,冷卻后再加一定量的黏土混合磨細,用水或其他液體調勻即為熔塊釉。可使水溶性物質變為不溶,增加釉的穩定性、懸浮性和與胎體的黏著性,減少氣泡。一般為低溫釉。
熔塊釉就是將部分原料先熔融成玻璃狀物質(即熔塊),再與其他物料混合加水研磨製漿使用的低溫釉料。
部分原料預先熔製成熔塊的形式而製作成的釉料的配方。熔塊釉分為全熔塊釉(熔塊一般為95%左右)和半熔塊釉(熔塊含量30%~85%)。配製釉料時,必須將碳酸鈉、碳酸鉀、硼砂、硼酸之類的水溶性原料和石英或其它硅酸鹽按一定比例混合,先製成熔塊,以防止這些原料在製備釉漿時溶化在水中,在施釉過程中易被坯體吸收,經乾燥后,這些水溶性鹽類又隨水分蒸發而集中在坯體表面,燒后產生缺陷。
將著色劑放在熔塊中預先熔融,還可使它在色釉中分佈更為均勻,提高著色效能。熔塊應與一定分量的可塑性粘土混合細磨,製成的釉漿才具有較穩定的懸浮性和對坯體的粘著性。此外,燒制熔塊過程中原料揮發物的排除,有利於後序製品的燒成,使難容原料變得易容,使釉料成分均勻,擴大了配釉原料的種類等。
(1)降低燒成溫度,擴大燒成範圍。熔塊熔制溫度都比較高,使得各種原料在高溫下充分反應和熔融,轉化成玻璃狀物質,二次再熔時,降低了釉料的熔點,擴大了釉的熔融範圍,為生產控制帶來方便。
(2)穩定釉料性質。為了保證釉料能適應低溫燒成的需求,通常在釉中加入較多的易熔化合物,如硼砂、硼酸、純鹼、硝酸鉀等,它們都是水溶性物質,易溶於水,若是不製成熔塊,作為生料釉,則上述水溶性鹽會溶於釉料的水中,施釉時,它們在坯體吸收水時一同進入坯體,從而改變了坯體與釉料的化學組成,影響最後的製品質量,若將它們預先製成熔塊,變成不溶於水的硅酸鹽或鋁硅酸鹽,可避免引起缺陷。
(3)降低釉料的毒性。引入釉料中的鉛丹、密陀僧(PbO)、氟硅酸鈉、BaCO等是有毒物質,對工人的身體健康有害,將它們經高溫煅燒製成熔塊,轉化為穩定的硅酸鹽,毒性大大降低或者消失,從而避免或減少了對工人的毒害。
(4)提高釉面質量,降低釉料收縮。製作熔塊時,會使得原料中能分解的物質及某些揮發物預先排出,在釉燒時不再出現這些過程,減少了針孔缺陷。同時,經熔制后的釉料,釉燒時,燒失量很小,幾乎不收縮,能更好地與坯體相適應,減少滾釉、縮釉等缺陷。
(5)保證釉漿具有良好的工作性能。引入釉料中的鉛丹(比密度9.1)、鋯英石(比密度4.5~4.7)等物質具有大的比密度,不製成熔塊,則釉料易發生偏析,釉漿中的物質按不同的比密度,分層沉澱。熔製成熔塊后,這些物質與其他物料熔為一體,密度均一,不再出現偏析。
(6)提高乳濁效果。對乳濁釉而言,製備成熔塊能使乳濁劑充分熔化,在隨後的釉燒過程中,再以細分散相析出,可以顯著地提高乳濁效果。
(1)凡溶於水的原料以及有毒的原料均需置於熔塊中。目的是保證釉料穩定,保證工人身體健康。
(4)熔塊配料中的AlO的用量不能超過0.2 mol(釉式中)。因為AlO含量增多,會使熔塊的耐火度及粘度顯著增大,易使熔塊不勻,同時熔制溫度升高,會增加揮發組分的逸失量。
(5)熔塊中鹼性氧化物物質的量之和應小於其他熔劑性氧化物的物質的量之和。這樣製成的熔塊可不溶於水。
熔塊釉與他種釉相比,具有下列顯著的特點:
(1)製造特殊,配料的一部分或全部須先製成熔塊;
(2)可用水溶性原料,但須配料前先將水溶性成分熔入熔塊中;
(3)擴大了釉的燒成溫度範圍,因此它可用於各類不同性質的製品。
熔塊釉是將原料和玻璃預先熔融,然後將原料配入熔塊中。這種方法有優點,也有缺點。現將優點列舉如下:
(1)水溶性原料如鹼性碳酸鹽、硝酸鹽、硼酸鹽等,本來不能應用在釉漿中,但可以使它們混入熔塊中變成不溶性玻璃。在釉漿中含有水溶性鹽類是不適宜的,因為多孔性坯件極易吸收這些物質,這樣,釉的組成在釉桶中極不穩定,同時,多孔性坯件吸取了水溶性鹽類,當乾燥時在坯件邊緣和凸出等部分進行結晶,因而這些地方的釉特別濃,致使在燒成後期產生釉面缺陷,此外,水溶性鹽類在色釉中產生攪動作用而使色釉不能均勻分佈。
(2)有些原料在低溫下反應緩慢,如鋇的化合物,但在熔塊組成中反而成為強烈的熔劑,這就擴大了原料選擇範圍。經過製成熔塊,能向釉中加入較大量的強熔劑,這樣,允許釉有更大的燒成溫度範圍和更好的色料選擇。
(3)某些釉原料與操作人員接觸時,對健康有損害,但用作熔塊的成分就可轉變為無害。
(4)熔塊是釉配方中的高度濃縮部分,與生釉中相應組成的體積相比要小。因為在製造熔塊的加熱過程中已經完成了一部分分解和化學反應,所以在釉料中化學反應就要緩慢些,因此就減少了對坯體和釉下色料的侵蝕作用。此外,熔塊釉施得薄而均勻且與坯體結合得緊密、堅牢。
(5)熔塊釉具有均一性,因此能防止釉組成中由於密度、粒度、形狀和顆粒硬度等的顯著差別所產生離析現象。最主要優點是色料能均勻分佈,從而可防止釉面出現雜色和斑點等缺陷,且釉面色澤光亮。
生鉛釉的鉛化合物懸浮在釉中,因而在使用過程中常發生離析現象。因此,這種釉在坯體施釉前必須進行攪拌,否則較重的顆粒將迅速沉澱出來。如果這種鉛化合物和其他組成以適當比例共製成熔塊,所生成的玻璃體密度小就更容易懸浮在釉漿中。如果SiO和AlO與鉛化合物共同混合製成熔塊,那麼就不能獲得滿意結果。這種混合物在低溫熔融時易於流動,而且熔塊的粘度小,極易被多孔性坯體吸收。如果將熔塊量適當的分配,並加入適當的耐火成分來控制熔融溫度,釉中非熔塊部分繼續溶解,將使釉進一步均勻,可得到更好的結果。
由於熔塊釉含有部分水溶性或毒性原料,因此,製備工藝分兩步進行。第一步制熔塊,第二步將熔塊與粘土等生料配合,再經球磨、過篩、除鐵,製成釉漿。
熔塊的製備方法,是先將各種原料按配方比例準確稱量,經混合均勻后再置於坩堝或池爐、迴轉爐中,以1250~1450℃的高溫進行熔煉,至完全熔融(抽出的細絲沒有結瘤)后,再傾入(或滴入)冷水中急冷,使之成為鬆脆的小塊,以利於粉碎。
原料預處理→原料檢驗→(原料儲備)→配方稱量→混合→過篩除鐵→(混合物儲存)→熔化→水淬→乾燥→檢驗→包裝。
(1)原料的製備
為了保證熔塊料混合均勻,所有原料都必須事先製成粉料。長石和石英等硬質料一般經干碾中碎后,以干法磨細碎。蘇州土等粘土類原料可先經烘乾然後干磨。化工原料可直接過篩配入。在生產實踐中發現,原料過細反而不利於熔制和保證熔塊的質量。因為,原料過細在池爐中易被煙氣帶走而改變其成分;熔化過急,熔體粘度急劇提高(像錇英砂之類能提高熔體粘度的礦物過早地熔人熔體),阻礙了熔塊熔化和澄清。
(2)混合配料
每批進廠原料應作細度、化學成分檢測,保證符合規定要求。配料要求稱量仔細,配比準確,混合均勻。稱量器具要校核准,稱料次序應與混料的投料次序相匹配。如用累計法稱量配料,則應先稱小料,后稱大料。通常用輪碾式混合機或反覆過篩的辦法混合熔料塊。混合后的粉料需進行過篩、除鐵各一次,一般用孔徑2~4 mm篩網。
(3)熔制
通常認為高溫、快速熔制既能保證熔塊熔融透明,又能防止過多的易揮發物揮發。整個過程要求在氧化氣氛中熔融,主要的控制參數是溫度和時間。在原料、粒度、混合等工藝質量穩定的情況下,穩定熔制制度是保證熔塊批量質量穩定的決定性因素。
(4)水淬成粒
熔塊經水淬成粒可縮短釉料研磨時間。
熔塊的熔制設備一般有以下三種:坩堝爐(連續式與間歇式)、池爐和迴轉爐。
(1)坩堝爐
熔制熔塊連續式坩堝爐在坩堝底部有一小孔,孔下面是用於淬冷熔塊的下水槽,如圖所示,結構組成因燃料種類不同,則坩堝個數不同。
熔制前用一個瓷球或用一個瓷管堵住穿孔,待坩堝內完全變紅熱時就可加料。加料要陸續加滿,以後隨粉料的熔融速度陸續補加生料。如果溫度偏低,流出的熔制熔塊不良時,必須單獨存放,以便進行復熔。
(2)池爐
我國牆地磚廠使用的熔塊池爐有兩種基本類型,即順流式和混流式。其主要差別在於順流式池爐物料流動方向與火焰方向是一致的;混流式池爐物料流動方向與火焰的方向,不是簡單的順流和逆流。下圖是兩種不同形式結構的示意圖。
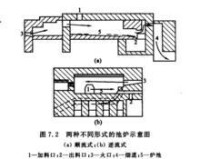
兩種不同形式的池爐示意圖
(3)迴轉爐
熔制熔塊的迴轉爐外形像一錐形球磨機,在鋼板的圓筒內,襯高鋁質耐火磚。筒體中央有進出料口。整個簡體放置在兩對旋轉托輪上,其中一對為主動旋轉託輪,由電機減速器驅動。筒體的一端為裝了噴嘴的孔洞,另一端為煙氣排出口,通向煙道。