塑料助劑
塑料助劑
塑料助劑又叫塑料添加劑,是聚合物(合成樹脂)進行成型加工時為改善其加工性能或為改善樹脂本身性能所不足而必須添加的一些化合物。例如,為了降低聚氯乙烯樹脂的成型溫度,使製品柔軟而添加的增塑劑;又如為了製備質量輕、抗振、隔熱、隔音的泡沫塑料而要添加發泡劑;有些塑料的熱分解溫度與成型加工溫度非常接近,不加入熱穩定劑就無法成型。因而,塑料助劑在塑料成型加工中佔有特別重要的地位。用於塑料成型加工品的一大類助劑,包括增塑劑、熱穩定劑、抗氧劑、光穩定劑、阻燃劑、發泡劑、抗靜電劑、防霉劑、著色劑和增白劑(見顏料)、填充劑、偶聯劑、潤滑劑、脫模劑等。其中著色劑、增白劑和填充劑不是塑料專用化學品,而是泛用的配合材料。
我國的塑料助劑行業是隨PVC行業的發展而發展起來的。同時,隨著塑料合成樹脂行業的發展,塑料助劑行業的應用領域不斷拓寬,產品品種有了較大幅度的增加,塑料助劑行業已成為門類比較齊全、產品品種繁多的重要行業,在技術水平、產品結構、生產規模和科技人員的素質等方面均有長足的發展,基本滿足了下遊行業對塑料助劑產品的需求。目 前,我國塑料助劑行業已經形成產值300億元以上的產業,其中約有50億元的出口。
從2005年開始,我國塑料助劑行業年均增長率保持在8%-10%的水平,遠遠高於世界塑料助劑4%的年均增長率。塑料助劑產業也得到了國家各部門的重視,並逐漸成為近年來最具發展潛力的新材料領域重要成員。“十一五”期間,隨著我國塑料工業的快速發展,各種塑料助劑產品的產能、產量和消費量都取得了較快的增長。2008-2010年我國塑料助劑的消費量分別約為273萬噸、282萬噸和300萬噸,2011年預計在320萬噸左右。
“十一五”期間,我國塑料工業呈現明顯的產業聚集發展態勢,規模企業數量增長迅速,產業結構逐漸向規模化、集約化方向調整。塑料助劑產業也正向規模化、集約化方向調整,這在增塑劑、熱穩定劑、衝擊改性劑和加工助劑方面尤為明顯。
塑料助劑作為通用塑料工程化、工程塑料高性能化不可或缺的成分以及合成樹脂改性實現功能化的關鍵,“十一五”期間,全行業的發展主要集中在通用品種的規模化生產,卻很少看到結構性創新產品出現,同時生產大多採用國外企業專利技術,所以,高性能的綠色、環保、無毒、高效塑料助劑的研發和生產已成為未來我國塑料助劑行業發展的主攻方向。增塑劑要提高非鄰苯二甲酸酯類產量,如環氧大豆油、偏苯三酸酯類;穩定劑應降低鉛鹽類比例,提高鈣/鋅複合類、低鉛稀土類、水滑石類以及有機熱穩定劑產量;阻燃劑應降低鹵素類比例,大力發展無機阻燃劑。同時要積極應對歐盟的環保法規,以及國內外對無毒環保產品的要求。塑料助劑企業應該和高校、科研院所聯合起來改變不合理的產品結構,開發環保型助劑品種。
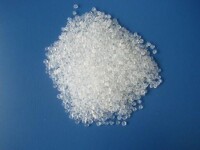
產品樣圖
塑料助劑的分類方式有多種,比較通行的方法是按照助劑的功能和作用進行分類。在功能相同的類別中,往往還要根據作用機理或者化學結構類型進一步細分。
功能 | 類別 |
改善加工性能 | 潤滑劑、脫模劑、穩定劑、加工助劑、觸變劑、增塑劑、PVC穩定劑 |
改善力學性能 | 增塑劑、增強填充劑、增韌劑、抗擊改性劑 |
改善光學性能 | 顏料、染料、成核劑、熒光增白劑 |
改善老化性能 | 抗氧劑、PVC穩定劑、紫外光吸收劑、殺菌劑、防霉劑 |
改善表面性能 | 抗靜電劑、滑爽劑、耐磨劑、防粘連劑、防霧劑 |
降低成本 | 稀釋劑、增溶劑、填料 |
改善其他性能 | 發泡劑、助燃劑、化學交聯劑、偶聯劑、防啃咬劑 |
(1)應與被添加的合成樹脂有較好的相容性,能長期穩定,均勻的分散在樹脂中。(2)協同效應。要盡量使用相互間能促進功能發揮的塑料助劑。
(3)耐久性好。不滲析,不會發,不遷移或被水及液體物質萃取。(4)適合製品的使用要求。(5)對加工條件的適應性要好。(6)分散性好,能在加工成型的過程中容易分散均勻。這六點可以滿足大多數製品對助劑的要求。當然很多PVC製品對PVC穩定劑有特殊的要求,這些要求在PVC穩定劑的發展中得到解決.
增塑劑
增塑劑是一類增加聚合物樹脂的塑性,賦予製品柔軟性的助劑,也是迄今為止產耗量最大的塑料助劑類別。增塑劑主要用於PVC軟製品,同時在纖維素等極性塑料中亦有廣泛的應用。增塑劑所涉及的化合物類別大致包括鄰苯二甲酸酯、脂肪二羧酸酯、偏苯三酸酯、聚酯、環氧酯、烷基磺酸苯酯、磷酸酯和氯化石蠟等,尤以鄰苯二甲酸酯類最為重要。
熱穩定劑
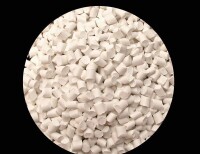
產品樣圖
加工改性劑
傳統意義上的加工改性劑幾乎特指硬質PVC加工過程中所使用的旨在改善塑化性能、提高樹脂熔體黏彈性和促進樹脂熔融流動的改性助劑,此類助劑以丙烯酸酯類共聚物(ACR)為主,在硬質PVC製品加工中具有突出的作用。現代意義上的加工改性劑概念已經延展到聚烯烴(如線性低密度聚乙烯LLDPE)、工程熱塑性樹脂等領域,預計未來幾年茂金屬樹脂付諸使用后還會出現更新更廣的加工改性劑品種。
抗衝擊改性劑
廣義地講,凡能提高硬質聚合物製品抗衝擊性能的助劑統稱為抗衝擊改性劑。傳統意義上的抗衝擊改性劑基本建立在彈性增韌理論的基礎上,所涉及的化合物也幾乎無一例外地屬於各種具有彈性增韌作用的共聚物和其他的聚合物。以硬質PVC製品為例,而今應用市場廣泛使用的品種主要包括氯化聚乙烯(CPE)、丙烯酸酯共聚物(ACR)、甲基丙烯酸酯—丁二烯—苯乙烯共聚物(MBS)、乙烯—乙烯基醋酸酯共聚物(EVA)和丙烯腈—丁二烯—苯乙烯共聚物(ABS)等。聚丙烯增韌改性中使用的三元乙丙橡膠(EPDM)亦屬橡膠增韌的範圍。20世紀80年代以後,一種無機剛性粒子增韌聚合物的理論應運而生,加上納米技術的飛速發展,賦予了塑料增韌改性和抗衝擊改性劑新的含義。對此,國內外已有大量的專著和文獻見諸報道。
塑料製品多數具有易燃性,這對其製品的應用安全帶來了諸多隱患。準確地講,阻燃劑稱作難燃劑更為恰當,因為“難燃”包含著阻燃和抑煙兩層含義,較阻燃劑的概念更為廣泛。然而,長期以來,人們已經習慣使用阻燃劑這一概念,所以在文獻中所指的阻燃劑實際上是阻燃作用和抑煙功能助劑的總稱。阻燃劑依其使用方式可以分為添加型阻燃劑和反應型阻燃劑。添加型阻燃劑通常以添加的方式配合到基礎樹脂中,它們與樹脂之間僅僅是簡單的物理混合;反應型阻燃劑一般為分子內包含阻燃元素和反應性基團的單體,如鹵代酸酐、鹵代雙酚和含磷多元醇等,由於具有反應性,可以化學鍵合到樹脂的分子鏈上,成為塑料樹脂的一部分,多數反應型阻燃劑結構還是合成添加型阻燃劑的單體。按照化學組成的不同,阻燃劑還可分為無機阻燃劑和有機阻燃劑。無機阻燃劑包括氫氧化鋁、氫氧化鎂、氧化銻、硼酸鋅和赤磷等,有機阻燃劑多為鹵代烴、有機溴化物、有機氯化物、磷酸酯、鹵代磷酸酯、氮系阻燃劑和氮磷膨脹型阻燃劑等。抑煙劑的作用在於降低阻燃材料的發煙量和有毒有害氣體的釋放量,多為鉬類化合物、錫類化合物和鐵類化合物等。儘管氧化銻和硼酸鋅亦有抑煙性,但常常作為阻燃協效劑使用,因此歸為阻燃劑體系。
以抑制聚合物樹脂熱氧化降解為主要功能的助劑,屬於抗氧劑的範疇。抗氧劑是塑料穩定化助劑最主要的類型,幾乎所有的聚合物樹脂都涉及到抗氧劑的應用。按照作用機理,傳統的抗氧劑體系一般包括主抗氧劑、輔助抗氧劑和重金屬離子鈍化劑等。主抗氧劑以捕獲聚合物過氧自由基為主要功能,又有“過氧自由基捕獲劑”和“鏈終止型抗氧劑”之稱,涉及芳胺類化合物和受阻酚類化合物兩大系列產品。輔助抗氧劑具有分解聚合物過氧化合物的作用,也稱“過氧化物分解劑”,包括硫代二羧酸酯類和亞磷酸酯化合物,通常和主抗氧劑配合使用。重金屬離子鈍化劑俗稱“抗銅劑”,能夠絡合過渡金屬離子,防止其催化聚合物樹脂的氧化降解反應,典型的結構如醯肼類化合物等。最近幾年,隨著聚合物抗氧理論研究的深入,抗氧劑的分類也發生了一定的變化,最突出的特徵是引入了“碳自由基捕獲劑”的概念。這種自由基捕獲劑有別於傳統意義上的主抗氧劑,它們能夠捕獲聚合物烷基自由基,相當於在傳統抗氧體系中增設了一道防線。此類穩定化助劑而今見諸報道的主要包括芳基苯並呋喃酮類化合物、雙酚單丙烯酸酯類化合物、受阻胺類化合物和羥胺類化合物等,它們和主抗氧劑、輔助抗氧劑配合構成的三元抗氧體系能夠顯著提高塑料製品的抗氧穩定效果。應當指出,胺類抗氧劑具有著色污染性,多用於橡膠製品,而酚類抗氧劑及其與輔助抗氧劑、碳自由基捕獲劑構成的複合抗氧體系則主要用於塑料及艷色橡膠製品。
光穩定劑也稱紫外線穩定劑,是一類用來抑制聚合物樹脂的光氧降解,提高塑料製品耐候性的穩定化助劑。根據穩定機理的不同,光穩定劑可以分為光屏蔽劑、紫外線吸收劑、激發態猝滅劑和自由基捕獲劑。光屏蔽劑多為炭黑、氧化鋅和一些無機顏料或填料,其作用是通過屏蔽紫外線來實現的。紫外線吸收劑對紫外線具有較強的吸收作用,並通過分子內能量轉移將有害的光能轉變為無害的熱能形式釋放,從而避免聚合物樹脂吸收紫外線能量而誘發光氧化反應。紫外線吸收劑所涉及的化合物類型較多,主要包括二苯甲酮類化合物、苯並三唑類化合物、水楊酸酯類化合物、取代丙烯腈類化合物和三嗪類化合物等。激發態猝滅劑意在猝滅受激聚合物分子上的能量,使之回復到基態,防止其進一步導致聚合物鏈的斷裂。激發態猝滅劑多為一些鎳的絡合物。自由基捕獲劑以受阻胺為官能團,其相應的氮氧自由基是捕獲聚合物自由基的根本,而且由於這種氮氧自由基在穩定化過程中具有再生性,因此光穩定效果非常突出,迄今已經發展成為品種最多、產耗量最大的光穩定劑類別。當然,受阻胺光穩定劑的作用並不僅僅局限在捕獲自由基方面,研究表明,受阻胺光穩定劑往往同時兼備分解氫過氧化物、猝滅單線態氧等作用。
填充增強體系助劑
填充和增強是提高塑料製品物理機械性能和降低配合成本的重要途徑。塑料工業中所涉及的增強材料一般包括玻璃纖維、碳纖維、金屬晶須等纖維狀材料。填充劑是一種增量材料,具有較低的配合成本,包括碳酸鈣、滑石粉、陶土、雲母粉、二氧化硅、硫酸鈣、粉煤灰、紅泥以及木粉和纖維素等天然礦物、合成無機物和工業副產物。事實上,增強劑和填充劑之間很難區分清楚,因為幾乎所有的填充劑都有增強作用。由於填充劑和增強劑在塑料中的用量很大,有的已經自成一個行業體系,習慣上已不在加工助劑的範疇討論。應當說明的是,而今廣泛研究的納米填充增強材料對塑料的改性作用已經遠遠超出填充和增強的意義,它們的應用將給塑料工業帶來一場新的革命。偶聯劑是無機和天然填充與增強材料的嚷面改性劑,由於塑料工業中的增強和填充材料多為無機材料,配合量又大,與有機樹脂直接配合時往往導致塑料配合物加工和應用性能的下降。偶聯劑作為表面改性劑能夠通過化學作用或物理作用使無機材料的表面有機化,進而增加配合量並改善配合物的加工和應用性能。見諸報道的偶聯劑大致包括長碳鏈脂肪酸、硅烷類化合物、有機鉻化合物、鈦酸酯類化合物、鋁酸酯類化合物、鋯酸酯類化合物以及酸酐接枝的聚烯烴等。
抗靜電劑的功能在於降低聚合物製品的表面電阻,消除靜電積累可能導致的靜電危害。按照使用方式的不同,抗靜電劑可以分為內加型和塗敷型兩種類型。內加型抗靜電劑是以添加或共混的方式配合到塑料配方中,成型后從製品的內部遷移到表面或形成導電網路,進而達到降低表面電阻泄放電荷的目的。塗敷型抗靜電劑是以塗布或浸潤的方式附著在塑料製品的表面,藉此吸收環境中的水分,形成能夠泄放電荷的電解質層。從化學物質的組成來看,傳統的抗靜電劑幾乎無一例外地屬於表面活性劑類化合物,包括季銨鹽類陽離子表面活性劑,烷基磺酸鹽類陰離子表面活性劑,烷醇胺、烷醇醯胺和多元醇脂肪酸酯等非離子表面活性劑等。然而,新出現的“高分子量永久型抗靜電劑”打破了這種常規,它們一般系親水性的嵌段共聚物,以共混合金的方式與基礎樹脂配合,通過形成導電通道傳導電荷。與表面活性劑類抗靜電劑相比,這種高分子量永久型抗靜電劑不會因遷移、揮發和萃取而損失,因而抗靜電性持久穩定,並極少受環境濕度的影響。
潤滑劑和脫模劑
潤滑劑是配合在聚合物樹脂中,旨在降低樹脂粒子、樹脂熔體與加工設備之間以及樹脂熔體內分子間摩擦,改善其成型時的流動性和脫模性的加工改性助劑,多用於熱塑性塑料的加工成型過程,包括烴類(如聚乙烯蠟、石蠟等)、脂肪酸類、脂肪醇類、脂肪酸皂類、脂肪酸酯類和脂肪醯胺類等。脫模劑可塗敷於模具或加工機械的表面,亦可添加於基礎樹脂中,使模型製品易於脫模,並改善其表面光潔性卧前者稱為塗敷型脫模劑,是脫模劑的主體,後者為內脫模劑,具有操作簡便等特點。硅油類物質是工業上應用最為廣泛的脫模劑類型。
我們知道,塑料製品實際上是基礎樹脂與各種顏料、·填料和助劑的混合體,顏料、填料和助劑在樹脂中的分散程度對塑料製品性能的優劣至關重要。分散劑是一種促進各種輔助材料在樹脂中均勻分散的助劑,多用於母料、著色製品和高填充製品。包括烴類(石蠟油、聚乙烯蠟、氧化聚乙烯蠟等)、脂肪酸皂類、脂肪散酯類和脂肪醯胺類等。
塑料的交聯與橡膠的硫化本質上沒有太大的差別,但在交聯助劑的使用上卻不完全相同。樹脂的交聯方式主要有輻射交聯和化學交聯兩種方式,有機過氧化物是工業上應用最廣泛的交聯劑類型。有時為了提高交聯度和交聯速度,常常需要並用一些助交聯劑和交聯促進劑。助交聯劑是用來抑制有機過氧化物交聯劑在交聯過程中對聚合物樹脂主鏈可能產生的自由基斷裂反應,提高交聯效果,改善交聯製品的性能,其作用在於穩定聚合物自由基。交聯促進劑則以加快交聯速度,縮短交聯時間為主要功能。不飽和聚酯和環氧樹脂等熱固性塑料的固化劑亦屬交聯劑的範疇,常見的類型如有機胺和有機酸酐類化合物。另外,紫外線輻射交聯工藝中所使用的光敏化劑也可視作交聯助劑看待。
用於聚合物配合體系,旨在通過釋放氣體獲得具有微孔結構聚合物製品,達到降低製品表觀密度之目的的助劑稱之為發泡劑。根據發泡過程產生氣體的方式不同,發泡劑可以分為物理髮泡劑和化學發泡劑兩種主要類型。物理髮泡劑一般依靠自身物理狀態的變化釋放氣體,多為揮發性的液體物質,氟氯烴(如氟里昂)、低烷烴(如戊烷)和壓縮氣體是物理髮泡劑的代表。化學發泡劑則是基於化學分解釋放出來的氣體進行發泡的,按照結構的不同分為無機類化學發泡劑和有機類化學發泡劑。無機發泡劑主要是一些對熱敏感的碳酸鹽類(如碳酸鈉、碳酸氫銨等)、亞硝酸鹽類和硼氫化合物等,其特徵是發泡過程吸熱,也稱吸熱型發泡劑。有機發泡劑在塑料發泡劑市場具有非常突出的地位,代表性的品種有偶氮類化合物、N—亞硝基類化合物和磺醯肼類化合物等。有機發泡劑的發泡過程多伴隨放熱反應,又有放熱型發泡劑之稱。此外,一些具有調節發泡劑分解溫度的助劑,即發泡助劑亦屬發泡劑之列。
防霉劑又稱微生物抑製劑,是一類抑制黴菌等微生物生長,防止聚合物樹脂被微生物侵蝕而降解的穩定化助劑。絕大多數聚合物材料對黴菌並不敏感,但由於其製品在加工中添加了增塑劑、潤滑劑、脂肪酸皂類等可以滋生黴菌類的物質而具有黴菌感受性。塑料用防霉劑所包含的化學物質很多,比較常見的品種包括有機金屬化合物(如有機汞、有機錫、有機銅、有機砷等)、含氮有機化合物、含硫有機化合物、含鹵有機化合物和酚類衍生物等。
防啃咬劑
防啃咬劑也稱防鼠咬劑,可使嚙齒類動物的口腔粘膜和味覺神經因受到強烈刺激而厭棄對其嚼咬破壞,對鼠類、野生動物、鳥類、貓狗等寵物有顯著的防止咬害效果。特別適用於農膜,管材,可替代不鏽鋼鎧裝外殼,大大降低生產成本。
PVC加工助劑是丙烯酸酯類共聚物(ACR)。
PVC加工助劑的基本功能就是改進PVC的加工性能,促進PVC混合料的塑化,以便在儘可能低的溫度下獲得塑化良好的物料,提高製品的質量。我們針對不同產品的需要,開發了以下五種類型的加工助劑。
1、通用型:促進物料的塑化。
2、潤滑型:除促進物料塑化外,兼有金屬剝離的作用,防止熔體與金屬表面的粘連,延長開車周期。
3、光亮型:除促進物料塑化外,能顯著增進位品的表面光亮度,適宜於對錶面光潔度需要較高的製品。
4、超強塑化型:促進物料塑化的能力高於其它類型,適宜於難以塑化的物料配方,例如碳酸鈣組份高、潤滑劑用量大或添加碳黑、纖維等改性劑的配方。
5、超強熔體強度型:除促進物料塑化外,還能大幅度地增加物料的熔體強度,提高生產的穩定性,延長生產周期,提高製品的力學性能,尤其是適宜於碳酸鈣含量高(大於wt30%)的製品。
促進塑化機理
無論哪一種PVC的加工形式,均需使PVC混合料均勻地得到塑化,只有塑化均勻良好的物料,其製品才具有良好的外觀和機械性能。
但與其它通用塑料相比,無增塑PVC只有在較高的溫度和剪切條件下才能塑化,但高溫下PVC很容易分解,為保證均勻塑化,提高硬PVC製品的質量,應在儘可能低的加工溫度和儘可能大的剪切力下,使物料塑化。一般來說PVC加工助劑必須具有下列特性,才具有促進塑化的功能。
1、熔融溫度低於PVC,在加工過程中先於PVC熔化。
2、因其與PVC具有良好的相容性,在加工過程中熔化后可以粘連PVC粒子,增加內摩擦,提高剪切扭矩,產生內熱,使物料中的溫度分佈均勻,塑化程度均一,從而促進了PVC物料的均勻塑化。
3、加工助劑具有足夠大的分子量,在加工過程中增大了熔體粘度(或強度),提高了熔體壓力,防止物料的打滑現象從而提高了剪切扭矩,使熔體和金屬表面的摩擦熱大幅度上升,促進了PVC混合料的混合均勻程度和塑化程度。
使用方法
加工助劑ACR的本質為固體增塑劑。如果ACR的熔點再降低、分子量再下降,則最終變為增塑劑。在研究中發現,熔點低的加工助劑(包括增塑劑)塑化速度快,熔體流動性好,但熔體粘度低、熔體強度低、熔體壓力低;熔點高的加工助劑塑化速度慢一些,熔體流動性差一些,但熔體粘度大、熔體壓力高、熔體強度高、後期塑化能力強。前者降低PVC材料的力學性能和耐候性,但後者幾乎不影響PVC材料的力學性能,並對其耐候性有所改善。
塑化效果良好的某種加工型ACR,對一種PVC配方會大幅度的提高擠出機的電流和扭矩,提高PVC的塑化度,但對另一種PVC配方則可能會使PVC製品的顏色變深而出現色差。有時一種加工型ACR在快速擠出機中是合適的,但在慢速擠出機中則不一定合適,反之亦然。因此,要使一種加工型ACR去滿足不同的配方、不同的製品、不同的加工設備的要求幾乎是不可能的。同樣,對傳統的加工助劑ACR,既要滿足塑化快,又要滿足熔體強度大、熔體壓力高的加工工藝要求也是不可能的。為滿足廣大客戶的個性化要求,我們開發出了一系列全新的具有不同促進塑化性能和不同其它特點的加工助劑,去適應用戶的要求,其中某些產品的性能已完全可以取代一些進口產品,我們對這些加工助劑的性能和使用方法進行了詳細研究,只要客戶提出自己的具體要求,該公司新材料科研中心可以向您推薦適用的產品型號、用量與使用方法。
一、成核劑
成核劑是一種用來改變聚丙烯結晶行為,進而改變其結晶形態、力學性能、熱力學性能和光學性能的功能性助劑。
1、聚丙烯成核劑 HBP
添加成核劑改性后的聚丙烯具有透明性好、光澤度高,力學性能和加工性能優良等特點,其使用範圍也比較廣泛。
2、聚甲醛成核劑
聚甲醛(POM)是一種具有優良綜合性質的高結晶工程塑料。其強度和硬度高、剛性好,並且有良好的耐磨性和耐疲勞性,因而被用來代替有色金屬和合金,廣泛應用於汽車、電子電器、建築、機械等行業。由於聚甲醛的結晶度高(一般結晶度超過 60%),製品存在缺口,衝擊強度低、成型收縮率大的缺點,與其他各種優異性能不匹配,需要進一步改進。改進聚甲醛材料的性能主要有兩種方法:嚴格控制加工條件和加入成核劑。研究發現,結晶性高聚物的衝擊強度與球晶的大小和分佈有關。實驗主要是通過在聚甲醛中加入成核劑,改變聚甲醛球晶的形態,減小其結晶尺寸和成型加工過程中的收縮率,提高其衝擊性,優化聚甲醛性能,使其能滿足一些特殊要求。
二、抗氧化劑
PP,PE,PS等塑料在製造、加工、儲存和使用過程中,由於光\氧、熱等因素的作用,常常發生氧化降解,引起塑料劣化,致使塑料失去耐候性和耐久性,影響塑料的強度和外觀。為了延長高分子材料的壽命,抑制或者延緩聚合物的氧化降解,通常使用抗氧劑。
1、主抗氧劑
主抗氧劑又稱自由基捕捉劑,是抗氧劑中起主要作用的一類。它能捕捉在聚合物熱氧化老化中生成的含氧自由基(·OH,RO·,ROO·)和碳自由基(但效果差),從而中止或減緩聚合物的熱氧老化。
2、輔助抗氧劑
輔助抗氧劑又稱氫過氧化物分解劑。它是一類能夠將熱氧化老化鏈反映中生成的聚合物氫過氧化物分解,使之生成失去活性的化合物,從而終止或減緩熱氧老化的助劑。由於它與主抗氧化劑常有協同效應,並只在與主抗氧化劑並用時才能發揮最大的效果,故通稱輔助抗氧劑。
3、碳自由基捕捉劑
碳自由基(即烷基自由基)通常在熱氧化老化的鏈反應中,在無氧及高溫的情況下生成。
三、增塑劑
增塑劑是現代塑料工業最大的助劑品種,對促進塑料工業特別是聚氯乙烯工業的發展起著決定性作用。凡能和樹脂均混合,混合時不發生化學變化,但能降低物料的玻璃化溫度和塑料成型加工時的熔體黏度,且本身保持不變,或雖起化學變化但能長期保留在塑料製品中並能改變樹脂的某些物理性質,具有這些性能的液體有機化合物或低熔點的固體,均稱為增塑劑。
聚酯增塑劑由二元酸和二元醇通過縮合反應製得,種類主要有己二酸類聚酯和苯酐聚酯等。聚酯增塑劑與一般常用的增塑劑最大的不同在於具有較大的分子量。聚酯增塑劑的分子量可以與 PVC相當,因此與PVC具有更好的相容性。更由於其揮發性低,耐油及耐脂肪族或芳香族碳氫化合物的抽出,在油漆與橡膠中耐遷移,且耐老化性能優異,與低分子量增塑劑相比,聚酯增塑劑具有耐抽出、耐高溫和遷移性小等性能超群的特點,使它享有“永久性增塑劑”之稱,是發展較快的一類增塑劑。
四、熱穩定劑
1、稀土熱穩定劑的熱穩定機理
稀土元素有眾多的軌道可作為中心離子接受配位體的孤對電子,同時,稀土金屬離子有較大的離子半徑,與無機或有機配位體主要通過靜電引力形成離子配鍵。PVC 降解時釋放的 HCL 反應有強烈的催化作用,普遍認為它是離子型機理催化反應的,有 [CLHCL] - 或 [CL] - 離子參與反應過程,而 [CLHCL] - 或 [CL] - 離可作為提供孤對電子的配位體,按照 Pearson 提出的“軟硬酸鹼原則”,硬鹼氯離子與稀土金屬離子易形成穩定的絡合物。因此稀土原子與 PVC 鏈上的氯原子之間具有很強的配位絡合能力, [CLHCL] - 、 [CL] - 即不在參與催化脫 HCL的反應,那麼對 PVC 就起到了一定的穩定作用。
2、抗氧劑 F 對聚甲醛熱穩定作用
聚甲醛(POM)作為一種綜合性能優良的工程塑料,被廣泛應用。但由於其特殊的分子結構,POM熱穩定性較差。在其熔融加工過程中,易在熱、氧作用下發生斷鏈、按自由基型分解方式進行熱降解,進而發生連續脫甲醛反映。通常加入抗氧劑來捕捉體系產生的自由基,中斷整個體系自動氧化循環過程,起到抗氧穩定作用在。在國內外POM生 產 應 用 中 常 用 瑞 士 Ciba 公 司 牌 號 為Irganox259 和 Irganox245 的酚類抗氧劑,可大幅度提高 POM的熱穩定性。
實驗人員選用高相對分子質量受阻酚類抗氧劑 F 作為POM抗氧劑,除起到高效熱穩定作用外,還能減少抗氧劑用量,降低POM生產成本。
1)採用熱失重率、熱失重速率、平衡扭矩分析測試結果表明,抗氧劑 F 在用量為 0.3~0.4時,對 POM可達到與 0.5%Irganox245 相當,甚至更好的熱穩定效果。
2)抗氧劑 F能高效抑制 POM樹脂在高溫加工過程中所引起的熱、氧、應力作用降解,有效延長POM製品的長期熱、氧壽命,並且較少用量的抗氧劑 F(0.3%)熱、氧穩定效能達到0.5%Irganox245 的水平,可將其推廣應用於 POM生產,進一步提高 POM熱穩定性,降低生產成本。
該公司開發的YM- 、YP- 系列PVC發泡調節劑實際上也是丙烯酸酯類加工助劑,它具備PVC加工助劑的所有基本特點,與PVC通用加工助劑的唯一不同就在於分子量,PVC發泡調節劑的分子量要遠高於通用型加工助劑。
發泡調節機理
在PVC發泡製品中,加入超高分子量聚合物的目的:一是為了促進PVC的塑化;二是為了提高PVC發泡物料的熔體強度,防止氣泡的合併,以得到均勻發泡的製品;三是為了保證熔體具有良好的流動性,以得到外觀良好的製品。由於不同的發泡製品生產廠家的產品不同,所用的設備、工藝、原料及潤滑體系均有差異,因此我們開發了具有不同性能的發泡調節劑,以滿足用戶的不同需求。
使用方法
1、發泡調節劑選擇的原則:
①不同聚合度的PVC,如S-700、S-800、S-1000,具有不同的加工溫度、熔體粘度和熔體流動性,要據此選用合適的發泡調節劑。
②塑化速度要合適
③熔體強度要足夠
④熔體流動性要好
⑤不同的產品,如發泡板材、發泡厚板、發泡薄板、木塑發泡板、鋼塑發泡板等,所需工藝條件不同,應根據各型號發泡調節劑的基本特性選用不同的型號。
⑥選擇與相應的PVC能夠分散良好的發泡調節劑,以保證熔體的均勻性和良好的板面質量。
⑦選擇良好的內外潤滑劑
⑧加入足夠的熱穩定劑
2、用法與用量
根據上述原則,在雙方技術人員充分交流的前提下,才有可能確定最適用的型號和用量。
PVC加工改性劑YMs-系列產品是該公司將先進的高分子合成技術與清華大學工程系化學工程研究室的納米技術相結合,研製開發的一種新型PVC改性加工助劑,它充分利用了納米材料比表面積大,表面自由能大的特點,克服了傳統的PVC加工助劑在溫度降低時塑化性能變差的缺陷。在加工過程中,納米材料強大的表面張力,轉化為與PVC分子的內摩擦力,因為這種內摩擦力隨著溫度的降低而增大,這就改善了傳統ACR的塑化性能隨溫度下降而顯著變差的問題。
HLn-系列產品與傳統的ACR相比有下列特點:
1)靜態穩定性要好於傳統的加工助劑。
2)溫度變化時,剪切力相應變化,可使PVC的塑化度基本不變。
3)能大大改善PVC的加工性能,提高製品的表面光潔度。
⒉1檢驗方法
1)外觀用目測
2)揮發按GB/T2914測定
3)粒度按GB/2916測定
4)加工性能用RM-200轉矩流變儀測定,轉速35rpm,溫度165oC,加料量61g;
性能評價配方:PVC,100g;CaCO3,5g;TiO2,4g;PE,0.15g;硬脂酸,0.2g;二鹽,2.5g;硬鉛,1.5g;硬鈣,0.7g;CPE,9g;加工助劑,2g。
⒉2加工助劑的加工性能
PVC加工助劑功能是增大混合物內部分子之間以及混合料與螺桿、料筒表面摩擦,從而提高PVC加工設備的電流和扭矩,使得PVC在儘可能低的加工溫度下均勻地進行塑化,以得到分解程度最低,外觀和機械性能最佳的PVC硬製品。如果PVC的加工溫度降低,則PVC製品中穩定劑的殘留量就越大,平衡的HCI的量也越低,製品的穩定性或者說耐候性能越好!而低溫加工的一個條件就是必須保證高剪切,也就是必須保證高的電流和扭矩。因此,PVC加工助劑的性能必須用扭矩和電流來評價,而能反映扭矩的試驗設備就是轉矩流變儀,所以該公司在HLn-系列產品的質量指標中,不是用粘度而是用流變儀來表徵加工助劑的加工性能。所有的產品在出廠前都用流變儀測試,如果流變曲線重合,則兩批產品的加工性能是相同的,從而確保了客戶在生產使用過程中的穩定性。
為了生產順利,首先選擇粒徑適中且粒徑分佈均勻的CaCO3,再根據潤滑平衡原則,從以下5點考慮。
1.內、外潤滑均不足:熔體粘度較大,塑化扭矩較大,熔體粘壁現象嚴重,物料表面有黃色的分解線,表面光滑性較差,製品力學性能較低。
2.內、外潤滑劑均過量:塑化扭矩較小,熔體塑化明顯不足,雖然製品光滑度很好,但壓點粘合較差,嚴重影響製品力學性能。
3.內潤滑劑較少、外潤滑劑較多,塑化時間明顯地延長,塑化扭矩減小,製品成型困難變脆。
4.內潤滑劑較多,外潤滑劑較少,塑化時間明顯地縮短,有較嚴重粘壁現象,熱穩定時間縮短,製品表面有分解黃線。
⒌當CaCO3粒徑過大時混合料塑化時間明顯延遲,螺桿扭矩較低生成的摩擦熱過少,熔體強度低製品難成型。為了增加熔體強度、促進塑化,加入一定數量的新型JL- M01聚合加工改性劑。新型JL- M01聚合加工改性劑能增加混合料的熔體粘度及粘附性,提高了剪切力對摩擦熱的轉換。
1、綠色增塑劑迎來擴產潮
2、需求快速發展推動熱穩定劑“綠色”改變
3、助劑產品有單一產品向多能產品,複合料方向轉變
4、加工及抗沖改性劑逐步取代PP/PE 材料