燒結鍋
燒結鍋
燒結鍋是鼓風燒結用的一種設備,燒結鍋多為圓形的。鍋內裝有鍋篦,鍋篦下方有進風通道,鍋身支架在基礎上,並可借手輪和轉動機構傾翻。燒結時,在爐篦上先撒上一層點火用的燃料,然後鋪上燒結料,點火鼓風燒結。燒成后,轉動鍋身,把燒成產品翻倒出來,再進行下一鍋燒結。
燒結鍋是鼓風燒結用的一種設備,燒結鍋多為圓形的。鍋內裝有鍋篦,鍋篦下方有進風通道,用於提供空氣,使得燃料燃燒充分。
我國燒結鍋普遍用於中小型燒結廠,一般直徑為2.5米,有效高度為0.8米,有效容積為4立方米。每鍋裝料7~8噸,可生產燒結礦3.5~4.5噸。
此工藝步驟可分為三步:
1、低溫預燒階段

燒結鍋
此階段開始出現再結晶,在顆粒內,變形的晶粒得以恢復,改組為新晶粒,同時表面的氧化物被還原,顆粒界面形成燒結頸。
3、高溫保溫完成燒結階段
此階段中的擴散和流動充分的進行和接近完成,形成大量閉孔,並繼續縮小,使孔隙尺寸和孔隙總數有所減少,燒結體密度明顯增加。
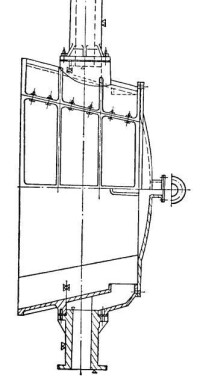
燒結鍋
鍋身用鐵或鋼鑄成,其下部有風口,上置有孔的鋼板或鐵板以載爐料,名叫假底或爐篦。鍋的外部左右兩側有軸,乘在軸承之上。軸的一端裝有聯動機構,由手輪戎馬達轉動,使鍋身旋轉,以傾出燒結礦。鍋的上部設有鋼板製成漏斗形的煙罩,可以升降,爐氣自此排人煙道。煙罩周圍設有工作門,其數量視鍋的大小而定,一般為4~8個。假底上開有很多的進風孔,通常為圓形,直徑9~18毫米,有的冶鍊廠改為橢圓形,通風很好。假底安裝在鍋內壁的凸緣或支架上,如用軟鋼板製成,常分為幾塊以便燒壞時更換。風口有設在鍋底中央用帆布袋與風管連接的,也有設庄鍋壁的下方,通過一端的空軸與風管連接的。
鍋的安裝有固定式及移動式,如果所用的燒結鍋是固定式,在當場轉動。移動式分兩種:1)鍋軸乘在車架上,而車輪則乘在鋼軌上;當燒結結束時,將車架推至卸礦場傾出燒結礦;2)燒結鍋乘在磚砌的圓圍牆上,燒結結束時,用吊車將鍋運至卸礦場傾卸。這種裝置的風口系開在圍牆上,因此只有假底而沒有鍋底,並且鍋身矮而直徑大。卸礦處設有條篩,以分出返粉,當卸礦時燒結塊從相當高的距離傾於條篩上具有破碎作用。
鑄鐵制的鍋在焙燒時有時開裂,不如鑄鋼製的耐用。改進的鍋身均由四塊合成,下裝鍋底,其接縫填塞石綿,用螺栓固定以防漏氣,這樣在鍋身燒壞時不必全部更換。
燒結焙燒可在不同的冶金器具中連行。所有煉燒器具可分成兩類:(1)人工操作的器具(2)機械化操作的器具。現將第一類器具中的烷結鍋作業在此討論。
燒結鍋按其形狀分為錐形鍋及球形鍋。這兩種鍋都是過了時代需求已失去其作用的器具,但現在某些工廠里有使用的。
鍋固定在雙軸手車上,以便鍋充滿后使躺鍋推開將料卸出。鍋安置在鐵罩的下面,罩則與煙道相連,以便排除氣體。鍋底部的進風管靠近在鼓風機管的支管,並用橡皮管與後者相連著。鼓風便依此系統由鼓風機供給而來並由爐篦下面進入鍋中。
燒結鍋的作業情況如下。將鍋安置在煙罩的下面,並使它與鼓風管相連起求。在爐篦之上裝入一層已磨碎的石灰石,厚3~4公分。石灰石能保證爐篦不受火併能阻止焙燒時形成的少量鉛及其他易熔物充塞其間。在石灰石層之上,擲放木片或小塊薪柴,並於它們燃燒之後,投入小煤塊並送入微風。在紅熱煤層之上,逐漸把已製備好的並已經浸濕的爐料加入。
把幾種潤濕的爐料加入鍋中以後,工人便能看出爐料沿噴火整個表面均勻燃燒已至何種程度。在那些因形成所謂“噴火口”而有鼓風逃逸的地方,加入新的爐料並用鏟使料靠緊一些。
隨著頸部分墟料的焙燒,噴火表面便開始發紅。在發紅的地方漸漸加入新鮮爐料。焙燒是成水平層進行的:在原先已經焙燒的爐料上面進行爐料新鮮部分的焙燒。鍋內大部分空間未被像焙燒器具那樣利用著,卻是成為已經焙燒的物料的儲藏室。因此,鼓風壓力是隨著鍋的充滿而增高的。在焙燒開始峙,鼓風壓力在10公釐汞柱,中間一段為25公釐,及至作業終了達到40~50公釐。鍋內溫度則是隨著高度而升高,並達到900℃甚至1000℃。過高的溫度是危險的,因為會使鉛和銀因揮發而受的損失猛烈增大。當鍋已充滿至頂部,便停止加料,並使鍋開始穿風。穿風的目的在使殘留的硫燒去,並靠此更緊迫的焙燒來使已程焙燒的物料最後結塊。鍋充滿過程為6~12小時,穿風時間為1.5~2小時。作業完成以後,便停止鼓風,使進風管分開,並用手使鍋沿軌推翻幾公尺。
已經焙燒的物料,在經第二次焙燒以後,其中含硫量慮應不超過1~3%。焙燒時有12~20%碎塊形成。
燒結鍋的配料計算與燒結機完全相同,作業也分為一次焙燒和兩次焙燒兩種;過程中所起的物理化學變化亦相同,其不同之點只是料層較厚而作業時間較長而已。
燒結鍋焙燒成績的好壞主要取決於:1)爐料各組份的配合及其準備程度(包括破碎、濕潤及混合等等);2)爐料的燃燒情況(火焰應均勻地上升等)。成績良好時結塊率達90%以上(返粉佔10%以下),否則只有80%上下。風壓的高低視風口直徑的大小及料層透氣性與其厚度而定。風壓不宜過高,以免增大煙塵損失。爐料的含硫量應在8%上下,燒結礦含硫在3%以下。每鍋操作時間視料層厚度及爐料成份與其物理及化學性質而定,約為4~8小時。在燒結過程中,爐料的含硫量極關重要,因為金屬硫化物是冶金燃料;如果含硫過多,會導至爐料過早熔結而妨礙脫硫。又如果爐料含硫不足,氧化反應雖進行得完全,但因燒結不好,而造成返粉過多的現象。
過程進行中,在鍋內硫化物強烈氧化的區域,料層溫度上升到1000~1100℃。但當這部分的爐料氧化及燒結結束時,溫度迅速地下降;已經燒結的下層爐料被冷風吹過而逐漸冷卻,同時把熱傳給空氣,使冷風變成熱風。在強烈進行氧化過程的區域之上的料層被上升的熱氣流加熱。因此,過程中反應熱的利用率很高。由於高溫區發生的氧化鉛蒸氣凝結在上層爐料的表面上,而鉛的揮發損失減少;同時上層爐料也具有捕集煙塵的作用。根據我國某鉛廠的燒結實踐,進入煙塵的鉛量約佔爐料中鉛含量的2~4%,通過收塵設備煙塵絕大部分可以收回。煙塵產量一般為爐料重量之3~6%。當爐氣排出時,因通過煙罩工作門進入大量的空氣,故爐氣中SO及SO的含量都很低(1.5~2%SO;±0.1%SO)。