冷鐓
少無切削金屬壓力加工工藝之一
冷鐓工藝是少無切削金屬壓力加工新工藝之一。它是一種利用金屬在外力作用下所產生的塑性變形,並藉助於模具,使金屬體積作重新分佈及轉移,從而形成所需要的零件或毛坯的加工方法。冷鐓工藝最適於用來生產螺栓、螺釘、螺母、鉚釘、銷釘等標準緊固件。
冷鐓工藝常用的設備為專用的冷鐓機。如生產量不太大,也可以用曲柄壓力機或摩擦壓力機代替。隨著我國國民經濟的飛速發展,我國工人階級自行設計製造的多工位自動冷鐓機,已經達到了專用、高效的先進水平。
1.冷鐓是在常溫條件下進行的。冷鐓可使金屬零件的機械性能得到改善。下表是冷鐓螺栓和切削加工螺栓的機械強度對比:
從表中可以看出,無論是何種規格的螺栓,冷鐓加工后的抗拉強度比切削加工的提高約10%左右,有的甚至可提高20%。這是因為冷鐓加工產品的金屬纖維不會被切斷,金屬內部結構被壓實,以及伴隨加工硬化現象的存在,所以金屬機械性能得到了改善。
2.冷鐓工藝可以提高材料利用率。以冷鐓螺栓為例,新工藝“凹穴”六角頭螺栓,材料利用率可達99%以上。除了‘料頭料尾的損失外,達到了完全無切削加工。如用切削加工,材料利用率則僅為40%。冷鐓螺母的材料利用率也可達80%左右,而切削加工螺母,其材料利用率只有54%。
3.冷鐓工藝可大大提高生產率。如冷鐓螺母與原切削工藝相比,生產率約提高25~30倍。
4.由於採用了多工位冷鐓機,實現了各道工序在一台機床上同時加工,從而減少了設備投資,減少了設備所佔用的生產場地,減少了半制品在各工序之問的運輸,特別是減輕了工人的勞動強度,改善了勞動條件。
5.冷鐓工藝能提高產品表面光潔度和保證產品精度。一般光潔度可達V5,特殊要求可達V6。對於大批生產螺栓,螺母等來說,完全可以保證其精度。
冷鐓工藝由於具有高的生產率,良好的產品質量,並i大大減少材料消耗,降低生產成本,改善勞動條件,因此愈來愈廣泛地應用在機械製造特別是標準緊固件的生產中,其中應用多工位冷鐓機生產的最有代表性的產品,是螺栓、螺釘和螺母。
1.要求有較高的塑性和較低的硬度
由於冷鐓時毛坯的側表面存在切向拉應力,客易產生縱向表面裂紋,如圖4-16所示,因此,冷鐓工藝應採用專用的高塑性、低硬度的材料。對於鋼材一般要求表面硬度為75-85HRB。
2.表面質量要求很高
由於冷鐓工藝主要用於標準件生產,這些產品一般不再進行切削加工,尤其是螺釘,螺栓等標準件,其桿部在冷鐓過程中變形極少,仍保持毛坯的原有表面,因此,必須要求冷鐓用原材料具有較低的表面粗糙度,不允許有划傷,麻斑、銹跡等表面缺陷。
3.尺寸精度要求高
為保證坯料的體積準確,必須要求坯料直徑公差很小。以螺栓為例,其原材料公稱尺寸及公差為Φ
材料的供應形式有冷拔盤料和冷拔棒料兩種。冷拔盤料的直徑規格為2~16mm,每盤重量為100~2000kg;一般直徑大於16mm的冷拔料以棒料的形式供應。
在冷鐓加工時,由於金屬產生加工硬化作用,冷鐓變形程度越大,變形抗力也將越大。當冷鐓變形程度超過金屬材料本身最大許用變形程度時,在零件側表面就會形成裂紋;當冷鐓的單位壓力超過模具所允許的壓力時,就會引起模具的損壞。因此,對各種不同尺寸形狀、不同冷鐓材料,應當選擇合理的變形程度。一般冷鐓變形程度常用下式表示:
式中,ε-冷鐓變形程度;
-鐓粗前毛坯原始高度;
-鐓粗后零件的高度。
另外,如果冷鐓前毛坯長度過高,冷鐓時則會產生側向彎曲,造成摺疊、夾灰等缺陷。因此,冷鐓時的變形程度要選得合適。
據一些工廠的實驗數據得知,不同金屬材料,在冷鐓時側表面出現裂紋的最大許用變形程度如下表:
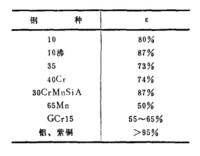
最大許用變形程度
冷鐓變形程度超過上列數據時,為防止產生裂紋,應進行中間退火,以消除冷鐓變形中產生的硬化現象,然後再繼續鐓鍛。除了考慮最大許用變形程度外,對於幾何形狀過分複雜的冷鐓產品,也必須考慮中間退火。如採用中間退火工藝,則只能分工序進行冷鐓。
冷鐓工藝除受上述變形程度影響外,還必須考慮鋤鍛時材料的彎曲。一般實跋經驗是,根據線材未夾持幫分的自由高度h與其直徑d之比,來決定鐓鍛次數。
當時,鐓鍛一次;
時,鐓鍛兩次;
時,鐓鍛三次。
在實際生產中,還要考慮產品的幾何形狀,按照上列數據多增加一次鐓鍛。如螺栓、螺釘、螺母的冷鐓次數,就要比上列計算數據多鐓一次。這是一方面為了考慮模具的使用壽命,另外也是為了保證產品質量。
冷鐓時的坯料長度,可根據體積不變原則來決定,即塑性變形前坯料的體積,等於冷鐓后零件的體積。如冷鐓后還要進行切邊或切削加工,那麼坯料的體積還應加上相應的切削量。
坯料體積決定后,它的頭部所需毛坯長度,可按下圖所示所示進行計算。
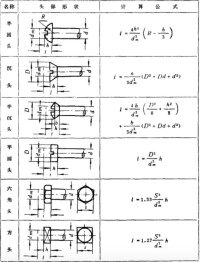
長度計算公式