自動雙頭倒角機
自動雙頭倒角機
自徠動雙頭倒角機的夾模與刀盤,經過精巧的設計,確保加工物件與刀盤的中心線準確不變,可以一次均勻的完成無縫鋼管的外角,內角及端面的加工,保證加工尺寸準確,通過振動盤自動上料,大大提高了生產效率,節省人力。
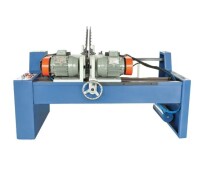
自動雙頭倒角機
雙頭倒角機將被倒角雙頭吊在散料布料台上,斜軌道處的擋料器將雙頭擋住,自動倒角機將分料器把雙頭逐根撥入對齊輥道中,對齊輥道將雙頭向倒角端齊頭,雙頭倒角機沿斜軌道下滑並通過對齊定位板進入主傳動的摩擦輪中,壓緊裝置升程將工件壓住,啟動主傳動軸讓工件旋轉起來,送進砂輪機開始倒角,倒角完畢,落下壓緊裝置,挑鋼鉤子將工件托上斜軌道,又一組擋料分料器將雙頭一根根地分到下一組對齊輥道中,並向反方向齊頭,下一台自動倒角機將另一端倒角,最後一組挑鋼勾子把成品送入收集槽中。
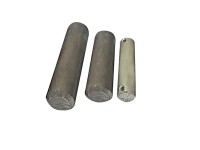
自動雙頭倒角機
主傳動機構主傳動機構由主動輪軸和惰性輪軸組成,主動輪軸和惰性輪軸分別鑲嵌了組丁苯橡膠輪,間距為,靠磨削端兩橡膠輪的間距為,雙頭置於其間,主動輪轉動時,雙頭將藉助與橡膠輪之間的摩擦力而迥轉。
熱軋鋼材總會有不同程度的彎曲,為防止工件在兩輪之間卡死和因跳離膠輪而使摩擦力矩減小的現象出現,設計時將主動輪軸的輸入端固定,兩軸靠磨削端的兩個橡膠輪也固定,其餘兩軸所有的橡膠輪皆能上下浮動,左右移動,完成整個雙頭倒角機的工作過程。
自動倒角機和雙頭倒角機的日常操作規程表
在每天的工作之前要準備及檢查工作
1、每天檢查 自動倒角機,雙頭倒角機的機體周圍環境衛生。
2、清點工具箱內工具是否齊全。
3、檢查雙頭倒角機氣源、電源及各按鈕開關、指示燈、電眼感應是否正常。剎車是否靈敏。
4、檢查自動倒角機油泵、石蠟油泵是否工作,油嘴是否噴油,確保設備運轉正常給油。
5、檢查縮徑模具、翻邊模具是否有鬆動,如有鬆動應立即做出調整。
1、在自動倒角機和雙頭倒角機開機之後后應立即測量罐高、翻邊尺寸,觀察縮徑長度是否均勻。
2、隨時抽檢縮徑翻邊后罐身是否有爆口、假焊、高低罐、翻邊塗膜脫落、焊縫漏塗、烘焦及起泡現象,如有立即停機,向焊機人員反應,並使其做出相應的調整。
3、在自動倒角機的生產中應定期檢查噴油潤滑情況,觀察油量大小,避免罐內有嚴重的石蠟油污染。
4、隨時注意前後工序的配合,觀察設備運轉情況如有異常立即停機。技術人員做出相關處理。
5、當雙頭倒角機停機時,應對各個模具,進行清潔,防止潔塵造成產品品質下降。
6、卡罐時,嚴禁用手從設備中取出壞罐,應用相關工具。避免造成人身傷害。
7、設備維修調整后,工具零件妥善安置好放可生產,並不斷抽檢產品品質情況。做好維修記錄和停機記錄。
8、設備維修時,嚴禁非相關人員隨意按動按鈕。設備運行時不得擅自離崗,以保證生產安全。
目前隨著國內鋼鐵企業的快速發展,國內的 自動倒角機發展迅速,自動倒角機在生產大圓鋼棒材產品過程中, 受定尺分段鋸切、冷床收集等工序的影響, 在棒材端部易產生飛邊、毛刺及腫頭現象,嚴重製約著產品表面質量的提高。而且, 隨著市場經濟的發展, 棒材深加工單位及使用單位對棒材產品提出了更高、更嚴的表面質量和包裝質量要求。
為此, 眾多企業在棒材的精整工序採取了多種措施, 如: 人工手提砂輪機修磨方式、固定式砂輪機修磨方式、機加工車床切削方式等, 但效果均不理想, 主要存在的問題有:
( 1) 作業率低, 不能與生產節奏有效匹配,易造成棒材積壓, 物流不暢。
( 2) 精整質量無法保證, 尤其人工、砂輪修磨方式, 棒材端部的腫頭很難徹底去除。
( 3) 精整工序勞動強度大, 作業環境惡劣。
(徠 4) 採用固定式砂輪機修磨方式及機加工車床切削方式時, 棒材在生產過程中產生的不平直度, 會導致棒材精整時整支旋轉進給困難, 棒材端部周期性擺動, 對砂輪片、切削刀片造成較大衝擊, 易導致砂輪片、刀片崩裂, 存在較大的安全隱患。