數字化工廠
新型生產組織方式
數字化工廠(DF)以產品全生命周期的相關數據為基礎,在計算機虛擬環境中,對整個生產過程進行模擬、評估和優化,並進一步擴展到整個產品生命周期的新型生產組織方式。
數字化工廠(DF)是現代數字製造技術與計算機模擬技術相結合的產物,同時具有其鮮明的特徵。它的出現給基礎製造業注入了新的活力,主要作為溝通產品設計和產品製造之間的橋樑。
在設計部分,CAD 和 PDM系統的應用已相當普及;在生產部分,ERP等相關的信息系統也獲得了相當的普及,但在解決“如何製造→工藝設計”這一關鍵環節上,大部分國內企業還沒有實現有效的計算機輔助治理機制,“數字化工廠”技術與系統作為新型的製造系統,緊承著虛擬樣機(VP)和虛擬製造(VM)的數字化輔助工程,提供了一個製造工藝信息平台,能夠對整個製造過程進行設計規劃,模擬模擬和治理,並將製造信息及時地與相關部分、供應商共享,從而實現虛擬製造和并行工程,保障生產的順利進行。
“數字化工廠”規劃系統通過同一的數據平台,通過具體的規劃設計和驗證預見所有的製造任務,在進步質量的同時減少設計時間,加速產品開發周期,消除浪費,減少為了完成某項任務所需的資源數目等,實現主機廠內部、生產線供給商、工裝夾具供給商等的并行工程。
數字化工廠(DF)是企業數字化輔助工程新的發展階段,包括產品開發數字化、生產準備數字化、製造數字化、管理數字化、營銷數字化。除了要對產品開發過程進行建模與模擬外,還要根據產品的變化對生產系統的重組和運行進行模擬,使生產系統在投入運行前就了解系統的使用性能,分析其可靠性、經濟性、質量、工期等,為生產過程優化和網路製造提供支持。
德國工程師協會定義:數字化工廠(DF)是由數字化模型、方法和工具構成的綜合網路,包含模擬和3D/虛擬現實可視化,通過連續的沒有中斷的數據管理集成在一起。
數字化工廠(DF)集成了產品、過程和工廠模型資料庫,通過先進的可視化、模擬和文檔管理,以提高產品的質量和生產過程所涉及的質量和動態性能:
●提高盈利能力
●提高規劃質量
●縮短產品投產時間
●交流透明化
●規劃過程標準化
●勝任的知識管理
虛擬現實模擬技術
主流市場觀點認為,數字化工廠主要涉及產品設計、生產規劃與生產執行三大環節,數字化建模、虛擬模擬、虛擬現實/加強現實(VR/AR)等技術包含在其中。
1. 產品設計環節——三維建模是基礎
在產品研發設計環節利用數字化建模技術為產品構建三維模型,能夠有效減少物理實體樣機製造和人員重複勞動所產生的成本。同時,三維模型涵蓋著產品所有的幾何信息與非幾何製造信息,這些屬性信息會通過PDM/cPDM(產品數據管理/協同產品定義管理)這種統一的數據平台,伴隨產品整個生命周期,是實現產品協同研製、產品從設計端到製造端一體化的重要保證。
例如,美國波音公司在其737-NX和787的設計製造中,利用數字化建模技術,不但有效縮短了研製周期,大幅降低了研製成本,而且通過PDM/cPDM,有效實現了產品設計與製造環節的信息協同,從而大幅提高了生產效率。
2.生產規劃環節——工藝模擬是關鍵
在生產規劃環節,基於PDM/cPDM中所同步的產品設計環節的數據,利用虛擬模擬技術,可以對於工廠的生產線布局、設備配置、生產製造工藝路徑、物流等進行預規劃。
虛擬模擬技術廣泛應用於汽車、船舶及其他大型設備製造過程中。例如,大眾汽車公司旗下斯柯達捷克工廠,即採用西門子的Tecnomatix,利用虛擬模擬工藝路徑規劃,來減少實際生產線調整改進所需要花費的成本。
3.生產執行環節——數據採集實時通
這個環節的數字化,體現在製造執行系統(MES)與其他系統之間的互聯互通上。MES與ERP、PDM/cPDM之間的集成,能夠保證所有相關產品屬性信息從始至終保持同步,並實現實時更新。
數字化工廠(DF)的集成,首先需要強大的界面和資料庫系統,將不同複雜層次之間和不同運作功能領域之間的實際數據和模塊進行聯合使用,常見的應用有:
●布局規劃與模擬——布局確認與優化
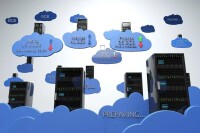
數字化工廠
●裝配過程平衡
●複雜的物流操作模擬
●機器人及複雜運動模擬
●零件加工模擬
●人力資源模擬
●人機工效模擬
●生產物流系統模擬
●控制軟體測試模擬
●生產動作控制模擬
在當今激烈的市場競爭中,製造企業已經意識到他們正面臨著巨大的時間、成本、質量等壓力。在設計部門,CAD & PDM系統的應用獲得了成功。同樣,在生產部門,ERP等相關信息系統也獲得了巨大的成功,但在解決“如何製造→工藝設計”這一關鍵環節上,大部分國內企業還沒有實現有效的計算機輔助管理機制,“數字化工廠”技術則是企業迎接21世紀挑戰的有效手段。
“數字化工廠”技術與系統作為新型的製造系統,為製造商及其供應商提供了一個製造工藝信息平台,使企業能夠對整個製造過程進行設計規劃,模擬模擬和管理,並將製造信息及時地與相關部門、供應商共享,從而實現虛擬製造和并行工程,保障生產的順利進行。在汽車行業,數字化工廠更是發揮著重要的作用。從產品設計到製造開始的工作轉換是汽車開發過程中最關鍵的步驟之一,“數字化工廠”規劃系統可以通過詳細的規劃設計和驗證預見所有的製造任務,在提高質量的同時減少設計時間,從而加速汽車開發周期;並且還可以消除浪費,減少為了完成某項任務所需的資源數量等。此外,“數字化工廠”規劃系統通過統一的數據平台,實現主機廠內部、生產線供應商、工裝夾具供應商等的并行工程。
1.全面的製造過程管理
“數字化工廠”提供了全面的製造過程管理,在實際產品生產前,在計算機模擬的環境中完成虛擬生產全部過程,生成經過“數字化工廠”驗證過的、實際生產所需的各種工藝數據和文檔。
2.工作流程
工作流程如圖2所示,下面分別詳細介紹:
(1)從設計部門獲取產品數據:
(2)從工裝工具、生產部門獲取資源數據(2D/3D):
通過系統集成,從企業的資源庫中自動下載相關資源數據;在“數字化工廠”環境中建立相關項目的資源庫。
(3)工藝規劃:
在“數字化工廠”規劃模塊中進行協同規劃或導入工藝部門已有工藝信息。工藝規劃包括:總工藝計劃、細節工藝計劃、生產計劃及產品、工藝、資源關聯及工時等工藝信息。
(4)工藝驗證、模擬:
(5)客戶化輸出:
通過系統集成和客戶化開發,輸出工藝執行文件;通過系統集成和客戶化開發,輸出生產、採購、招投標、維護、培訓等信息或將數據傳遞到現有的CAPP系統中。
3.規劃模式
整個過程始終涉及汽車主機廠和生產線供應商,這就要求各企業使用同一平台以保證實現并行工程和統一的數據規範,從而實現并行工廠。由於協作模式、控制權及平衡標準等的不同,全球不同汽車規劃體系(美系、歐系、日系等)使用的“數字化工廠”解決方案具有不同模式和本地化特點。北京迪基透科技有限公司通過多年與不同廠家的合作,逐步積累了豐富的經驗,已經探索出適合中國本地的模式,下面以汽車業的具體項目說明。
“數字化工廠”解決方案覆蓋了汽車生產的所有過程。
1.白車身解決方案
這是一個可以在網路環境下運行的解決方案,實現白車身生產線、裝配單元和工藝過程的設計、規劃、方案驗證及詳細的設計和模擬、優化,並保證信息及時更新、交流和共享。
該解決方案在製造過程的整個生命周期內支持汽車OEM的生產線設計和廠房布局,以電子化工藝過程表(eBOP)的格式定義製造過程並把他們存儲在統一的製造伺服器e-Manufacturing Server(eMS)上,這就可以在整個製造鏈上方便地讀寫、交換和協同地互動式操作;BIW Solution提供了完整的白車身製造工程的規劃、設計、管理、項目跟蹤的團隊協同製造環境;該方案主要解決白車身焊接生產線的工藝規劃、焊接管理、焊接模擬和裝焊線的布局,同時應用物流模塊對整個生產線進行物流分析和優化。
完整的工廠規劃及生產線2D/3D布局圖能使時間節省約40%,實施該方案后,顯著提高了工藝規劃效率和質量;在綜合的焊接管理方面,減少焊接信息查詢的時間75%,減少丟失焊點80%;并行工程的應用減少項目規劃的工作量約30%;並增強了主機廠與生產線供應商的協作等。
2.總裝解決方案
總裝解決方案(見圖4)主要解決總裝生產線的工藝規劃,多車型混線生產管理,複雜的物流模擬優化,根據定單的排產計劃和總裝線的布局等,支持用戶完成從生產裝配過程分析到具體裝配站點的三維可視化設計;提供對於複雜操作的三維模擬分析;提供了完整的總裝製造工程的規劃、設計、管理及項目跟蹤的團隊協同製造環境;人機工程可以用於人工裝配操作的模擬來對操作場地和裝配循環時間進行優化等;還具有用於混產規劃過程模擬、分析生產線的性能,包括產量、物流、生產線平衡、瓶頸和緩衝區大小等。
總裝解決方案在規劃過程中考慮了多種方案的優選,減少了用於驗證裝配可行性的模型數量;對複雜裝配干涉問題的模擬能早期預測和消除工程風險;可用於多車型同線混裝的工藝方案設計和排產計劃的制定。
3.發動機解決方案
該解決方案提供發動機機加工生產線和裝配線的設計、優化以及質量管理的全面的製造過程解決方案。它提供了一套強大的應用程序,對發動機和傳動系統加工生產線進行分析、規劃和模擬。該解決方案可以自動識別零件的工藝特徵、設計加工工序、自動選擇最佳的加工參數和刀具和生成NC刀具路徑乃至NC程序,並為生產線上的工位分配優化的工序。發動機解決方案流程如圖5所示。
4.物流解決方案
物流解決方案主要針對複雜製造體系進行建模模擬(如車身線,總裝線,噴漆線、發動機線等),包括:對生產線的製造能力進行評估;分析和優化生產線的緩衝區尺寸;找出瓶頸點並進行優化;制定最佳的物流控制策略;定義精確的製造系統參數等。
其中的生產線物流規劃、方案驗證包括:物流布局規劃和模擬驗證;生產線緩存區的位置設定和最佳儲存量控制;物流路徑的規劃與模擬優化;輸送鏈系統的布局,控制方案,運行策略;生產次序的優化;物流路徑的流量和瓶頸分析。運輸物流規劃、方案驗證包括:物流運輸道路路徑規劃;道路負載瓶頸流量分析;運輸車輛合理承載量計算;集貨方式和物料運輸器具規劃設計;運輸計劃(時間,車次,道路,器具)。倉儲物流規劃、方案驗證包括:存儲區布局和尺寸設計;進貨/出貨結構指令設計;物流穩定性分析;優化物流控制策略;優化集貨合貨物分配模型;優化快速貨流運轉機制;運輸設備系統方案規劃、模擬優化。
如今隨著國家對教育的投入力度加大,越來越多的中高職學校以示範校建設為契機,全力開展與企業接軌的專業建設,汲取企業的先進位造經驗,其中數控、機電、模具等專業均建設數字化工廠項目,數字化工廠項目仿照企業模式,通過PLM體驗中心、現代實訓車間、8S管理等內容建設構建出數字化工廠模型,再配合企業應用廣泛的CAD/CAPP/CAM/PDM/DNC等軟體,完成數字化工廠核心內涵建設,並由此展開教學模式改革,做到真正與企業接軌。
“數字化工廠”貫穿整個工藝設計、規劃、驗證、直至車間生產工藝整個製造過程,在實施過程需要注意系統集成方面的問題,“數字化工廠”不是一個獨立的系統,規劃時,需要與設計部門的CAD/PDM系統進行數據交換,並對設計產品進行可製造性驗證(工藝評審),同時,所有規劃還需要考慮工廠資源情況。所以,“數字化工廠”與設計系統CAD/PDM和企業資源管理系統ERP的集成是必須的。同時,“數字化工廠”還有必要把企業已有的規劃“知識”(如工時卡、焊接規範等)集成起來,整個集成的底部是PLM構架。
同時,類似於PDM系統和ERP系統,每個企業都有自己的流程和規範,考慮到很多人都在一個環境中協同工作(工藝工程師、設計工程師、零件和工具製造者、外包商、供應商以及生產工程師等),隨時會創建大量的數據,所以,“數字化工廠”規劃系統也存在客戶化定製的要求,如操作界面、流程規範、輸出等,主要是便於使用和存取等。