共找到2條詞條名為注射成型的結果 展開
- 塑料加工方法
- 穆沙R.卡邁勒等主編圖書
注射成型
塑料加工方法
塑料在注塑機加熱料筒中塑化后,由柱塞或往複螺桿注射到閉合模具的模腔中形成製品的塑料加工方法。此法能加工外形複雜、尺寸精確或帶嵌件的製品,生產效率高。大多數熱塑性塑料和某些熱固性塑料(如酚醛塑料)均可用此法進行加工。用於注塑的物料須有良好流動性,才能充滿模腔以得到製品。 20世紀70年代以來,出現了一種帶有化學反應的注射成型,稱為反應注射成型,發展很快。
注射成型是將注射機熔融的塑料,在柱塞或螺桿推力作用下進入模具,經過冷卻獲得製品的過程。
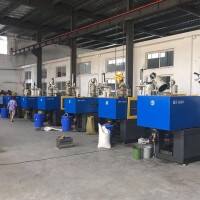
卧式注塑機
即注射成型機(見彩圖)。由注射裝置、合模裝置和注塑模具三部分組成。注塑機的規格有兩種表示法:一種是每次最大注射體積或重量,另一種是最大合模力。注塑機其他主要參數為塑化能力、注塑速率和注射壓力。
注塑機的主要部分。將塑料加熱塑化成流動狀態,加壓注射入模具。注射方式有柱塞式、預塑化式和往複螺桿式。後者(圖1)具有塑化均勻、注射壓力損失小、結構緊湊等優點,應用較廣泛。
用以閉合模具的定模和動模,並實現模具開閉動作及頂出成品。
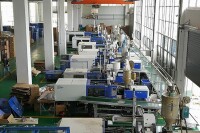
注塑車間
因加工物料而異。熱塑性塑料的注射成型包括加料、塑化、注射、保壓、冷卻、脫模等過程。熱固性塑料和橡膠的成型也包括同樣過程,但料筒溫度 較熱塑性塑料的低,注射壓力卻較高,模具是加熱的,物料注射完畢在模具中需經固化或硫化過程,然後趁熱脫膜。
注射成型是指有一定形狀的模型,通過壓力將融溶狀態的膠體注入摸腔而成型,工藝原理是:將固態的塑膠按照一定的熔點融化,通過注射機器的壓力,用一定的速度注入模具內,模具通過水道冷卻將塑膠固化而得到與設計模腔一樣的產品。
注射成型(注塑)是使熱塑性或熱固性模塑料先在加熱料筒中均勻塑化,而後由柱塞或移動螺桿推擠到閉合模具的模腔中成型的一種方法。
注射成型幾乎適用於所有的熱塑性塑料。注射成型也成功地用於成型某些熱固性塑料。注射成型的成型周期短(幾秒到幾分鐘),成型製品質量可由幾克到幾十千克,能一次成型外形複雜、尺寸精確、帶有金屬或非金屬嵌件的模塑品。因此,該方法適應性強,生產效率高。
注射成型用的注射機分為柱塞式注射機和螺桿式注射機兩大類,由注射系統、鎖模系統和塑模三大部分組成;其成型方法可分為:
(1)排氣式注射成型。排氣式注射成型應用的排氣式注射機,在料筒中部設有排氣口,亦與真空系統相連接,當塑料塑化時,真空泵可將塑料中合有的水汽、單體、揮發性物質及空氣經排氣口抽走;原料不必預乾燥,從而提高生產效率,提高產品質量。特別適用於聚碳酸酯、尼龍、有機玻璃、纖維素等易吸濕的材料成型。
(2)流動注射成型。流動注射成型可用普通移動螺桿式注射機。即塑料經不斷塑化並擠入有一定溫度的模具型腔內,塑料充滿型腔后,螺桿停止轉動,借螺桿的推力使模內物料在壓力下保持適當時間,然後冷卻定型。流動注射成型克服了生產大型製品的設備限制,製件質量可超過注射機的最大注射量。其特點是塑化的物件不是貯存在料筒內,而是不斷擠入模具中,因此它是擠出和注射相結合的一種方法。
(3)共注射成型。共注射成型是採用具有兩個或兩個以上注射單元的注射機,將不同品種或不同色澤的塑料,同時或先後注入模具內的方法。用這種方法能生產多種色彩和(或)多種塑料的複合製品,有代表性的共注射成型是雙色注射和多色注射。
(4)無流道注射成型。模具中不設置分流道,而由注射機的延伸式噴嘴直接將熔融料分注到各個模腔中的成型方法。在注射過程中,流道內的塑料保持熔融流動狀態,在脫模時不與製品一同脫出,因此製件沒有流道殘留物。這種成型方法不僅節省原料,降低成本,而且減少工序,可以達到全自動生產。
(5)反應注射成型。反應注射成型的原理是將反應原材料經計量裝置計量后泵入混合頭,在混合頭中碰撞混合,然後高速注射到密閉的模具中,快速固化,脫模,取出製品。它適於加工聚氨酯、環氧樹脂、不飽和聚酯樹脂、有機硅樹脂、醇酸樹脂等一些熱固性塑料和彈性體。主要用於聚氨酯的加工。
(6)熱固性塑料的注射成型。粒狀或團狀熱固性塑料,在嚴格控制溫度的料筒內,通過螺桿的作用,塑化成粘塑狀態,在較高的注射壓力下,物料進入一定溫度範圍的模具內交聯固化。熱固性塑料注射成型除有物理狀態變化外,還有化學變化。因此與熱塑性塑料注射成型比,在成型設備及加工工藝上存在著很大的差別。下表比較了熱固性與熱塑性塑料注射成型的差別。
熱固性與熱塑性塑料注射成型條件的比較
工藝條件 | 熱固性塑料 | 熱塑性塑料 |
料筒溫度 | 溫度低,95℃以下,溫度控制嚴格 | 溫度高,150℃以上,溫度控制不嚴格 |
料筒中停留時間 | 短 | 較 長 |
料筒加熱方式 | 液體介質(水、油) | 電加熱 |
模具溫度 | 150一200℃ | 100℃以下 |
注射壓力 | 100-200MPa | 35-140MPa |
注射量 | 注射量較小,料筒前部余料很小 | 注射量較大,料筒前部余料較多 |
注塑成型是一門工程技術,它所涉及的內容是將塑料轉變為有用並能保持原有性能的製品。注射成型的重要工藝條件是影響塑化流動和冷卻的溫度,壓力和相應的各個作用時間。
1、料筒溫度:注射模塑過程需要控制的溫度有料筒溫度,噴嘴溫度和模具溫度等。前兩程溫度主要影響塑料的塑化和流動,而後一種溫度主要是影響塑料的流動和冷卻。每一種塑料都具有不同的流動溫度,同一種塑料,由於來源或牌號不同,其流動溫度及分解溫度是有差別的,這是由於平均分子量和分子量分佈不同所致,塑料在不同類型的注射機內的塑化過程也是不同的,因而選擇料筒溫度也不相同。
2、噴嘴溫度:噴嘴溫度通常是略低於料筒最高溫度的,這是為了防止熔料在直通式噴嘴可能發生的“流涎現象”。噴嘴溫度也不能過低,否則將會造成熔料的早凝而將噴嘴堵死,或者由於早凝料注入模腔而影響製品的性能。
3、模具溫度:模具溫度對製品的內在性能和表觀質量影響很大。模具溫度的高低決定於塑料結晶性的有無、製品的尺寸與結構、性能要求,以及其它工藝條件(熔料溫度、注射速度及注射壓力、模塑周期等)。
注塑過程中壓力包括塑化壓力和注射壓力兩種,並直接影響塑料的塑化和製品質量。
1、塑化壓力:(背壓)採用螺桿式注射機時,螺桿頂部熔料在螺桿轉動後退時所受到的壓力稱為塑化壓力,亦稱背壓。這種壓力的大小是可以通過液壓系統中的溢流閥來調整的。在注射中,塑化壓力的大小是隨螺桿的轉速都不變,則增加塑化壓力時即會提高熔體的溫度,但會減小塑化的速度。此外,增加塑化壓力常能使熔體的溫度均勻,色料的混合均勻和排出熔體中的氣體。一般操作中,塑化壓力的決定應在保證製品質量優良的前提下越低越好,其具體數值是隨所用的塑料的品種而異的,但通常很少超過20㎏/c㎡。
2、注射壓力:在當前生產中,幾乎所有的注射機的注射壓力都是以柱塞或螺桿頂部對塑料所施的壓力(由油路壓力換算來的)為準的。注射壓力在注塑成型中所起的作用是,克服塑料從料筒流向型腔的流動阻力,給予熔料充模的速率以及對熔料進行壓實。
注射壓力分射膠壓力和保壓壓力,通常是1到4段射膠壓力+1到3段保壓壓力,一般保壓壓力小於射膠壓力,根據實際使用的塑膠材料進行調節,以達到佳的物理性能,外觀和尺寸要求。
完成一次注射模塑過程所需的時間稱成型周期,也稱模塑周期。它實際包括以下幾部分:
成型周期:成型周期直接影響勞動生間率和設備利用率。因此,在生產過程中應在保證質量的前提下,盡量縮短成型周期中各個有關時間。在整個成型周期中,以注射時間和冷卻時間最重要,它們對製品的質量均有決定性的影響。注射時間中的充模時間直接反比於充模速率,生產中充模時間一般約為3~5秒。
注射時間中的保壓時間就是對型腔內塑料的壓力時間,在整個注射時間內所佔的比例較大,一般約為20~120秒(特厚製件可高達5~10分鐘)。在澆口處熔料封凍之前,保壓時間的多少,對製品尺寸準確性有影響,若在以後,則無影響。保壓時間也有最惠值,已知它依賴於料溫,模溫以及主流道和澆口的大小。如果主流道和澆口的尺寸以及工藝條件都是正常的,通常即以得出製品收縮率波動範圍最小的壓力值為準。冷卻時間主要決定於製品的厚度,塑料的熱性能和結晶性能,以及模具溫等。冷卻時間的終點,應以保證製品脫模時不引起變動為原則,冷卻時間性一般約在30~120秒鐘之間,冷卻時間過長沒有必要,不僅降低生產效率,對複雜製件還將造成脫模困難,強行脫模時甚至會產生脫模應力。成型周期中的其它時間則與生產過程是否連續化和自動化以及兩化的程度等有關。