空氣分離
空氣分離
空氣分離,簡稱空分。是指應用低溫冷凍原理從空氣中分離出其組分(氧、氮和氬、氦等稀有氣體)的過程。一般先將空氣壓縮,並徠冷至很低溫度,或用膨脹方法使空氣液化,再在精餾塔中進行分離。例如當液態空氣沸騰時,比較容易揮發的氮(沸點一196℃)先氣化,氧則后氣化(沸點一183℃)。
空氣分離最常用的方法是深度冷凍法。此方法可製得氧、氮與稀有氣體,所得氣體產品的純度可達98.0%~99.9%。此外,還採用分子篩吸附法分離空氣(見變壓吸附),後者用於製取含氧70%~80%的富氧空氣。近年來,有些國家還開發了固體膜分離空氣的技術。氧氣、氮氣及氬氣、氦氣等稀有氣體用途很廣,所以空氣分離裝置廣泛用於冶金、化工、石油、機械、採礦、食品、軍事等工業部門。
1895年,德國人C.林德研究成功了一次節流循環液化空氣的方法,這是最簡單的深度冷凍循環。它採用節流膨脹和逆流換熱,稱為林德循環。1902年,德國林德公司製成了第一套林德循環單級精餾工業裝置。同年,法國人G.克勞德研究成功了帶往複式膨脹機的中壓冷凍循環液化空氣的方法,可減少冷凍消耗,稱為克勞德循環。1939年,蘇聯人∏.Л.卡皮查將離心式膨脹機用於低壓空分裝置,稱為卡皮查循環,使能耗進一步下降。目前,各國都趨向發展大型化板翅式換熱器的全低壓空分裝置,使單機制氧能力不斷提高,能耗不斷降低。中國於1953年開始製造每小時生產30m3的制氧裝置,1958年製造了每小時生產3350m3的制氧成套設備,1970年設計了板翅式換熱器的大型全低壓空分裝置,每小時制氧能力為10000m3。深度冷凍法 分為兩步,先行製冷,再加之精餾即可得到不同的氣體產品。
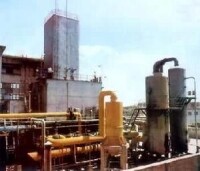
徠空氣分離
為了使空氣液化,可採用不同的深度冷凍循環裝置,主要以林德循環和克勞德循環為基礎。前者是通過節流膨脹製冷;後者除仍有節流膨脹外,還有一部分氣體在膨脹機中作等熵膨脹。氣體進行等熵膨脹時,溫度的降低要比節流膨脹大,而且能回收一部分壓縮功,所以比節流膨脹經濟。其他各種改進的深度冷凍循環,有雙壓節流循環、帶氨預冷節流循環、逐級重疊循環等。
在深度冷凍法的各種循環中,典型的流程(見圖)是先使空氣在過濾器中濾去塵埃等雜質進入壓縮機,再經分子篩凈化器除去空氣中在低溫下易凝固氣體,如水蒸氣和二氧化碳等,已凈化的空氣在第一換熱器中由產品氮氣和氧氣降溫。出第一換熱器后,空氣分成兩路:一路經第二換熱器繼續冷卻后,再經節流閥降壓;另一路經膨脹機降壓。兩路膨脹后的空氣溫度均降至103K左右,進入雙級精餾塔的下塔底部。
在深度冷凍法中,主要的分離過程是在雙級精餾塔中進行的。該塔由上、下兩塔和塔間的冷凝蒸發器組成。進入下塔底部的空氣在該處的溫度和壓力條件下,已部分液化。由於液氮沸點比液氧沸點低,因而下塔底部的液化氣體是富氧液態空氣,含氧量一般為30%~40%。下塔操作壓力應高於上塔才能使下塔頂部氮的冷凝溫度高於上塔底部液態氧的沸騰溫度(見p-V-T關係)。從而使冷凝蒸發器內熱量由管內傳向管間,並具有一定的傳熱溫差。冷凝蒸發器同時起到了下塔塔頂冷凝和上塔塔底加熱的作用。空氣在下塔由下而上經過多層塔板精餾,使易揮發組分氮的濃度逐漸提高,並在冷凝蒸發器管內冷凝成液氮。一部分液氮在下塔作迴流液;一部分收集於液氮槽,經減壓後作為上塔塔頂迴流液。下塔底部的富氧液態空氣,經節流閥進入上塔中部,與冷凝蒸發器蒸發出來的氣體逆流接觸。由此使下流液體中的含氧量由上至下不斷增加,最後積聚在冷凝蒸發器管間,含氧量可達99%以上,並不斷在此蒸發出產品氧而引出塔外。上塔塔頂引出的則是產品氮,濃度亦可達98%以上。出精餾塔的產品氧和產品氮的溫度都很低,可通過換熱器使輸入空氣降溫。
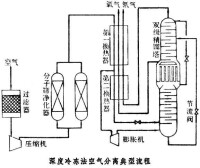
空氣分離
分子篩吸附法 基於分子篩對氮和氧的不同吸附力,空氣通過分子篩床層后,吸附相和氣相中的組成將發生變化從而達到分離的目的,由於吸附相含氮量較高,故流出氣體中含氧量較高。吸附柱足夠長時,可製得一定純度的氧氣,分子篩可採用減壓脫附的方法再生。