冷室壓鑄機
冷室壓鑄機
冷室壓鑄機是指壓射室和壓射沖頭不浸於熔融金屬中,而將定量的熔融金屬澆到壓射室中,然後進行壓射的一種壓鑄機立室冷室壓鑄機的壓射方式呈垂直放置,顯然沿襲了熱式壓鑄機的壓射方式,典型的和成熟的立式冷室壓鑄機是由捷克工程師Josef Polak於1927年發明製成的。
壓鑄技術發展至今有150餘年的歷史,與傳統的、古老的鑄造技術相比,只能說是一種年輕的工藝技術。然而,由於壓鑄技術所具有的許多特點,使壓鑄件的應用領域日益擴大,遍及各個工業門類,因而發展速度十分驚人,受到了普遍的關注。
壓鑄機是壓鑄生產中重要的基礎技術裝備,與壓鑄工藝的互存、互動關係非常突出,壓鑄工藝的改進或採用新的技術,都要有與之相應的或新型的壓鑄機作為技術支撐。所以,在壓鑄技術的發展進程中,壓鑄機始終擔負著重要的角色,起著積極的、直接的推動作用。
壓鑄技術起源於印刷工業的鉛字鑄造技術。據文獻報道,19世紀初,世界印刷工業蓬勃發展,活字(單字母的鉛字)的需求量日益增多,於是鑄字機
應運而生,較早的鑄字機是美國WilliamWing於1805年製成的。1822年,美國William Church製造了一種用活塞壓射的鑄字機。後來,美國DavidBruce於1838年製造了一種新的鑄字機,其生產效率更高,並且很快便在世界上流傳,一直延續到19世紀中葉。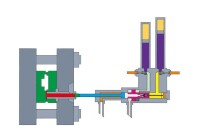
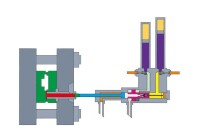
冷室壓鑄機
最早問世的冷室壓鑄機可以追溯到1920年,是由CarlRoehri率先發明並製造的,這台冷室壓鑄機就是熔爐與機器分離的,當用手工把熔爐中的熔融金屬澆入壓室(料筒)后,隨即就有一個沖頭將熔融金屬壓射入模具內,其後,在頂出鑄件的同時,壓室內多餘金屬形成的余料並隨著鑄件一起取出。可見,即使用現在的標準來說,這完全是典型的冷室壓鑄機一次工作循環的過程。隨著不斷的研究、試驗,發現冷室壓鑄機不但適用於鋁合金、鎂合金的壓鑄,也適合於銅合金的壓鑄。還有,更可以生產大型而複雜的鋅合金壓鑄件。經過一系列的改進和變革,冷室壓鑄機分為立式冷室壓鑄機和卧式冷室壓鑄機2種。
立室冷室壓鑄機的壓射方式呈垂直放置,顯然沿襲了熱式壓鑄機的壓射方式,典型的和成熟的立式冷室壓鑄機是由捷克工程師JosefPolak於1927年發明製成的。其初衷原是為了銅合金壓鑄而開發的,但後來發現同樣適用於鋁合金和鎂合金的壓鑄。從那時起,這種機器在東歐流行了30餘年之久,但因自動澆料不便、生產效率相對稍低以及維護費時等不足之處,向大型化發展的難度也很大,故後來用量逐漸減少。然而,由於這種立式冷室壓鑄機最大的特點是可以開設中心澆口,故在個別場合還保留其應有的地位。至於另一種立式冷室壓鑄機呈上下開合模的結構,其壓室置於下模內,熔融金屬從底部壓射入模具,這種機器在壓鑄電機轉子的生產中仍佔有一定的位置。
卧式冷室壓鑄機於20世紀20年代初就已開發製造,因具有較多優點,特別是一次工作循環的程序比立式冷室壓鑄機更為簡便,經過其後的十幾年的改進而漸趨定型,在歐美各國廣為流傳。
自第二次世界大戰以來,成為鋁合金、鎂合金和銅合金的壓鑄生產的典型機型。由於卧式冷室壓鑄機在大型化、單元化、集成化、自動化等方面,顯示出巨大的優勢,還有,卧式冷室壓鑄機對鋅、鋁、鎂、銅等有色金屬的壓鑄都適用,並且也適用於黑色金屬的壓鑄,因此,在壓鑄機的發展進程中,始終佔據著主導的地位。
隨著我國國民經濟持續增長的大好形勢,我國的壓鑄工業的前景定會更加輝煌,壓鑄機製造業將繼續努力,為進一步促進我國的壓鑄工業的發展做出更大的貢獻 。
在20世紀40年代的中後期,我國只有為數不多的進口壓鑄機,其中有:英國的小型氣動熱室機(上海)、捷克的Polak600型(鎖模力76t)立式冷室壓鑄機(昆明)和美國KUX的鎖模力100t的卧式冷室壓鑄機(重慶)。
20世紀50年代,我國自行設計製造出全液壓的50型卧式冷室壓鑄機,鎖模力有500kN和1000kN兩種規格。當時,也成批地進口了捷克的Polak立式冷室壓鑄機,共4種規格,最大的鎖模力為2200kN,前蘇聯的卧式冷室壓鑄機,曲肘式合模,共3種規格,最大的鎖模力為5300kN。到了20世紀60年代初,開始自行製造立式冷室壓鑄機和卧式冷室壓鑄機,即900型(鎖模力1150kN)和J1113型(鎖模力1250kN)。進入20世紀70年代,為了發展系列化產品,組織了以濟南鑄鍛機械研究所為主,有上海工藝研究所和上海壓鑄機廠參加,聯合進行一些有關的技術工作:編製壓鑄機型譜草案,初步規範了我國壓鑄機的系列的主要技術參數;設計和試製了J1125、J1140和J1163型全液壓卧式冷室壓鑄機;設計製造了1台鎖模力4000kN全液壓卧式冷室壓鑄機(上海鍛壓機床廠製造);生產了第一台熱室壓鑄機和第一台自動澆料裝置。及至20世紀80年代和90年代初,有關單位繼續完成了鎖模力16000kN以下的卧式冷室壓鑄機系列產品的開發;立式冷室壓鑄機也形成了鎖模力2500kN以下的系列產品;1986年試製出國內第一台J1163A型自動壓鑄機組;1990年開發出國內第一台柔性壓鑄單元,鎖模力為4000kN;其後的幾年裡,又將輔助裝置和參數檢測裝置加以定型並形成產品。在壓鑄機的設計工作方面,20世紀80年代,設計的壓鑄機壓射性能已接近當時的國外水平;合模機構全部採用液壓驅動、曲肘機械擴力結構取代了全液壓。而熱室壓鑄機在當時也形成了鎖模力1500kN以下的系列化產品,全立式壓鑄機也有了鎖模力3150kN以下的系列化產品。
為了進一步推動我國壓鑄機生產的發展,1980年頒布了第一個壓鑄機參數標準,1990年在重新修訂和頒布壓鑄機參數標準的同時,還頒布了第一個壓鑄機精度、技術條件標準,使壓鑄機的設計、製造和驗收有了可遵循(或參照)的依據 。
20世紀60年代,上海壓鑄機廠成為國內第一家壓鑄機專業生產廠,不久,壓鑄機的生產廠家不斷湧現,相繼有隆華、灌南、阜新等一批專業生產壓鑄機的骨幹企業。多年來,這些壓鑄機廠生產了大量的國產壓鑄機,為我國壓鑄事業的發展做出了貢獻。在大型壓鑄機方面,阜新壓鑄機廠還曾生產了鎖模力為28000kN的大型壓鑄機,為當時填補了國內的空白。
20世紀90年代,我國的壓鑄機發展更為迅速,壓鑄機的設計水平、技術參數、性能指標、機械結構、製造質量等都有不同程度的提高,有的已經達到或接近國外水平,正在向大型化、自動化和單元化進軍。在此期間,國內新的壓鑄機企業陸續嶄露頭角,其中,香港力勁公司是典型的代表,該公司開發了多項國內領先的壓鑄機機型,例如:卧式冷室壓鑄機最大空壓射速度6m/s(1997年)和8m/s(2000年初)、鎂合金熱室壓鑄機(2000年初)、勻加速壓射系統(2002年)、最大空壓射速度10m/s及多段壓射系統(2004年6月)、實時控制壓射系統(2004年8月)和鎖模力30000kN的大型壓鑄機(2004年7月)等。近年來,上海壓鑄機廠、灌南壓鑄機廠等骨幹企業都開發了最大空壓射速度為8m/s以上的卧式冷室壓鑄機和鎖模力在10000kN以上的大型壓鑄機。可見,我國正在形成一個有實力的、具有自主知識產權的壓鑄機製造業。
隨著大型壓鑄的迅速發展,實現自動化的趨勢迫在眉睫,誠然,自動化對中小型壓鑄機來說也同樣重要,於是,需要有自動化壓鑄機進行自動化壓鑄生產便很快地提到議事日程上來。初期自動化壓鑄機的組成主要是:以主機作為核心,配備澆料、噴塗、取件等3項裝置,有時加上切邊機,然後把相關程序的運作銜接起來,實現壓鑄生產過程自動化。1964年,KUX公司提出了實現自動化應解決的問題,除了壓鑄機主機配置3項機械手以外,還應考慮其他的配備和問題,包括:防止分型面金屬飛濺、合模過程的機器與模具的安全性、模具吹氣清理和噴塗、壓鑄件的取出方法、壓鑄件水冷卻並放置在傳送帶上、操作程序、生產效率、機器的構造、保溫爐的容量及金屬運輸、壓鑄件的切邊、等等,這基本上就是一個壓鑄單元的要求。
約在20世紀60年代中,機器人(Robot)開始在壓鑄工業中應用,極大地推動了自動化壓鑄機的發展,美國AllenStevens公司成為最早用機器人於壓鑄生產的壓鑄廠之一。Toshiba公司於1970年介紹了日本開發自動化壓鑄機的進展情況,據稱,日本進行全自動壓鑄機的試驗是在1961年開始的,但那時的壓鑄機的構造尚不能適合自動化的要求,工業上的配套問題也未解決,但就在不到10年的時間,日本有了自動化的壓鑄機。20世紀70年代的10年裡,壓鑄生產廠家對自動化壓鑄機的需求日漸增多,有的公司如SouthernDieCasting&Engineering公司,除了對壓鑄機自動化裝備提出建議之外,還認為必須配備好的模具才能體現出壓鑄自動化的優點。還有,歐洲同樣也加快了採用自動化壓鑄機的步伐,1983年,Weingarten公司介紹了4缸汽缸體在2500t級壓鑄機上的生產情況,當時這台壓鑄機已經採用了數字控制,同時著重對全自動壓鑄機的自動化生產進行了較為全面的闡述。可見,這個時期,壓鑄生產自動化、建立柔性單元已成為壓鑄業界全球性的新話題。
20世紀60年代以後,液壓技術、自動化控制技術、電子計算機技術、檢測技術、冶金技術、材料工程、化工技術等各種工業技術迅猛發展,新的工業產品也是日新月異,而機械製造技術和模具製造技術也在同步地迅速發展。在這種時代背景下,必然為壓鑄生產技術的發展創造了最有力的技術基礎,通過對各種技術的應用,自動化壓鑄機也就得以日益完善。當以自動化壓鑄機為核心,配置了各種輔助裝置和配備了周邊設備,並加以按預定的程序運行,便形成了壓鑄單元。卧式冷室壓鑄機上通常配置的輔助裝置包括:澆料、模具清理和噴塗、潤滑劑的壓送、取件、預熱並放置鑄入鑲件、沖頭及壓室潤滑、壓射參數檢測、壓射過程監控、鎖模力檢測,大杠自動抽出和複位、機器運動副潤滑、壓力液液面位置及溫度顯示、故障診斷及報警、快速換模、安全護欄等,有的將噴塗、取件、放入鑄入鑲件等其中的2項或3項裝置合用一台機械手;周邊設備則指:保溫爐、熔化爐、金屬液(或料錠料塊)添加和運送、鑄入鑲件加熱、壓鑄件出模后的冷卻、壓鑄件疵病部位即時簡易檢測、壓鑄件切邊、壓鑄件噴丸或光飾、壓鑄件工序間及成品的傳送、抽排煙霧等;當壓鑄工藝需要時,再配置模具溫度控制裝置、真空裝置、帶密封環的沖頭及其配用的壓室、局部加壓裝置等,此時主機操縱程序應具有與之相銜接的控制功能。
上述配置的齊全程度,與產品的壓鑄工藝和技術要求有關,也與機型大小有關。此外,每個壓鑄單元就是一個獨立的工作主體,當一個廠房內布置的都是由壓鑄單元組成的,便成為一個沒有操作工的壓鑄自動化生產線。這時,還可以將加料和輸送壓鑄件成品這2個首尾工序各自分別連接成運輸線,使廠房更加整齊。由於壓鑄生產自動化的核心是壓鑄機主機,因此,壓鑄單元和壓鑄自動化生產線的發展,便成為壓鑄機發展的重要部分。