共找到2條詞條名為金屬切削原理的結果 展開
- 專業學科
- 2005年機械工業出版社出版圖書
金屬切削原理
專業學科
《金屬切削原理》是2009年3月國防工業出版社出版的圖書,作者是龐麗君。本書主要內容包括金屬切削中切屑的形成和變形、切削力和切削功、切削熱和切削溫度、刀具的磨損機理和刀具壽命、切削振動和加工表面質量等。
《金屬切削原理》內容分為兩部分,共計16章。第1章~第10章為金屬切削原理部分,主要內容包括:基本定義、刀具材料、金屬切削過程、切削力、切削熱與切削溫度、刀具磨損和使用壽命、工件材料切削加工性、已加工表面質量、刀具合理幾何角度和切削用量的選擇、磨削。第11章~第16章為切削刀具部分,主要包括:成形車刀、銑削與銑刀、孔加工刀具、拉刀、齒輪刀具及螺紋刀具。《金屬切削原理》可作為高等院校機械類及有關專業本科、專科的教材,也可供機械類和相近專業的其他類型學校的師生和工程技術人員參考。
本書力求突出基礎理論的講解,以增強工程實踐能力的培養為目標,內容做到少而精,深淺度適中。在編寫中既注重基本知識的闡述,又聯繫生產實際,還注意介紹航空企業的先進金屬切削與刀具設計、製造及其使用技術。
全書分為金屬切削原理和刀具設計兩大部分。重點放在切削原理部分:在闡明金屬切削加工的基本定義、切削機理和切削過程中的基本現象和規律的基礎上,進一步研究工件、刀具材料和切削參數合理選擇問題,旨在提高加工表面質量和生產效率、限度地降低成本。
刀具部分:簡單介紹常用切削方法和刀具的結構特點和使用範圍;為了滿足刀具專業課與課程設計的需要,較詳細介紹了幾種專用刀具的設計原理和方法。
第1章 基本概念
1.1 概述
1.2 切削運動、加工表面和切削用量三要素
1.2.1 切削運動和工件上的加工表面
1.2.2 主運動、進給運動與合成切削運動
1.2.3 切削用量三要素
1.3 刀具幾何角度及其選擇
1.3.1 車刀切削部分的組成
1.3.2 車刀切削部分的標註角度
1.4 刀具工作角度
1.5 切削層參數
1.6 切削方式
習題
第2章 刀具材料
2.1 刀具材料應具備的性能
2.2 高速鋼
2.2.1 普通高速鋼
2.2.2 高性能高速鋼
2.2.3 粉末冶金高速鋼
2.2.4 塗層高速鋼
2.3 硬質合金
2.3.1 硬質合金的種類和性能
2.3.2 硬質合金的選用
2.3.3 其他新型硬質合金
2.4 高硬刀具材料
2.4.1 陶瓷
2.4.2 金剛石
2.4.3 立方氮化硼
習題
第3章 金屬切削過程
3.1 概述
3.2 變形區劃分及各變形區變形規律
3.2.1 切屑的形成過程
3.2.2 切削過程中的三個變形區
3.3 切削變形的表示方法
3.3.1 切削變形係數
3.3.2 相對滑移
3.3.3 相對滑移與變形係數的關係
3.4 剪切角
3.4.1 作用在切屑上的力
3.4.2 剪切角的計算
3.5 切屑的種類
3.5.1 切屑的類型
3.5.2 卷屑和斷屑
3.6 前刀面上的摩擦
3.7 積屑瘤
3.7.1 積屑瘤現象及形成原因
3.7.2 積屑瘤對切削加工的影響
3.7.3 抑制積屑瘤的措施
3.8 影響切削變形的因素
3.8.1 工件材料的影響
3.8.2 刀具幾何參數的影響
3.8.3 切削用量
習題
第4章 切削力
4.1 概述
4.2 切削力來源
4.3 切削合力、分力及切削功率
4.3.1 切削合力和分力
4.3.2 切削功率、單位切削功率和單位時間金屬切除量
4.3.3 單位切削力kc
4.4 切削力測量和經驗公式建立
4.4.1 測力儀
4.4.2 切削力的經驗公式
4.4.3 實驗數據的處理和經驗公式的建立
4.5 影響切削力的因素
4.5.1 工件材料的影響
4.5.2 切削用量的影響
4.5.3 刀具幾何參數的影響
4.5.4 其他因素的影響
習題
第5章 切削熱與切削溫度
5.1 切削熱的產生和傳出
5.2 切削溫度測量
5.3 影響切削溫度主要因素
5.3.1 切削用量對切削溫度的影響
5.3.2 工件材料對切削溫度的影響
5.3.3 刀具幾何參數對切削溫度的影響
5.3.4 其他因素的影響
習題
第6章 刀具磨損和使用壽命
6.1 刀具磨損形態與原因
6.1.1 刀具磨損形態
6.1.2 刀具磨損原因
6.2 刀具磨損過程與磨鈍標準
6.2.1 刀具磨損過程
6.2.2 刀具磨鈍標準
6.2.3 刀具使用壽命
6.3 切削用量與刀具使用壽命的關係
習題
第7章 工件材料的切削加工性
7.1 工件材料切削加工性的概念和衡量加工性的指標
7.1.1 工件材料切削加工性的概念
7.1.2 衡量加工性的指標
7.2 影響工件材料切削加工性的因素及改善途徑
7.2.1 影響工件材料切削加工性的因素
7.2.2 改善材料可加工性的途徑
7.3 材料切削加工性的綜合分析方法
7.4 航空材料切削加工性分析
7.4.1 高溫合金切削加工性分析
7.4.2 鈦合金切削加工性分析
習題
第8章 已加工表面質量
8.1 概述
8.2 已加工表面形成過程
8.3 表面粗糙度
8.3.1 理論粗糙度
8.3.2 實際粗糙度
8.3.3 影響表面粗糙度的因素
8.4 加工硬化和殘餘應力
8.4.1 加工硬化
8.4.2 已加工表面的殘餘應力
習題
第9章 刀具合理幾何角度和切削用量的選擇
第10章 磨削
第11章 成形車刀
第12章 銑削與銑刀
第13章 孔加工刀具
第14章 拉刀
第15章 齒輪刀具
第16章 螺紋刀具簡介
參考文獻
金屬切削原理的研究始於19世紀中葉。1851年,法國人M.科克基拉最早測量了鑽頭切削鑄鐵等材料時的扭矩,列出了切除單位體積材料所需功的表格。1864年,法國人若塞耳首先研究了刀具幾何參數對切削力的影響。1870年,俄國人И.Α.季梅首先解釋了切屑的形成過程,提出了金屬材料在刀具的前方不僅受擠壓而且受剪切的觀點。1896年,俄國人Α.Α.布里克斯開始將塑性變形的概念引入金屬切削。至此,切屑形成才有了較完整的解釋。1904年,英國人J.F.尼科爾森製造了第一台三向測力儀,使切削力的研究水平跨前了一大步。1907年美國人F.W.泰勒研究了切削速度對刀具壽命的影響,發表了著名的泰勒公式。1915年,俄國人Я.Γ.烏薩喬夫將熱電偶插到靠近切削刃的小孔中測得了刀具表面的溫度(常稱人工熱電偶法),並用實驗方法找出這一溫度同切削條件間的關係。1924~1926年,英國人E.G.赫伯特、美國人H.肖爾和德國人K.科特文各自獨立地利用刀具同工件間自然產生熱電勢的原理測出了平均溫度(常稱自然熱電偶法)。1938~1940年美國人H.厄恩斯特和M.E.麥錢特利用高速攝影機通過顯微鏡拍攝了切屑形成過程,並且用摩擦力分析和解釋了斷續切屑和連續切屑的形成機理。40年代以來,各國學者系統地總結和發展了前人的研究成果,充分利用近代技術和先進的測試手段,取得了很多新成就,發表了大量的論文和專著。例如,美國人S.拉馬林加姆和J.T.布萊克於1972年通過掃描電鏡利用微型切削裝置對切屑形成作了動態觀察,得到用位錯力學解釋切屑形成的實驗根據。
切屑形成機理 從力學的角度來看,根據簡化了的模型,金屬切屑的形成過程與用刀具把一疊卡片等推到 等位置(圖1)的情形相似,卡片之間相互滑移即表示金屬切削區域的剪切變形。經過這種變形以後,切屑從刀具前面上流過時又在刀、屑界面處產生進一步的摩擦變形。通常,切屑的厚度比切削厚度大,而切屑的長度比切削長度短,這種現象就叫切屑變形。金屬被刀具前面所擠壓而產生的剪切變形是金屬切削過程的特徵。由於工件材料、刀具和切削條件不同,切屑的變形程度也不同,因此可以得到各種類型的切屑(圖2)。
研究金屬切削加工過程中刀具與工件之間相互作用和各自的變化規律的一門學科。
在用低、中速連續切削一般鋼材或其他塑性材料時,切屑同刀具前面之間存在著摩擦,如果切屑上緊靠刀具前面的薄層在較高壓強和溫度的作用下,同切屑基體分離而粘結在刀具前面上,再經層層重疊粘結,在刀尖附近往往會堆積成一塊經過劇烈變形的楔狀切屑材料,叫做積屑瘤。積屑瘤的硬度較基體材料高一倍以上,實際上可代替刀刃切削。積屑瘤的底部較穩定,頂部同工件和切屑沒有明顯的分界線,容易破碎和脫落,一部分隨切屑帶走,一部分殘留在加工表面上,從而使工件變得粗糙。所以在精加工時一定要設法避免或抑制積屑瘤的形成。積屑瘤的產生、成長和脫落是一個周期性的動態過程(據測定,它的脫落頻率為),它使刀具的實際前角和切削深度也隨之發生變化,引起切削力波動,影響加工穩定性。在一般情況下,當切削速度很低或很高時,因沒有產生積屑瘤的必要條件(較大的切屑與刀具前面間的摩擦力和一定的溫度),不產生積屑瘤。
切削力
切削時刀具的前面和後面上都承受法向力和摩擦力,這些力組成合力F,在外圓車削時,一般將這個切削合力F分解成三個互相垂直的分力(圖3):切向力──它在切削速度方向上垂直於刀具基面,常稱主切削力;徑向力 ──在平行於基面的平面內,與進給方向垂直,又稱推力;軸向力 ──在平行於基面的平面內,與進給方向平行,又稱進給力。一般情況下, 最大, 和F 較小,由於刀具的幾何參數、刃磨質量和磨損情況的不同和切削條件的改變, 、 對 的比值在很大的範圍內變化。切削過程中實際切削力的大小,可以利用測力儀測出。測力儀的種類很多,較常用的是電阻絲式和壓電晶體式測力儀。測力儀經過標定以後就可測出切削過程中各個分力的大小。
車削時的切削功率主要為主切削力 所消耗,可用下式計算:
式中 為主切削力(牛);為切削速度(米/分)。
切削熱
切削金屬時,由於切屑剪切變形所作的功和刀具前面、後面摩擦所作的功都轉變為熱,這種熱叫切削熱。使用切削液時,刀具、工件和切屑上的切削熱主要由切削液帶走;不用切削液時,切削熱主要由切屑、工件和刀具帶走或傳出,其中切屑帶走的熱量最大,傳向刀具的熱量雖小,但前面和後面上的溫度卻影響著切削過程和刀具的磨損情況,所以了解切削溫度的變化規律是十分必要的。
切削溫度
切削過程中切削區各處的溫度是不同的,形成一個溫度場(圖4), 這個溫度場影響切屑變形、積屑瘤的大小、加工表面質量、加工精度和刀具的磨損等,還影響切削速度的提高。一般說來,切削區的金屬經過剪切變形以後成為切屑,隨之又進一步與刀具前面發生劇烈摩擦,所以溫度場中溫度分佈的最高點不是在正壓力最大的刃口處,而是在前面上距刃口一段距離的地方。切削區的溫度分佈情況,須用人工熱電偶研究金屬切削加工過程中刀具與工件之間相互作用和各自的變化規律的一門學科。在設計機床和刀具、制訂機器零件的切削工藝及其定額、合理地使用刀具和機床以及控制切削過程時,都要利用金屬切削原理的研究成果,使機器零件的加工達到經濟、優質和高效率的目的。
刀具磨損
刀具在切削時的磨損是切削熱和機械摩擦所產生的物理作用和化學作用的綜合結果。刀具磨損表現為在刀具後面上出現的磨損帶、缺口和崩刃等,前面上常出現的月牙窪狀的磨損,副後面上有時出現的氧化坑和溝紋狀磨損等(圖5)當這些磨損擴展到一定程度以後就引起刀具失效,不能繼續使用。刀具逐漸磨損的因素,通常有磨料磨損、粘著磨損、擴散磨損、氧化磨損、熱裂磨損和塑性變形等。在不同的切削條件下,尤其是在不同切削速度的條件下,刀具受上述一種或幾種磨損機理的作用。例如,在較低切削速度下,刀具一般都因磨料磨損或粘著磨損而破損;在較高速度下,容易產生擴散磨損、氧化磨損和塑性變形。
刀具壽命
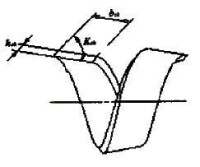
切屑軸截面參數計算公式
式中為刀具壽命(分);為切削速度(米/分);和為常數(與切削條件有關)。
生產中常根據加工條件按最低生產成本或最高生產率的原則,來確定刀具壽命和擬定工時定額。
切削加工性
指零件被切削加工成合格品的難易程度。它根據具體加工對象和要求,可用刀具壽命的長短、加工表面質量的好壞、金屬切除率的高低、切削功率的大小和斷屑的難易程度等作為判據。在生產和實驗研究中,常以作為某種材料的切削加工性的指標,它的含義是:當刀具壽命為分鐘時,切削該材料所允許的切削速度。 越高,表示加工性越好, 一般取火10分鐘。
加工表面質量
通常包括表面粗糙度、加工硬化、殘餘應力、表面裂紋和金相顯微組織變化等。切削加工中影響加工表面質量的因素很多,例如刀具的刀尖圓弧半徑、進給量和積屑瘤等是影響表面粗糙度的主要因素;刀具的刃口鈍圓半徑和磨損及切削條件是影響加工硬化和殘餘應力的主要因素。因此,生產中常通過改變刀具的幾何形狀和選擇合理的切削條件來提高加工表面質量。
切削振動
切削過程中,刀具與工件之間經常會產生自由振動、強迫振動或自激振動(顫振)等類型的機械振動。自由振動是由機床零部件受到某些突然衝擊所引起,它會逐漸衰減。強迫振動是由機床內部或外部持續的交變干擾力(如不平衡的機床運動件、斷續切削等)所引起,它對切削產生的影響取決於干擾力的大小及其頻率。自激振動是由於刀具與工件之間受到突然干擾力(如切削中遇到硬點)而引起初始振動,使刀具前角、后角和切削速度等發生變化,以及產生振型耦合等,並從穩態作用的能源中獲得周期性作用的能源,促進並維持振動。通常,根據切削條件可能產生各種原生型自激振動,從而在加工表面上留下的振紋,又會產生更為常見的再生型自激振動。上述各種振動通常都會影響加刀表面質量,降低機床和刀具的壽命,降低生產率,並引起雜訊,極為有害,必須設法消除或減輕。
切屑控制
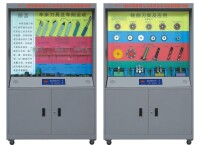
應用
在設計和使用機床和刀具時,需要應用切削原理中有關切削力、切削溫度和刀具切削性能方面的數據。例如,在確定機床主軸的最大扭矩和剛性等基本參數時,要應用切削力的數據;在發展高切削性能的新材料時,需掌握刀具磨損和破損的規律;在切削加工中分析熱變形對加工精度的影響時,要研究切削溫度及其分佈;在自動生產線和數字控制機床上,為了使機床能正常地穩定工作,甚至實現無人化操作,更要應用有關切屑形成及其控制方面的研究成果,並在加工中實現刀具磨損的自動補償和刀具破損的自動報警。為此,各國研製了品種繁多的在線檢測刀具磨損和破損的感測器,其中大多數是利用切削力或扭矩、切削溫度、刀具磨損作為感測信號。此外,為了充分利用機床,提高加工經濟性和發展計算機輔助製造(),常需要應用切削條件、刀具幾何形狀和刀具壽命等的優化數據。因此,金屬切削原理這門學科在生產中的應用日益廣泛,各國都通過切削試驗或現場採集積累了大量的切削數據,並用數學模型來表述刀具壽命、切削力、功率和加工表面粗糙度等同切削條件之間的關係,然後存入計算機,建立金屬切削資料庫或編製成切削數據手冊,供用戶查用。