煤液化
煤液化
煤液化是把固體煤炭通過化學加工過程,使其轉化成為液體燃料、化工原料和產品的先進潔凈煤技術。根據不同的加工路線,煤炭液化可分為直接液化和間接液化兩大類,煤的液化屬於化學變化。
根據不同的加工路線,煤炭液化可分為直接液化和間接液化兩大類。直接液化意味著碳化和氫化
煤的液化方法主要分為煤的直接液化和煤的間接液化兩大類。
(1)煤直接液化煤在氫氣和催化劑作用下,通過加氫裂化轉變為液體燃料的過程稱為直接液化。裂化是一種使烴類分子分裂為幾個較小分子的反應過程。因煤直接液化過程主要採用加氫手段,故又稱煤的加氫液化法。
(2)煤間接液化間接液化是以煤為原料,先氣化製成合成氣,然後,通過催化劑作用將合成氣轉化成烴類燃料、醇類燃料和化學品的過程。
用氫化過程將煤液化是德國在20世紀20年代發明的,將煤粉和重油混合,在催化劑的作用下,在400 °C至5000 °C溫度和20到70兆帕的條件下反應:nC + (n+ 1) H2→ CnH2n+ 2
在第二次世界大戰期間,德國由於缺乏燃油,廣泛應用這種方法生產燃油和潤滑油,直到20世紀80年代。現代由於尋多種新型催化劑的應用,這種方法越來越成熟,被許多國家採納。
間接液化就是先把煤進行氣化,生成水煤氣,再合成乙烷、乙醇等燃料,也可以進一步合成燃油。
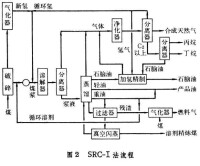
煤直接液化示意圖
煤直接液化技術是由德國人於1913年發現的,並於二戰期間在德國實現了工業化生產。德國先後有12套煤炭直接液化裝置建成投產,到1944年,德國煤炭直接液化工廠的油品生產能力已達到423萬噸/年。二戰後,中東地區大量廉價石油的開發,煤炭直接液化工廠失去競爭力並關閉。
徠70年代初期,由於世界範圍內的石油危機,煤炭液化技術又開始活躍起來。日本、德國、美國等工業發達國家,在原有基礎上相繼研究開發出一批煤炭直接液化新工藝,其中的大部分研究工作重點是降低反應條件的苛刻度,從而達到降低煤液化油生產成本的目的。世界上有代表性的直接液化工藝是日本的NEDOL工藝、德國的IGOR工藝和美國的HTI工藝。這些新直接液化工藝的共同特點是,反應條件與老液化工藝相比大大緩和,壓力由40MPa降低至17~30MPa,產油率和油品質量都有較大幅度提高,降低了生產成本。到目前為止,上述國家均已完成了新工藝技術的處理煤100t/d級以上大型中間試驗,具備了建設大規模液化廠的技術能力。煤炭直接液化作為曾經工業化的生產技術,在技術上是可行的。國外沒有工業化生產廠的主要原因是,在發達國家由於原料煤價格、設備造價和人工費用偏高等導致生產成本偏高,難以與石油競爭。
煤的分子結構很複雜,一些學者提出了煤的複合結構模型,認為煤的有機質可以設想由以下四個部分複合而成。第一部分,是以化學共價鍵結合為主的三維交聯的大分子,形成不溶性的剛性網路結構,它的主要前身物來自維管植物中以芳族結構為基礎的木質素。第二部分,包括相對分子質量一千至數千,相當於瀝青質和前瀝青質的大型和中型分子,這些分子中包含較多的極性官能團,它們以各種物理力為主,或相互締合,或與第一部分大分子中的極性基團相締合,成為三維網路結構的一部分。第三部分,包括相對分子質量數百至一千左右,相對於非烴部分,具有較強極性的中小型分子,它們可以分子的形式處於大分子網路結構的空隙之中,也可以物理力與第一和第二部分相互締合而存在。第四部分,主要為相對分子質量小於數百的非極性分子,包括各種飽和烴和芳烴,它們多呈遊離態而被包絡、吸附或固溶於由以上三部分構成的網路之中。
煤複合結構中上述四個部分的相對含量視煤的類型、煤化程度、顯微組成的不同而異。上述複雜的煤化學結構,是具有不規則構造的空間聚合體,可以認為它的基本結構單元是以縮合芳環為主體的帶有側鏈和多種官能團的大分子,結構單元之間通過橋鍵相連,作為煤的結構單元的縮合芳環的環數有多有少,有的芳環上還有氧、氮、硫等雜原子,結構單元之間的橋鍵也有不同形態,有碳碳鍵、碳氧鍵、碳硫鍵、氧氧鍵等。
從煤的元素組成看,煤和石油的差異主要是氫碳原子比不同。煤的氫碳原子比為0.2~1,而石油的氫碳原子比為1.6~2,煤中氫元素比石油少得多。
煤在一定溫度、壓力下的加氫液化過程基本分為三大步驟。
(1)當溫度升至300℃以上時,煤受熱分解,即煤的大分子結構中較弱的橋鍵開始斷裂,打碎了煤的分子結構,從而產生大量的以結構單元為基體的自由基碎片,自由基的相對分子質量在數百範圍。
(2)在具有供氫能力的溶劑環境和較高氫氣壓力的條件下、自由基被加氫得到穩定,成為瀝青烯及液化油分子。能與自由基結合的氫並非是分子氫(H2),而應是氫自由基,即氫原子,或者是活化氫分子,氫原子或活化氫分子的來源有:①煤分子中碳氫鍵斷裂產生的氫自由基;②供氫溶劑碳氫鍵斷裂產生的氫自由基;③氫氣中的氫分子被催化劑活化;④化學反應放出的氫。當外界提供的活性氫不足時,自由基碎片可發生縮聚反應和高溫下的脫氫反應,最後生成固體半焦或焦炭。
(3)瀝青烯及液化油分子被繼續加氫裂化生成更小的分子。
直接液化典型的工藝過程主要包括煤的破碎與乾燥、煤漿製備、加氫液化、固液分離、氣體凈化、液體產品分餾和精製,以及液化殘渣氣化製取氫氣等部分。氫氣製備是加氫液化的重要環節,大規模製氫通常採用煤氣化及天然氣轉化。液化過程中,將煤、催化劑和循環油製成的煤漿,與製得的氫氣混合送入反應器。在液化反應器內,煤首先發生熱解反應,生成自由基“碎片”,不穩定的自由基“碎片”再與氫在催化劑存在條件下結合,形成分子量比煤低得多的初級加氫產物。出反應器的產物構成十分複雜,包括氣、液、固三相。氣相的主要成分是氫氣,分離后循環返回反應器重新參加反應;固相為未反應的煤、礦物質及催化劑;液相則為輕油(粗汽油)、中油等餾份油及重油。液相餾份油經提質加工(如加氫精製、加氫裂化和重整)得到合格的汽油、柴油和航空煤油等產品。重質的液固淤漿經進一步分離得到重油和殘渣,重油作為循環溶劑配煤漿用。
煤直接液化粗油中石腦油餾分約佔15%-30%,且芳烴含量較高,加氫后的石腦油餾分經過較緩和的重整即可得到高辛烷值汽油和豐富的芳烴原料,汽油產品的辛烷值、芳烴含量等主要指標均符合相關標準(GB17930-1999),且硫含量大大低於標準值(≤0.08%),是合格的優質潔凈燃料。中油約佔全部直接液化油的50%-60%,芳烴含量高達70%以上,經深度加氫后可獲得合格柴油。重油餾分一般占液化粗油的10%-20%,有的工藝該餾分很少,由於雜原子、瀝青烯含量較高,加工較困難,可以作為燃料油使用。煤液化中油和重油混合經加氫裂化可以製取汽油,並在加氫裂化前進行深度加氫以除去其中的雜原子及金屬鹽。
(1)液化油收率高。例如採用HTI工藝,神華煤的油收率可高達63%-68%;
(2)煤消耗量小,一般情況下,1噸無水無灰煤能轉化成半噸以上的液化油,加上制氫用煤,約3-4噸原料產1噸液化油。
(3)餾份油以汽、柴油為主,目標產品的選擇性相對較高;
(4)油煤漿進料,設備體積小,投資低,運行費用低;
(5)反應條件相對較苛刻,如德國老工藝液化壓力甚至高達70MPa,現代工藝如IGOR、HTI、NEDOL等液化壓力也達到17-30MPa,液化溫度430-470℃;
(6)出液化反應器的產物組成較複雜,液、固兩相混合物由於粘度較高,分離相對困難;
(7)氫耗量大,一般在6%-10%,工藝過程中不僅要補充大量新氫,還需要循環油作供氫溶劑,使裝置的生產能力降低。
我國從70年代末開始煤炭直接液化技術研究。煤炭科學研究總院北京煤化所對近30個煤種在0.1噸/日裝置上進行了50多次運轉試驗,開發了高活性的煤液化催化劑,進行了煤液化油的提質加工研究,完成了將煤的液化粗油加工成合格的汽油、柴油和航空煤油的試驗。“九五”期間分別同德國、日本、美國有關部門和公司合作完成了神華、黑龍江依蘭、雲南先鋒建設煤直接液化廠的預可行性研究。
在開發形成“神華煤直接液化新工藝”的基礎上,神華集團建成了投煤量6t/d的工藝試驗裝置,於2004年10月開始進行溶劑加氫、熱油連續運轉,並於2004年12月16日投煤,進行了23小時投料試運轉,打通了液化工藝,取得開發成果。
經過近一年的時間進行裝置的改造,裝置於2005年10月29日開始第二次投煤試驗,經過近18天(412小時)的連續平穩運轉,完成了預定的試驗計劃,於11月15日順利停車,試驗取得了成功。經統計,試驗期間共配製煤漿206噸,共消耗原煤105噸(其中乾燥無灰基煤85噸);共製備863催化劑油漿44噸。
神華集團公司位於鄂爾多斯的使用自己技術的直接液化項目的先期工程於2004年8月25日正式開工建設。
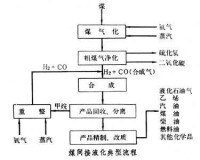
煤間接液化示意圖
1923年,德國化學家首先開發出了煤炭間接液化技術。40年代初,為了滿足戰爭的需要,德國曾建成9個間接液化廠。二戰以後,同樣由於廉價石油和天然氣的開發,上述工廠相繼關閉和改作它用。之後,隨著鐵系化合物類催化劑的研製成功、新型反應器的開發和應用,煤間接液化技術不斷進步,但由於煤炭間接液化工藝複雜,初期投資大,成本高,因此除南非之外,其它國家對煤炭間接液化的興趣相對於直接液化來說逐漸淡弱。
煤炭間接液化技術主要有三種,即的南非的薩索爾(Sasol)費托合成法、美國的Mobil甲醇制汽油法和正在開發的直接合成法。煤間接液化技術在國外已實現商業化生產,全世界共有3家商業生產廠正在運行,它們分別是南非的薩索爾公司和紐西蘭、馬來西亞的煤炭間接液化廠。紐西蘭煤炭間接液化廠採用的是Mobil液化工藝,但只進行間接液化的第一步反應,即利用天然氣或煤氣化合成氣生產甲醇,而沒有進一步以甲醇為原料生產燃料油和其它化工產品,生產能力1.25萬桶/天。馬來西亞煤炭間接液化廠所採用的液化工藝和南非薩索爾公司相似,但不同的是它以天然氣為原料來生產優質柴油和煤油,生產能力為50萬噸/年。因此,從嚴格意義上說,南非薩索爾公司是世界上唯一的煤炭間接液化商業化生產企業。
南非薩索爾公司成立於50年代初,1955年公司建成第一座由煤生產燃料油的Sasol-1廠。70年代石油危機后,1980年和1982年又相繼建成Sasol-2廠和Sasol-3廠。3個煤炭間接液化廠年加工原煤約4600萬t,產品總量達768萬t,主要生產汽油、柴油、蠟、氨、乙烯、丙烯、聚合物、醇、醛等113種產品,其中油品佔60%,化工產品佔40%。該公司生產的汽油和柴油可滿足南非28%的需求量,其煤炭間接液化技術處於世界領先地位。
此外,美國SGI公司於80年代末開發出了一種新的煤炭液化技術,即LFC(煤提油)技術。該技術是利用低溫乾餾技術,從次煙煤或褐煤等非煉焦煤中提取固態的高品質潔凈煤和液態可燃油。美國SGI公司於1992年建成了一座日處理能力為1000t的次煙煤商業示範廠。
費托合成(Fisher-Tropsch Sythesis)合成是指CO在固體催化劑作用下非均相氫化生成不同鏈長的烴類(C1~C25)和含氧化合物的反應。該反應於1923年由F.Fischer和H.Tropsch首次發現后經Fischer等人完善,並於1936年在魯爾化學公司實現工業化,費托(F-T)合成因此而得名。
費托合成反應化學計量式因催化劑的不同和操作條件的差異將導致較大差別,但可用以下兩個基本反應式描述。
(1)烴類生成反應
CO+2H2→(-CH2-)+H2O
(2)水氣變換反應
CO+ H2O→H2+ CO2
由以上兩式可得合成反應的通用式:
2CO+H2→(-CH2-)+ CO2
由以上兩式可以推出烷烴和烯烴生成的通用計量式如下:
(3)烷烴生成反應
nCO+(2n+1)H2→CnH2n+2+nH2O
2nCO+(n+1)H2→CnH2n+2+nCO2
3nCO+(n+1)H2O→CnH2n+2+(2n+1)CO2
nCO2+(3n+1)H2→CnH2n+2+2nH2O
(4)烯烴生成反應
nCO+2nH2→CnH2n+nH2O
2nCO+nH2→CnH2n+nCO2
3nCO+nH2O→CnH2n+2nCO2
nCO2+3nH2→CnH2n+2nH2O
間接液化的主要反應就是上面的反應,由於反應條件的不同,還有甲烷生成反應,醇類生成反應(生產甲醇就需要此反應),醛類生成反應等等。
煤間接液化可分為高溫合成與低溫合成兩類工藝。高溫合成得到的主要產品有石腦油、丙烯、α-烯烴和C14~C18烷烴等,這些產品可以用作生產石化替代產品的原料,如石腦油餾分製取乙烯、α-烯烴製取高級洗滌劑等,也可以加工成汽油、柴油等優質發動機燃料。低溫合成的主要產品是柴油、航空煤油、蠟和LPG等。煤間接液化製得的柴油十六烷值可高達70,是優質的柴油調兌產品。
煤間接液化制油工藝主要有Sasol工藝、Shell的SMDS工藝、Syntroleum技術、Exxon的AGC-21技術、Rentech技術。己工業化的有南非的Sasol的漿態床、流化床、固定床工藝和Shell的固定床工藝。國際上南非Sasol和Shell馬來西亞合成油工廠已有長期運行經驗。
典型煤基F-T合成工藝包括:煤的氣化及煤氣凈化、變換和脫碳;F-T合成反應;油品加工等3個純“串聯”步驟。氣化裝置產出的粗煤氣經除塵、冷卻得到凈煤氣,凈煤氣經CO寬溫耐硫變換和酸性氣體(包括H2和CO2等)脫除,得到成分合格的合成氣。合成氣進入合成反應器,在一定溫度、壓力及催化劑作用下,H2S和CO轉化為直鏈烴類、水以及少量的含氧有機化合物。生成物經三相分離,水相去提取醇、酮、醛等化學品;油相採用常規石油煉製手段(如常、減壓蒸餾),根據需要切割出產品餾份,經進一步加工(如加氫精製、臨氫降凝、催化重整、加氫裂化等工藝)得到合格的油品或中間產品;氣相經冷凍分離及烯烴轉化處理得到LPG、聚合級丙烯、聚合級乙烯及中熱值燃料氣。
(1)合成條件較溫和,無論是固定床、流化床還是漿態床,反應溫度均低於350℃,反應壓力2.0-3.0MPa;
(2)轉化率高,如SASOL公司SAS工藝採用熔鐵催化劑,合成氣的一次通過轉化率達到60%以上,循環比為2.0時,總轉化率即達90%左右。Shell公司的SMDS工藝採用鈷基催化劑,轉化率甚至更高;
(3)受合成過程鏈增長轉化機理的限制,目標產品的選擇性相對較低,合成副產物較多,正構鏈烴的範圍可從C1至C100;隨合成溫度的降低,重烴類(如蠟油)產量增大,輕烴類(如CH4、C2H4、C2H6、……等)產量減少;
(4)有效產物-CH2-的理論收率低,僅為43.75%,工藝廢水的理論產量卻高達56.25%;
(5)煤消耗量大,一般情況下,約5~7t原煤產1t成品油。
(6)反應物均為氣相,設備體積龐大,投資高,運行費用高;
(7)煤基間接液化全部依賴於煤的氣化,沒有大規模氣化便沒有煤基間接液化。
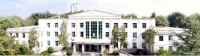
山西煤化所辦公樓
“七五”期間,山西煤化所開的煤基合成汽油技術被列為國家重點科技攻關項目。1989年在代縣化肥廠完成了小型實驗。“八五”期間,國家和山西省政府投資2000多萬元,在晉城化肥廠建立了年產2000噸汽油的工業試驗裝置,生產出了90號汽油。在此基礎上,提出了年產10萬噸合成汽油裝置的技術方案。2001年,國家863計劃和中科院聯合啟動了“煤變油”重大科技項目。中科院山西煤化所承擔了這一項目的研究,科技部投入資金6000萬,省政府投入1000萬和本地企業的支持,經過一年多攻關,千噸級漿態床中試平台在2002年9月實現了第一次試運轉,併合成出第一批粗油品,低溫漿態合成油可以獲得約70%的柴油,十六烷值達到70以上,其它產品有LPG(約5%~10%)、含氧化合物等。其核心技術費托合成的催化劑、反應器和工藝工程也取得重大突破。
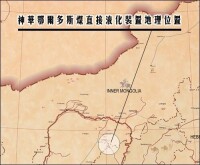
神華鄂爾多斯煤直接液化裝置地理位置
在技術開發的同時,國內煤炭企業對引進成熟技術、建設煤間接液化工廠做了大量工作。平頂山煤業集團、寧夏煤業集團以及神華集團就建設間接液化商業化示範工廠進行了煤種評價試驗和建廠預可行性研究,並就引進技術、投融資、立項等做了大量前期工作,項目正在論證階段。