迴流焊
焊接工藝的一種
迴流焊技術在電子製造領域並不陌生,我們電腦內使用的各種板卡上的元件都是通過這種工藝焊接到線路板上的,這種設備的內部有一個加熱電路,將空氣或氮氣加熱到足夠高的溫度后吹向已經貼好元件的線路板,讓元件兩側的焊料融化后與主板粘結。這種工藝的優勢是溫度易於控制,焊接過程中還能避免氧化,製造成本也更容易控制。
由於電子產品PCB板不斷小型化的需要,出現了片狀元件,傳統的焊接方法已不能適應需要。起先,只在混合集成電路板組裝中採用了迴流焊工藝,組裝焊接的元件多數為片狀電容、片狀電感,貼裝型晶體管及二極體等。隨著SMT整個技術發展日趨完善,多種貼片元件(SMC)和貼裝器件(SMD)的出現,作為貼裝技術一部分的迴流焊工藝技術及設備也得到相應的發展,其應用日趨廣泛,幾乎在所有電子產品領域都已得到應用。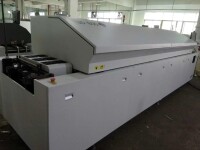
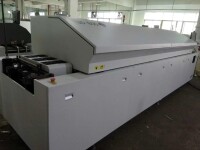
迴流焊
根據產品的熱傳遞效率和焊接的可靠性的不斷提升,迴流焊大致可分為五個發展階段。
熱板傳導迴流焊設備:熱傳遞效率最慢,5-30W/m2K(不同材質的加熱效率不一樣),有陰影效應。
紅外熱輻射迴流焊設備:熱傳遞效率慢,5-30W/m2K(不同材質的紅外輻射效率不一樣),有陰影效應,元器件的顏色對吸熱量有大的影響。
熱風迴流焊設備:熱傳遞效率比較高,10-50W/m2K,無陰影效應,顏色對吸熱量沒有影響。
氣相迴流焊接系統:熱傳遞效率高,200-300W/m2K,無陰影效應,焊接過程需要上下運動,冷卻效果差。
真空蒸汽冷凝焊接(真空汽相焊)系統:密閉空間的無空洞焊接,熱傳遞效率最高,300W-500W/m2K。焊接過程保持靜止無震動。冷卻效果優秀,顏色對吸熱量沒有影響。
熱板傳導迴流焊:這類迴流焊爐依靠傳送帶或推板下的熱源加熱,通過熱傳導的方式加熱基板上的元件,用於採用陶瓷(Al2O3)基板厚膜電路的單面組裝,陶瓷基板上只有貼放在傳送帶上才能得到足夠的熱量,其結構簡單,價格便宜。中國的一些厚膜電路廠在80年代初曾引進過此類設備。
紅外(IR)迴流焊爐:此類迴流焊爐也多為傳送帶式,但傳送帶僅起支托、傳送基板的作用,其加熱方式主要依紅外線熱源以輻射方式加熱,爐膛內的溫度比前一種方式均勻,網孔較大,適於對雙面組裝的基板進行迴流焊接加熱。這類迴流焊爐可以說是迴流焊爐的基本型。在中國使用的很多,價格也比較便宜。
氣相迴流焊接:氣相迴流焊接又稱氣相焊(VaporPhaseSoldering,VPS),亦名凝熱焊接(condensationsoldering)。加熱碳氟化物(早期用FC-70氟氯烷系溶劑),熔點約215℃,沸騰產生飽和蒸氣,爐子上方與左右都有冷凝管,將蒸氣限制在爐膛內,遇到溫度低的待焊PCB組件時放出汽化潛熱,使焊錫膏融化后焊接元器件與焊盤。美國最初將其用於厚膜集成電路(IC)的焊接,氣柏潛熱釋放對SMA的物理結構和幾何形狀不敏感,可使組件均勻加熱到焊接溫度,焊接溫度保持一定,無需採用溫控手段來滿足不同溫度焊接的需要,VPS的氣相中是飽和蒸氣,含氧量低,熱轉化率高,但溶劑成本高,且是典型臭氧層損耗物質,因此應用上受到極大的限制,國際社會現今基本不再使用這種有損環境的方法。
熱風迴流焊:熱風式迴流焊爐通過熱風的層流運動傳遞熱能,利用加熱器與風扇,使爐內空氣不斷升溫並循環,待焊件在爐內受到熾熱氣體的加熱,從而實現焊接。熱風式迴流焊爐具有加熱均勻、溫度穩定的特點,PCB的上、下溫差及沿爐長方向的溫度梯度不容易控制,一般不單獨使用。自20世紀90年代起,隨著SMT應用的不斷擴大與元器件的進一步小型化,設備開發製造商紛紛改進加熱器的分佈、空氣的循環流向,並增加溫區至8個、10個,使之能進一步精確控制爐膛各部位的溫度分佈,更便於溫度曲線的理想調節。全熱風強制對流的迴流焊爐經過不斷改進與完善,成為了SMT焊接的主流設備。
紅外線+熱風迴流焊:20世紀90年代中期,在日本迴流焊有向紅外線+熱風加熱方式轉移的趨勢。它足按30%紅外線,70%熱風做熱載體進行加熱。紅外熱風迴流焊爐有效地結合了紅外迴流焊和強制對流熱風迴流焊的長處,是21世紀較為理想的加熱方式。它充分利用了紅外線輻射穿透力強的特點,熱效率高、節電,同時又有效地克服了紅外迴流焊的溫差和遮蔽效應,彌補了熱風迴流焊對氣體流速要求過快而造成的影響。
這類迴流焊爐是在IR爐的基礎上加上熱風使爐內溫度更加均勻,不同材料及顏色吸收的熱量是不同的,即Q值是不同的,因而引起的溫升AT也不同。例如,lC等SMD的封裝是黑色的酚醛或環氧,而引線是白色的金屬,單純加熱時,引線的溫度低於其黑色的SMD本體。加上熱風后可使溫度更加均勻,而克服吸熱差異及陰影不良情況,紅外線+熱風迴流焊爐在國際上曾使用得很普遍。
由於紅外線在高低不同的零件中會產生遮光及色差的不良效應,故還可吹入熱風以調和色差及輔助其死角處的不足,所吹熱風中又以熱氮氣最為理想。對流傳熱的快慢取決於風速,但過大的風速會造成元器件移位並助長焊點的氧化,風速控制在1.Om/s~1.8ⅡI/S為宜。熱風的產生有兩種形式:軸向風扇產生(易形成層流,其運動造成各溫區分界不清)和切向風扇產生(風扇安裝在加熱器外側,產生面板渦流而使各個溫區可精確控制)。
熱絲迴流焊:熱絲迴流焊是利用加熱金屬或陶瓷直接接觸焊件的焊接技術,通常用在柔性基板與剛性基板的電纜連接等技術中,這種加熱方法一般不採用錫膏,主要採用鍍錫或各向異性導電膠,並需要特製的焊嘴,因此焊接速度很慢,生產效率相對較低。
熱氣迴流焊:熱氣迴流焊指在特製的加熱頭中通過空氣或氮氣,利用熱氣流進行焊接的方法,這種方法需要針對不同尺寸焊點加工不同尺寸的噴嘴,速度比較慢,用於返修或研製中。
激光迴流焊,光束迴流焊:激光加熱迴流焊是利用激光束良好的方向性及功率密度高的特點,通過光學系統將激光束聚集在很小的區域內,在很短的時間內使被加熱處形成一個局部的加熱區,常用的激光有C02和YAG兩種,是激光加熱迴流焊的工作原理示意圖。
激光加熱迴流焊的加熱,具有高度局部化的特點,不產生熱應力,熱衝擊小,熱敏元器件不易損壞。但是設備投資大,維護成本高。
感應迴流焊:感應迴流焊設備在加熱頭中採用變壓器,利用電感渦流原理對焊件進行焊接,這種焊接方法沒有機械接觸,加熱速度快;缺點是對位置敏感,溫度控制不易,有過熱的危險,靜電敏感器件不宜使用。
聚紅外迴流焊:聚焦紅外迴流焊適用於返修工作站,進行返修或局部焊接。
台式迴流焊爐:台式設備適合中小批量的PCB組裝生產,性能穩定、價格經濟(大約在4-8萬人民幣之間),國內私營企業及部分國營單位用的較多。
立式迴流焊爐:立式設備型號較多,適合各種不同需求用戶的PCB組裝生產。設備高中低檔都有,性能也相差較多,價格也高低不等(大約在8-80萬人民幣之間)。國內研究所、外企、知名企業用的較多。
迴流焊爐的溫區長度一般為45cm~50cm,溫區數量可以有3、4、5、6、7、8、9、10、12、15甚至更多溫區,從焊接的角度,迴流焊至少有3個溫區,即預熱區、焊接區和冷卻區,很多爐子在計算溫區時通常將冷卻區排除在外,即只計算升溫區、保溫區和焊接區。
迴流焊加工的為表面貼裝的板,其流程比較複雜,可分為兩種:單面貼裝、雙面貼裝。
預塗錫膏→貼片(分為手工貼裝和機器自動貼裝)→迴流焊→檢查及電測試。
A面預塗錫膏→貼片(分為手工貼裝和機器自動貼裝)→迴流焊→B面預塗錫膏→貼片(分為手工貼裝和機器自動貼裝)→迴流焊→檢查及電測試。
溫度曲線是指SMA通過回爐時,SMA上某一點的溫度隨時間變化的曲線。溫度曲線提供了一種直觀的方法,來分析某個元件在整個迴流焊過程中的溫度變化情況。這對於獲得最佳的可焊性,避免由於超溫而對元件造成損壞,以及保證焊接質量都非常有用。
在SMT迴流焊工藝造成對元件加熱不均勻的原因主要有:迴流焊元件熱容量或吸收熱量的差別,傳送帶或加熱器邊緣影響,迴流焊產品負載等三個方面。
1.通常PLCC、QFP與一個分立片狀元件相比熱容量要大,焊接大面積元件就比小元件更困難些。
2.在迴流焊爐中傳送帶在周而復使傳送產品進行迴流焊的同時,也成為一個散熱系統,此外在加熱部分的邊緣與中心散熱條件不同,邊緣一般溫度偏低,爐內除各溫區溫度要求不同外,同一載面的溫度也差異。
3.產品裝載量不同的影響。迴流焊的溫度曲線的調整要考慮在空載,負載及不同負載因子情況下能得到良好的重複性。負載因子定義為:LF=L/(L+S);其中L=組裝基板的長度,S=組裝基板的間隔。
迴流焊工藝要得到重複性好的結果,負載因子愈大愈困難。通常迴流焊爐的最大負載因子的範圍為0.5~0.9。這要根據產品情況(元件焊接密度、不同基板)和再流爐的不同型號來決定。要得到良好的焊接效果和重複性,實踐經驗很重要。
焊接加熱過程中也會產生焊料塌邊,這個情況出現在預熱和主加熱兩種場合,當預熱溫度在幾十至一百範圍內,作為焊料中成分之一的溶劑即會降低粘度而流出,如果其流出的趨勢十分強烈,會同時將焊料顆粒擠出焊區外形成含金顆粒,在溶融時如不能返回到焊區內,也會形成滯留焊料球。
除上面的因素外SMD元件端電極是否平整良好,電路線路板布線設計與焊區間距是否規範,助焊劑塗敷方法的選擇和其塗敷精度等會是造成橋接的原因。
又稱曼哈頓現象。片式元件在遭受急速加熱情況下發生的翹立,這是因為急熱元件兩端存在的溫差,電極端一邊的焊料完全熔融后獲得良好的濕潤,而另一邊的焊料未完全熔融而引起濕潤不良,這樣促進了元件的翹立。因此,加熱時要從時間要素的角度考慮,使水平方向的加熱形成均衡的溫度分佈,避免急熱的產生。
防止元件翹立的主要因素以下幾點:
1.選擇粘力強的焊料,焊料的印刷精度和元件的貼裝精度也需提高。
2.元件的外部電極需要有良好的濕潤性濕潤穩定性。推薦:溫度400C以下,濕度70%RH以下,進廠元件的使用期不可超過6個月。
3.採用小的焊區寬度尺寸,以減少焊料溶融時對元件端部產生的表面張力。另外可適當減小焊料的印刷厚度,如選用100um。
4.焊接溫度管理條件設定對元件翹立也是一個因素。通常的目標是加熱要均勻,特別是在元件兩連接端的焊接圓角形成之前,均衡加熱不可出現波動。
潤濕不良是指焊接過程中焊料和電路基板的焊區(銅箔),或SMD的外部電極,經浸潤后不生成相互間的反應層,而造成漏焊或少焊故障。其中原因大多是焊區表面受到污染或沾上阻焊劑,或是被接合物表面生成金屬化合物層而引起的。譬如銀的表面有硫化物,錫的表面有氧化物都會產生潤濕不良。另外焊料中殘留的鋁、鋅、鎘等超過0.005%以上時,由於焊劑的吸濕作用使活化程度降低,也可發生潤濕不良。因此在焊接基板表面和元件表面要做好防污措施。選擇合適和焊料,並設定合理的焊接溫度曲線。
迴流焊接是SMT工藝中複雜而關鍵的工藝,涉及到自動控制、材料、流體力學和冶金等多種科學、要獲得優良的焊接質量,必須深入研究焊接工藝的方方面面。
隨著眾多電子產品向小型、輕型、高密度方向發展,特別是手持設備的大量使用,在元器件材料工藝方面都對原有SMT技術提出了嚴峻的挑戰,也因此使SM得到了飛速發展的機會。lC引腳腳距發展到0.5mm、0.4mm、0.3mm,BGA已被廣泛採用,CSP也嶄露頭角,並呈現出快速上漲趨勢,材料上免清洗、低殘留錫膏得到廣泛應用。所有這些都給迴流焊工藝提出了新的要求,一個總的趨勢就是要求迴流焊採用更先進的熱傳遞方式,達到節約能源,均勻溫度,適合雙面板PCB和新型器件封裝方式的焊接要求,並逐步實現對波峰焊的全面代替。總體來講,迴流焊爐正朝著高效、多功能和智能化方向發展,主要有以下發展途徑,在這些發展領域迴流焊引領了未來電子產品的發展方向。
在迴流焊中使用惰性氣體保護,已經有一段時間了,並已得到較大範圍的應用,由於價格的考慮,一般都是選擇氮氣保護。氮氣迴流焊有以下優點。
(1)防止減少氧化。
(2)提高焊接潤濕力,加快潤濕速度。
(3)減少錫球的產生,避免橋接,得到良好的焊接質量。
雙面PCB已經相當普及,並在逐漸變得複雜起來,它得以如此普及,主要原因是它給設計者提供了極為良好的彈性空間,從而設計出更為小巧、緊湊的低成本產品。雙面板一般都有通過迴流焊接上面(元器件面),然後通過波峰焊來焊接下面(引腳面)。而有一個趨勢傾向於雙面迴流焊,但是這個工藝製程仍存在一些問題。大板的底部元件可能會在第二次迴流焊過程中掉落,或者底部焊接點的部分熔融而造成焊點的可靠性問題。
通孔插裝元器件
通孔迴流焊有時也稱為分類元器件迴流焊,正在逐漸興起,它可以去除波峰焊環節,而成為PCB混裝技術中的一個工藝環節,這項技術的一個最大的好處就是可以在發揮表面貼裝製造工藝優點的同時使用通孔插件來得到較好的機械連接強度,對於較大尺寸的PCB板的平整度不能夠使所有表面貼裝元器件的引腳都能和焊盤接觸,同時,就算引腳和焊盤都能接觸上,它所提供的機械強度也往往是不夠大的,很容易在產品的使用中脫開而成為故障點。
出於對環保的考慮,鉛在21世紀將會被嚴格限用,雖然電子工業中用鉛量極小,不到全部用量1%,但也屬於禁用之列,在發展趨勢中將會被逐步淘汰,許多地方正在開發可靠而又經濟的無鉛焊料,所開發出的多種替代品一般都具有比錫鉛合金高40屯左右的熔點溫度,這就意味著迴流焊必須在更高的溫度下進行,氮氣保護可以部分消除因溫度提高而增加的氧化和對PCB本身的損傷。
特殊的爐子已經被開發出來處理貼裝有SMT元件的連續柔性板,與普通迴流爐最大的不同點是這種爐子需要特製的軌道來傳遞柔性板。當然,這種爐子也需要能處理連續板的問題,對於分離的PCB板來講,爐中的流量與前幾段工位的狀況無依賴關係,但是對於成卷連續的柔性板,柔性板在整條線上是連續的,線上任何一個特殊問題,停頓就意味著全線必須停頓,這樣就產生一個特殊問題,停頓在爐子中的部分會因過熱而損壞,因此,這樣的爐子必須具備應變隨機停頓的能力,繼續處理完該段柔性板,並在全線恢復連續運轉時回到正常工作狀態。
市場對於縮小體積的需求,使CSP、MPM甚至POP得到較多應用,這樣元器件貼裝后具有更小的佔地面積和更高的信號傳遞速率。填充或灌膠被用來加強焊點結構,使其能抵受住由於矽片與PCB材料的熱脹係數不一致而產生的應力,一般常會採用上滴或圍填法來把晶片用膠封起來。
使用計算機技術對迴流焊焊接工藝進行模擬的方法得到了廣泛的關注,此方法可以大大縮短工藝準備時間,降低實驗費用,提高焊接質量,減小焊接缺陷。
通過使用PCBCAD數據的產品模型結構建立,迴流焊工藝模擬模型,可以替代傳統的在線參數的設置過程,甚至可以用來在生產前確保PCB設計與迴流焊工藝的兼容性,指導可製造性設計(DFM),該模擬模型也可以消除使用熱電偶測試時無法稷蓋全部產品區域的缺陷,PCB組件模型求解器和構建的迴流焊爐模型,對於特定的工藝設置,可以較精確地預測PCB組件的迴流焊溫度曲線。使用該方法在PCB設計階段來進行新產品的工藝優化,可以很簡單地確保產品設計與工藝設備的相容性。
可替換裝配和迴流焊技術工藝(AlternativeAssemblyandReflowTechnology,AART)引起了PCB組裝業的興趣。AART工藝可以同時進行通孔元器件和表面貼裝元器件的迴流焊接,省去了波峰焊和手工焊,與傳統的AART工藝相比具有更少的成本、周期和缺陷率。通過AART工藝,可以建立複雜的PCB組裝工藝。AART必須考慮材料、設計和影響它的工藝因素。一個決策系統(DecisionSupportSystem,DSS)可以幫助工程師實施AART工藝。
迴流焊過程式控制制
智能化再流爐內置計算機控制系統,在Window視窗操作環境下可以很方便地輸入各種數據,可迅速地從內存中取出或更換迴流焊工藝曲線,節省調整時間,提高生產效率。
過程式控制制的目的是實現所要求的質量和儘可能低的成本這兩個目標。以前,過程式控制制主要集中於對缺陌的檢測,以提高質量;經發展,控制的最根本的內涵是對各種工藝進行連續的監控,並尋找出不符合要求的偏差。過程式控制制是一種獲得影響最終結果的特定操作中相關數據的能力,一旦潛在的問題出現,就可實時地接收相關信息,採取糾正措施,並立即將工藝調整到最佳狀況。監控實際工藝過程數據,才算是真正的工藝過程式控制制,這在迴流焊工藝控制中,也就意味著要對製造的每塊板子的熱曲線進行監控。
一種能夠連續監控迴流焊爐的自動管理系統,能夠在實際發生工藝偏移之前指示其工藝是否偏移失控,此即自動迴流焊管理(AutomaticReflowManagement,ARM)系統,此系統把連續的SPC直方圖、線路平衡網路、文件編製和產品跟蹤組成完整的軟體包,並能自動實時榆測工藝數據,並做出判斷來影響產品成本和質量,自動迴流焊管理系統的基本功能是精確地自動檢測和收集通過爐子的產品數據,它提供下列功能:不需要驗證工藝曲線;自動搜集迴流焊工藝數據;對零缺陷生產提供實時反饋和報警;提供迴流焊工藝的自動SPC圖表和修正過程能力指數(ComplexProcessCapabilityindex,Cpk)變數報警。