膜分離
分離技術
膜分離是在20世紀初出現,20世紀60年代后迅速崛起的一門分離新技術。膜分離技術由於兼有分離、濃縮、純化和精製的功能,又有高效、節能、環保、分子級過濾及過濾過程簡單、易於控制等特徵,因此,目前已廣泛應用於食品、醫藥、生物、環保、化工、冶金、能源、石油、水處理、電子、仿生等領域,產生了巨大的經濟效益和社會效益,已成為當今分離科學中最重要的手段之一。
膜是具有選擇性分離功能的材料。利用膜的選擇性分離實現料液的不同組分的分離、純化、濃縮的過程稱作膜分離。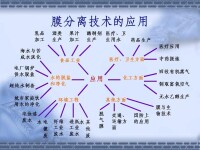
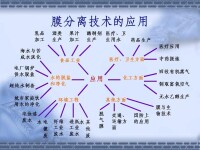
膜分離
膜分離與傳統過濾的不同在於,膜可以在分子範圍內進行分離,並且這過程是一種物理過程,不需發生相的變化和添加助劑。
膜的孔徑一般為微米級,依據其孔徑的不同(或稱為截留分子量),可將膜分為微濾膜(MF)、超濾膜(UF)、納濾膜(NF)和反滲透膜(RO)等;根據材料的不同,可分為無機膜和有機膜:無機膜主要還只有微濾級別的膜,主要是陶瓷膜和金屬膜,有機膜是由高分子材料做成的,如醋酸纖維素、芳香族聚醯胺、聚醚碸、聚氟聚合物等等。
膜分離都採用錯流過濾方式。
膜分離是一門新興的跨學科的高新技術。膜的材料涉及無機化學和高分子化學;膜的製備、分離過程的特徵、傳遞性質和傳遞機理屬於物理化學和數學研究範疇;膜分離過程中涉及的流體力學、傳熱、傳質、化工動力學以及工藝過程的設計,主要屬於化學工程研究範疇;從膜分離主要應用的領域來看,還涉及生物學、醫學以及與食品、石油化工、環境保護等行業相關的學科。
膜分離過程已成為工業上氣體分離、水溶液分離、化學品和生化產品的分離與純化的重要過程。廣泛應用於食品、飲料加工過程、工業污水處理、大規模空氣分離、濕法冶金技術、氣體和液體燃料的生產以及石油化工製品生產等。
膜從廣義上可以定義為兩相之間的一個不連續區間。這個區間的三維量度中的一度和其餘兩度相比要小的多。膜一般很薄,厚度從幾微米、幾十微米至幾百微米之間,而長度和寬度要以米來計量。
膜可以是固相,液相,甚至是氣相的。用各種天然或人工材料製造出來的膜品種繁多,在物理、化學和生物性質上呈現出多樣的特性。膜可以對雙組分或多組分體系進行分離,分級,提純或濃縮。
大部分的分離膜都是固體膜,其中尤以有機高分子聚合物材質製成的膜及其分離過程為主。但仍有待發展。氣體在理論上可以構成分離膜,但研究它的人很少。
物質選擇透過膜的能力可分為兩類:一種是藉助外界能量,物質發生由低位向高位的流動;另一種是以化學位差為推動力,物質發生由高位向地位的流動。
(1)常溫下進行
有效成分損失極少,特別適用於熱敏性物質,如抗生素等醫藥、果汁、酶、蛋白的分離與濃縮
(2)無相態變化
保持原有的風味
(3)無化學變化
典型的物理分離過程,不用化學試劑和添加劑,產品不受污染
(4)選擇性好
可在分子級內進行物質分離,具有普遍濾材無法取代的卓越性能
(5)適應性強
處理規模可大可小,可以連續也可以間隙進行,工藝簡單,操作方便,易於自動化
(6)能耗低
只需電能驅動,能耗極低,其費用約為蒸發濃縮或冷凍濃縮的1/3-1/8
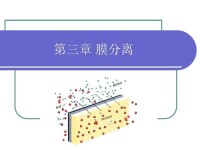
圖1 膜分離工藝現場
膜可分液膜和固體膜。固體膜又可分:
①無機多孔膜,由無機質的多孔材料構成。將膠體和不溶性微粒強制沉積於無機多孔膜上便製成動力形成膜;
②合成膜,通常採用醋酸纖維素、芳香族聚醯胺、聚碸、聚乙烯、聚丙烯等高分子材料製成。
合成膜又分為離子交換膜、均質膜和多孔膜:
①離子交換膜由帶有可電離的陽離子或陰離子的高分子材料所構成;
②均質膜是均勻的高分子薄膜;
③多孔膜是在鑄膜液中加發孔劑,經過蒸發和凝膠分離而成的。
多孔膜又分為非對稱膜和複合膜:
①非對稱膜的膜體可分為表皮層和支撐層:表皮層質地緻密,厚度很小(0.1~0.2μm),但它決定了膜的選擇性和滲透性能;支撐層具有多孔結構,它提供必要的機械強度。膜的結構可通過調節鑄膜液組成和凝膠形成條件予以控制。
②複合膜是以多孔膜作支撐層,覆以極薄的表皮層。用於工業分離的合成膜,可製成片狀、管狀和中空纖維狀等,因此膜分離設備也隨之具有多種結構形式。膜的結構形態,通常藉助於電子顯微鏡技術、電子透射或掃描來觀察。
按所使用的膜的類型,分為液膜分離和合成膜分離:
①液膜分離過程分為乳化液膜和固定液膜的分離過程;
②合成膜的分離過程包括微過濾、超過濾、反滲透、氣體滲透分離、滲透蒸發、滲析及電滲析等過程。
膜分離過程可簡化為滲透過程。
滲透過程的機理研究尚處於發展之中,有多種描述方法,目前尚未得出統一的理論。滲透的基本問題是膜內傳遞的概念。物質在膜內的傳質通量可概括為;傳質通量=滲透係數×傳遞推動力式中傳質通量為單位時間內單位膜面積的物質透過量;滲透係數為單位時間內單位膜面積在單位推動力作用下的物質透過量;傳遞推動力有多種,各有其計量單位。滲透係數不僅取決於滲透物質的屬性,也取決於膜材料的化學屬性和膜的物理構型。
描述膜滲透機理的主要模型有:
①溶解-擴散模型:適用於液體膜、均質膜或非對稱膜表皮層內的物質傳遞。
在推動力作用下,滲透物質先溶解進入膜的上游側,然後擴散至膜的下游側,擴散是控制步驟。例如氣體的滲透分離過程中,推動力是膜兩側滲透物質的分壓差。當溶解服從亨利定律(見相平衡關聯)時,組分的滲透率是組分在膜中的擴散係數和溶解度係數的乘積。混合氣體的分離依賴於各組分在膜中滲透率的差異。溶解-擴散模型用於滲透蒸發(又稱汽滲,上游側為溶液,下游側抽真空或用惰性氣體攜帶,使透過物質汽化而分離)時,還須包括膜的汽液界面上各組分的熱力學平衡關係。
②優先吸附-毛細管流動模型:
由於膜表面對滲透物的優先吸附作用,在膜的上游側表面形成一層該物質富集的吸附液體層。然後,在壓力作用下通過膜的毛細管,連續進入產品溶液中。此模型能描述多孔膜的反滲透過程。
③從不可逆熱力學導出的模型:
膜分離過程通常不只依賴於單一的推動力,而且還有伴生效應(如濃差極化)。不可逆熱力學唯象理論統一關聯了壓力差、濃度差、電位差對傳質通量的關係,採用線性唯象方程描述這種具有伴生效應的過程,並以配偶唯象係數描述伴生效應的影響。
膜分離技術是指在分子水平上不同粒徑分子的混合物在通過半透膜時,實現選擇性分離的技術,在飲用水凈化、工業用水處理,食品、飲料用水凈化、除菌,生物活性物質回收、精製等方面得到廣泛應用,並迅速推廣到紡織、化工、電力、食品、冶金、石油、機械、生物、製藥、發酵等各個領域。分離膜因其獨特的結構和性能,在環境保護和水資源再生方面異軍突起,在環境工程,特別是廢水處理和中水回用方面有著廣泛的應用前景。
膜在大自然中,特別是在生物體內是廣泛存在的,首先出現的是超濾膜和微孔過濾,然後才出現反滲透。
1748年AbbleNelkt發現水能自然地擴散到裝有酒精溶液的豬膀胱內,首次揭示了膜分離現象,但是直到本世紀60年代中期,膜分離技術才應用在工業上。
1861年Schmidt首先提出超過濾的概念,他指出,當溶液用比濾紙孔徑更小的棉膠膜或賽璐玢膜過濾時,如果對接觸膜的溶液施加壓力並使膜兩側產生壓力差,那麼它可以過濾分離溶液中如細菌、蛋白質、膠體那樣的微小粒子,這種過濾精度要比通常的濾紙過濾高的多,因此稱這種膜過濾法為超過濾。
在截留分子量級重要概念提出后,關於截留各種不同分子量的超過濾膜,是Machaelis等用各種比例的酸性和鹼性高分子電解質混合物,以水-丙酮-溴化鈉為溶劑首先製成的。此後,一些國家又相繼用各種高分子材料研製了具有不同用途的超過濾膜,並由美國Amicon公司首先進行了商品化生產。將各種形狀的大面積的超過濾膜放在耐壓裝置中的膜組件中,隨著反滲透組件的研製而發展起來的。
幾種主要膜技術發展近況大致如下:
微濾在20世紀30年代硝酸纖維素微濾膜商品化,60年代主要開發新品種。雖然早在100多年前已在實驗室製造微孔濾膜,但是直到1918年才由Zsigmondy提出商品微孔過濾膜的製造法,並報道了在分離和富集微生物、微粒方面的應用。1925年在德國建立世界上第一個微孔濾膜公司“Sartorius”,專門經銷和生產微孔濾膜。第二次世界大戰後,美國對微孔濾膜的製造技術和應用技術進行了廣泛的研究研究微孔濾膜主要是發展新品種,擴大應用範圍。使用溫度在-100~260℃。
超濾從20世紀70年代進入工業化應用后發展迅速,已成為應用領域最廣的技術。日本開發出孔徑為5~50nm的陶瓷超濾膜,截留分子量為2萬,並開發成功直徑為1~2mm,壁厚200~400um的陶瓷中空纖維超濾膜,特別適合於生物製品的分離提純。
離子交換膜和電滲析技術主要用於苦鹹水脫鹽,引起氯鹼工業的深刻變化。離子膜法比傳統的隔膜法節約總能耗30%,節約投資20%。90年世界上已有34個國家近140套離子膜電解裝置投產,到2000年全世界將1/3氯鹼生產轉向膜法。
20世紀60年代Loeb與Sourirajan發明了第一代高性能的非對稱性醋酸纖維素膜,把反滲透首次用於海波及苦鹹水淡化。70年代開發成功高效芳香聚醯胺中空纖維反滲透膜,使RO膜性能進一步提高。90年代出現低壓反滲透複合膜,為第三代RO膜,膜性能大幅度提高,為RO技術發展開闢了廣闊的前景。超純水製造、鍋爐水軟化,食品、醫藥的濃縮,城市污水處理,化工廢液中有用物質回收。
1979年Monsanto公司用於H2/N2分離的Prism系統的建立,將氣體分離推向工業化應用。1985年Dow化學公司向市場提供以富N2為目的空氣分離器“Generon”氣體分離用於石油、化工、天然氣生產等領域,大大提高了過程的經濟效益。
20世紀80年代後期進入工業應用的膜分離技術是用滲透汽化進行醇類等恆沸物脫水,由於該過程的能耗僅為恆沸精餾的1/3~1/2,且不使用苯等挾帶劑,在取代恆沸精餾及其它脫水技術上具有很大的經濟優勢。德國GFT公司是率先開發成功唯一商品GFT膜的公司。90年代初向巴西、德、法、美、英等國出售了100多套生產裝置,其中最大的為年產4萬噸無水乙醇的工業裝置,建於法國。除此之外,用PV法進行水中少量有機物脫除及某些有機/有機混合物分離,例如水中微量含氯有機物分離,MTBE/甲醇分離,我國膜科學技術的發展是從1958年研究離子交換膜開始的。60年代進入開創階段。1965年著手反滲透的探索,1967年開始的全國海水淡化會戰,大大促進了我國膜科技的發展。70年代進入開發階段。這時期,微濾、電滲析、反滲透和超濾等各種膜和組器件都相繼研究開發出來,80年代跨入了推廣應用階段。80年代又是氣體分離和其他新膜開發階段。
隨著我國膜科學技術的發展,相應的學術、技術團體也相繼成立。她們的成立為規範膜行業的標準、促進膜行業的發展起著舉足輕重的作用。半個世紀以來,膜分離完成了從實驗室到大規模工業應用的轉變,成為一項高效節能的新型分離技術。1925年以來,差不多每十年就有一項新的膜過程在工業上得到應用。
由於膜分離技術本身具有的優越性能,產業界和科技界把膜過程視為二十一世紀工業技術改造中的一項極為重要的新技術。曾有專家指出:誰掌握了膜技術誰就掌握了化學工業的明天。
80年代以來我國膜技術跨入應用階段,同時也是新膜過程的開發階段。在這一時期,膜技術在食品加工、海水淡化、純水、超純水製備、醫藥、生物、環保等領域得到了較大規模的開發和應用。並且,在這一時期,國家重點科技攻關項目和自然科學基金中也都有了膜的課題。
為眾多的企業帶來了較為顯著的經濟效益、社會效益和環境效益。
鑒於微孔濾膜的分離特徵,微孔濾膜的應用範圍主要是從氣相和液相中截留微粒、細菌以及其他污染物,以達到凈化、分離、濃縮的目的。
具體涉及領域主要有:醫藥工業、食品工業(明膠、葡萄酒、白酒、果汁、牛奶等)、高純水、城市污水、工業廢水、飲用水、生物技術、生物發酵等。
早期的工業超濾應用於廢水和污水處理。三十多年來,隨著超濾技術的發展,如今超濾技術已經涉及食品加工、飲料工業、醫藥工業、生物製劑、中藥製劑、臨床醫學、印染廢水、食品工業廢水處理、資源回收、環境工程等眾多領域。
納濾的主要應用領域涉及:食品工業、植物深加工、飲料工業、農產品深加工、生物醫藥、生物發酵、精細化工、環保工業……
由於反滲透分離技術的先進、高效和節能的特點,在國民經濟各個部門都得到了廣泛的應用,主要應用於水處理和熱敏感性物質的濃縮,主要應用領域包括以下:食品工業、牛奶工業、飲料工業、植物(農產品)深加工、生物醫藥、生物發酵、製備飲用水、純水、超純水、海水、苦鹹水淡化、電力、電子、半導體工業用水、醫藥行業工藝用水、製劑用水、注射用水、無菌無熱源純水、食品飲料工業、化工及其它工業的工藝用水、鍋爐用水、洗滌用水及冷卻用水
除了以上四種常用的膜分離過程,另外還有滲析、控制釋放、膜感測器、膜法氣體分離等。
微濾和超濾截留分子量有限可用於精密過濾
膜分離技術根據孔徑大小分類,依次為微濾、超濾、納濾和反滲透。微濾和超濾都屬於精密過濾,通常納濾膜的孔徑範圍在0.1~1微米,超濾膜孔徑在0.05um至1nm之間,超濾膜的截留特性是以對標準有機物的截留分子量來表徵,通常截留分子量範圍在1000~300000,對小分子有機污染物的去除效果不明顯,達不到深度處理的要求。同時,超濾設備佔地少,通水量可增加一倍,在城市土地資源緊張的今天,超濾設備在水廠改擴建過程中擁有非常廣闊的空間。膜分離技術
超濾水質生物安全的有效手段
水質標準的第一項指標就是生物指標(總大腸菌群),超濾可以有效去除細菌、病毒,保證水質生物安全,減少水處理過程中消毒劑的使用量,進而減少消毒副產物的二次污染問題。經東麗超濾膜處理后的水,出水濁度在0.1度以下,保證微生物的安全性。
納濾膜的孔徑為幾納米,截留分子量在80~1000的範圍內,對無機鹽有一定的截留率。反滲透是水處理領域最高端的單項處理技術,能夠阻擋所有溶解性鹽及分子量大於100的有機物,經過反滲透處理的出水水質較好。納濾和反滲透是深度處理的有效手段,可解決化學污染和有機污染問題。
微濾、超濾、納濾和反滲透,這四種類型的膜分離技術在水處理過程中都發揮著重要的作用,廣泛應用於各種水處理的終端過濾、工業給水的預處理和飲用水的處理,近十幾年來,我國在膜組件及相應的配套設備方面有了較大的進步,雖然在品種的系列化和質量上與國外先進技術存在一定的差距,但國內產品已經具備了替代進口同類產品的水平。膜分離技術在化工、醫藥、分析檢測和環保等領域獲得了廣泛的應用和認可,也取得了很好的經濟、社會和環境效益。