迴流爐
電子科技工業SMT製程需要的設備
迴流爐也就是迴流焊爐(也叫“再流焊、再流爐、再流焊爐”),是電子科技工業SMT製程所需要的一種設備。
迴流爐工藝是通過重新熔化預先分配到印製板焊盤上的膏狀軟釺焊料,實現表面組裝元器件焊端或引腳與印製板焊盤之間機械與電氣連接的軟釺焊。迴流爐是SMT(表面貼裝技術)最後一個關鍵工序,是一個實時過程式控制制,其過程變化比較複雜,涉及許多工藝參數,其中溫度曲線的設置最為重要,直接決定迴流焊接質量。
靈活通用的焊接系統
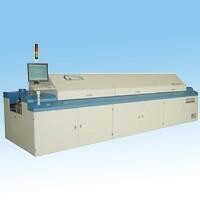
迴流爐
優勢:
■ 可對應於高性能的焊接要求
■ 預熱和焊接過程的無氧環境
■ 整個焊接組件的溫度一致性
■ 決不會發生溫度過熱現象
■ 決無陰影現象
■ 可進行單板多次焊接
■ 超低的操作成本
■ 靈活通用性和獨立操作性
工作載板具有廣泛的通用性和方便的靈活性。選配附帶密閉冷卻系統,永久過濾系統和數據收集功能。
標準基板尺寸:
-VP1000-33: 300x350 mm
-VP1000-53: 500x350 mm
-VP1000-56: 600x500 mm
自定義尺寸:
- 基板規格: 1500 x 1000 mm
- 最大產品高度 300 mm
- 最大基板重量 25 kg
線上無鉛焊接系統
在線VP1000 - 56si系統是基於VP1000系列上的在線生產機器模塊化設計可使機器具備以下低成本特色:
■ 具備自動進板和出板功能
■ 自動載入和排出載板治具
■ 可方便與前後的設備或儲板設備連接
優勢:
■ 可對應於高性能的通用在線焊接要求
■ 預熱和焊接過程的無氧環境
■ 整個焊接組件的溫度一致性
■ 決不會發生溫度過熱現象
■ 決無陰影現象
■ 可進行單板多次焊接
■ 無任何損耗時間即可進行曲線測定
■ 超低的操作成本
標準基板尺寸:
- VP 1000 - 56si: 500 x 600 mm
每板生產周期60秒
自檢測功能的傳輸導軌
帶 3 mm or 5 mm邊緣支持的雙導軌
迴流爐焊接
A類設置:包括單面迴流爐產品,雙面迴流爐第一面、雙面(一面焊膏、另一面膠水)的焊膏面(帶BGA產品不在此類);
B類設置:包括普通雙面迴流爐的第二面;
C類設置:包括所有帶BGA的產品;
手機設置:289、389、802手機主板。
迴流爐的溫度曲線分為以下幾段:預熱、保溫乾燥、焊接。預熱是為了使元器件在焊接時所受的熱衝擊最小。元器件一般能忍受的溫度變化速率為4℃/SEC以下,因此預熱階段升溫速率一般控制在1℃/SEC~3℃/SEC,同時溫升太快會造成焊料濺出。保溫乾燥是為了保證焊料助焊劑完全乾燥,同時助焊劑對焊接面的氧化物去除,起活化作用。迴流焊接區,錫膏開始融化並呈流動狀態,一般要超過熔點溫度20℃才能保證焊接質量。為了保證呈流動狀態的焊料可潤濕整個焊盤以及元器件的引出端,要求焊料呈熔融狀態的時間為40~90秒,這也是決定是否產生虛焊和假焊的重要因素。
對於焊接,溫度曲線要求如下:
階段 | 溫度 | 時間 | |
預熱 | 室溫升至110℃~150℃ | 50秒左右 | |
保溫乾燥 | 130℃~160℃ | 80~150秒 | |
焊接 | 大於183℃ | 40~90秒 | |
200℃以上 | 20~45秒 | ||
峰值溫度 | MAX230℃ | ||
MIN 210℃ |
膠水固化
對於LOCTITE3609,3611紅膠的溫度曲線要求:
溫度範圍 | 持續時間 |
140~160℃ | 80~130秒 |
對於LOCTITE3513紅膠的溫度曲線要求(Underfill):
一般生產線均採用強迫對流熱風迴流爐(Hot-air reflow oven),其熱特性改變相對較小,同時採用免清洗焊膏Qualitek delta(sn/pb比例63/37),能必較完美完成公司現有PCB低密度產品迴流焊接,高密度PCB板則須特別控制。現在我們對迴流爐管制的具體操作是檢查迴流爐各溫區溫度,定期測量溫度曲線,以檢驗迴流爐是否被控制在正常壯態狀態否達到焊膏及膠水推薦溫度曲線,同時檢查溫度的均勻性。但是,公司PCB組裝上大量使用BGA、PLCC、FINE PITCH 等元件,加上PCB材料、尺寸、元件布置、可焊性的不同,其傳熱程度、溫度曲線和迴流焊爐溫度設置必然有差別。必須對不同類型PCB作溫度曲線測量。
迴流爐熱風迴流原理
當PCB進入預熱區時,焊膏中的水份、氣體蒸發,助焊劑濕潤元件引腳和焊盤,焊膏開始軟化並覆蓋焊盤,使元件引腳和焊盤與氧氣隔離;PCB進入迴流區時,溫度迅速上升,焊膏達到熔化狀態,對PCB上的元件引腳和焊盤濕潤、擴散、迴流、之後冷卻形成錫焊接頭,從而完成了迴流焊。
強迫對流熱風迴流即通過氣流循環,在元件的上下兩個表面,以相對較低的溫度而產生高效的熱傳遞,同時使小型元件避免過熱,避免由於單面受熱引起PCB變形,PCB上大量的焊點相對均勻地受熱,從而實現迴流焊接。
爐溫曲線測試方法
具體的溫度曲線一般隨所用測試方法、測試點的位置以及SMA的載入情況的不同而有所不同。再流焊機溫度曲線的測試,一般採用能隨SMA組件一同進入爐膛內的溫度採集器進行測試,測量採用K型熱電偶,偶絲直徑0.1~0.3mm為宜,測試后將溫度採集器數據輸入計算機或專用溫度曲線數據處理機並顯示或列印出SMA組件隨傳送帶運行形成的溫度曲線。
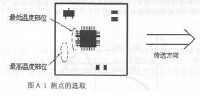
A1:爐溫曲線測點的選取
1)選取能代表SMA組件上溫度變化的測試點,一般至少應選取三點,這三點應反映出表面組裝組件上溫度最高、最低、中間部位上的溫度變化。再流焊機所用傳送方式的不同有時會影響最高、最低部位的分佈情況,這點應根據具體爐子情況具體考慮。對於網帶式傳送的再流焊機表面組裝件上最高溫度部位一般在SMA與傳送方向相垂直的無元件的邊緣中心處,最低溫度部位一般在SMA靠近中心部位的大型元器件處(如PLCC),參見圖A1。
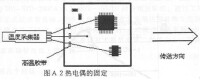
A2:爐溫曲線測試熱電偶的固定
3)將被測的SMA組件連同溫度採集器一同置於再流焊機入口處的傳送鏈/網帶上,隨著傳送鏈/網帶的運行,將完成一個測試過程。注意溫度採集器距待測的SIMA組件距離應大於100mn。
4)將溫度採集器記錄的溫度曲線顯示或列印出來。由於測試點熱容量的不同,通過三個測試點所測的溫度曲線形狀會略有不同,爐溫設定是否合理,可根據三條曲線預熱結束時的溫度差、焊接峰值溫度以及再流時間來考慮。
迴流爐溫設置步驟
1)首先,按照生產量設定傳送帶速,注意帶速不能超過再流焊工藝允許的最大速度(這裡指應滿足預熱升溫速率運≤3℃/s,焊接峰值溫度和再流時間應滿足焊接要求)。
2)初次設定爐溫。
3)在確保爐內溫度穩定后,進行首次溫度曲線測試。
4)分析所測得的溫度曲線與所設計的溫度曲線的差別,進行下一次爐溫調整。
5)在確保爐內溫度穩定以及測試用SMA冷卻到室溫后,進行下一次溫度曲線的測試。
6)重複4)~5)過程,直到所測溫度曲線與設計的理想溫度曲線一致為止。
紅外/熱風再流焊接是一個非平衡過程。對不同的SMA、不同的焊膏、不同的傳送速度、不同的板間距必須設計一個特定的溫度曲線。理想的溫度曲線應根據焊接峰值溫度、再流時間、預熱最大升溫速率以及SMA各點取得的最好熱平衡來考慮。
隨著“山寨”文化的流行,迴流爐的前景如日中天。像日東、SUNEAST這類公司就是靠迴流爐起家的。