PFMEA
用於模具設計等階段的分析技術
PFMEA是製程失效模式及影響分析(Process Failure Mode and Effects Analysis)的英文簡稱,是由負責製造/裝配的工程師/小組主要採用的一種分析技術,用以最大限度地保證各種潛在的失效模式及其相關的起因/機理已得到充分的考慮和論述。
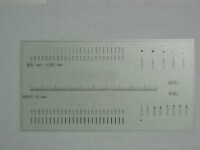
PFMEA
嚴重度(S):指一給定失效模式最嚴重的影響後果的級別,是單一的FMEA範圍內的相對定級結果。嚴重度數值的降低只有通過設計更改或重新設計才能夠實現。
頻度(O):指某一特定的起因/機理髮生的可能發生,描述出現的可能性的級別數具有相對意義,但不是絕對的。
探測度(D):指在零部件離開製造工序或裝配之前,利用第二種現行過程式控制制方法找出失效起因/機理過程缺陷或後序發生的失效模式的可能性的評價指標;或者用第三種過程式控制制方法找出後序發生的失效模式的可能性的評價指標。
風險優先數(RPN):指嚴重度數(S)和頻度數(O)及不易探測度數(D)三項數字之乘積。
顧客:一般指“最終使用者”,但也可以是隨後或下游的製造或裝配工序,維修工序或政府法規。
新件模具設計階段。
新件試模、試做階段。
新件進入量產前階段。
新件客戶抱怨階段。
PFMEA的分析原理

PFMEA
(2)評價失效對產品質量和顧客的潛在影響;
(3)找出減少失效發生或失效條件的過程式控制制變數,並制定糾正和預防措施;
(4)編製潛在失效模式分級表,確保嚴重的失效模式得到優先控制;
(5)跟蹤控制措施的實施情況,更新失效模式分級表。
“過程功能/要求”
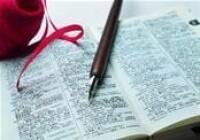
PFMEA
“潛在的失效模式”
是指過程可能發生的不滿足過程要求或設計意圖的形式或問題點,是對某具體工序不符合要求的描述。它可能是引起下一道工序的潛在失效模式,也可能是上一道工序失效模式的後果。典型的失效模式包括斷裂、變形、安裝調試不當等;
“失效後果”
是指失效模式對產品質量和顧客可能引發的不良影響,根據顧客可能注意到或經歷的情況來描述失效後果,對最終使用者來說,失效的後果應一律用產品或系統的性能來闡述,如雜訊、異味、不起作用等;
“嚴重性”
是潛在失效模式對顧客影響後果的嚴重程度,為了準確定義失效模式的不良影響,通常需要對每種失效模式的潛在影響進行評價並賦予分值,用1-10分表示,分值愈高則影響愈嚴重。“可能性”:是指具體的失效起因發生的概率,可能性的分級數著重在其含義而不是數值,通常也用1—10分來評估可能性的大小,分值愈高則出現機會愈大。“不易探測度”:是指在零部件離開製造工序或裝備工位之前,發現失效起因過程缺陷的難易程度,評價指標也分為1—10級,得分愈高則愈難以被發現和檢查出;
“失效的原因/機理”
是指失效是怎麼發生的,並依據可以糾正或控制的原則來描述,針對每一個潛在的失效模式在儘可能廣的範圍內,列出每個可以想到的失效起因,如果起因對失效模式來說是唯一的,那麼考慮過程就完成了。否則,還要在眾多的起因中分析出根本原因,以便針對那些相關的因素採取糾正措施,典型的失效起因包括:焊接不正確、潤滑不當、零件裝錯等;
“現行控制方法”
是對當前使用的、儘可能阻止失效模式的發生或是探測出將發生的失效模式的控制方法的描述。這些控制方法可以是物理過程控制方法,如使用防錯卡具,或者管理過程式控制制方法,如採用統計過程式控制制(SPC)技術;
“風險級(RPN)”
是嚴重性、可能性和不易探測性三者的乘積。該數值愈大則表明這一潛在問題愈嚴重,愈應及時採取糾正措施,以便努力減少該值。在一般情況下,不管風險級的數值如何,當嚴重性高時,應予以特別注意;
“建議採取的措施”
是為了減少風險發生的嚴重性、可能性或不易探測性數值而制定的應對方案,包括行動計劃或措施、責任人、可能需要的資源和完成日期等。當失效模式排出先後次序后應首先對排在最前面的風險事件或嚴重性高的事件採取糾正措施,任何建議措施的目的都是為了阻止其發生,或減少發生后的影響和損失;
“措施結果”
是對上述“建議採取的措施”計劃方案之實施狀況的跟蹤和確認。在明確了糾正措施后,重新估計並記錄採取糾正措施后的嚴重性、可能性和不易探測性數值,計算並記錄糾正後的新的風險級值,該數值應當比措施結果之前的風險級值低得多,從而表明採取措施后能夠充分降低失效帶來的風險。
在實際應用中,SMT裝配有諸如單面貼裝、雙面貼裝、雙面混裝等操作方式,各種操作方式的具體生產工藝流程各不相同。為r說明如何將PFMEA應用於SMT裝配過程,現在就以工藝流程相對簡單的單面貼裝為對象,闡述應用PFMEA的方法。
單面貼裝過程功能描述如下:單面貼裝的主要環節有印刷焊膏、貼裝元器件、焊接元器件,其工藝流程是:印刷焊膏一一貼裝元器件一一AOT檢驗一一迴流焊接一一焊點檢驗,該裝配過程涉及的主要設備有絲印機、貼片機、迴流焊爐和檢測設備。
通過對長期SMT生產過程的總結,單面貼裝工作方式中暴露的焊點常見失效模式有:焊錫球、冷焊、焊橋、立片,其因果分析圖如圖所示。
根據圖2中對這幾種失效模式的因果分析和檢驗、設計人員的實踐經驗,現對這些失效模式分析如下:
焊錫球是迴流焊接中經常碰到的一個問題。通常片狀元件側面或細間距引腳之間常常出現焊錫球。
失效後果:焊錫球會造成短路、虛焊以及電路板污染。可能導致少部分產品報廢或全部產品返工,將嚴重度評定為5。
現有故障檢測方法:人工目視和x射線檢測儀檢測。
失效原因為:
助焊劑缺陷——活性降低,頻度為3,檢測難度為6,風險指數RPN為90。
模板缺陷——開孔尺寸不當焊盤過大等,頻度為5,檢測難度為4,風險指數RPN為100。
迴流溫度曲線設置不當,頻度為7,檢測難度為5,風險指數RPN為175。現行控制措施:調整迴流焊溫度曲線使之與使用焊膏特性相適應。
冷焊的表象是焊點發黑,焊膏未完全熔化。
失效後果:產生開路和虛焊,可能導致少部分產品報廢或全部產品返工,嚴重度評定為50現有故障檢測方法:人工目視和x射線檢測儀檢測。
失效原因為:
迴流焊接參數設置不當,溫度過低,傳送速度過快,頻度為3,檢測難度為5,風險指數為750現行控制措施:按照焊膏資料或可行經驗設置迴流焊溫度曲線。
焊橋
焊橋經常出現在引腳較密的丁C上或間距較小的片狀元件間,這種缺陷在檢驗標準中屬於重大缺陷。焊橋會嚴重影響產品的電氣性能,所以必須要加以根除。
失效後果;焊橋會造成短路等後果,嚴重的會使系統或主機喪失主要功能,導致產品全部報廢,用戶不滿意程度很高,嚴重度評定為8。
現有故障檢測方法:人工目視和x射線檢測儀檢測。
失效原因為:
模板缺陷——開孔尺寸過大等,頻度為7,檢測難度為6,風險指數RPN為336。
焊膏缺陷——粘度不當等,頻度為5,檢測難度為5,風險指數RPN為200。
迴流焊接預熱溫度和預熱時間設置不當,頻度為5,檢測難度為4,風險指數RPN為160。現行控制措施:降低預熱溫度,縮短預熱時間。
立片
立片主要發生在小的矩形片式元件(如貼片電阻、電容)迴流焊接過程中。引起這種現象的主要原因是元件兩端受熱不均勻,焊膏熔化有先後所致。
失效後果:導致開路,引發電路故障,會使系統或整機喪失主要功能,嚴重度評定為7。現有故障檢測方法:人工目視檢測。
失效原因分別為:貼片精度不夠,頻度為3,檢測難度為5,風險指數RPN為105.迴流焊接預熱溫度較低,預熱時間較短,頻度為5,檢測難度為4,風險指數RPN為140。現行控制措施:適當提高預熱溫度,延長預熱時間。
焊膏印刷過厚,頻度為5,檢測難度為5,風險指數RPN為175。現行控制措施:針對不同的器件選用適當厚度的絲印模板。
在計算了各潛在失效模式的RPN值之後,後續工作就是開展相應的工藝試驗,探尋針對高RPN值和高嚴重度的潛在失效模式的糾正措施,並在糾正後,重新進行風險評估,驗證糾正措施的可行性與正確性。
現以汽車內飾產品——汽車內飾件的製造過程為例,來簡單介紹如何利用PFMEA分析製造過程風險,並予以改進的。為了使PFMEA進行的條理清晰,需使用一個表樣,(見表一),按照表格中對應的數字編號的內容進行介紹。
1.基本數據在表格上部填上所分析的零部件及PFMEA小組成員的相關信息。
2.過程功能/要求簡單描述將被分析的過程或作業,並進行編號。根據過程流程圖,對所規劃的過程進行準確地描述,描述必須完整。如果含許多不同潛在失效模式的作業,可把這些以獨立項目列出。
潛在失效模式所謂潛在失效模式是指過程可能潛在不滿足過程要求,是對具體作業不符合要求的描述。搜集在各過程<工序中可能的缺陷,即使特定條件下可能發生的缺陷模式也應列出。也包括以往歷史的經驗。
潛在失效後果是指失效模式對顧客的影響,站在顧客的角度描述失效的後果,這裡的顧客可以是下道工序或是最終使用者。就舉例中的汽車門內飾板對最終使用者來說,失效後果可以是漏水、雜訊、外觀不良等,對下道作業失效後果可以是無法安裝無法鑽孔等。
5.嚴重度是對一個已假定失效模式的最嚴重影響的評價等級。要減少嚴重度識別等級,只能通過對零件的設計變更,或對過程重新設計,否則,嚴重度不會發生變化。嚴重度分1(無影響)-10(後果嚴重)級。
6.分類是對過程式控制制的一些特殊過程特性進行分類,其符號是公司內部的規定,或是顧客的規定。
7.失效起因/機理簡單說就是每一種缺陷發生的可能的原因,原因可以是生產或裝配所決定的。需對每一原因儘可能簡要地描述。
8.頻度(發生率)是指具體的失效起因發生的可能性,這種可能性分級只代表其含義,不代表具體數字。只有通過設計更改或過程更改才可能改變頻度級別。頻度分1(極低頻率)-10(很高頻率)級。
9.現行過程式控制制儘可能阻止現有過程失效模式的發生,可以採用防錯措施或加工后評價等方法。比如F增加防錯裝置或增加檢驗頻次。
10.探測度(發現率)是指在缺陷發生時被發現的概率。也分為1(很可能)(不可能)5級。
11.風險順序數(RPN)是產品嚴重度、頻度和探測度的乘積。假如嚴重度為S,頻度為O,探測度為D,則RPN=(S)×(O)×(D)。該值從1(無風)-1000(高風險)。對於高嚴重度、高RPN值的缺陷需優先採取排除措施。
12.建議的措施通常把風險順序數的組成部分作為尋找措施的一個依據。但對於對用戶嚴重影響的缺陷,則應通過改進產品或過程,而不是通過大量的檢驗。若頻度很高則應通過改進產品或過程,若一個缺陷很難發現也即探測度低,則既要改進檢驗措施,也要減小缺陷發生頻度。
13.對建議措施的責任把負責實施建議措施的相關人員及計劃完成日期記錄下來,以便對措施進行跟蹤與評價。
14.採取的措施對已經實施的措施進行記錄。
15.措施實施后的RPN在措施實施后,重新對缺陷風險(RPN)進行評定。求得新的風險順序數后與改進前的狀況進行比較,以便估計所採取的措施是否有效,是否必要採取進一步的措施。從例中可以看出:經採取措施后RPN明顯降低,措施有效。以上是利用PFMEA進行過程風險分析,進行質量改進的簡單描述,我們可以總結為。
一、PFMEA是不斷更新的,是動態的。要求在產品開發/過程開發或生產製造過程中對PFMEA進行不斷地更新和處理,無論是以往的歷史經驗或是可能發生的缺陷都應體現在PFMEA表格中。
二、在進行PFMEA時一定要對缺陷及其風險進行客觀地與實際相符的評定,不能擅自推斷,造成PFMEA缺乏準確性。
三、PFMEA不是表面的東西,是小組成員集體的努力,應該包括但不局限於設計、製造、質量、服務等部門。
四、PFMEA是一種有目的的方法,可以通過這種方法及早發現缺陷,對缺陷的風險進行評估,然後制定避免這些缺陷的對策。
AQuA Pro®是一套100%基於網路的集成資料庫管理工具,可以創建、維持、分析並組織APQP、PPAP以及其他產品實現文件,進而幫助用戶持續改進產品設計和製造過程,其應用範圍廣泛,從全球性、地區性、企業,部門甚至到個人層面,有助於提高產品質量並縮短開發周期。
關聯文件
設計失效模式及後果分析
設計驗證計劃與報告
過程流程圖
過程失效模式及後果分析
關鍵控制計劃
動態控制計劃
現場作業指導書
特性表單
表單
操作人員檢查清單
映射工藝段和產品族繼承
AQuA Pro® 的精髓 -t 映射工藝段和產品族繼承”可以幫助用戶以族類產品形式快速創建產品結構樹。AQuA Pro® 幫助用戶基於已有產品及過程信息快速創建全新產品。在改變局部或全體過程時,軟體將自動更新利用相同的信息的所有產品和過程信息。毋庸置疑,此特點可以利用最小的操作最大程度上簡操化用戶在APQP文件及記錄上人工操作的工作。90%的情況下用戶只需改變產品或過程規格即可。
自動生成客戶格式
AQuA Pro® 允許改變格式以滿足客戶的具體PPAP要求。用戶可以選擇添加、刪除或更改欄位,控制欄標題和寬度,添加和改變文件標題等。AQuA Pro® 可以自動提出所需要的信息並自動轉化為客戶要求的格式提交。設計專屬的作業指導書Aqua Pro® 是行業內唯一一款允許用戶對作業指導書進行完全自定義設計的軟體。而且這種設計只需要完成一次,軟體會自動匹配此設計模板至公司所有產品。用戶可以非常方便利用圖片和註釋等設計作業指導書。同時支持和作業順序,與控制計劃鏈接在一起,例如量具信息、工具/設備和尺寸等。
其他突出特點
動態報告生成
過程流程圖自動繪製