共找到3條詞條名為切削加工的結果 展開
- 工業上所使用的某種操作
- 現代文化出版社出版的雜誌
- 電子工業出版社出版的圖書
切削加工
工業上所使用的某種操作
切削加工是指用切削工具(包括刀具、磨具和磨料)把坯料或工件上多餘的材料層切去成為切屑,使工件獲得規定的幾何形狀、尺寸和表面質量的加工方法。
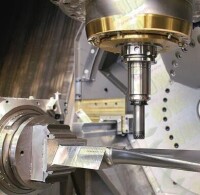
切削加工
切削加工是利用切削刀具和工件的相對運動,從毛坯(鑄件、鍛件、型材等)上切除多餘金屬層,以獲得尺寸精度、形狀和位置精度、表面質量完全符合圖樣要求的機器零件的加工方法。經過鑄、鍛、焊所加工出來的大都為零件的毛坯,一般很少能夠在機器上直接使用,還需要進一步切削加工,才能滿足零件的技術要求。切削加工分為機械加工(簡稱機加工)和鉗工兩大部分。機械加工是指通過工人操作機床對零件進行切削加工。
切削加工是機械製造中最主要的加工方法。雖然毛坯製造精度不斷提高,精鑄、精鍛、擠壓、粉末冶金等加工工藝應用日廣,但由於切削加工的適應範圍廣,且能達到很高的精度和很低的表面粗糙度,在機械製造工藝中仍佔有重要地位。
金屬材料的切削加工有許多分類方法。常見的有以下3種。
1、按工藝特徵區分
切削加工的工藝特徵決定於切削工具的結構以及切削工具與工件的相對運動形式。按工藝特徵,切削加工一般可分為:車削、銑削、鑽削、鏜削、鉸削、刨削、插削、拉削、鋸切、磨削、研磨、珩磨、超精加工、拋光、齒輪加工、蝸輪加工、螺紋加工、超精密加工、鉗工和刮削等。
2、按切除率和精度分
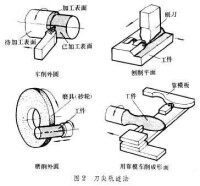
切削加工相關圖片(3)
3、按表面形成方法區分
切削加工時,工件的已加工表面是依靠切削工具和工件作相對運動來獲得的。按表面形成方法,切削加工可分為 3類。①刀尖軌跡法:依靠刀尖相對於工件表面的運動軌跡來獲得工件所要求的表面幾何形狀,如車削外圓、刨削平面、磨削外圓、用靠模車削成形面等。刀尖的運動軌跡取決於機床所提供的切削工具與工件的相對運動。②成形刀具法:簡稱成形法,用與工件的最終表面輪廓相匹配的成形刀具或成形砂輪等加工出成形面。此時機床的部分成形運動被刀刃的幾何形狀所代替,如成形車削、成形銑削和成形磨削等。由於成形刀具的製造比較困難,機床-夾具-工件-刀具所形成的工藝系統所能承受的切削力有限,成形法一般只用於加工短的成形面。③展成法:又稱滾切法,加工時切削工具與工件作相對展成運動,刀具(或砂輪)和工件的瞬心線相互作純滾動,兩者之間保持確定的速比關係,所獲得加工表面就是刀刃在這種運動中的包絡面。齒輪加工中的滾齒、插齒、剃齒、珩齒和磨齒(不包括成形磨齒)等均屬展成法加工。
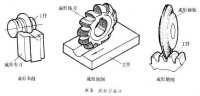
切削加工相關圖片(2)
提高切削質量的途徑
切削加工質量主要是指工件的加工精度(包括尺寸、幾何形狀和各表面間相互位置)和表面質量(包括表面粗糙度、殘餘應力和表面硬化)。隨著技術的進步,切削加工的質量不斷提高。18世紀後期,切削加工精度以毫米計;20世紀初,切削加工精度最高已達0.01毫米;至50年代,切削加工精度最高已達微米級;70年代,切削加工精度又提高到0.1微米。影響切削加工質量的主要因素有機床、刀具、夾具、工件毛坯、工藝方法和加工環境等方面。要提高切削加工質量,必須對上述各方面採取適當措施,如減小機床工作誤差、正確選用切削工具、提高毛坯質量、合理安排工藝、改善環境條件等。
減小機床工作誤差
通常採用的方法有:①選用具有足夠精度和剛度的機床。②必要時可以採取補償校正的方法,如在螺紋磨床或滾齒機上,根據事先測得的機床傳動鏈誤差加裝誤差校正裝置,以校正機床的傳動系統誤差。③採用機床夾具來保證加工精度,如利用鏜模加工箱體上的孔隙,使孔距精度由鏜模決定而不受機床定位誤差的影響。④防止機床熱變形對加工精度的影響。⑤消除機床內部振源和採取隔振措施,以減少振動對加工精度和粗糙度的影響。⑥提高機床自動化程度,如採用主動測量或自動控制系統,以減少加工過程中的人為誤差。
正確選用切削工具
應採用耐磨性好的刀具,合理選用刀具幾何參數,並仔細地研磨刃口,使其光滑而鋒利。例如用磨具加工,一般選用較細、較硬磨粒的磨具,砂輪要正確和及時地修整。
工件毛坯要具有均勻的材質和加工余量,同時採用適當的熱處理,如時效處理、退火、正火、調質等措施以消減內應力,並改善材料的切削加工性。
採用合理的工藝程序;正確選用切削用量,以減小切削力和切削熱的影響,並防止產生自激振動;選用合適的切削液對切削區進行充分冷卻和潤滑;選擇工件的安裝定位基準和夾緊方式時,注意減小安裝誤差和工件變形。
保持加工環境清潔;對外部振源和熱源採取隔離措施;精密加工在恆溫、恆濕和防塵的條件下進行。
提高切削用量以提高材料切除率,是提高切削加工效率的基本途徑。常用的高效切削加工方法有高速切削、強力切削、等離子弧加熱切削和振動切削。
1、高速切削
一般指採用硬質合金刀具所能達到的切削速度的切削加工。磨削速度在45米/秒以上的切削稱為高速磨削。採用高速切削(或磨削)既可提高效率,又可減小表面粗糙度。用硬質合金刀具高速車削普通鋼材的切削速度可達200米/分;用陶瓷刀具可達500米/分;用金剛石刀具車削有色金屬的切削速度可達 900米/分。實驗室中試驗的超高速切削的速度可達4000米/分以上。60年代以來,磨削速度已從 30米/秒左右逐步提高到45、60、80以至 100米/秒;實驗室中的磨削速度已達200米/秒。高速切削(或磨削)要求機床具有高轉速、高剛度、大功率和抗振性好的工藝系統;要求刀具有合理的幾何參數和方便的緊固方式,還需考慮安全可靠的斷屑方法。
2、強力切削
指大進給或大切深的切削加工,一般用於車削和磨削(見緩進給磨削)。強力車削的主要特點是車刀除主切削刃外,還有一個平行於工件已加工表面的副切削刃同時參與切削,故可把進給量比一般車削提高几倍甚至十幾倍。在一般機床上,只要功率足夠和工藝系統剛度好就可實行強力切削。與高速切削比較,強力切削的切削溫度較低,刀具壽命較長,切削效率較高;缺點是加工表面較粗糙。強力切削時,徑向切削力很大,故不適於加工細長工件。
3、等離子弧加熱切削
利用等離子弧的高溫把工件切削區的局部瞬時加熱到800~900℃的切削方法,常採用陶瓷刀具,適用於加工大件。切削時要根據工件的材質、尺寸以及切削速度、切削深度和進給量來調整等離子弧的加熱強度。適當調整后,可使工件已加工表面的溫度保持在 150℃以下而不致發生金相組織變化。這種方法適於加工淬硬工件和難加工金屬材料的切削。材料切除率可提高2~20倍,成本降低30~85%。
4、振動切削
沿刀具進給方向附加低頻或高頻振動的切削加工,可以提高切削效率。低頻振動切削具有很好的斷屑效果,可不用斷屑裝置,使刀刃強度增加,切削時的總功率消耗比帶有斷屑裝置的普通切削降低40%左右。高頻振動切削也稱超聲波振動切削,有助於減小刀具與工件之間的摩擦,降低切削溫度,減小刀具的粘著磨損,從而提高切削效率和加工表面質量,刀具壽命約可提高40%。
對木材、塑料、橡膠、玻璃大理石、花崗石等非金屬材料的切削加工,雖與金屬材料的切削類似,但所用刀具、設備和切削用量等各有特點。
木材製品的切削加工主要在各種木工機床上進行,其方法主要有:鋸切、刨切、車削、銑削、鑽削和砂光等。
刨削通常用木工平刨床或木工壓刨床(見木工刨床)。兩者都可用旋轉的刨刀刨削平面或型面,其中壓刨床加工可得到較高的尺寸精度。當表面的光潔程度要求較高時可用木工精光刨。
木料的外圓一般在木工車床上車削。
木料的開榫、開槽、刻模和各種型面的加工,可用成形銑刀在木工銑床上銑削。
鑽孔可用木工鑽頭、麻花鑽頭或扁鑽,在台鑽或木工鑽床上進行。小孔也可用手電筒鑽加工。
木料表面的精整可用木工砂光機。平面砂光可用帶式砂光機;各種型面的砂光可用滾筒式砂光機;端面砂光和邊角倒棱可用盤式砂光機。也可用木工車床或木工鑽床砂光。
木料加工的切削速度比金屬切削高得多,所以刀具的刃口都較薄而鋒利,進給量也較大。如鋸切速度常達40~60米/秒;車削或刨削時,刀具前角常達30°~35°,切削速度達60~100米/秒,故出屑量很大。切削時一般不用切削液,干切下來的大量木屑可用抽風機吸走。高速旋轉的木工機床一般都設有機動進給和安全防護裝置,但不少木材的切削加工仍需用手動進給,因此必須特別注意操作安全。
塑料的剛度比金屬差,易彎曲變形,尤其是熱塑性塑料導熱性差,易升溫軟化。故切削塑料時,宜用高速鋼或硬質合金刀具,選用小的進給量(0.1~0.5 毫米/轉)和高的切削速度,並用壓縮空氣冷卻。若刀具鋒利,角度合適(一般前角為10°~30°,后角為5°~15°),可產生帶狀切屑,易於帶走熱量。若短屑和粉塵太多則會使刀具變鈍並污染機床,這時需要對機床上外露的零件和導軌進行保護。切削賽璐珞時,容易著火,必須用水冷卻。
車削酚醛塑料、氨基塑料和膠布板等熱固性塑料時,宜用硬質合金刀具,切削速度宜用 80~150米/分;車削聚氯乙烯或尼龍、電木等熱塑性塑料時,切削速度可達200~600米/分。
銑削塑料時,採用高速鋼刀具,切削速度一般為35~100米/分;採用硬質合金刀具,切削速度可提高2~3倍。
塑料鑽孔可用螺旋角較大的麻花鑽頭,孔徑大於30毫米時,可用套料鑽。採用高速鋼鑽頭時,常用切削速度為40~80米/分。由於塑料有膨縮性,鑽孔時所用鑽頭直徑應比要求的孔徑加大0.05~0.1毫米。鑽孔時,塑料下面要墊硬木板,以阻止鑽頭出口處孔壁周圍的塑料碎落。
刨削和插削的切削速度低,一般不宜用於切削塑料,但也可用木工刨床進行整平和倒棱等工作。攻絲時可採用溝槽較寬的高速鋼絲錐,並用油潤滑;外螺紋可用螺紋梳刀切削。對尼龍、電木和膠木等熱固性塑料,可以用組織疏鬆的白剛玉或碳化硅砂輪磨削,也可用砂布(紙)砂光,但需用水冷卻。由於熱塑性塑料的磨屑容易堵塞砂輪,一般不宜磨削。
車削硬橡膠工件時,可用刃口鋒利的硬質合金車刀(前角為12°~40°,后角為10°~20°),採用150~400米/分的切削速度,可以干車,也可用水或壓縮空氣冷卻。如用高速鋼刀具車削,切削速度要低些。
硬橡膠鑽孔可用頂角為80°左右的硬質合金或高速鋼麻花鑽頭干鑽。當鑽削孔徑為10~20毫米時,切削速度可取21~24米/分。硬橡膠工件也可用松而軟的砂輪磨削。
玻璃(包括鍺、硅等半導體材料)的硬度高而脆性大。對玻璃的切削加工常用切割、鑽孔、研磨和拋光等方法。
對厚度在 3毫米以下的玻璃板,最簡單的切割方法是:用金剛石或其他堅硬物質在玻璃表面手工刻劃,利用刻痕處的應力集中,即可用手摺斷。
玻璃的機械切割一般採用薄鐵板(或不鏽鋼薄片)製成的圓鋸片,並在切削過程中加磨料和水。常用的磨料是粒度為 400號左右的碳化硅或金剛石。當需要把圓棒形的半導體錠料切割成 0.4毫米左右厚度的晶片時,有採用環形圓鋸片,利用其內圓周對棒狀錠料進行切割的,切割0.4毫米厚度的晶片,切縫寬約為0.1~0.2毫米。方形晶片平面的切割常採用薄片砂輪直接劃出划痕后折斷,圓形晶片也可採用超聲波切割。
研磨和拋光玻璃的工作原理與金屬的相似。研磨后的玻璃表面是半透明的細毛面,必須經過拋光后才能成為透明的光澤表面。研磨壓力一般取1000~3000帕,磨料可用粒度為W5~20號的石英砂、剛玉、碳化硅或碳化硼,水與磨料之比約為 1:2。玻璃研磨后,平整的毛面常留有平均深度為4~5微米的凹凸層,且有個別裂紋深入表裡,故拋光時常需去除厚達20微米玻璃層,這個厚度約為研磨去除量的1/10左右,但拋光所需的時間遠比研磨長(數小時到數十小時)。拋光碟的材料通常採用毛氈、呢絨或塑料,所用磨料是粒度W5號以下的氧化鐵(紅粉)、氧化鈰和氧化鋯等微粉(直徑 5微米以下)。研磨時加等量的水製成懸浮液作為拋光劑,在 5~20℃的環境溫度下工作效果較好。
在玻璃上鑽削大孔或中孔時,一般用端部開槽的銅管或鋼管作為鑽頭,在30米/分的切削速度下進行,同時在鑽削部位注入碳化硅或金剛石磨料和潤滑油。鑽孔時,玻璃必須用毛氈或橡膠墊平,以防壓碎。對孔徑5毫米以下的小孔常採用衝擊鑽孔法,即用硬質合金圓鑿以2000轉/分左右的轉速,同時通過電磁振蕩器使圓鑿給玻璃表面以6千赫的振動衝擊,這種方法的效率很高,只要10秒鐘就可鑽出孔徑2毫米、深5毫米的小孔。對方孔和異形孔採用超聲波(18~24千赫)加工最為方便。
玻璃的外圓加工一般用碳化硅砂輪磨削,也可用金剛石車刀或負前角的硬質合金車刀在2000轉/分左右的轉速下進行車削。
對大理石、花崗石和混凝土等堅硬材料的加工主要用切割、車削、鑽孔、刨削、研磨和拋光等方法。切割時可用圓鋸片加磨料和水;外圓和端面可採用負前角的硬質合金車刀以10~30米/分的切削速度車削。鑽孔可用硬質合金鑽頭,切削速度為4~7米/分。大的石料平面可用硬質合金刨刀或滾切刨刀刨削;精密平滑的表面可用三塊互為基準對研的方法或磨削和拋光的方法獲得。