共找到3條詞條名為高爐的結果 展開
- 冶鍊設備
- Minecraft中的一種物品
- 焚化設備
高爐
冶鍊設備
高爐是用鋼板作爐殼,殼內砌耐火磚內襯。高爐本體自上而下分為爐喉、爐身、爐腰、爐腹、爐缸5部分。由於高爐煉鐵技術經濟指標良好,工藝簡單,生產量大,勞動生產效率高,能耗低等優點,故這種方法生產的鐵佔世界鐵總產量的絕大部分。
高爐生產時從爐頂裝入鐵礦石、焦炭、造渣用熔劑(石灰石),從位於爐子下部沿爐周的風口吹入經預熱的空氣。在高溫下焦炭(有的高爐也噴吹煤粉、重油、天然氣等輔助燃料)中的碳同鼓入空氣中的氧燃燒生成的一氧化碳和氫氣,在爐內上升過程中除去鐵礦石中的氧,從而還原得到鐵。煉出的鐵水從鐵口放出。鐵礦石中未還原的雜質和石灰石等熔劑結合生成爐渣,從渣口排出。產生的煤氣從爐頂排出,經除塵后,作為熱風爐、加熱爐、焦爐、鍋爐等的燃料。高爐冶鍊的主要產品是生鐵,還有副產高爐渣和高爐煤氣。
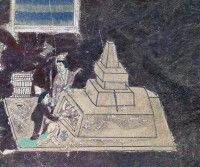
古代高爐想象圖
大約四萬年前,山頂洞人已經用赤鐵礦作顏料和裝飾品。
赤鐵礦是最易還原的鐵礦石,赤鐵礦進入人類生活,預示著日後冶鐵術的發明。西安半坡遺址出土的六千年前的陶窯,說明當時我們的祖先已經熟練地掌握了火的使用。
商代硬陶的燒成溫度已達1180℃。
這種高溫為金屬冶鍊準備了良好的條件。而商代煉銅技術的進步,對高爐的出現更具有決定意義。一,高爐起源於煉銅爐中國早期煉銅的原料是氧化礦,其中包括孔雀石。
已經發掘的殷商和春秋時期的冶銅遺址中,銅礦與赤鐵礦放在一起,銅渣中的氧化鐵含量很高,有的達到40帕左右。
這些遺物證實,在煉銅過程中,易還原的鐵礦石曾經被帶到爐內。戰國時期的文獻《山海經》,對銅礦與鐵礦伴生曾有多次記載:白馬山“其陰多鐵,多赤銅”,丙山“多金、銅、鐵”。
這種伴生現象,可能是煉銅爐最早使用含銅鐵礦的原因。純銅熔點是1083℃。銅中含鐵成分愈高,熔點也愈高。煉銅爐在始初階段溫度較低,原料中的鐵不可能大量還原出來。隨著煉銅爐加高、擴大,爐料在爐內經過充分預熱,爐溫逐漸提高,如超過1300℃就有可能煉出生鐵。
歷史
目前所知最古老高爐是中國西漢時代(紀元前1世紀)熔爐。在紀元前5世紀中國文物中就發現鑄鐵出土可見該時代熔煉已經實用化。初期熔爐內壁是用粘土蓋的,用來提煉含磷鐵礦。西方最早的熔爐則是於瑞典1150年到1350年間出現。這兩國的熔爐都是自行發展摸索出現,沒有互相傳達關係。
使用石炭的近代高爐出現於1709年。由於歐洲當時森林多用途砍伐導致木炭產量減少、被迫開發使用石炭的煉鐵法導致新技術出現,大幅增加煉鐵效率。
![高爐[冶鍊設備]](https://i1.twwiki.net/cover/w200/md/2/md2a93fca02d8736952a49c178f0e524e.jpg)
高爐[冶鍊設備]
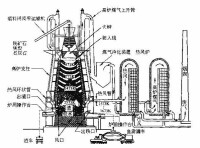
高爐結構
高爐冶鍊用的原料主要由鐵礦石、燃料(焦炭)和熔劑(石灰石)三部分組成。
通常,冶鍊1噸生鐵需要1.5-2.0噸鐵礦石,0.4-0.6噸焦炭,0.2-0.4噸熔劑,總計需要2-3噸原料。為了保證高爐生產的連續性,要求有足夠數量的原料供應。
因此,無論是生鐵廠家還是鋼廠採購原料的工作是尤其重要。
![高爐[冶鍊設備]](https://i1.twwiki.net/cover/w200/mf/4/mf43a3866a5c9ae1945c444c07f83481b.jpg)
高爐[冶鍊設備]
上料、配料系統
高爐上料是煉鐵高爐系統中最重要的一環,及時、準確的配料、上料是保證高爐產量和產品質量的前提。根據現代化高爐的要求,上料控制系統需要實現自動上料及上料數據的報表列印,體現系統穩定性、先進性和經濟實用性,因此從設計的初級階段到完成應用階段,需要一直採用先進的控制方案和硬體控制系統,才能最終完成了這一重要的系統。目前國內常用的配料方法有兩種,即容積配料法和重量配料法。容積配料法是利用物料的堆比重,通過給料設備對物料容積進行控制,達到配加料所要求的添加比例的一種方法。此法優點是設備簡單,操作方便。其缺點是物料的堆比重受物料水分、成分、粒度等影響。所以,儘管閘門開口大小不變,若上述性質改變時,其給料量往往不同,造成配料誤差。重量配料法是按照物料重量進行配料的一種方法,該法是藉助於電子皮帶稱和定量給料自動調節系統實現自動配料的。
高爐內襯
高爐爐殼內部砌有一層厚345~1150毫米的耐火磚,以減少爐殼散熱量,磚中設置冷卻設備防止爐殼變形。高爐各部分磚襯損壞機理不同,為了防止局部磚襯先損壞而縮短高爐壽命,必須根據損壞、冷卻和高爐操作等因素,選用不同的耐火磚襯。爐缸、爐底傳統使用高級和超高級粘土磚。這部分磚是逐漸熔損的,因收縮和砌磚質量不良,過去常引起重大燒穿事故,爐缸、爐底大多用碳素耐火材料,基本上解決了爐底燒穿問題。爐底使用碳磚有三種型式:全部為碳磚;爐底四周和上部為碳磚,下部為粘土磚或高鋁磚;爐底四周和下部為碳磚,上部為粘土磚或高鋁磚。后兩種又稱為綜合爐底。設計爐底厚度有減薄趨勢(由0.5d右減至0.3d左右或爐殼內徑的1/4厚度,d為爐缸直徑)。碳磚的缺點是易受空氣、二氧化碳、水蒸氣和鹼金屬侵蝕。爐腰特別是爐身下部磚襯,由於磨損、熱應力、化學侵蝕等,容易損壞。採用冷卻壁的高爐,投產兩年左右,爐身下部磚襯往往全被侵蝕。爐身上部和爐喉磚襯要求具有抗磨性和熱穩定性的材料,以粘土磚為宜。爐腹磚襯被侵蝕后靠“渣皮”維持生產。
近幾年應用噴補技術修補磚襯已相當普遍。噴補高鋁質耐火材料(含Al2O340~60%),壽命為砌襯的3/4。
產品
生鐵是高爐產品(指高爐冶鍊生鐵),而高爐的產品不只是生鐵,還有錳鐵等,屬於鐵合金產品。錳鐵高爐不參加煉鐵高爐各種指標的計算。高爐煉鐵過程中還產生副產品水渣、礦渣棉和高爐煤氣等。
高爐煉鐵的特點:規模大,不論是世界其它國家還是中國,高爐的容積在不斷擴大,如我國寶鋼高爐是4063立方米,日產生鐵超過10000噸,爐渣4000多噸,日耗焦4000多噸。
冶鍊過程
高爐冶鍊是把鐵礦石還原成生鐵的連續生產過程。鐵礦石、焦炭和熔劑等固體原料按規定配料比由爐頂裝料裝置分批送入高爐,並使爐喉料面保持一定的高度。焦炭和礦石在爐內形成交替分層結構。礦石料在下降過程中逐步被還原、熔化成鐵和渣,聚集在爐缸中,定期從鐵口、渣口放出。
鼓風機送出的冷空氣在熱風爐加熱到800~1350℃以後,經風口連續而穩定地進入爐缸,熱風使風口前的焦炭燃燒,產生2000℃以上的熾熱還原性煤氣。上升的高溫煤氣流加熱鐵礦石和熔劑,使成為液態;並使鐵礦石完成一系列物理化學變化,煤氣流則逐漸冷卻。下降料柱與上升煤氣流之間進行劇烈的傳熱、傳質和傳動量的過程。
下降爐料中的毛細水分當受熱到100~200℃即蒸發,褐鐵礦和某些脈石中的結晶水要到500~800℃才分解蒸發。主要的熔劑石灰石和白雲石,以及其他碳酸鹽和硫酸鹽,也在爐中受熱分解。石灰石中CaCO3和白雲石中MgCO3的分解溫度分別為900~1000℃和740~900℃。鐵礦石在高爐中於400℃或稍低溫度下開始還原。部分氧化鐵是在下部高溫區先熔於爐渣,然後再從渣中還原出鐵。
焦炭在高爐中不熔化,只是到風口前才燃燒氣化,少部分焦炭在還原氧化物時氣化成CO。而礦石在部分還原並升溫到1000~1100℃時就開始軟化;到1350~1400℃時完全熔化;超過1400℃就滴落。焦炭和礦石在下降過程中,一直保持交替分層的結構。由於高爐中的逆流熱交換,形成了溫度分佈不同的幾個區域,①區是礦石與焦炭分層的干區,呈塊狀帶,沒有液體;②區為由軟熔層和焦炭夾層組成的軟熔帶,礦石開始軟化到完全熔化;③區是液態渣、鐵的滴落帶,帶內只有焦炭仍是固體;④風口前有一個袋形的焦炭迴旋區,在這裡,焦炭強烈地迴旋和燃燒,是爐內熱量和氣體還原劑的主要產生地。
冷卻系統
早期的小高爐爐壁無冷卻設備,19世紀60年代高爐磚襯開始用水冷卻。冷卻設備主要有冷卻水箱和冷卻壁兩種。因高爐各部分熱負荷而異。爐底四周和爐缸使用碳磚時採用光面冷卻壁。爐底之下可用空氣、水或油冷卻。爐腹使用碳磚時可從外部向爐殼噴水冷卻,使用其他磚襯時,用冷卻水箱或鑲磚冷卻壁。爐腰和爐身下部多採用傳統的銅冷卻水箱,左右間距250~300毫米,上下間距1~1.5米。爐身上部可採用各種形式的冷卻設備,一般用鑄鐵或鋼板焊接的冷卻水箱。近幾年來爐腰和爐身有的用鑲磚冷卻壁汽化冷卻。但爐身下部由於熱負荷較高,多改用強制循環純水冷卻;爐喉一般不冷卻。冷卻介質過去使用工業水,現在改用軟水和純水。直流或露天循環供水系統也已被強制循環供水系統所代替,後者優點是熱交換好、無沉澱、消耗水量少等。
2、打水停爐降料面時,禁止開大鐘。大鐘上不準有積水。至少每1h分析一次煤氣中二氧化碳和氫的含量,氫含量不得超過6%。
3、應有爐頂專用水泵,爐頂溫度應保持在400~500℃之間。爐頂打水應採用均勻雨滴狀噴水,防止水流順爐牆流下引起爐牆塌落。
4、大、中修的高爐,料面降至風口水平面時,即可休風停爐。大修高爐應在爐底(爐缸)水溫差較大的位置上開殘鐵口眼,要放盡殘鐵。
一、高爐結瘤事故的預防
高爐結瘤的原因是多種多樣的,其基本成因是已熔化的物質再凝結,並粘附於爐牆上逐步長大,對其成因應提前採取預防措施,防止高爐結瘤事故的出現。
1)穩定原燃料質量
原燃料質量差、含粉量大,在低料線時極易導致粉末聚集,誘發上部結瘤;同時,粉末聚集層下到軟熔帶時易引發透氣性變差,出現小崩料和小滑尺現象,控制不當易誘發爐涼等事故,影響高爐冶鍊的正常進行。原燃料質量差,容易導致爐況失常,出現難行懸料,使得頂溫升高,不能得到有效控制,極易導致上部結瘤。為此,在生產組織中,應根據原燃料質量確定高爐的冶鍊方案,保證高爐穩定順行,對小的爐況波動進行先期處理,防止出現大的爐況失常。
2)禁止長期低料線作業
長期低料線作業會破壞高爐順行,使裝料制度受到嚴重破壞,同時可導致高爐熱制度被打亂,使高爐溫度場紊亂繼而誘發爐牆結厚甚至結瘤。根據低料線作業的具體原因應採取不同的針對性措施,對上料能力不足的應選擇適宜的批重,用提高料車滿載率來提高上料能力,保證高爐滿料線率。對由於設備故障造成的低料線,應採取相應的措施予以調劑,應注意在趕料線時可採取適當發展邊緣的裝料制度,根據料線的深度加足凈焦或適當減輕負荷,確保高爐爐溫充沛、爐況穩定順行。
3)及時處理邊緣堆積
高爐採取強化冶鍊措施后,裝料制度與送風制度未及時進行再匹配時,容易導致邊緣堆積。具體表現為鐵前易憋壓,對減風操作爐況好轉敏感,上下渣溫差大,經常出現小崩料和滑尺,下料不均,風口工作不均衡。為此,對邊緣堆積應及時處理,採取增大風口直徑的送風制度、適宜強度的高爐操作、發展邊緣的裝料制度、降低爐渣鹼度的造渣制度、確定適宜爐溫的熱制度進行調劑,必要時採用洗爐劑洗爐或以全倒裝強烈發展邊緣的操作方法,用高溫煤氣沖刷結厚的爐牆。
4)控制適宜的冷卻強度
高爐冷卻制度不合理也會促發爐牆結瘤,為此,應根據高爐的實際運行情況,對各部位確定適宜的冷卻強度,如對爐身部位冷卻水在開爐初期應適當控制其冷卻強度,防止在此部位形成瘤根,進而造成高爐結瘤等惡性事故的出現。
5)穩定操作方針
高爐操作可變因素較多,高爐冶鍊進程是在相對穩定的基礎上運行的。為此,高爐操作者應一絲不苟地貫徹操作方針、統一各班操作,減少人為操作波動,使爐內溫度場保穩定均衡,防止人為造成爐況波動,導致高爐結瘤。
6)及時消除爐牆結厚
爐牆結厚如果處理不當或處理不及時,極易引發高爐結瘤。因此,對爐牆結厚徵兆應及時採取果斷措施進行處理,在高爐強化冶鍊時不定期採取發展邊緣的裝料制度或採取降低冶鍊強度的操作措施對爐況進行適當的預防性處理,防止出現惡性結瘤事故。
7)減少附加料大量入爐
附加料低熔點化合物大量入爐,在條件具備時便會引發高爐結瘤事故。為此,在生產組織時應控制好生產節奏,確定附加料最大配入量,調整好爐料結構,使生產組織在受控狀態下有序運行,防止高爐結瘤事故的發生。
8)減少鐵前各工序變料
鐵前各工序的每一次變料都會給高爐帶來不同程度的波動,在生產組織管理時,應盡量用長遠的眼光組織各工序在一定時期內不變料,變料后應做好技術跟蹤與服務工作,對變料后引起的爐況波動做提前判斷、事先預防。高爐結瘤事故是爐況失常的綜合體現,避免小的爐況波動,就會有效地防止其產生的根基,也會贏得高爐操作的主動權,達到高爐操作的預期效果。
二、高爐結瘤事故的處理
1)綜合判斷,下化中洗上炸
在爐況失常時,應臨時成立爐況處理領導小組,控制方案和措施由高爐操作者具體實施。領導小組在對高爐爐況進行綜合判斷得出結論時,應在充分研討的基礎上,確定處理爐況方案。在對爐瘤部位進行判斷後,應採取下部化中部洗上部炸的措施,對中下部爐瘤應以集中加串焦或加洗爐料進行洗爐,用高溫煤氣流沖刷的方式予以處理;同時,要調整好相應的送風制度和裝料制度,使其達到預期的效果。
2)制定措施,降料面露爐瘤
對上部爐瘤,應果斷做出炸瘤決定,及早制定炸瘤措施,確定爐瘤位置,加長探尺降料面,將爐瘤徹底裸露,隔離其與爐料的依附,為實施炸瘤創造必要的條件。在降料面的過程中,應保證兩個探尺工作正常,處理爐況不能頻繁拉風,有富氧的高爐應充分利用富氧條件處理爐況,防止在處理爐瘤的過程中導致爐瘤快速長大。
3)前期準備,確定炸瘤方案
對上部爐瘤進行爆破時,應做好前期準備工作,準備好炸瘤工具,如鋼管、炮泥、廢舊布袋等,然後從下至上進行炸瘤,注意每次炸瘤炮藥用量,防止損壞爐頂設備等。炸瘤應選准突破口而後予以實施,並注意人身安全等,應將瘤根徹底清除。
4)爐況恢復,及時出凈渣鐵
炸瘤之前應加足空焦,炸瘤后也應補充相應的熱量,根據爐瘤大小確定炸瘤后的操作,及時出凈化瘤后的物質量,防止後續事故的再發生;待爐瘤化解完畢后,逐一穩定每一項操作參數,而後將爐況完全恢復。
一、毒物危害分析
高爐項目涉及有毒物主要為一氧化碳,一氧化碳主要存在於熱風爐作業,爐前出鐵作業。一氧化碳對人體的危害如下:一氧化碳經呼吸道吸入,屬窒息性氣體,主要引起人體急性中毒,一氧化碳進入人體,與血紅蛋白結合,導致機體缺氧,患者出現頭痛、頭暈、噁心,甚至死亡。慢性危害不明顯。危害級別Ⅱ級。
二、防毒措施安全檢查
1、生產裝置應密封化、管道化,防止有毒物質泄漏、外逸;
2、生產過程機械化、程序化和自動控制使作業人員不接觸或少接觸有毒物質,防止誤操作造成中毒事故;
3、受技術、經濟條件限制,仍然存在有毒物質逸散且自然通風不能滿足要求時,應設置必要的機械通風排毒;
4、對排出的有毒氣體、液體、固體應經過相應的凈化裝置處理,以達到環境保護排放標準;
5、對有毒物質泄漏可能造成重大事故的設備和工作場所,必須設置可靠的事故處理裝置和應急防護裝置;
6、根據有毒物質的性質、有毒作業的特點和防護要求,在有毒作業環境中應配置事故櫃、急救箱和個體防護裝置;
7、針對缺氧危險工作環境以及發生缺氧窒息和中毒窒息的原因,應配備通風換氣設備和搶救器具;
8、有缺氧、窒息危險的工作場所,應在醒目處設置警示標誌。
(1)對高爐出鐵時在鐵口、砂口、渣溝、擺動溜槽、鐵溝等處產生的煙塵採用低壓長袋脈衝除塵器除塵;對槽上、槽下系統的含塵煙氣,採用100m三電場高壓靜電除塵器除塵,處理達標後由高煙囪排放。收集下來的粉塵經加濕后運灰車運走,防止二次揚塵。
(3)熱風爐、鍋爐房煙氣由高煙囪直接外排。
(4)高爐煤氣除塵採用濕式——溫(VS)煤氣清洗系統,煤氣經除塵后含塵濃度很低。
(5)車間內、料場還設有洒水抑塵、沖洗地面設施,減少崗位粉塵對人體的危害。
(6)對於粉塵作業的職工配備相應的個人防護用品,包括呼吸道防塵用品、身體防塵用品(防塵帽、防塵服等)。
(1)運人、儲存與放料系統。大中型高爐的原料和燃料大多數採用膠帶機運輸,比火車運輸易於自動化和治理粉塵。儲礦槽未鋪設隔柵或隔柵不全,周圍沒有欄桿,人行走時有掉入槽的危險;料槽形狀不當,存有死角,需要人工清理;內襯磨損,進行維修時的勞動條件差;料閘門失靈常用人工捅料,如料突然崩落往往造成傷害。放料時的粉塵濃度很大,尤其是採用膠帶機加振動篩篩分料時,作業環境更差。因此,儲礦槽的結構應是永久性的、十分堅固的。各個槽的形狀應該做到自動順利下料,槽的傾角不應該小於50°,以消除人工捅料的現象。金屬礦槽應安裝振動器。鋼筋混凝土結構,內壁應鋪設耐磨襯板;存放熱燒結礦的內襯板應是耐熱的。礦槽上必須設置隔柵,周圍設欄桿,並保持完好。料槽應設料位指示器,卸料口應選用開關靈活的閥門,最好採用液壓閘門。對於放料系統應採用完全封閉的除塵設施。
(2)原料輸送系統。大多數高爐採用料車斜橋上料法,料車必須設有兩個相對方向的出入口,並設有防水防塵措施。一側應設有符合要求的通往爐頂的人行梯。卸料口卸料方向必須與膠帶機的運轉方向一致,機上應設有防跑偏、打滑裝置。膠帶機在運轉時容易傷人,所以必須在停機后,方可進行檢修、加油和清掃工作。
(3)頂爐裝料系統。通常採用鍾式向高爐裝料。鍾式裝料以大鐘為中心,有大鐘、料斗、大小鍾開閉驅動設備、探尺、旋轉布料等裝置組成。採用高壓操作必須設置均壓排壓裝置。做好各裝置之間的密封,特別是高壓操作時,密封不良不僅使裝置的部件受到煤氣沖刷,縮短使用壽命,甚至會出現大鐘掉到爐內的事故。料鐘的開閉必須遵守安全程序。為此,有關設備之間必須連鎖,以防止人為的失誤。