稀薄燃燒發動機
混合氣中汽油含量低的發動機
稀薄燃燒發動機就是混合氣中的汽油含量低,汽油與空氣之比可達1:25以上的發動機。
發動機混合氣中的汽油含量低,汽油與空氣之比可達1:25以上[Lean burn refers to the use of lean mixtures in an internal combustion engine. The air-fuel ratios can be as high as 25:1, so the mixture has considerably less fuel in comparison to the stoichiometric combustion ratio (14.7:1 for petrol for example).]
上世紀70年代,受到石油危機及排放法規收緊的影響,人們開始對稀薄燃燒技術產生濃厚的興趣。從理論上來講,稀薄燃燒既實現了燃料的充分利用,又可大幅降低發動機的換氣損失,同時還能減少污染物的排放,可謂是一舉多得。
當時,最先提出技術方案的是日本的豐田與本田兩家企業。由它們設計的一種帶有副燃燒室的發動機,便能實現利用稀薄混合氣驅動發動機做功,再用氧化催化器凈化排出的尾氣。可遺憾的是,由於從副燃燒室噴出火焰再傳導到主燃燒室,熱量損失過大,其最終的節油效果相比普通汽油機並未有明顯改善。
到了上世紀80年代,豐田、本田、通用等公司先後設計出了一種具有開口式燃燒室的稀薄燃燒發動機,用以取代此前的副燃燒室設計。這種燃燒室不僅在熱量損失上比原設計要小上很多,且對缸內渦流的形成效果也更為出色。
與此同時,隨著燃料噴射更加精細化,以及各類感測器的日趨成熟和精確,精密控制空燃比已成為可能。故在這一時期,微機控制電噴技術也逐漸在稀薄燃燒發動機中得到普及。其中最具代表性的莫過於豐田T-LCS(豐田稀薄燃燒系統),該系統採用了速度密度型汽油噴射裝置,能各種工況下,對噴油時間、噴油量及點火時間等參數進行精確、高效調節,進而使發動機擁有更為理想的工作狀態。
不過要說稀薄燃燒發動機真正嶄露頭角,那已經是上世紀90年代后的事情了。
藉此契機,將缸內直噴技術與稀薄燃燒技術相結合,開始成為燃燒燃燒技術研發的新寵。相較於採用氣道噴射稀薄燃燒技術,直噴稀薄燃燒技術在能量榨取上可謂是更加“窮凶極惡”。不僅將前者的優點完整加以保留,且在動力輸出指標上,也普遍高出將近一成。
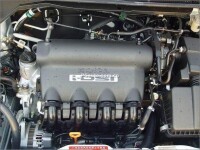
稀薄燃燒發動機
稀薄燃燒技術的最大特點就是燃燒效率高,經濟、環保,同時還可以提升發動機的功率輸出。因為在稀薄燃燒的條件下,由於混合氣點火比理論空燃比條件下困難,暴燃也就更不容易發生,因此可以採用較高的壓縮比設計提高熱能轉換效率,再加上汽油能在過量的空氣里充分燃燒,所以在這些條件的支持下能榨取每滴汽油的所有能量。
車汽油發動機實現稀燃的關鍵技術歸納起來有以下三個主要方面:
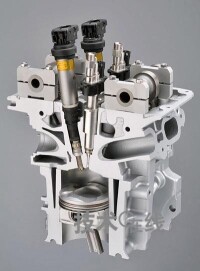
稀薄燃燒發動機
高能點火和寬間隙火花塞有利於火核形成,火焰傳播距離縮短,燃燒速度增快,稀燃極限大。有些稀燃發動機採用雙火花塞或者多極火花塞裝置來達到上述目的。
比較著名的三菱缸內噴注汽油機(GDI),可令混合比達到40:1。它採用立式吸氣口方式,從氣缸蓋的上方吸氣的獨特方式產生強大的下沉氣流。這種下沉氣流在彎曲頂面活塞附近得到加強並在氣缸內形成縱向渦旋轉流。在高壓旋轉噴注器的作用下,壓縮過程後期被直接噴注進氣缸內的燃料形成濃密的噴霧,噴霧在彎曲頂面活塞的頂面空間中不是擴散而是氣化。這種混和氣被縱向渦旋轉流帶到火花塞附近,在火花塞四周形成較濃的層狀混和狀態。這種混合狀態雖從燃燒室整體來看十分稀薄,但由於呈現從濃厚到稀薄的層狀分佈,因此能保證點火併實現穩定燃燒。
大眾的直噴汽油發動機(FSI),則是採用了一個高壓泵,汽油通過一個分流軌道(共軌)到達電磁控制的高壓噴射氣門。它的特點是在進氣道中已經產生可變渦流,使進氣流形成最佳的渦流形態進入燃燒室內,以分層填充的方式推動,使混合氣體集中在位於燃燒室中央的火花塞周圍。
本田最新的VTEC發動機也將採用稀燃技術。這款取名為VTEC-i 2.0升發動機將比一般本田發動機省油20%,其特點是將VTEC技術與稀燃技術相結合,也是當低轉速時令其中一組進氣門關閉,在燃燒室內形成一道稀薄的混合氣體渦流,層狀分佈集結在火花塞周圍作點燃引爆,從而起到稀薄燃燒作用。
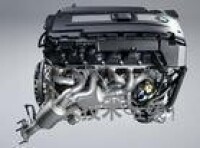
稀薄燃燒發動機
隨著空燃比的增加,由於採用稀的混合氣使燃燒溫度降低,NOx的排放明顯減少,同時燃燒產物中的氧成分有利於HC和CO的氧化,因此,HC和CO的排放也減小,然而,隨著空燃比增加到一定程度,由於燃燒速度的降低可能會使燃燒不完全,HC的排放會迅速增加。如果能合理地設計緊湊的燃燒室,並組織好空氣運動使燃燒在短時間內完成,那麼三種排放都可以大大減少。
根據稀燃發動機運轉狀態,在分層稀薄燃燒到均質理論空燃比燃燒過程中,空燃比連續變化。因此,三效催化轉化器不能夠凈化排放氣體中的NOx。這是因為三效催化轉化器要利用排氣中的HC或CO進行NOx還原反應的緣故。在稀薄燃燒中,在排放氣體中殘留很多氧氣,不能進行NOx還原反應。為了使NOx吸儲型催化劑獲得高效功能,其溫度必須保持在250-500℃範圍內。當超過這一溫度範圍發動機會自動轉換到均質理論空燃比燃燒,並通過三效催化轉化器進行廢氣處理。
然而這又與燃油經濟性下降相關,為此,必須增加廢氣冷卻裝置。
利用這種冷卻裝置,排放氣體通過NOx吸儲型催化轉化而被冷卻,由於稀薄燃燒的範圍寬,催化轉化器的壽命也延長。然而,NOx吸儲型催化轉化器會受到硫侵蝕而中毒,所以必須把汽油中的含硫量盡量降低到最少。但是,如前所述,含硫低的汽油不是到處能供應的。大眾汽車公司採取的措施是,把催化劑反應溫度提高到650°以上,從而把附著在催化劑上的硫通過燃燒而加以消除。
在高速行駛時,能夠保持這樣高的催化劑溫度,但是,在城市內行駛時則催化劑溫度下降,就不能燒除附著在催化劑的硫。為此,通過NOx感測器監視硫附著在催化劑上的程度,根據監測情況提高排放氣體的溫度。
作為其措施,一般採用點火正時延遲,儘管這樣做會引起燃油經濟性惡化,但是為了凈化處理NOx,這是不得已而為之。
另外,稀燃發動機由於噴射器的加入導致了對設計和製造的要求都相當的高,如果布置不合理、製造精度達不到要求導致剛度不足甚至漏氣只能得不償失。
稀燃發動機對燃油品質的要求也比較高。
那經歷了數十年的發展演變,今天稀薄燃燒技術又是何種模樣呢?
首先,從技術角度來看,其主要呈現出兩大特點。
1.超稀薄燃燒愈發受到關注。前年紅極一時的本田的i-VTEC I型直噴汽油發動機,其空燃比可達65:1,這要放在稀薄燃燒技術的發展初期,簡直就是痴人說夢。
2.結構大幅精簡,控制漸成核心。無論是本田的VETC-i,還是三菱的MVV,與早期的稀薄燃燒系統相比,其自身構造都得到了相當程度上的簡化,並逐漸趨於穩定。利用多氣門及精確噴射控制,繁冗的硬體結構被塵封史冊,取而代之的是對軟體方面的不斷優化。
其次,雖然當今的稀薄燃燒技術稱得上是遍地開花,叫法各異,但實際上若以噴油方式對其加以分門別類,卻又基本上可劃歸為氣道噴射稀薄燃燒(PFI)與缸內直噴稀薄燃燒(GDI)兩種實現形式。