PCBN刀具
用於加工鐵件的立方氮化硼刀具
PCBN刀具是人造立方氮化硼刀具,在高溫的時候還能保持高硬度的特性,主要做加工鐵件之用。立方氮化硼CBN(Cubic Boron Nitride)是20世紀50年代首先由美國通用電氣(GE)公司利用人工方法在高溫高壓條件下合成的,其硬度僅次於金剛石而遠遠高於其它材料,因此它與金剛石統稱為超硬材料。
CBN具有較高的硬度、化學惰性及高溫下的熱穩定性,因此作為磨料CBN砂輪廣泛用於磨削加工中。由於CBN具有優於其它刀具材料的特性,因此人們一開始就試圖將其應用於切削加工,但單晶CBN的顆粒較小,很難製成刀具,且CBN燒結性很差,難於製成較大的CBN燒結體,直到20世紀70年代,前蘇聯、中國、美國、英國等國家才相繼研製成功作為切削刀具的CBN燒結體——聚晶立方氮化硼PCBN(Polycrystalline Cubic Boron Nitride)。從此,PCBN以它優越的切削性能應用於切削加工的各個領域,尤其在高硬度材料、難加工材料的切削加工中更是獨樹一幟。經過30多年的開發應用,現在已出現了用以加工不同材料的PCBN刀具材質。
按添加成分分:有直接由CBN單晶燒結而成的PCBN和添加一定比例粘結劑的PCBN燒結體兩大類;按製造複合方式分:有整體PCBN燒結塊和與硬質合金複合燒結的PCBN複合片兩類。目前應用較廣的是帶粘結劑的PCBN複合片,根據添加的粘結劑比例不同則PCBN硬度也不同,粘結劑含量越多則硬度越低、韌性越好;粘結劑種類不同,則PCBN的用途也不同,如表1所示為常見粘結劑的PCBN刀具及其用途。
CBN含量(%)-粘結劑種類-主要用途
~60-TiN-淬火鋼
~70-TiC-鑄鐵
~70-Al2O3-鑄鐵
~90-AlN-高強度鑄鐵
~80-Co-耐熱合金鋼鑄鐵
由於CBN微粉中殘留有WBN、HBN、葉蠟石、石墨、鎂、鐵等雜質;另外它和結合劑粉末中均含有吸附氧、水汽等,對燒結不利。因此原材料的凈化處理方法是確保合成聚晶性能的重要環節之一。研製時我們採用下列方法對CBN微粉和結合劑材料進行凈化處理:首先在300 C左右用NaOH處理CBN徽粉,去除其中的葉蠟石和HBN;然後煮高氯酸去除石墨;最後用HCl在電熱板上煮沸除去金屬,並用蒸餾水洗至中性。結合劑用的Co、Ni、Al等採用氫還原處理。然後將CBN和結合劑按一定配比混合均勻並參入石墨模具中,送入壓力小於1E2的真空爐內,加熱800~1000°C處理1h,除去其表面的污垢、吸附氧及水汽等,使CBN晶粒表面很潔凈。
結合劑材料的選擇及加入量方面,總的結合劑加入量應充足但不能過多。實驗結果表明,聚晶耐磨性和抗彎強度等與平均自由程(粘結相層厚度)關係密切,當平均自由程為0. 8~1.2μm時,聚晶磨耗比值最高,此時結合劑摻入量為10%~15%(質量比)。
除了結合劑的選擇之外,CBN粒度及粒度配比的確定也至關重要,根摒加工精度和表面質量要求,製造切削工具用的CBN粒度大約分為:粗粒度20~30μm;中粒度3~10微米;細粒度2微米。用粗粒度做成的聚晶難以做成精度要求高的刀具,但其耐磨性、抗衝擊性較高,細粒度做成的聚晶製成刀具可滿足精加工和超精加工的要求
PCBN 複合片是直接在高溫高壓下把CBN層與硬質合金襯底複合在一起,經過切割、焊接工藝做成各種焊接成型切削刀具或刀片。
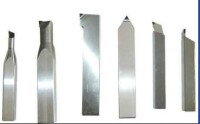
各種焊接成型PCBN刀具
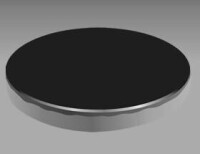
PCBN複合片
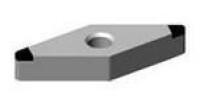
PCBN複合片製成的焊接刀片
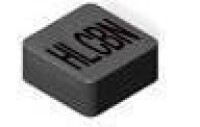
立方氮化硼整體聚晶刀片
整體PCBN燒結塊是不帶合金基體直接燒結成為整體PCBN刀肧,經過刃磨后製成立方氮化硼整體聚晶刀片。如右圖。合成設備國外所用合成設備多為兩面頂壓機,國內大多為六面頂壓機。
生產出的PCBN刀具胚體需要刃磨才能用於切削,刃磨刀具獲得正確的幾何形狀和表面粗糙度。一般分粗磨、精磨和研磨工序。粗磨採用180~240號樹脂結合劑金剛石砂輪,進刀量為0. 01 mm/雙行程;精磨用wlo~W14樹脂結合劑砂輪,進刀量為0. 005 mm/雙行程;研磨用W5~W3的金剛石砂輪或研磨膏,研磨刃磨中應特別注意金剛石砂輪的開刃修整對刃磨的影響。儘管刃磨過程中刀具在砂輪的整個端面來回擺動以使砂輪表面消耗一致,但實際上砂輪表面仍容易產生凹凸不平,須經常修整。
PCBN刀具的壽命與其幾何參數密切相關,合適的前後角可提高刀具的抗衝擊性能。排屑能力及散熱能力。前角的大小直接影響切削刃的受力情況和刀片的內應力狀態。為了避免刀尖承受機械衝擊所造成的拉應力過大,一般採用負前角(-5。~- 10。),同時為減少后角磨損,主副后角為6。,刀尖半徑為0.4–1.2mm的圓角,並倒棱研磨光滑。
1,高純度、高凈化率的原材料,可靠規範的胚體合成工藝,這兩項直接決定立方氮化硼刀具的性能。當然,這也是市場上立方氮化硼刀具價格參差不齊的最大原因。
2,磨加工,由於立方氮化硼刀具不像硬質合金刀片具備複雜槽型和塗層,性能主要取決於刀具胚體性能,而磨加工的工藝和精度直接決定切削時的微觀性能。所以採用周邊磨床,刀具成本雖然提高不少,但是立方氮化硼刀具的質量和耐用度都會上一個檔次。
3,嚴格檢驗手段:除了尺寸精度和表面質量外,立方氮化硼刀具生產過程中,最容易產生廢品的是電鏡檢測下的微觀缺陷。刃口處肉眼看不到的微觀缺陷是立方氮化硼刀具使用過程中崩刃口的導火索,容易造成使用時出現刀具扎刀問題。
從使用角度講:抗衝擊性能好,特別是粗加工領域,使用時不崩刃,不碎裂,這是立方氮化硼刀具使用安全性的最基本保證。耐磨性能好,高效加工的同時,能夠低成本的代替硬質合金刀具和陶瓷刀片,這是立方氮化硼刀具使用經濟型的保證。
由於PCBN刀具多為高端產品,製造強度大,技術門檻高,目前主要為國外製造商所控制,在2009年,複合超硬刀具材料市場全球佔有率前幾位的公司為清一色的國外公司,分別是元素六(30%)、DI公司(20%)、日本住友(18%)、韓國日進(9%)、MegaDiamond(4.5%)、TomeiDiamond(4.5%)、Dennistools(4%),幾大公司就佔據了市場的90%。
在非複合超硬刀具市場中,立方氮化硼整體聚晶刀片已經是我國的強項,河南超硬材料研究所研的HLCBN作為優勢品牌出口到歐洲、美洲等高端用戶市場的達20萬片,在我國的超硬刀具行業獨樹一幟,況且隨著國內六面頂壓機技術的成熟和普及,在整體聚晶氮化硼刀片製造工藝上比國外更有優勢。
由於CBN晶體與金剛石晶體都屬閃鋅礦型,且晶格常數相近,化學鍵類型相同,因而CBN具有接近金剛石的硬度和抗壓強度,又因為其是由N、B原子所組成,因此具有比金剛石更高的熱穩定性和化學惰性。PCBN刀具材料主要性能如下:
CBN單晶的顯微硬度為HV8000~9000,是目前已知的第二高硬度的物質,PCBN複合片的硬度一般為HV3000~5000。因此用於加工高硬度材料時具有比硬質合金及陶瓷更高的耐磨性,能減少大型零件加工中的尺寸偏差或尺寸分散性,尤其適用於自動化程度高的設備中,可以減少換刀調刀輔助時間,使其效能得到充分發揮。
CBN的耐熱性可達1400~1500℃,在800℃時的硬度為Al2O3/TiC陶瓷的常溫硬度,因此,當切削溫度較高時,會使被加工材料軟化,與刀具間硬度差增大,有利於切削加工進行,而對刀具壽命影響不大。
CBN具有很高的抗氧化能力,在1000℃時也不產生氧化現象,與鐵系材料在1200~1300℃時也不發生化學反應,但在1000℃左右時會與水產生水解作用,造成大量CBN被磨耗,因此用PCBN刀具濕式切削時需注意選擇切削液種類。一般情況下,濕切對PCBN刀具壽命無明顯提高,所以使用PCBN刀具時往往採用干切方式。
CBN材料的導熱係數低於金剛石但大大高於硬質合金,並且隨著切削溫度的提高,PCBN刀具的導熱係數不斷增大,因此可使刀尖處熱量很快傳出,有利於工件加工精度的提高。
CBN與不同材料的摩擦係數在0.1~0.3之間,大大低於硬質合金的摩擦係數(0.4~0.6),而且隨摩擦速度及正壓力的增大而略有減小。因此低的摩擦係數及優良的抗粘結能力,使CBN刀具切削時不易形成滯留層或積屑瘤,有利於加工表面質量的提高。
PCBN刀具最適合於鑄鐵、淬硬鋼等材料的高速切削加工。由PCBN刀具切削鑄鐵及淬硬鋼時刀具后刀面磨損與切削距離的關係可以看出:當切削速度超過一定限度后,切削速度越高,PCBN刀具后刀面磨損速度反而越小,即高速切削下刀具的壽命反而高,這一特點尤其適合現代高速切削加工。
對淬硬體(硬度HRC55以上)的精加工,通常採用磨削加工方法來完成,然而隨著刀具材料發展及車床(尤其是數控車床)加工精度的提高,以硬態切削代替磨削來完成零件的最終加工已成為一個新的精加工途徑,這種以車代磨的工藝方法有以下優點:
(1)可提高加工柔性,突破了砂輪磨削的限制,通過改變切削刃及走刀方式可以加工出幾何形狀各異的工件;
(2)切削加工中的環保問題日益嚴峻,磨削加工產生的廢液和廢棄物越來越難以處理和清除,而且對人體有害,而硬態切削無須加冷卻液,意義重大;
(3)切削效率高,加工時間短,設備投資費用小,可降低加工成本;
(4)切除相同體積所消耗的能量僅為磨削的20%,因此產生的切削熱較少,加工表面不易引起燒傷和微小裂紋,易於保持工件表面性能的完整性;
(5)同樣金屬去除率情況下,硬態切削較磨削節省能源。
通常用於硬態切削的刀具材料有陶瓷、TiC塗層刀片及PCBN刀具材料,但要在較高速度(1000m/min以上)下進行硬態車削,PCBN是最佳刀具材料品種。如在汽車變速箱同步器套撥叉(材料為20CrMnTi,硬度為HRC58~62)加工採用以車代磨后,效率提高4倍以上,加工成本降低為原來磨削工藝的1/3~1/2。
由於經濟與環保方面的原因,近幾年干切削加工方法已成為機械製造領域中的重點研究課題。我們首先來看一下濕切工藝由於使用切削液帶來的問題:
(1)長期暴露在空氣中或切削加工中由切削熱造成的切削液霧狀揮發,容易污染環境、危害操作者健康,切削液中的硫、氯等添加劑危害更大,影響加工表面質量;
(2)切削液的使用影響加工成本,據統計,切削液占生產成本的15%,而刀具費用僅佔3%~4%;
(3)切削液的滲漏、溢出會污染環境,易發生安全、質量事故;
(4)切削液的傳輸、回收、過濾等裝置及其維護費用較高,增加了生產成本。
由於以上原因,干切削加工工藝已在西方工業發達國家有了相當的應用。由美國Makino公司推薦的“紅月牙”(Red Crescent)干切工藝,既可以充分發揮刀具的切削性能,與濕切相比又能大大提高生產率。其機理是由於切削速度很高,產生的熱量聚集於刀具前部,使切削區附近材料達到紅熱狀態,屈服強度下降,進而達到提高切削效率的效果。採用紅月牙干切削工藝的前提條件是在較高切削溫度下,被切材料強度有明顯下降,變得易切削,而刀具材料的強度在同樣狀態下要有較好的紅硬性及熱穩定性,還要有較好的耐磨性和抗粘結性。
適用於干切工藝的刀具材料有陶瓷、金屬陶瓷、塗層硬質合金及PCBN刀具材料等等,但就紅硬性和熱穩定性來說,PCBN材料是最適合干切工藝的刀具材料,且由於PCBN刀具材料具有上述優點,更適於高速條件下的乾式切削加工,用PCBN刀具切削灰口鑄鐵干切削和濕切削兩種情況下的對比可以看出:PCBN在高速干切情況下,比濕切削具有更高的刀具壽命。
PCBN刀具有很高的硬度及耐磨性,能在高切削速度下長時間地加工出高精度零件(尺寸分散性小),大大減少換刀次數和刀具磨損補償停機所花費的時間。因此,很適合於數控機床及自動化程度較高的加工設備,並且能使設備的高效能得到充分發揮。
在難加工材料應用方面,PCBN刀具也顯示了其卓越的性能,如表面噴焊(塗)材料的加工,用其它材料刀具加工,刀具壽命極低,也無法採用磨削方法加工,而PCBN是惟一適合的刀具材料;又如,在石油電站設備中使用的高合金耐磨鑄鐵,採用PCBN刀具較硬質合金刀具提高切削效率4倍以上,單件刀具成本下降為原來的1/5。另外在硬質合金等燒結材料的切削加工方面,PCBN刀具也顯示了很好的切削性能。
由於PCBN具有較高的硬度和耐磨性,在高溫下不與鐵族金屬起反應的化學惰性,因此主要用於高硬度材料及難加工材料的切削加工,如淬硬鋼、高合金耐磨鑄鐵、高溫合金、高速鋼、表面噴焊材料、燒結金屬材料等難加工材料的切削加工。
(1)加工淬硬鋼,可起到以車代磨的效果,由於切削深度比磨削深度大十幾倍以上,因此加工效率高,表面不產生燒傷。如以車代磨加工變速滑動齒輪(20CrMnTi,硬度為HRC58~62)時,切削比原磨削加工效率提高4倍以上。
(2)加工高合金(含鎢或鉻18%)耐磨鑄鐵,切削速度較硬質合金刀具提高10倍以上,切削效率提高4倍以上。
(3)加工高鈷鉻鉬耐蝕耐熱合金,PCBN刀具切削速度為160m/min,是硬質合金刀具的8倍。
(4)加工熱噴塗(噴焊)材料,表面噴焊件無法用磨削加工,而用硬質合金刀具切削效率極低,改用PCBN刀具后可提高加工效率,節省加工費用50%以上。PCBN刀具還可用於有色金屬的精密切削及燒結金屬的切削加工等等。
如果正確選擇切削用量、刀具幾何參數及其他加工條件,則PCBN是一種高效長壽命刀具,能創造很高的經濟效益,但如果使用方法不當,則會造成很大的浪費。
(1)合理選擇切削用量:切削速度要根據被加工材料進行選擇,一般要大大高於硬質合金刀具。切削硬度HRC55~65的淬硬鋼可選切削速度為80~120m/min,由於PCBN切削硬材料是將切削區內微小區域的金屬軟化而進行的,因此切削速度過低時,就不能發揮PCBN刀具的切削性能。進給量一般不能大於0.2mm/r,背吃刀量一般選擇小於0.3mm。
(2)合理選擇刀具幾何參數:由於PCBN刀具的韌性高於陶瓷,低於硬質合金,因此刀具幾何參數的選擇主要考慮的就是保證刃口強度,刀具前角一般選擇(0°~-10°),后角選擇較小,為10°左右。除特殊要求外,為保證刀尖強度,刀尖角一般不要小於90°;刃口要磨出負倒棱,一般取為0.2mm×(-15°~-30°),使用前要用30~50倍放大鏡對刀具進行檢查,確保刃口無崩刃。
(3)冷卻與潤滑:對其他材料刀具,採用冷卻潤滑液有利於提高加工表面和延長刀具壽命,但對PCBN刀具除極特殊情況下,不加冷卻液同樣可達到理想的加工質量和較長的刀具壽命,對PCBN刀具來說是怕軟不怕硬。若使用冷卻液,則不能使用水溶性冷卻液,因為CBN易在1000℃產生水解作用,造成刀具嚴重磨損。
(4)對機床的工藝系統:由於PCBN刀具多用於淬硬鋼及耐磨鑄鐵等難加工材料的切削加工,且刀具有負倒棱,因而徑向力較大。這就要求機床剛度和精度要好,系統振動要小,刀具安裝時懸臂要小,PCBN刀具不宜用於荒面加工。
目前,雖然PCBN刀具材料的價格相對硬質合金及陶瓷刀具的價格還偏高,但均攤到每個工件上的刀具成本卻低於其他材料刀具,採用先進切削加工工藝時,若將磨削機床等設備投資攤入生產成本,則PCBN刀具的使用會帶來更大經濟效益。對一般中小企業來說,精加工工序的磨削加工始終是製造過程的瓶頸,若購置性能好的車床,採用PCBN刀具,應用以車代磨等先進切削加工工藝,即可節省設備投資、提高生產率,又可大大增加加工過程的柔性。另外,目前由於人員費用的增大及環境保護方面的要求,大力推廣使用PCBN刀具,充分發揮其潛在效能,提高切削加工技術水平也是具有重要意義的。
由於 PCBN 刀具材料具有優良的切削性能,所以特別適合加工其硬度在 HRC45 以上的淬火鋼、耐磨鑄鐵、 HRC35 以上的耐熱合金以及 HRC30 以下而其它刀片很難加工的珠光體灰口鑄鐵。
為了充分發揮 PCBN 刀片的優越性,取得滿意的加工效果,在實際使用時,除參照表 1 所推薦的 PCBN 刀片選用的切削用量外,還應根據機床、工件及其它有關條件的具體情況全面考慮,合理選擇。
硬態切削時,徑向力很大,這就要求機床功率要大,機床系統剛性要好,這既可保護 PCBN 刀具,又可獲得滿意的加工效果。裝夾 PCBN 刀具時,刀具的懸伸長度要盡量短,以防止刀桿顫振和變形,使 PCBN 刀具保持良好的加工狀態。
表 1 PCBN 刀片常用切削用量
工件材料 切削速度 (m/min) 進給量 (mm/r) 切削深度 (mm)
灰鑄鐵 180 ~ 230HB 400 ~ 1000 0.15 ~ 0.5 0.12 ~ 2.0
硬鑄鐵 400HB 70 ~ 150 0.15 ~ 0.5 0.12 ~ 2.0
淬火鋼 45HRC 60 ~ 140 0.15 ~ 0.5 0.2 ~ 2.5
耐熱合金 35HRC 100 ~ 240 0.05 ~ 0.3 0.1 ~ 2.5
2.PCBN 刀具的強度比硬質合金刀具低,因此在硬態切削加工時,一般都採用負前角、較大的后角和負倒棱,這不僅有利於對切削刃進行補強,而且具有很好的耐磨性。通常負倒棱尺寸取 (0.1 ~ 0.5)× ( 10° ~ 30° )為宜。若切削進行適當的鈍化處理,效果會更好。此外,在可能的情況下,盡量採用小主偏角和大的刀尖圓弧半徑,這有助於保護刀刃,延長刀具的使用壽命。
3. 為很好地使用 PCBN 刀具,穩定地控制工件質量,準確判斷 PCBN 刀具的耐用度至關重要。如果一直使用磨損已很嚴重的刀具,那麼切削力及切削溫度增加、切削不暢,就難以控制工件尺寸及表面完整性,甚至使 PCBN 刀具無法繼續修磨而報廢。為保證刀具的正常使用,建議 PCBN 刀具后刀面磨損量達 0.3 ~ 0.6mm( 精車時取小值 ) 時應進行重磨。但重磨需要一定的設備和技巧,多數工廠的機床不具備適合的條件,一般 PCBN 刀具的重磨都應由專業廠來完成。
4. 對於硬度高和不規則的工件,由於 PCBN 刀片較脆、怕衝擊。從工件端面切入、切出,尤其在表面有夾渣、砂眼、凹凸不平的時候,最易發生衝擊,使刃口破裂,造成耐用度降低。所以在使用 PCBN 刀具前,最好先將冷硬層粗車一次,並在工件切入切出端先倒角,以減小 PCBN 刀具衝擊力。
5.PCBN 刀具不適於加工較軟的黑色金屬材料。
6. 確定切削速度、進給量及切削深度要綜合考慮生產效率和加工成本。一般來講,其切削速度可比硬質合金刀具高 2 倍左右,高的切削速度產生大的切削熱量,使被加工材料的塑性增大,有利於控制切屑和降低切削力。
7. 使用 PCBN 刀具時,可加冷卻液,也可不加,使用冷卻液時則一定要充分冷卻。
有關使用 PCBN 刀具常見的磨損,磨損原因及預防措施見表 2。
表 2 PCBN 刀片的磨損形式、原因及預防措施
磨損形式 主要原因 預防措施
月牙窪磨損 工件硬度太軟;切速太快;產生化學和擴散磨損 改用硬質合金刀具或陶瓷刀具;降低切速 使用冷卻液
壓力面磨損 切削速度太快;進給量太大;刀具后角太小 增大切速和進給量;增大后角
邊界磨損 主偏角太大;進給量太大;切速太小 減小主偏角;減小進給量;增大切速
斷裂磨損 系統剛性差;刀尖角太小;進給量與切速太大;刀具刃口脆 提高系統剛性,增大刀尖角;降低進給量和切速並採用負倒棱刀具
PCBN 層破裂 系統剛性差;工件衝擊太大; PCBN 層太薄,刀具刃口過脆 提高工藝系統剛性;工件表面預加工和倒角;採用厚的 PCBN 層;採用負倒棱刀具
陶瓷結合劑金剛石砂輪結合金剛石和陶瓷結合劑的共同特點,具有磨削力強,磨削時溫度比較低,磨具磨損比較小;可以適應各種冷卻液的作用;磨削時磨具的形狀保持性好,磨出工件的精度高;磨具內有較多的氣孔,磨削時有利於排屑和散熱,不易堵塞、不易燒傷工件;磨具的自銳性比較好,修整間隔的時間長,修整比較容易等優點。
選擇合理的工藝參數,陶瓷結合劑金剛石砂輪在磨削PCBN刀具方面,由於樹脂結合劑較軟,磨削時容易變形,不能有效地磨削PCBN刀具;金屬結合劑由於對磨粒的結合能力太強而使磨具自銳性差,磨削效率低,而且金屬結合劑砂輪會造成PCBN刀具邊緣產生最最嚴重的破壞;綜合磨削效率、磨具耐用度及工件表面的加工質量,陶瓷結合劑金剛石砂輪是磨削PCBN刀具理想的選擇。