楔橫軋
楔橫軋
楔橫軋,即兩個帶楔形模的軋輥,以相同的方向旋轉,帶動圓形坯料旋轉,坯料在楔形型的作用下,軋製成各種形狀的台階軸。這種橫軋的變形主要為徑向壓縮和軸向延伸。
目錄
楔橫軋指圓柱形坯料在兩軋輥的模具間或在兩平板模具之間發生連續局部變形,軋製成的零件形狀和模具底部型槽的形狀一致。楔橫軋大致可以分為兩大類:輥式楔橫軋和板式楔橫軋。其中,輥式楔橫軋的成形原理:形模塊的軋輥,模塊的作用下,以相同方向旋轉,帶動圓形坯料向相反方向旋轉,兩個裝有楔坯料在楔形徑向壓縮、軸
而使軋制的零件形狀和模具底部型槽的形狀一致,如圖1-2所示。板式楔橫軋則是在上模板和下模板的相對滑動過程中,藉助裝在上、下模板的模具,使圓柱形的坯料在徑向變形的同時產生軸向變形,加工成與模具型腔形狀一致的圓柱形或圓錐形零件,如圖1-3所示。在楔橫軋軋制過程中,軋件成形經歷了四個階段,這四個階段分別對應著楔形模的四個區段,見圖1-4。整個過程如下:楔形模的起始部分使坯料旋轉起來並沿圓周方向在坯料上軋出一條由淺至深的V形溝槽,這一部分稱為楔入段,(圖1-4中L,區段);接著在其後的楔形模將由淺而深、由窄而寬的V形溝槽車L成深度和寬度一樣的V形溝槽,這一部分稱之為楔入平整段(圖1-4中L2區段);隨後楔形模使V形溝槽擴展,這一部分稱為展寬段(圖1-4中L:區段),這是軋件的主要變形區段;最後是精整段(圖1-4中L;區段),對軋件進行整形,以提高軋件的外觀質量和尺寸精度。
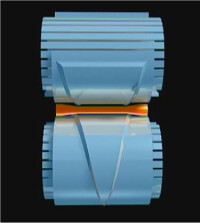
楔橫軋
與傳統的鍛造或切削工藝相比,楔橫軋工藝有如下優點}4}: (1)生產效率高,通常是其它工藝的5-20倍。如果產品的幾何形狀不太複雜,那麼使用對稱模具一次就可以加工一對工件。在實際生產中,軋輥的轉速通常為10-30rpm,那麼每分鐘至少可以軋制10--30個工件。(2)材料利用率高。通常,在傳統機械加工中(例如切削加工)約有40%的材料以切屑的形式浪費掉,而在楔橫軋工藝中僅有不足10%的材料浪費掉。(3)產品質量好。楔橫軋件金屬纖維流線沿產品外形連續分佈,並且晶粒進一步得到細化,所以其綜合機械性能較好,產品精度也高。(4)工作環境得到了改善。由於楔橫軋軋製成形過程中無衝擊,噪音小,加之無需冷卻液的使用,所以其工作環境得到了大大改善。(5)自動化程度高。車I.件從成形、表面精整到最後成品都是由機器自動完成,所需操作人員較少。
楔橫軋的局限性是:通用性差,只能生產圓截面的軸類件,需要專門的設備和模具;模具的設計、製造、及生產工藝調整比較複雜,且模具尺寸大。所以,該工藝適合軸類零件的大批量生產,不適合於小批量生產。而且不能軋制大型件,軋制棒料的長度也受到限制。因而pR需進行設計方法的創新與改進,擴大楔橫軋的應用範圍,充分發揮現有軋機的能力。
楔橫軋發展狀況早在19世紀,人們就開始探討用楔橫軋的方法生產軸類零件,但由於技術水平的限制一直未能用於生產。到1961年,捷克斯洛伐克首先將這項工藝與設備用於工業生產,其主要產品為五金工具坯、小型汽車零件等,從而成為世界上眾所周知的軸類零件加工新工藝。隨後,英國的雷德曼((Redman)公司引進了這項技術,製造出UL-3 5輥式楔橫軋機,東德的耶爾福(Erfurt)公司研發出UWQ40 X 400, UWQ80 X 630兩種搓板式楔橫軋機,同樣得到較為廣泛重視。以後,日本、蘇聯等國家也先後採用這種工藝生產軸類零件毛坯,收到了較明顯的技術經濟效果。在國外,用楔橫軋工藝已生產出上百種零件毛坯,如電機軸、汽車變速箱二軸、汽車四聯齒輪等產品的毛坯。產品的直徑範圍為6-150毫米,長度範圍為40-1200毫米。楔橫軋既可以生產零件毛坯,又可以為模鍛件制坯,還可以實現無切屑的精軋。楔橫軋工藝主要以熱軋為主,小直徑產品也可以實現冷軋。早在20世紀50年代,我國就開始楔橫軋的探討與實驗工作。上世紀60年代初,重慶大學等進行楔橫軋汽車球銷的研究工作,並獲得初步成功。70年代初,原東北工學院(現東北大學)在實驗室試軋出火車D軸的模擬件,以後與瀋陽軋鋼廠合作,試軋出火車D軸,但由於種種原因未能應用於生產之中。70年代中期,清華大學與北京電訊工具廠合作,試軋出尖嘴鉗毛坯。之後,上海鍛壓機床廠研製成功了單輥弧形楔橫軋鯉魚鉗毛坯新工藝,成功軋制出雙頭呆板手、鯉魚嘴鉗等,成為國內第一家將楔橫軋應用於生產中的單位。但由於單輥弧形式楔橫軋在模具製造、工藝調整等方面都十分困難,故一直沒能得到推廣。從70年代初起,原北京鋼鐵學院(現北京科技大學)就開展了楔橫軋技術的研究開發和推廣工作,先後幫助工廠建成楔橫軋生產線40多條,開發並應用於生產的零件130多種,包括汽車、拖拉機、摩托車、發動機、油泵與水泵等機器的軸類零件。其研究成果被國家科委列入《中華人民共和國重大科技成果(1979-1988))),並被國家科委、國家教委以及冶金工業部確立“軸類零件軋制(斜軋與楔橫軋)研究與推廣中心”。 80年代以來,機械部濟南鑄鍛研究所、鄭州機械所、北京機電研究所、吉林工業大學,先後開展了楔橫軋的研究與開發,並取得了一定進展。通過近幾年年來的研究、實踐,我國楔橫軋技術無論是在設備方面還是在工藝方面都取得了一定的進展,現己成為世界上開發和投產楔橫軋產品最多的國家之一,專業化楔橫軋廠迅猛發展起來,並帶來了顯著的經濟效益和社會效益。隨著我國汽車、摩托車等製造業的發展,楔橫軋技術必將為我國在節材、節能、高效生產領域中發揮重要的作用。階梯軸是多數通用機械中主要傳動零件,廣泛應用於機械、航空、航海等工業之中。其材質、表面質量及綜合機械性能均要求很高,階梯軸的強度對整台機器壽命影響很大,其質量的優劣,直接影響著機器的工作性能和使用壽命。目前,階梯軸的加工仍廣泛採用傳統的切削加工,存在著材料利用率低、能耗大、生產率低、成本高等不足。20世紀60年代出現的一種先進位造技術—楔橫軋工藝,以其獨特的優點引起了人們的注意,這一軸類零件新成形工藝,與傳統的鍛造、切削工藝相比有效率高、節材節能、產品精度高、模具壽命長等優點[f}l。所以該技術日益受到人們的重視,被廣泛地應用於汽車、拖拉機、摩托車、發電機上的軸類件或連桿件的生產中。而且隨著工業的快速發展與拓寬,楔橫軋產品有著巨大的國內及國際市場,發展前景廣闊。