著色劑
使食品著色的物質
著色劑是一種使食品著色的物質,可刺激食慾。按來源劃分可分為化學合成色素和天然色素兩類。允許使用的化學合成色素有:莧菜紅、胭脂紅、徠赤蘚紅、新紅、檸檬黃、日落黃、靛黃、亮藍,以及為增強上述水溶性酸性色素在油脂中分散性的各種色素。允許使用的天然色素有:甜菜紅、紫膠紅、越桔紅、辣椒紅、紅米紅等45種。
定義:任何可以使物質顯現設計需要顏色的物質都稱為著色劑。它可以是有機或無機的,可以是天然的或合成的。
以給食品著色為主要目的的添加劑稱著色劑,也稱食用色素。食用色素使食品具有悅目的色澤,對增加食品的嗜好性及刺激食慾有重要意義。
我國允許使用的化學合成色素有:莧菜紅、胭脂紅、赤蘚紅、新紅、檸檬黃、日落黃、靛藍、亮藍,以及為增強上述水溶性酸性色素在油脂中分散性的各種色素。
我國允許使用的天然色素有:甜菜紅、紫膠紅、越桔紅、辣椒紅、紅米紅等45種。
著色劑主要分顏料和染料兩種。顏料按結構可分為有機顏料和無機顏料。染料是可用於大多數溶劑和被染色塑料的有機化合物、優點為密度小、著色力高、透明度好,但其一般分子結構小,著色時易發生遷移。
可分為兩大類:天然著色劑和人工合成著色劑。
1、天然著色劑
天然著色劑是從動、植物和微生物中提取或加工而成的類胡蘿蔔素。中國常使用天然動、植物作著色劑,如把人蔘莖葉粉、萬壽菊粉、紫育精粉、木薯葉粉、松針葉粉、橘皮粉、銀合歡葉粉、胡蘿蔔、蝦蟹殼粉、海藻等作為畜、禽、水產品的著色劑。
2、合成著色劑
合成著色劑主要是類胡蘿蔔素。如β-阿朴-8-胡蘿蔔醛(C30H40O)或β-阿-朴-8-類胡蘿蔔素乙酯(C32H44O)以及檸檬黃素(C33H44O)、斑蝥素、加利紅、加利黃、露康定等。
可分為脂溶性著色劑和水溶性著色劑。
人工合成著色劑可分類偶氮類、氧蒽類和二苯甲烷類等;
天然著色劑可分為吡咯類、多烯類、酮類、醌類和多酚類等。
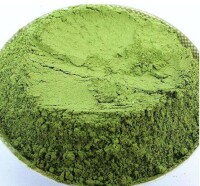
著色劑
天然著色劑主要是指由動、植物組織中提取的色素,多為植物色素,包括微生物色素、動物色素及無機色素。常用的天然著色劑有辣椒紅、甜菜紅、紅曲紅、胭脂蟲紅、高粱紅、葉綠素銅鈉、薑黃、梔子黃、胡蘿蔔素、藻藍素、可可色素、焦糖色素等等。天然著色劑色彩易受金屬離子、水質、pH值、氧化、光照、溫度的影響,一般較難分散,染著性、著色劑間的相溶性較差,且價格較高。
合成著色劑
合成著色劑的原料主要是化工產品。中國食品添加劑使用衛生標準(GB2760-1996)列入的合成色素有胭脂紅、莧菜紅、日落黃、赤蘚紅、檸檬黃、新紅、靛藍、亮藍等等。與天然色素相比,合成色素顏色更加鮮艷,不易褪色,且價格較低。
根據心理學家的分析結果,人們憑感覺接受的外界信息中,83%的印象來自視覺。產品外觀的重要性,這其中特別是外觀顏色尤為重要。就飼料產品而言,用戶用不用某種飼料產品,飼料的外觀顏色起著極重要的決定作用。對畜、禽、水產品而言,特別是禽類產品,消費者是否樂於購買食用,胴體表皮的顏色、禽蛋的卵黃顏色都是極主要的因素。畜、禽、水產品的外觀顏色取決於所採食的飼料的色素含量和累積。傳統的粗養方式,由於飼養期較長,動物機體內累積的色素、味素較多,最終產品的外觀色澤非常宜人,消費者樂於接受,產品的價格也高;相反,由於現代育種及飼養技術的迅速發展,畜、禽。魚蝦等的生長速度很快,產品的飼養期很短,因而從天然飼料中獲得的色素累積很少,產品顯得蒼白,失去對消費者的吸引力,價格亦低。由此,著色劑的添加使用在現代飼料工業和現代畜牧水產養殖業中日益普遍。
第一,通過著色劑改變飼料的色澤。特別是在日益增加使用非傳統飼料原料的情況下,添加著色劑以便掩蓋某些非傳統飼料原料(如菜籽餅粕等)的不良顏色,迎合用戶心理習慣,增加市場競爭力;同時,也起到刺激食慾和誘食的作用;
第二,通過著色劑改善畜、禽、水產品的色澤,提高其商品價值。如添加著色劑使肉雞皮膚。禽蛋卵黃、牛奶的黃油以及魚蝦等水產品的肉質具有更鮮艷、美觀的色澤和更優良的產品質量,迎合消費者的心理。
生產企業違禁添加著色劑、甜味劑,長期食用此類產品將嚴重危害人體健康。質監部門提醒消費者在選購果醬產品時務必認準品牌。果醬是以一種或多種水果為原料,經預處理、破碎或打漿、加糖濃縮等工藝製成的一種輔助食品。質監部門此次共抽查了18家企業生產的19批次果醬產品,合格13批次,抽樣合格率為68.4%。抽查結果表明,江西市場上銷售的果醬產品質量堪憂。據質監部門介紹,不合格產品存在的主要問題一是違禁添加著色劑。本次抽查的6批次不合格產品中,全部違禁添加著色劑檸檬黃,3批次產品違禁添加著色劑胭脂紅。產品中添加著色劑主要是為了使產品顏色鮮艷,利於產品銷售;二是違禁添加甜味劑。本次抽查的6批次不合格產品中,有3批次產品違禁添加甜味劑糖精鈉。這主要是由於部分企業為節約成本使用糖精鈉代替食糖生產造成的。長期食用著色劑和甜味劑超標的果醬產品,將危害消費者的身體健康。
2012年4月6日,衛生部官方網站發函,擬撤銷38種食品添加劑。其中,包含茶黃色素、茶綠色素、柑桔黃、黑加侖紅等17種著色劑。
著色劑成為塑料製品安全衛生的隱患
目前,歐美日等國家和地區對可用於食品接觸製品的著色劑種類和要求等都制定了相應規定,如歐盟AP(89)1決議對塑料著色劑質量有明確指標要求,FDA法規21CFR178.3297部分也對塑料製品中允許使用的著色劑及其最高用量做了明確規定。質量規格不符的著色劑可能帶來諸多安全衛生隱患,主要包括:致癌物質芳香胺超標、成品脫色試驗不合格以及重金屬含量超標等。此外,不合格著色劑還可能含多氯聯苯等有害物質。
影響徠著色劑著色效果的主要因素:著色劑的著色效果如何,受許多因素的影響,主要影響因素如下:
顏料是不能溶於普通溶劑的著色劑,故要獲得理想的著色性能,需要用機械方法將顏料均勻分散於塑料中。無機顏料熱穩定性、光穩定性優良,價格低,但著色力相對差,相對密度大;有機顏料著色力高、色澤鮮艷、色譜齊全、相對密度小,缺點為耐熱性、耐候性和遮蓋力方面不如無機顏料。
白色顏料主要有鈦白粉、氧化鋅、鋅鋇白三種。鈦白粉分金紅石型和銳鈦型兩種結構,金紅石型鈦白粉折射率高、遮蓋力高、穩定、耐候性好。炭黑是常用黑色顏料,價格便宜,另外還具有對塑料的紫外線保護(抗老化)作用和導電作用,不同生產工藝可以得到粒徑範圍極廣的各種不同炭黑,性質差別也很大。炭黑按用途分有色素炭黑和橡膠補強用炭黑,色素炭黑按其著色能力又分為高色素炭黑、中色素炭黑和低色素炭黑。炭黑粒子易發生聚集,要提高炭黑的著色力,要解決炭黑的分散性。
珠光顏料又叫雲母鈦珠光顏料,是一種二氧化鈦塗覆的雲母晶片。根據色相不同,可分為銀白類珠光顏料、彩虹類珠光顏料、彩色類珠光顏料三類。能自由著色是多數塑料的一大優點。如何利用價格低廉的著色劑生產色彩豐富、色澤持久的塑料製品也是塑料加工者所關注的問題。著色劑可分染料和顏料兩大類。染料是有強烈著色能力的有機化合物,它雖有色彩鮮艷、色譜齊全、著色力大等優點,但它們的耐熱、耐光、耐溶劑性一般不佳,易從塑料中滲出或遷移,因此印染工業中大量使用的水溶性染料一般都不適用於塑料,只有某些油溶性和醇溶性染料如偶氮類、蒽醌類染料在耐熱性要求不高時方可使用,所以塑料工業中所用的著色劑主要是顏料。顏料可分無機和有機的兩種。無機顏料有熱穩定性好、價格便宜的優點,但它的色澤缺乏光亮和透明性,而有機顏料的著色強度高,色彩鮮艷,但價格較昂。無機顏料主要有二氧化鈦、氧化鐵、氧化鋅、鉻酸鹽、錫化物和汞鎘等。其中二氧化鈦是最廣泛應用的白顏料,常與其它顏料相溶配得一系列色彩。它有化學惰性、熱穩定性好、價格不貴、著色強度高等優點。有機顏料主要有炭黑、偶氮顏料、酞花菁、喹哪酮、異吲哚酮、蒽醌、硫靛及各種酸鹼顏料,其中炭黑是最普通使用的黑顏料,它有價廉色牢、分散性好、流動性佳之優點同時它還是賦於塑料導電性和防紫外線降解的良好填充候性等。對理想的著色劑可以提出許多要求,例如希望它色彩鮮艷、著色力大、容易在塑料中分散均勻不凝集、耐熱性高而對塑料的流動性無影響、不影響樹脂的耐老化性及其別的使用性能、耐候耐曬又價廉無毒等等。但實際上找不到全優的著色劑,只能針對不同的用途來考慮不同的側面。例如,對塑料部件一類裝飾品以滿足色彩方面要求為主;對工業用塑料部件著重考慮著色劑對製品物理機械性能的影響;對中空容器著眼於著色劑的化學穩定性、不與所盛物品作用;對食品包裝材料重點在無毒無味之類的衛生要求。
其優點是分散性好、成本低,可小批量操作。由於它省卻了其它著色劑,如色母、色漿等加工過程中人力物力的消耗,因而成本低,買賣雙方不受量的限制。製造色母不可能做1~2kg,但色粉可以根據需要任意指定質量,配製十分方便。使用色粉著色,與其它造粒著色相比,加工的樹脂少經歷一次降解過程,有利於減少塑料製品的老化,增加其使用壽命。
為了使飼料產品更迎合用戶的傳統習慣,一般把飼料染色加工成淡黃色或黃色產品。在生產飼料過程中,只需把檸檬黃等常用著色劑按一定比例加入,即可達到該目的。
動物本身並不能合成色素。研究也發現,只有含氧功能基(如羥基、醯基、酮基等)的類胡蘿蔔素(carotenoids)類在畜、禽、水產品內才有著色效果。這類類胡蘿蔔素包括:
葉黃素、番茄紅素和玉米黃素等幾大類。飼料中的類胡蘿蔔素都是以棕油酸二酯的形式存 在。這些存在於飼料中的類胡蘿蔔素經動物的消化,以自由態的形式吸收,主要是與低密度 脂蛋白(LDL)結合而被吸收;吸收后的類胡蘿蔔素以遊離狀態進入血液,並隨著血液循環進入皮膚和蛋黃等組織。在此,類胡蘿蔔素重新轉化為棕油酸二酯沉積下來,使皮膚和蛋黃等呈現出人們喜歡的顏色(如黃色)。不同的類胡蘿蔔素以不同的效率沉積於不同的組織中,一般酯化的葉黃素和玉米黃素比結晶的葉黃素和玉米黃素在動物機體組織中的沉積效果更 好。飼料中添加脂肪更能促進色素的沉積作用,且發現添加動物脂肪比添加植物油更有效。此外,隨著飼料中色素水平的提高,在動物組織中色素的沉積比例下降。據報道,如果每天每隻雞進食0.3~1.0mg的色素,大約有30%~45%可沉積在蛋黃中,若色素進食量提高到5mg或更高,則只有15%~20%可在蛋黃中沉積。甲殼動物通過食入綠色植物,將植物中 類胡蘿蔔素轉化為蝦育素和雞油菌黃質沉積在體內。魚類通過攝食大量的甲殼類和浮游生物,使其肉質呈鮮色。金魚和對蝦等可改變吸收后色素的組成,如將葉黃素轉變為蝦紅素,然後再在體組織中沉積。
我國允許使用的合成著色劑有10種。天然著色劑多以植物性著色劑為主,不僅安全。而且許多天然著色劑具有一定營養價值和生理活性。如廣泛用於果汁飲料的β-胡蘿蔔素著色劑,不僅是維生素A原,還具有很明顯的抗氧化、抗衰老等保健功能,GB2760-2011將其列入可在各類食品中按生產需要適量使用的食品添加劑。用於各種食品著色的紅曲紅色素還具有明顯的降血壓作用。隨著人們對食品添加劑安全性意識的提高,大力發展天然、營養、多功能的天然著色劑已成為著色劑的發展方向。
塑料著色主要是無機和有機顏料,要求其具有較高的著色強度和艷度;良好的透明性或者遮蓋性、分散性、耐候性、熱穩定性、化學穩定性、電氣功能、環保性能等。著色力大小。著色力大小直接決定著著色劑的用量,一般來說隨著著色劑粒徑減少而增加,有機顏料比無機顏料著色力高出許多,當彩色顏料與白色顏料並用時,著色力可以得到顯著提高,如今有機顏料和超細粒子得到廣泛應用和發展。分散性。著色劑在聚合物中只有比較容易以微小的粒子狀態均勻分散,才能獲得良好的著色效果。由於顏料含有很多聚集粒子,因此必須經高剪切力的分散以打碎大聚集體,形成小聚體而達到要求的粒子細度,才能獲得理想的光學效果。採用對顏料表面處理等方法可以將顏料加工成一定實用形態,如色母粒,可以有效地改善顏料的分散性。另外添加一些助劑也可以改善著色劑的分散性。耐光和耐候性。一般來說無機顏料光穩定性比較好,在有機著色劑中,酞青系、喹吖啶酮系、二惡嗪、異吲哚啉酮等有機顏料的耐光性十分優異,可以與無機顏料相比擬;蒽醌和茈酮等染料也具有良好的耐光性。耐遷移性。著色劑的遷移主要有三種類型,1)溶劑抽出,即在水和有機溶劑中滲色;2)接觸遷移,造成相鄰的物體的污染;3)表面噴霜,主要由於著色劑在熱加工時在聚合物中的溶解度較大,而常溫下溶解度較小,因而逐漸結晶析出造成的。無機顏料在聚合物中分散一般是非均相的,不會產生噴霜現象,而有機顏料在聚合物中和其他有機物都有程度不同的溶解性,比較容易發生遷移。有機顏料遷移的難易與聚合物和其他添加劑(尤其是增塑劑和軟化劑)的種類有很大關係。通過實驗表明,一般來說,有機酸的無機鹽遷移性比較小;分子量較高的比低的遷移性小。耐熱性。優良的耐熱穩定性能是作為塑料著色劑的重要指標,大多數無機顏料的耐熱性都比較好,基本能夠滿足塑料加工要求,而有機著色劑耐熱性能較差。由於各種樹脂、塑料化學結構的不同,在進行加工成型過程中要求不同的加熱溫度(軟化點以上),溫度的高低將直接影響到著色劑的選擇,以使其著色在規定溫度下不發生明顯的顏色變化,樹脂結構的特性不同,對著色劑要求也不一樣,表1為樹脂塑料加工成型溫度及對著色劑的要求。另外其他一些樹脂的加工溫度分別為,氟樹脂,350℃;丙烯酸酯類樹脂,180—200℃;有機硅樹脂,180℃;酚醛樹脂,150—160℃;環氧樹脂,150℃;纖維素塑料180℃等。可以根據不同的溫度選用適合的著色劑。化學穩定性。由於塑料的使用環境不同,因此要充分考慮著色劑的耐化學藥品性能,如PVC及其他含氯聚合容易分解產生氯化氫,對著色劑的著色效果和耐色牢度可能產生較大的影響,因此PVC及其他含氯聚合物製品必須使用耐酸性著色劑;如某些塑料製品中其他添加劑組份如抗氧劑、受阻胺光穩定劑、分散劑對顏料的影響也不容忽視。電氣性能。聚氯乙烯、聚乙烯等塑料大量用作電線電纜的絕緣層或護套,這些應用領域要求著色劑具有良好的電絕緣性能,有些著色劑添加後會導致電絕緣性能的下降,一般來說導致電絕緣性能降低的原因主要是由於顏料表面殘餘的電解質,而並非顏料的本身,因此某些含有可溶性鹽的顏料不適用於電線電纜等塑料製品的著色,通常炭黑、鈦白粉、鉻黃、酞青藍等顏料的電氣性能較好。環保性能。隨著國內外環保法規日趨嚴格,許多製品對塑料著色劑的毒性提出嚴格要求,著色劑的毒性問題愈來愈引起人們關注。如今美國、歐盟等國家已明確限制使用重金屬,主要包括鎘、鉛、硒等著色劑;德國等國家也相繼出台法規限制使用一些芳香胺類染料和有機顏料。目前我國尚有大量的有毒著色劑在生產與使用,要完全替代仍面臨技術和成本方面的挑戰。
1 色彩性能(著色力)
1.1 色彩性能在塑料著色上的重要性
色彩性能是塑料著色劑最基本的性能,色彩性能是指著色力、色調、和遮蓋力,它們是評價著色性能的第一特徵。著色力是指著色劑賦予塑料著色深度的一種度量,著色力可以定量為絕對值,也可與其它著色劑相比的相對值。色調是指顏料的基本色澤。在色度學上可以用色調,明度和飽和度來表示。色彩性能是著色劑在塑料著色的重要性能指標,它決定了塑料製品色彩質量,著色成本及著色過程的穩定性。
1.2 顏料在塑料中著色力測定方法
(1)測試設備 二輥煉塑機輥轉:25轉/分,轉速比1:1.2輥表面鍍鉻。平板壓機 可加熱和冷卻。不鏽鋼鏡面板二塊,內框:正方型框,片厚0.5mm。(2)測試原料 由聚氯乙烯樹脂,增塑劑,穩定劑,鈦白粉,顏料組成。(3)測試方法 將輥筒表面溫度控制在160℃,PVC薄片厚度0.4mm;煉塑時間:7~8分鐘出片;壓片:在溫度165℃~170℃壓片時間1分鐘后保壓速冷。(4)測色 測標準色值、計算K/S值,顏料著色力測試可以與它的標準樣品比較二者著色力的差別,當調整到二者具有相同著色力。測試也可用高密度聚乙烯,低密度聚乙烯,聚丙烯等。
1.3 塑料著色如何正確應用著色力指標
(1)同一種顏料應用在不同塑料著色時,其色彩性能,著色力等指標不盡相同,嚴格地講提及顏料在塑料著色色彩性能必須提及它的應用解質。
(2)標準深度 在色度學中,可通過在標準條件下製備的樣品色深度來判斷顏料的絕對深度,以達到一定顏色深度所必需的量來表示。其表示方法為標準深度,1/3標準深度,1/25標準深度。這種表示方法可通過Schmelzer所設計的色光連續深度圖直觀地表示出來。
(3)著色劑最大吸收波長決定它的顏色,而在最大吸收波長處的吸收能力決定了它的著色力。但著色力不僅與其化學結構有關,而且還與顏料易分散性有關。顏料易分散性越好,其著色力越高。(4)顏料著色力與配色有著及其重要的意義。例如需要配成深色調應選擇著色力高品種(有機顏料),當需要配成淺色調時應選擇著色力低品種(無機顏料)。在配色時弄一顏料缺少時,或價格較貴,可選用同色其它顏色代替,但兩種顏料著色力不同在代替時配成同樣色調所需要量也不同。
2 耐熱穩定性
2.1 耐熱穩定性對塑料著色的重要性
對於各種不同類型塑料樹脂,根據其設備,工藝條件,產品要求,其加工溫度在120℃至350℃/5分鐘不等,如軟硬質聚氯乙烯一般在170℃~200℃,低密度和高密度聚乙烯,聚苯乙烯在200℃~280℃,而聚丙烯,聚烯胺,ABS,聚碳酸酯則在250℃~330℃。
顏料的耐熱穩定性是指在一定溫度下和一定時間內,顏料不發生明顯的色光,著色力和性能的變化。顏料在塑料中受熱變化是由下列因素構成:(1)顏料因受熱化學結構分解,例如偶氮顏料因受熱偶氮基斷裂而變色;(2)顏料和塑料樹脂中添加劑間互相化學作用;(3)顏料受熱溶解在樹脂中;(4)顏料受熱后其粒徑大小發生變化而變化。
顏料耐熱穩定性優良品種,可防止顏料在受熱下因分解或晶形變化而導至變色,耐熱穩定性是顏料用於塑料著色一個重要應用性能指標。
2.2 塑料用顏料耐熱穩定性測試方法
2.2.1 測試設備 單螺桿擠出機:L/D=24;注塑機。
2.2.2 測試原料 顏料 塑料解質(HDPE,PP,PS,等)。測試濃度:顏料濃度分別為0.1%,0.05%,0.025%,0.005%;對應鈦白粉均為1%。
2.2.3 測試方法可將定量顏料混合物按(2)濃度在單螺桿擠出機多次擠出成均勻粒子。在注塑機中按一定恆定時間,以200℃,220℃,240℃,260℃,280℃,300℃間隔溫度,逐步製造樣板並進行測試,評定:按待色板冷卻16小時后,對色板進行測試,色差E=3為該濃度耐熱穩定性。
2.3 塑料著色如何正確應用顏料耐熱穩定性指標
(1)顏料在塑料加工中耐熱穩定性指標與使用濃度有關
有些顏料在不同濃度下,其耐熱穩定性能相差很大,如C.I.顏料紫23用於HDPE著色,濃度低於0.025%耐熱性只有200℃,大於0.1%,才有260℃。(2)顏料在塑料加工中耐熱穩定性指標與應用需料解質有關顏料在某一應用解質和某一濃度下耐熱穩定性指標,並不等於其在其它解質下的指標相提並論,例如C.I.顏料紫23在滌綸原液著色時能耐260℃/4小時。因此,顏料在這些使用情況下需慎重試驗后才能選用。(4)顏料在塑料加工中耐熱性指標與鈦白粉的加入濃度有關一般,加入鈦白粉后耐熱性指標將會有所下降。(5)著色樹脂本身的耐熱性指標與鈦白粉的加入濃度有關(5)著色樹脂本身的熱穩定性的影響樹脂受熱時由於熱降解作用而發生變色如泛黃等,這也會影響顏料在塑料中應用耐熱指標。
3 易分散性
3.1 易分散性對塑料著色的重要性
顏料的易分散性是指顏料著色過程中分散能力,因為大部分塑料家工工藝均為熔融擠出工藝,顏料在熔融出工藝中所受到剪切力相對與顏料在油墨加工工藝中在錕研磨和顏料在塗料加工工藝中砂磨要小的多,因此,顏料在塑料中易分散性是顏料在塑料中應該的又一個重要指標。
易分散性好壞不僅影響著色力和色光,而且會因分散不好著色不均,生產條痕或色點影響著色外觀,更嚴重影響著色成品的機械性能。具有良好分散性的顏料可以得到一個理想艷度,光亮度,透明性塑料製品,因此,顏料易分散性對塑料著色有重要意義。
顏料用於化纖紡絲,其易分散性好壞更具有重要意義。在紡絲過程中因熔體壓力多大,不得不頻繁更換濾網,浪費大量材料和人工,使設備停車時間過長。更嚴重導致生產無法正常進行。
3.2 顏色易分散性測定方法
3.2.1 測試方法
(1) 顏料易分散性測定方法
測試方法:按顏料在塑料中著色力測定法取沖淡PVC片材一半,將輥筒表面溫度控制為130℃,PVC薄片厚度0.3mm,煉塑時間7~8分鐘出片。壓片溫度165~170℃;壓片時間上1分鐘后保壓速冷。評定:以在二種不同剪切力條件混煉后著色力提高來計算分散性。其中5級最好,1級最差。
(2)顏料過濾性能測試
顏料過濾性能(壓力指數)是對顏料凝聚的數量和顏料分散體中尺寸過大顆粒的測量。由於顏料堵塞擠出機濾網引起的擠出機內部熔體壓力的升高,由kg/cm2/min數表示。
3.2.2 測試設備
單螺桿擠出機L/D=25,壓縮比為:1:3
濾網組合按下列指定順序:60,100,325,60,20目,熔融壓力感測器,放置在螺桿末端和濾網之間(範圍0kg/cm2~25kg/cm2)
3.2.3 測試濃度:顏料含量3%的聚丙烯混合物。
3.2.4 測試方法:
設定擠出溫度:輸送段200℃,其餘段240℃,擠出量:53g/min。把樣品混合物加入擠出機,當樣品混合物進出時,記錄壓力P0,連續操作60分鐘內記錄壓力P60,顏料過濾壓力指數DF值可用下列公式計算:DF=(P60-P0)/60 DF值小於0.15,表明顏料分散性良好。
3.3 塑料著色如何正確應用顏料易分散性指標
3.3.1 顏料易分散性對塑料製品的影響
顏料易分散性對塑料製品的光學性能有直接影響,塑料製品著色深度與易分散性好壞有關,透明性隨顏料分散粒徑減小而增大,色調也與分散性有關。
3.3.2 顏料在塑料中分散及其他影響
顏料在塑料中的分散性除了顏料本身分散性外,還與其它重要因素有關。
當今世界塑料材料及其製品的應用已涉及到各行各業、方方面面、以至每一個家庭,越來越多的企業人士參與到塑料製品的生產與銷售中來。對於塑料製品該選用何種著色劑也成為塑膠行業人士的討論話題。
1 塑料著色劑的種類
塑料著色劑的種類,以其物理形態共分為四種:粉狀著色劑-色粉;糊狀著色劑-色漿;液狀著色劑;固狀著色劑-色母。其中,廣泛應用的是粉狀著色劑和固狀著色劑。因此,對於其它二種著色劑本文不作討論。
2 各種著色劑的特點
2.1 色粉著色的特點
直接用色粉(顏料或染料)添加適量粉狀助劑對塑料粒子進行著色的方法,又稱干法著色。
但最大缺點是顏料在運輸、倉儲、稱量、混和過程中會飛揚,產生污染,嚴重影響工作環境。隨著環保、企業ISO9000指標等要求,色粉著色越來越受到局限,但對於特殊效果的著色,採用色粉直接混合著色具有一些色母著色達不到的效果。舉例來說:一些耐熱性差、怕剪切的顏料粉製成色母,由於其承受高溫的時間長,而在色母加工設備中受剪切作用的時間長,著色效果會明顯減弱,如珠光色粉、熒光粉、夜光粉。用珠光色粉製成色母再著色塑料,比直接用珠光粉混入塑料著色,其珠光效果要減弱10%左右,且注塑產品還容易產生流線狀疤痕和接縫。在製造這類色母時,均採取相應措施,儘可能地減少色母在加工過程中受熱的溫度、時間及受剪切的程度(不用雙螺桿造粒機,而用單螺桿造粒機等)。
干法著色另一個令用戶頭疼的問題是擠出機的料斗不易清洗。用以著色的色粉在白油等濕潤劑的作用下,沾附上料筒內壁(乃至螺桿上)。當需要換料時,清洗料筒便成了現場操作工的難題,費時費料,事倍功半,而使用色母著色就沒有這個問題。
另外,使用色粉著色,由於顏料粉均勻分佈在需著色的樹脂中,所以其分散性較好,這個結論只能針對注塑產品,特別是厚壁產品而言,對於吹膜、紡絲類產品則另當別論。因為色粉一般都沒進行過預處理,當其混於樹脂后,僅靠從擠出機進料口、螺桿、至出料口這麼一段距離以及這麼短的塑化混合時間,要使顏料粉的分子與被著色的顏料分子很好地攜起手來--充分結合,是完全不能保證的,會有“夾生”現象產生。但這種“夾生”現象在厚壁產品中會被掩蓋掉,在吹膜、紡絲產品中就顯而易見。所以後者的著色方法仍以色母為主。
除此以外,色粉因生產廠商的生產日期、批號的不同,同一牌號的色粉也存在著一定的色差,即使用戶堅持用同一配方,但在加工過程中很難做到批與批之間的注塑產品的顏色一致性,而色母在生產過程中可以通過中途取樣、檢驗、調節來彌補每批色粉的色差,相對來說,色母對顏色的重複性明顯優於色粉。
正因為色粉用於塑料製品的著色有種種局限,受到了其它著色劑的挑戰,但由於生產成本相對較低,定色、配色不受量的限制,對於發展中國家的中小企業、私人企業來說,要想參與激烈的市場競爭,使用色粉有其一定的經濟性,特別是一些色樣單一、產量大、對著色要求不高的產品,如PVC門窗、EVA鞋底等,還是青睞於它,因而色粉著色劑無法完全退出舞台。
2.2 色母著色特點
為了克服色粉著色的種種弊端,提高塑料製品的質量,隨著塑料工業的不斷發展,塑料樹脂種類、助劑種類、塑料製品加工設備及工藝的不斷創新、突破,塑料著色的另一途徑--色母粒著色已被廣泛採用,色母粒著色技術也在應用與實踐中不斷得到提高。
所謂色母粒,即採用某種工藝與相應設備,在助劑的作用下,將顏料(或染料)混入載體,通過加熱、塑化、攪拌、剪切作用,最終使顏料粉的分子與載體樹脂的分子充分地結合起來,再製成與樹脂顆粒相似大小的顆粒。將這種高濃度著色劑稱為色母粒,其作用與“糖精”相似,使用時,只需在要著色的樹脂中添加較小的比例(1%~4%),就能達到著色樹脂的目的。
與色粉著色相比,色母粒著色有以下明顯的優點:
(1)改善了由於色粉飛揚帶來的環境污染問題,使用過程中換色容易,不必對擠出機料斗進行特別的清洗,倍感方便。
(2)針對性強,配色正確。由於色母製造工廠在製造過程中已針對適用樹脂的性能,合理地選擇了顏料(染料)、助劑、加工設備、加工工藝,對生產過程中不同批號的色粉可能帶來的色差,及時進行修正、補色,出廠時再進行檢驗,因此,可以保證相同牌號的色母,前後兩批顏色保持相對的穩定。
(3)與成批樹脂干法染色造粒后再去制塑件相比,使用色母可以減少塑料製品經二次加工后所造成的樹脂性能老化,有利於塑料製品使用壽命的提高。
使用色母最大的優點是:在加工過程中,顏料在助劑的作用下,色母粒經過充分混煉與載體樹脂完全結合。在使用時,按一定的比例置於待加工的樹脂中,色母很快地進入角色,與該樹脂認“親家”。親和力--相容性明顯優於色粉著色,因此,對於生產薄膜與紡絲製品的廠家來說,更能體會到。
當然,色母粒著色也有其局限性,由於添加量少,塑料製品的加工時間短,受擠出機螺桿長徑比的限制,色母分散性往往不如色粉。多了一次製造過程,染色成本也必定高於色粉著色。色母中的載體與需著色樹脂的性能有差異時,塑料製品表面常常會出現未分散點、色斑、花紋,所以,色母的使用因其相容性及分散性而受到限制。
3 通用色母和專用色母的選擇
正因為色母粒著色比色粉著色有著許多的優越性,隨著塑料製品加工工業的發展,特別是眾多合資企業的建立及出口產品對著色要求的提高,色母粒著色逐漸佔主導地位,就色母粒的適用性分類,它可分為通用色母與專用色母。
3.1 專用色母
在生產製造色母粒時,選用與欲著色樹脂相同的樹脂作為載體,加入高濃度的顏料(染料),在助劑的作用下,經加溫、塑化、混煉、擠出造粒,製成專門適合於該種樹脂的染色劑,稱為專用色母。專用色母的濃度可高可低,一般添加量在1%~4%之間。
3.2 通用色母
通用色母(也有人稱之為“萬能色母”)與專用色母主要區別在於:通用色母雖然也用某種樹脂作載體,但它可以適用於除其載體樹脂之外的其它樹脂的著色,因此稱之為通用色母。
所謂通用色母,一般採取以下幾個措施(有的製造工廠乾脆不用樹脂作載體,而全部用高熔點的丙烯蠟作載體):首先選用低熔點、高融體指數的樹脂作為通用色母的載體,如PE或EVA;其次,色母粒中顏料粉比率儘可能的高,因此通用色母必定是高濃度色母,在注塑製品中使用量一般是1%。由於色母中不同介質載體十分少(扣除助劑因素,一般在20%左右),當它再以1%的比例稀釋於欲著色的樹脂中時,該塑料製品內所含的不同樹脂的含量:0.2kg/100=2g/kg。為了使通用色母能與被著色的其它種類的樹脂結合好(親和性好),在通用色母中還採用了其它措施,如多加入特殊作用的偶聯劑、延長密煉時間等,這些都有利於提高通用色母的廣泛適用性。
3.3 選擇原則
究竟選用何種色母為宜?是否通用色母最妥?讓從製造工廠、經銷商、用戶以及經濟效益、方便與否、製品效果等幾方面來進行分析。
從製造工廠來講:為了生產通用色母必須選用耐熱等級較高的、適用面廣的顏料,而顏料粉耐溫等級到了某個程度后,每提高10℃~20℃,顏料的成本卻要上升50%~100%。當用某種耐高溫的顏料製成的通用色母,用於高熔點樹脂著色時,是物當其用,而用於LDPE這樣低熔點的樹指,提高的卻是剩餘價值。
除上面所述的著色偏色外,由於添加比率小,分散性相對差些,塑料製品表面易出現花紋、色斑、色點,仍至因料種不和而引起脆皮等現象,特別是對大面積、薄壁形狀又複雜的塑件更要引起注意,這時儘可能採用專用色母,且選擇濃度低的色母,以增加添加量來提高其分散性(可選擇1∶20、1∶10的專用色母)。
通過上面的分析比較可以看到,通用色母及專用色母各有千秋,但從著色效果及製品性能來說專用色母仍優於通用色母。建議當用戶確定了自己欲著色的樹脂的種類后,首選專用色母。