丁基橡膠
合成橡膠的一種
丁基橡膠是合成橡膠的一種,由異丁烯和少量異戊二烯合成。製成品不易漏氣,一般用來製造汽車、飛機輪子的內胎。丁基橡膠是異丁烯和異戊二烯的共聚物,它在1943年投入工業生產。
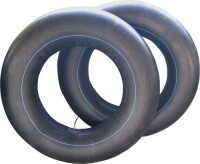
丁基橡膠
1943年,美國埃索化學公司首先實現了工業化生產。此後,加拿大、法國、蘇聯等也相繼實現了丁基橡膠的工業化生產。80年代初,世界丁基橡膠生產能力約為650kt,占合成橡膠總產量約5%。
丁基橡膠自實現工業化生產以來,原料路線、生產工藝以及聚合釜的結構形式一直變化不大,一般採用氯甲烷作稀釋劑,三氯化鋁作催化劑,控制這兩者的用量可以調節單體的轉化率。根據產品不飽和度的等級要求,異戊二烯的用量一般為異丁烯用量的1.5%~4.5%,轉化率為60%~90%。聚合溫度維持在-100℃(採用乙烯及丙烯作冷卻劑)。丁基橡膠的聚合是以正離子反應進行的,反應溫度低,速度快,放熱集中,且聚合物的分子量隨溫度的升高而急劇下降。因此,迅速排出聚合熱以控制反應在恆定的低溫下進行,是生產上的主要問題。聚合釜(見圖)採用具有較大傳熱面積並裝有中心導管的列管式反應器。操作時借下部攪拌器高速旋轉,增大內循環量,從而保證釜內各點溫度均勻。
為改善丁基橡膠共混性差的缺點,1960年以來出現了鹵化丁基橡膠。這種橡膠是將丁基橡膠溶於烷烴或環烷烴中,在攪拌下進行鹵化反應製得。它含溴約2%或含氯1.1%~1.3%,分別稱溴化丁基橡膠和氯化丁基橡膠。丁基橡膠鹵化后,硫化速度大大提高,與其他橡膠的共混性和硫化性能均有所改善,粘結性也有明顯提高。鹵化丁基橡膠除有一般丁基橡膠的用途外,特別適用於製作無內胎輪胎的內密封層、子午線輪胎的胎側和膠粘劑等。
淤漿法:淤漿法是以氯甲烷為稀釋劑,以H2O-AlCl3為引發體系,在低溫(-100℃左右)下將異丁烯與少量異戊二烯通過陽離子聚合製得的。
溶液法:傳統的淤漿法合成丁基橡膠生產工藝技術成熟,但由於聚合反應溫度低,製冷設備龐大,聚合釜連續運轉周期短,能耗高(1kg膠能量消耗約35~55MJ)。為了能提高反應溫度,對用溶液法合成丁基橡膠進行了大量的研究。
丁基橡膠因其聚合物所具有的獨特性能,所以被廣泛用於製造內胎、防振橡膠、工業膠板、醫用橡膠等許多方面。本文主要就配合劑對丁基橡膠物性的影響進行敘述。
炭墨對普通丁基橡膠物性的影響與對鹵化丁基橡膠基本相同。各種炭黑對物性的影響如下:
(2)FT(細粒子熱裂炭黑)、MT(中粒子熱裂炭黑)等粒徑較大的炭黑,其硫化膠的伸長率大;
(3)無論是哪一種炭黑,隨著其用量增加,硫化膠的定伸應力和硬度增大,而伸長率減小;
(4)SRF(半補強爐黑)硫化膠的壓縮永久變形比其它炭黑都優異;
(5)爐法炭黑的壓出加工性能優於槽法炭黑和熱裂炭黑等。
丁基橡膠大都用石油類油如石蠟油、石蠟和酯類增塑劑作為軟化劑,其中石油類油和酯類增塑劑對丁基橡膠物性的影響如下:
(1)因油的添加,拉伸強度、定伸應力、硬度降低,伸長率增加;
(2)因油的添加,門尼粘度降低,門尼焦燒時間增長;
(3)因油的添加,壓出性能得到一定的改善;
(4)因油的添加,耐臭氧、耐壓縮永久變形、耐熱性降低;
(5)因酯類增塑劑的添加,低溫性能得到改善,但效果依油的型號而異;
(6)因酯類增塑劑的添加,耐壓縮永久變形、耐熱性降低。
白色填充劑與炭黑一樣,也是粒徑小的補強效果好,拉伸強度、定伸應力、撕裂強度、硬度等較大;粒徑大的有損於抗撕裂、耐屈撓和耐磨耗性等。各種白色填充劑對丁基橡膠的補強效果如下:
(1)白炭黑的補強效果在白色填充劑中最大,適用於要求強度和耐磨耗性高的橡膠製品;
(2)滑石粉的形狀有各種各樣,其中棒狀、粒狀的補強性能差,片狀的可顯著改善拉伸強度和定伸應力;
(3)碳酸鈣高填充時可減少伸長率和彈性的損失,並可用於降低產品成本;
丁基橡膠除一般性硫黃硫化外還有各種硫化體系,可根據不同用途進行選擇,特別對於鹵化丁基橡膠,與二烯類橡膠一樣通過雙鍵用硫黃、醌和樹脂進行硫化,此外通過鹵基還可用金屬氧化物、二硫代氨基甲酸金屬鹽及硫脲等進行硫化,對於溴化丁基橡膠可用過氧化物硫化。
國內有很多從事再生丁基橡膠生產的企業,丁基再生膠指的是利用已經經過硫化使用后的丁基廢舊橡膠通過再生工藝使其重新具有一定的使用價值的橡膠。丁基橡膠與丁基復原橡膠其生產用的原料不同,丁基橡膠是由異丁烯與少量的異戊二烯合成而得,丁基復原橡膠(丁基再生膠)則是廢舊橡膠加工而成。丁基橡膠是純生膠,丁基復原橡膠是含有多種助劑的混合物。所以如果想要降低丁基橡膠生產成本,我們可以選擇使用再生膠的做法,通過混合來降低其成本。
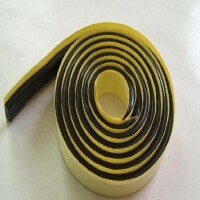
丁基橡膠
丁基橡膠的缺點主要包括:
第一,硫化速度慢,與天然橡膠等高不飽和橡膠相比,其硫化速度慢3倍左右,需要高溫或長時間硫化;
第二,互粘性差,須藉助於增粘劑、增粘層改善與其它橡膠的粘合,且粘合力較低;
第三,與其它橡膠相容性差,一般僅能與乙丙橡膠和聚乙烯等並用;
第四,與補強劑之間作用弱,與不飽和橡膠相比,丁基橡膠與補強劑之間作用較弱,需要進行熱處理或使用添加劑,以增加橡膠的補強作用,提高拉伸強度、定伸應力、彈性、耐磨和電絕緣性能等。
以上缺點限制了丁基橡膠的使用用途,也不建議與石油溶劑,膠煤油和芳氫同時使用。
2005年,中國丁基橡膠消費量近15萬噸,國產丁基橡膠不足3萬噸,80%依靠進口,從1999年至2004年,進口量年均增長率達26.9%。由於,國際石油市場價格不斷上升,丁基橡膠價格也不斷攀升。近幾年來丁基橡膠的價格由15000元/T左右,上升呈現在的32000元/T以上。而丁基橡膠製品的價格雖然有所上升,但整體算價格上升幅度不超過30%,遠遠趕不上丁基橡膠價格成倍的上升。所以很多使用丁基橡膠的企業把目光轉向了丁基橡膠的最佳替代產品――丁基再生橡膠。
丁基橡膠產品均為塊狀膠,膠塊先用高壓聚乙烯薄膜熱合封裝後放入木箱進行貯存和運輸。膠塊凈重量為(25± 0.2)kg;每箱膠凈重量為1050kg。
丁基橡膠應存放在通風、清潔、乾燥的倉庫中,嚴禁露天堆放和陽光直接照射。
1、生產現狀
中國丁基橡膠的研究開發始於20世紀60年代,並建立了中試生產裝置,后因各種原因而停止。1999年,北京燕山石油化工公司合成橡膠廠引進義大利PI公司技術,建成中國惟一的一套30kt/a丁基橡膠生產裝置。該裝置能夠生產ⅡR1751、ⅡR1751F和ⅡR0745三個牌號的普通丁基橡膠產品,其中ⅡR1751屬於內胎級產品,中等不飽和度,高門尼粘度,相當於Exxon公司的268、Bayer公司的301
及俄羅斯的BK1675N產品牌號,主要用於製造輪胎內胎、硫化膠囊和水胎等製品;IR1751F是食品、醫藥級產品,中等不飽和度,高門尼粘度可用於口香糖基礎料以及醫用瓶塞的生產;ⅡR0745是絕緣材料、密封材料和薄膜級產品,極低不飽和度、低門尼粘度,主要用於電絕緣層和電纜頭薄膜的生產。
最初兩年,由於技術、設備等方面的原因,該裝置難以連續穩定運行,開工率較低,產品合格率低,原材料消耗、動力消耗及成本偏高。2000年和2001年產量分別只有4.055kt以及和4.190kt。經過近兩年的技術攻關,生產裝置的運行狀況有了很大程度的改善,產量逐年增加,2002年產量達到21.545kt,其中產品合格率為84.7%,2003年產量進一步增加到27kt,其中產品合格率達到95.4%。
2、進出口情況
由於中國丁基橡膠的生產能力和產量還不能滿足實際生產的需求,因而每年都得進口,且進口量不斷增加。1998年中國丁基橡膠的總進口量只有26.869kt,2003年增加到83.475kt,比2002年增長50.7%,1998-2003年進口量的年均增長率高達25.4%。在2003年的總進口量中,普通丁基橡膠的進口量為42.986kt,同比增長36.5%;鹵化丁基橡膠的進口量為40.489kt,同比增長69.0%。其中初級形態普通丁基橡膠的進口量為35.168kt,同比增長49.8%;初級形態鹵化丁基橡膠的進口量為26.942kt,同比增長72.4%。2004年上半年進口丁基橡膠44.292kt,同比增長8.3%。其中初級形態丁基橡膠的進口量為10.784kt,初級形態鹵化丁基橡膠的進口量為16.490kt,中國丁基橡膠的進出口情況見表5所示。
從進口來源看,中國初級形態普通丁基橡膠進口主要來自俄羅斯、加拿大和日本,2003年中國從這3個國家進口的初級形態普通丁基橡膠總量達到26.876kt,約佔初級形態普通丁基橡膠總進口量的76.4%。鹵化丁基橡膠則主要來自西歐和北美國家,約佔總進口量的84%,來自日本的產品約佔總進口量的3.9%。中國初級形態普通丁基橡膠的進口來源情況見表6所示。
中國初級形態普通丁基橡膠進口量中,進口加工貿易和一般貿易所佔的比例逐漸減少,而邊境小貿易所佔的比例卻逐年增加。普通丁基橡膠的進口主要集中在滿洲里、廈門、青島等海關,從這三個海關進口的丁基橡膠約佔總進口量的79.2%。鹵化丁基橡膠則主要從上海、青島及蕪湖等海關進口,進口量約佔總進口量的63%。年來中國初級形態普通丁基橡膠的貿易方式見表7所示。
3、消費現狀及市場前景
隨著中國汽車輪胎工業等的不斷發展,中國丁基橡膠的消費量不斷增加。中國丁基橡膠的供需平衡情況見表8所示。
2003年,中國丁基橡膠的總消費量為100kt/a(其中鹵化丁基橡膠的消費量約為40kt/a),其中輪胎方面的消費量約佔總消費量的84%,醫藥瓶塞的消費量約佔總消費量的11%,其他方面的消費量約佔總消費量的5%。
⑴輪胎。丁基橡膠被廣泛用於生產汽車輪胎及車力胎(自行車、摩托車等)的內胎內襯、硫化膠囊和水胎,特別是子午線輪胎的快速發展和汽車輪胎品級的不斷提高,促使中國丁基橡膠消費量的不斷增長。但是國內丁基橡膠在輪胎行業的應用與國外相比,差距仍很大。例如發達國家的輪胎內胎已經全部實現了丁基化,與中國相鄰的印度以及馬來西亞和泰國等東南亞國家,輪胎的丁基化率也已經達到70%~90%,因此中國丁基橡膠的使用還有很大的發展潛力。
國內普通丁基橡膠主要用於生產丁基橡膠內胎(含自行車、摩托車)和硫化膠囊,牌號主要有Exxon公司的268,Bayer公司的301和俄羅斯的1675N。主要使用企業有樺林輪胎股份有限公司、山東三角集團有限公司、青島橡膠集團有限責任公司、廈門正新橡膠工業有限公司、上海輪胎橡膠集團股份有限公司、杭州中策橡膠股份有限公司和張家港安固橡膠工業有限公司等。
作為國民經濟的支柱產業,中國汽車工業正在迅速發展,逐步向大型化、高速化、專業化發展,輪胎也隨國際潮流向子午化、扁平化、無內胎化轉化。同時,高速公路的發展速度加快,也促進了輪胎的丁基化速度。中國內胎丁基化(包括農用胎)和汽車輪胎子午化比例還很低,根據國家有關部門發布的工業行業“十五”規劃,中國輪胎工業主要發展子午胎,在輪胎的結構上,轎車子午胎髮展寬斷面系列、高速度級產品;載重車子午胎重點發展無內胎全鋼絲子午胎,以滿足未來汽車和道路升級發展的需要。輪胎行業將推廣高等級轎車子午胎、輕卡車子午線輪胎、低斷面和無內胎全鋼載重子午線輪胎生產技術;並且子午胎髮展已經獲得國家政策性鼓勵。經國務院批准,財政部與國家稅務總局發布[2000]145號文,規定自2001年1月1日起,對“汽車輪胎”稅目中的子午線輪胎免征消費稅,其餘子午化輪胎繼續按10%稅率徵收消費稅。國家政策鼓勵子午胎髮展,將會大大促進國內鹵化丁基橡膠需求的增長。2003年中國輪胎行業(包括汽車輪胎及車力胎)對丁基橡膠的消費量約為84kt/a,預計2005年對丁基橡膠的消費量將達到約115kt/a,其中鹵化丁基橡膠的消費量為56kt/a;2010年消費量將達到約170kt/a,其中鹵化丁基橡膠的消費量約為100kt/a。
⑵醫用瓶塞。醫用瓶塞丁基化是中國鹵化丁基橡膠的第二大需求市場。為了保證用藥安全,國家醫藥主管部門發布國葯管注[2000]462號文,規定2004年底以後國內所有藥用膠塞(包括粉針劑、輸液及口服液等各劑型膠塞)一律停止使用普通天然膠瓶塞。醫用瓶塞生產廠家正在擴大丁基橡膠
膠塞的生產能力,主要使用鹵化丁基橡膠以適應國內需求。中國引進的第一條丁基橡膠瓶塞生產線於1992年在湖北華強藥用包裝製品廠建成投產。中國較大的生產線有10多條,其中產量較大的企業有湖北華強、石家莊一橡、上海新亞、金湖玻璃儀器廠、江陰蘭陵、江陰中馬、江陰有色、湖北白蓮以及株洲華益等,所用的丁基橡膠牌號主要有Exxon1066、2211、2244及Bayer公司的1045、1240等。2003年中國醫藥瓶塞對丁基橡膠的消費量約為11kt/a,預計2005年消費量將達到約14kt/a,2010年消費量將達到約20kt/a。
⑶其他方面。在其他方面,丁基橡膠主要用於生產膠帶、膠管、粘合劑和防水卷材等橡膠製品,2003年消費量約為5kt/a,預計2005年和2010年需求量將分別達到11kt/a和20kt/a。
由此可見,預計到2005年中國丁基橡膠的需求量將達到約140kt/a,其中鹵化丁基橡膠的需求量將達到約70kt/a。2010年丁基橡膠的需求量將達到約210kt/a,其中鹵化丁基橡膠的需求量將達到約120kt/a。中國丁基橡膠的消費現狀及預測情況見表9所示。
4、市場價格
2000年前中國未生產丁基橡膠,國內供給基本上依賴於進口,國內市場價格以進口為主導。北京燕山石化公司的丁基橡膠裝置在2000年和2001年連續兩年運行不太正常,產量較低,因此國內丁基橡膠市場價格仍受進口產品的控制。2002年該裝置的開工率達到70%,國產丁基橡膠已經佔據了國內約31%的市場份額,對國內丁基橡膠的價格起到了一定的牽製作用,但國產丁基橡膠受進口產品的衝擊厲害,其初級形狀的丁基橡膠價格從2000年的1980美元/t下降到2003年的1780美元/t。
自1997年以來,中國初級丁基橡膠的進口價格基本上維持在1500美元/t以上(1998年除外),鹵化丁基橡膠進口價格一直維持在2200美元/t以上。2000年,由於國內市場需求迅速增加以及Bayer公司出口減少,使得國內丁基橡膠貨源緊張,價格大幅度上漲,初級丁基橡膠進口平均價格高達1984美元/t,比1999年上漲了20%以上。近兩年,由於俄羅斯丁基橡膠擴大對中國的出口,使得國內丁基橡膠的平均進口價格有所下降。
2003年普通初級丁基橡膠的進口平均價格為1789美元/t,比2002年下降約2.6%;但從法國、日本、美國和加拿大等國家進口的產品價格仍維持在2000美元/t以上的價位;從俄羅斯進口的產品價格平均為1687美元/t,比2002年增長5.7%。初級鹵化丁基橡膠的平均進口到岸價格為2568美元/t,較2002年增長4.1%;初級鹵化丁基橡膠與普通丁基橡膠的進口價格相比,要高出約43%;從歐美進口的鹵化丁基橡膠價格比普通丁基橡膠的價格要高約21%,從俄羅斯進口的產品則較普通丁基橡膠的價格高約1.6%。中國初級形態丁基橡膠進口數量及平均價格見表10所示。
丁基橡膠由於其良好的物理性能和化學性能,與藥品的良好相容性而普遍使用於抗生素及輸液產品上。但由於丁基膠塞在加工合成中,為進一步提高其性能,往往會加入補強劑,填充劑如高嶺土等。但高嶺土的過多加入導致了膠塞物理性能的下降,特別是在穿刺落屑方面,增加了用藥的不安全性,故國家食品藥品監督管理局於2002年頒布了氯化丁基膠塞(YBB00042002)和溴化丁基膠塞(YBB00052002)二個產品標準,對膠塞熾灼殘渣進行了嚴格控制,以確保產品的安全、使用性能。但由於膠塞
配方的複雜性,標準執行中也存在著方法學上的問題。
為配合國家食品藥品監督管理局丁基膠塞標準的修訂工作,本文結合標準要求,兼顧膠塞配方的特點,比較了膠塞灰份測定(ISO247-1990)及YBB00042002、YBB00052002方法的實驗結果,探討了溫度及加入硫酸對測定結果的影響以選擇最佳的實驗條件。
實驗部分
1.試樣:
選擇了國內有代表性的十三家膠塞生產企業生產的140個批號的鹵代丁基膠塞產品,規格有20A,20B的抗生素膠塞及28B的輸液膠塞。
1.實驗條件選擇
●溫度選擇:
由於溫度高低對膠塞殘渣結果影響較大,故實驗選擇二種條件進行。
實驗條件一:溫度為800℃,參照中華人民共和國藥典2000年版熾灼殘渣檢查法進行,實驗中,不加硫酸。
實驗條件二:溫度為950℃,參照ISO247-1990膠塞灰份測定法進行,實驗中,加硫酸。
●測定方法:
方法一:參照ISO247-1990膠塞灰份測定法進行
精密稱定膠塞產品1~5克,置已恆重坩堝中,加3.5ml硫酸,使其全部浸潤,加熱。如果反應中,混合物過度膨脹,調低溫度以避免樣品損失。當反應溫和后,升溫至過量的硫酸全部揮發,將坩堝轉移到馬弗爐中,在950℃±25℃條件下,持續加熱1小時至灰化完全,取出坩堝轉移至乾燥器內,放冷至室溫,精密稱定后,再將其放回馬弗爐中,在950℃±25℃條件下,加熱30分鐘,然後置乾燥器中,放冷至室溫,精密稱定,二次質量之差不大於總質量的1%。
方法二:參照YBB00042002或YBB00052002改進方法進行
取該品1.0克,置已恆重坩堝中,精密稱定,緩緩熾灼至完全炭化,再於800℃熾灼使其完全炭化,移至乾燥器內,放冷至室溫,精密稱定后,在800℃熾灼至恆重。
2.實驗結果
膠塞產品經上述二個實驗方法后的熾灼殘渣結果,見表1。
表1丁基橡膠塞熾灼殘渣測定結果
樣品序號結果
800℃,不加硫酸結果
950℃,加硫酸 備註
溴化抗生素30.7 31含鋅、鎂,已硅化
溴化抗生素 30.8 30.9含鋅、鎂,已硅化
溴化抗生素48.3 52.6--
溴化抗生素20-A51.6 51.7含鎂,硅化
氯化抗生素20-B2 47.4 48含鋅,硅化
溴化輸液28-B 43.9 43.7 配方LL-04,含鎂,硅化A級
溴化輸液28-B 44.6 44.8 含鎂,1/2A硅化
氯化輸液 49.1 49.7 --
氯化抗生素 32.2 32.1 --
氯化輸液28-B 46.7 47.4 含鋅,硅化
氯化輸液28-B 42.5 43 含鋅,1/2A硅化
溴化輸液 45.3 46.2 含鋅,未硅化
3.討論
⑴YBB00042002(或YBB00052002)方法與ISO247方法的主要差異在於:
a.溫度:YBB00042002(或YBB00052002)採用的實驗溫度為700~800℃,而ISO247-1990採用的實驗溫度為950℃,溫度高低對殘渣結果的影響隨膠塞配方而異。
b.硫酸的加入與否及加入先後順序:對一般產品來說,熾灼過程,加入硫酸有助於熾灼或炭化完全,但由於膠塞產品組成的複雜性,如膠塞配方中含活性劑氧化鎂等時,熾灼過程中,加入硫酸會幹擾實驗結果。因此,消除干擾是實驗方法應該值得注意的一個環節。
⑵參照ISO-1990方法採用加硫酸,溫度為950℃條件時,140批樣品實驗結果在30.9~52.6%,其中有42批結果大於YBB00042002(或YBB00052002)標準指標45.0%的要求;參照中華人民共和國藥典2000年版,不加硫酸,溫度為800℃條件時,140批樣品實驗結果在30.7~51.6%,其中有35批結果大於YBB00042002(或YBB00052002)標準指標45.0%的要求。
⑶實驗結果顯示:加硫酸、溫度為950℃的實驗結果較之不加硫酸、溫度為800℃的實驗結果高0.2~1.0%。此外,由於加硫酸的實驗條件,得到的實驗結果偏差較大,且污染實驗環境,故不宜選用。
⑷建議採用:不加硫酸、溫度為800℃作為膠塞熾灼殘渣的實驗條件。
丁基橡膠(簡稱ⅡR)是世界上第四大合成橡膠(SR)膠種,是異丁烯和異戊二烯在Friedel-Craft催化劑作用下進行陽離子聚合反應的產物,外觀為白色或淡黃色晶體,無臭無味,玻璃化溫度很低,不溶於乙醇和丙酮。由於丁基橡膠具有優良的氣密性和良好的耐熱、耐老化、耐酸鹼、耐臭氧、耐溶劑、電絕緣、減震及低吸水等性能,使得其廣泛應用於內胎、水胎、硫化膠囊、氣密層、胎側、電線電纜、防水建材、減震材料、藥用瓶塞、食品(口香糖基料)、橡膠水壩、防毒用具、粘合劑、內胎氣門芯、防腐蝕製品、碼頭船護旋、橋樑支承墊以及耐熱運輸帶等方面。
丁基橡膠的生產始於20世紀40年代,1943年Exxon公司在美國BatonRouge工廠實現了丁基橡膠的工業化生產。1944年,加拿大Polysar公司採用美國技術在Sarnia建成丁基橡膠生產裝置。1959年後,法國、英國、日本也開始生產丁基橡膠。1991年,Bayer公司購買Polysar全部合成橡膠業務,Exxon公司也收購了在法國的丁基橡膠生產裝置,從此世界丁基橡膠的生產基本上被Exxon和Bayer兩大公司所壟斷。1982年,前蘇聯在陶里亞蒂建成世界唯一的溶液聚合法丁基橡膠生產裝置,所用聚合反應器由蘇聯合成橡膠研究院和義大利PI公司合作開發。
鹵化丁基橡膠(HⅡR)可分為氯化丁基橡膠(CⅡR)和溴化丁基橡膠(BⅡR)兩大類,是丁基橡膠在脂肪烴溶劑中與氯或溴進行反應的產物,其工業化生產始於20世紀50年代末,1960年Exxon公司在BatonRouge工廠開始生產氯化丁基橡膠,Polysar公司於1971開始生產溴化丁基橡膠。
世界上只有美國、德國、俄羅斯和義大利4個國家擁有丁基橡膠生產技術,在國際市場上,Exxon公司和Bayer公司的丁基橡膠產品處於壟斷地位,生產能力約佔世界總生產能力的80%,此外,這兩大公司在新產品和新技術的開發方面也處於世界領先地位。中國只有中國石化燕山石油化工公司合成橡膠廠1家生產企業,產量不能滿足國內實際生產的需求,每年都要大量進口,開發利用前景廣闊。
美國Exxon公司和德國Bayer公司的丁基橡膠生產技術和新產品開發能力在世界上處於絕對領先地位,對外不轉讓技術,鹵化丁基橡膠生產技術和生產裝置也只有這兩家公司所有。2004年,全世界共有9個國家的12套裝置生產丁基橡膠,總生產能力為892kt/a,其中北美地區的生產能力為393kt/a,佔世界丁基橡膠總生產能力的44.1%;歐洲的生產能力為264kt/a,佔世界總生產能力的29.6%;亞太地區的生產能力為145kt/a,佔世界總生產能力的16.3%;中歐和獨聯體的生產能力為90kt/a,佔世界總生產能力的10.1%。其中Exxon公司的丁基橡膠總生產能力為459kt/a,佔世界丁基橡膠總生產能力的51.5%;Bayer公司的總生產能力為255kt/a,佔世界總生產能力的28.6%。全球現有的丁基橡膠生產裝置中,採用Exxon公司專利技術的有6套,其中3套可兼產鹵化丁基橡膠;採用Bayer公司生產技術的裝置有2套,均可生產丁基橡膠和鹵化丁基橡膠;俄羅斯的2套丁基橡膠裝置、羅馬尼亞和中國的各1套裝置只能生產丁基橡膠。2004年世界丁基橡膠生產廠家生產情況見表1所示。
消費現狀
汽車工業的發展和對汽車安全性、舒適性的進一步要求,加速了汽車輪胎子午化的技術進步及無內胎輪胎的發展。在過去幾年中,世界丁基橡膠的總消費量呈穩定增長的趨勢,年增長率一直保持在2%左右。最近兩年需求量有所增加,年均增長率達到5%左右。2003年全世界丁基橡膠的總消費量約為747kt/a,其中鹵化丁基橡膠的消費量約為500kt/a,約佔丁基橡膠總消費量的66.9%。預計到2006年,世界丁基橡膠的總消費量將超過800kt/a,其中鹵化丁基橡膠所佔的比例將超過70%。1996-2003年世界丁基橡膠的消費量情況見表2所示。
1993-1998年,美國丁基橡膠消費量的年均增長率為4.2%,1998-2002年消費量的年均增長率為1.5%,2002年美國丁基橡膠的總消費量為202kt/a,其中產量為182kt/a,進口量為67kt/a,出口量為47kt/a,產品約80%用於生產輪胎、膠管、輪胎製品,9%用於生產汽車零部件,6%用於生產膠粘劑、填縫膠和密封膠,4%用於醫藥領域,1%用於其他行業(主要包括電氣絕緣、各種襯裡、口香糖以及屋頂防水卷材等)。其中鹵化丁基橡膠主要用於生產無內胎輪胎,約佔丁基橡膠總消費量的60%,預計今後幾年,美國丁基橡膠的消費量將以年均約1.5%的速度增長,到2006年總消費量將達到220kt/a左右。美國丁基橡膠的供需情況見表3所示。
1997-2002年西歐丁基橡膠消費量的年均增長率約為4.8%,2002年總消費量為222kt/a,其中產量為236kt/a,進口量為19kt/a,出口量為33kt/a,產品的86.7%用於生產輪胎、膠管及輪胎製品,5.2%用於生產汽車零部件,8.1%用於其他領域(包括膠粘劑、填縫膠、密封膠、醫藥、電氣絕緣、各種襯裡、口香糖以及屋頂防水卷材等)。輪胎工業是西歐丁基橡膠的消費主體,法國又是西歐丁基橡膠消費最為集中的國家,其消費量約佔西歐丁基橡膠總消費量的37%,其次是德國,消費量約佔西歐總消費量的27%。西歐丁基橡膠的消費增長主要取決於汽車工業的發展,特別是取決於幾大汽車生產企業的發展方向和速度。預計今後幾年,西歐丁基橡膠消費量的增長幅度不會很大,到2006年總消費量將達到約230kt/a。西歐丁基橡膠的供需情況見表4所示。
由於亞洲金融危機的影響,1997-1998年日本丁基橡膠的消費量有所下降,1998年下降到最低谷,消費量僅為44kt/a,此後又快速增長,1998-2002年日本丁基橡膠消費量的年均增長率約為13.9%,2002年總消費量為67kt/a,其中產量為72kt/a,進口量為29kt/a,出口量為34kt/a,產品約82.8%用於生產輪胎、膠管及輪胎製品,10.9%用於生產膠粘劑、填縫膠、密封膠、醫藥等工業產品,6.3%用於其他領域(包括電氣絕緣、各種襯裡、口香糖以及屋頂防水卷材等)。最近幾年,由於無內胎輪胎的推廣,日本無內胎輪胎佔據了日本輪胎市場總量的95%,因此鹵化丁基橡膠的消費量不斷增加,日本鹵化丁基橡膠的消費量約佔丁基橡膠總消費量的70%。預計到2006年,日本丁基橡膠的總消費量將達到約70kt/a。
存在問題和發展建議
通過引進國外技術,中國建成了一套30kt/a的丁基橡膠生產裝置,並且通過近幾年的不斷努力,實現了安全平穩生產,產量不斷提高,在國內市場中所佔的份額逐漸擴大,在一定程度上滿足了國內實際生產的需求。但與國外發達國家相比,還存在一定的差距,主要表現在以下幾個方面:
⑴生產能力小,產量少,產品自給率低。中國丁基橡膠的生產能力只有30kt/a,遠低於其經濟規模50kt/a
的生產水平,更低於Exxon公司和Bayer公司70kt/a以上的生產規模,造成生產成本相對較高,產品自給率只有30%左右,在國際市場中缺乏競爭力;⑵技術力度開發不夠,品種牌號仍顯單一。中國引進的3個普通丁基橡膠產品牌號還不能完全生產,鹵化丁基橡膠等其他改性丁基橡膠產品還不能生產,造成一些高等級產品大量進口,而通用產品銷售不暢的被動局面,在一定程度上影響了中國丁基橡膠的健康發展;⑶產品質量不夠穩定。中國生產的丁基橡膠產品在粘連、黃變、產品批次、揮發分以及門尼值波動幅度等方面還存在在一些問題,還有待提高;⑷產品應用範圍較小。中國丁基橡膠產品約84%用於汽車行業行業,其他方面的應用還比較少;⑸技術服務水平還不能很好地滿足用戶的需求。為了使中國丁基橡膠工業快速健康發展,建議:
⑴提高產品質量,節省能耗和物耗,以提高產品在市場中的競爭力。產品質量是產品競爭的關鍵因素。針對中國丁基橡膠產品存在的問題,應該加大技改力度,不斷改善產品質量,把用戶的要求作為產品生產的標準;加大節能降耗力度,降低生產成本,使產品在國內市場上更具有競爭力。
⑵在保證現有丁基橡膠生產裝置正常穩定運行的前提下,加快新品種和新牌號的研究開發和生產,增加國產丁基橡膠的牌號品種,不斷完善產品品種結構,以更好地滿足市場需求。另外,除了加大丁基橡膠在輪胎內胎用膠的需求外,還應積極開發丁基橡膠的非內胎用膠市場。
⑶擴大生產規模,以滿足國內市場迫切需求的需要,提高國內市場的佔有率。中國丁基橡膠的產量僅能滿足國內需求量的三分之一左右,今後隨著需求量的增加,滿足率還可能更低,因此建議有條件的企業可以考慮新建1~2套50kt/a以上規模的生產裝置,以滿足國內實際生產的需求。
⑷儘快建成鹵化丁基橡膠生產裝置。鹵化丁基橡膠在丁基橡膠中佔有重要的地位,隨著中國子午線輪胎、無內胎輪胎以及醫藥瓶塞等應用領域應用技術的發展,國內對鹵化丁基橡膠的需求量將越來越大。因此國內應儘快著手鹵化丁基橡膠生產技術的準備或引進工作,儘早投產,以便能儘早滿足國內橡膠工業無內胎輪胎等產品發展用膠的需要。
⑸加強應用技術研究,提高服務意識和水平。加強與國內有關應用研究單位或輪胎等生產企業的聯繫和合作,研究開發適合國產丁基橡膠的內胎、水胎及膠囊的專用配方和加工技術。同時,建立一支專家型營銷隊伍,為實現丁基橡膠“市場-開發-生產-市場”的良性循環奠定基礎。
⑹積極擴大出口,參與國際市場的競爭。在滿足國內需求的前提下,應積極擴大向國際市場的出口,尤其是要加大向韓國等東南亞地區國家的出口,以便為今後丁基橡膠參與國際競爭奠定基礎。
談及汽車隔音,相信很多車主都願意清楚地查詢隔音的構成成分。當時要引薦隔音的首要構成組分——丁基橡膠,丁基橡膠是由異丁烯和異戊二烯在-100℃低溫共聚形成的高分子聚合物。製品丁基橡膠在己烷溶劑等溶解,然後與氯或溴進行鹵化反應可製成鹵化丁基橡膠。丁基橡膠的功能首要由聚異丁烯主鏈及其不飽和度極底的構造所選擇,其不飽和度僅為0.5%∽3.3%(mol)約為天然橡膠的1/50。鹵化的丁基橡膠首要用於生產汽車、卡車、飛機輪胎內襯層,丁基橡膠可用於出產汽車上的膠管、自行車的輪胎和球膽,鹵化丁基橡膠還可以用於醫用瓶塞、密封套和藥用膠塞等領域。口香糖基料是丁基橡膠的一個非常有趣的應用。
那麼當時一同來查詢丁基橡膠的長處:
氣體在聚合物等分散速度與聚合物分子的熱活動有關,丁基橡膠分子鏈中側甲基陳列密集,限制了聚合物分子的熱活動,因而透氣率低,氣密性好。
丁基橡膠硫化膠具有優異的耐熱不變性,硫磺硫化的丁基橡膠可在100℃或稍低溫度下於空氣中長時間運用,用樹脂硫化的丁基橡膠運用溫度可達150℃∽200℃。丁基橡膠的熱氧老化屬降解型,老化趨勢為軟化。
丁基橡膠分子構造中短少雙鍵,且側鏈甲基散布密度較大,因而具有優勝的接收震動和衝擊能量的特徵,在很寬的溫度局限內(-30∽-50℃)丁基橡膠的回彈特徵都不大於20%,這標清晰清楚明了丁基橡膠的接收機械功用的才幹優於其它橡膠。丁基橡膠在高變形速度下的阻尼性質是聚異丁烯鏈段所固有的,在很大程度上,它不受運用溫度、不飽和度程度、硫化外形和配方改動的影響。因而,丁基橡膠是那時較為理想的隔音減振資料。
丁基橡膠分子鏈空間構造呈螺旋狀,固然其甲基較多,但散布在螺旋兩側的每一對甲基彼此都錯開一個角度,所以丁基橡膠分子鏈仍相當和婉,玻璃化溫度較低,彈性也較好。
丁基橡膠分子鏈的高飽和度使之具有很高的耐臭氧性,和耐天候老化性。耐臭氧功用約優於自然橡膠,是丁苯橡膠的10倍。
丁基橡膠的高飽和構造,使之具有較高的化學不變性。丁基橡膠對大都無機酸和有機酸都具有優勝的抗腐蝕性,固然它不耐濃氧化酸,如硝酸和硫酸,然則能耐非氧化酸和中等濃度的氧化酸,並耐鹼溶液和氧化恢復溶液。在70%的硫酸中浸泡13周后,丁基橡膠強度和伸長率簡直沒有損丟失,而自然橡膠和丁苯橡膠功用已嚴厲下降。
丁基橡膠的電絕緣性和耐電暈功用比淺顯組成橡膠好,體積電阻率比淺顯橡膠高10∽100倍,介電常數為(1kHz)為2∽3功率因數(100Hz)為0.0026。
丁基橡膠的水浸透率極低,在常溫下的吸水率比其它橡膠低,僅為後者1/10∽1/15。
丁基橡膠是合成橡膠的一種,而瀝青阻尼片則是具有刺鼻性氣味的有害材料。
第一是聞氣味,含瀝青的材料會有刺鼻的氣味散發出來,第二更精準的方法是採用燃燒的方法,取一塊待測材料,點燃,如果劇烈燃燒,並伴有煙和強烈的刺激性氣味,併發生滴流現象。