連續反應器
連續反應器
連續反應器即反應一直持續的進行,不會斷(除開故障),內常設有攪拌(機械攪拌、氣流攪拌等)裝置,進料裝置,溫度壓力調節及監控設備等。
最常用的連續反應器是催化劑固定床反應器以及連續攪拌釜反應器(CSTR)。經過改進之後,CSTR可以採用催化劑的懸浮床形式。主要運用於化學品、燃料和聚合物的大規模生產上。
當某一化學產品產量達到約每年幾千萬磅(一般是經濟刺激下而進行的連續生產)的高水平時,就要用專門生產這種產品的反應器。這種反應器可能會穩定操作一年甚至更久,只有在定期維護、更換催化劑等情況下才按要求停車。
幾乎所有石油煉化行業中的反應器都是連續操作的。這是由於在煉廠生產的各種燃料、潤滑油和化學中間體的年生產率要求都很大。許多常見的聚合物如聚乙烯和聚苯乙烯也是在大體積連續反應器中生產,就像很多大宗化學品,如苯乙烯、乙烯、氨和甲醇的生產一樣。
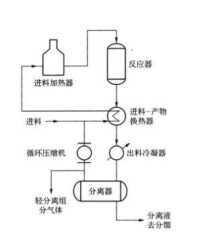
一個典型的連續反應設備流程
除非反應物的轉化率非常高,否則從連續反應器中出來的大部分未轉化的反應物通過循環同到原料流中。一些產物和(或)惰性組分也可能進行迴流用以控制反應器內的溫度等。
連續反應器通常在穩態下操作。進料流的流量和組成恆定,反應器操作條件不隨時間變化。在為理想連續攪拌釜式反應器(CSTR)和理想活塞流反應器(PFR)這兩種理想連續反應器建立設計方程時,我們假設處於穩態。
在正常生產狀態下,連續反應器應連續穩定運行,反應器的各個變數均需保持在某一恆定值上。所以,連續反應器的控制系統多為定值控制系統。
反應器進料流量控制的主要目的是為了充分利用原料,保證各進料組分進入反應器的量適宜且相互之間保持一定的比例,以減小由於原料使用不充分而帶來的經濟損失,並使進料流量儘可能穩定,以利於生產過程的乎穩操作。為此,可以對各進料組分的流量分別進行定值調節,如圖所示,如其中某一物流的流量不易進行控制,則可採用圖所示的定比值控制系統。
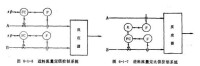
進料流量控制系統
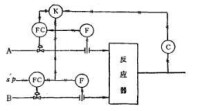
進料流量變化值控制系統
當進料濃度發生變僻由於其他原因使各進料組分間的實際比率發生變化時,可以利用成分分析儀錶監視反應器出口物料的成分,並以此為依據利用反饋修正進料比率的失衡。圖即為可以採用的方案。由於此法主要取決於成分的在線測量,所以這一方法的實施在實際過程中有一定的困難。當無 法在線修正進料比率時,可以採用離線分析的方法,定期對進料比進行人工校正。此外,利用反應器下游設備分離后的物流成分,也可以判斷反應器進料比是否適宜,並且在理論上也可以此為依據,對反應器進料比率進行在線反饋控制。但是,這樣會帶來很大的純滯后時間,嚴重影響調節系統的穩定性.但可以此作為對進料比進行人工校正的依據。
由於一般工業用流量測量儀錶的精度不是很高,所以,對流量控制要求較高時,採用這種儀錶的控韶系統將無法滿足要求。除開發精度更高的流量測量儀錶外,可以利用計量貯罐採用稱重或容量等梅度較高的測量方法測量反應器的進料量。對流量較小的進料,·可以使用計量泵調節其進料值。這樣就可以有效地改善進料配比的控制精度。
當進料中某一物料的價格遠高於其他物料時,由於這種物料的流量通常較小,故可以採用計量泵控制其流量。如這時採用比例調節,則應以此物流為主流量進行。為提高貴重物料的使用率,或出於其他原因,在實際反應系統中常有某一(廉價)物料過量使用,這時對進料流量比率的控制要求相對較低,控制質量一般比較容易得到滿足。當反應器物料循環使用時,循環物料多為過量,情況與此相似。但由於循環物流的成分會發生變化,所以也帶來了新的問題。對於催化刑,添加劑等流量小但控制要求高的物流,通常多採用多個反應器串聯使用時,只有第一個反應器的進料有可能進行定值調節。從第二個反應器開始,其進料量為前一個反應器的出料量,雖然有時也可進行調節,但只能以上游反應器的物料貯量為較移。因此,第一個反應器的控制情況是非常關鍵的。
如前所述,反應器的溫度控制常常用以代替直接的質量控制。另外,由於反應熱與反應溫度多為正反饋關係,所以反應器溫度有可能失控,使工藝過程處於危險狀況。因此,溫度控制是大多數反應器控制中不可缺少的一個環節。
根據控制的目的、反應器類型及反應器中所進行的化學反應等,反應器溫度控制所用的溫度點可以有不同的選擇。常用的溫度點包括反應器的內點溫度、反應器進口物料溫度、反應器出口物料溫度、反應器進出口物料溫差等。反應器的溫度控制一般以調節其換熱介質的流量或溫度實現,有時也可以利用反應器的進料溫度與流量等作為調節作用。
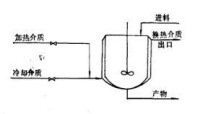
具有加熱和冷卻能力的換熱系統
由於溫度與壓力有一定的關係,反應器內壓力的變化常為溫度變化的前奏,因而可選取反應器內的壓力作為溫度串級調節的副參數,構成串級調節系統。由於壓力先於溫度變化而變化,所以該方案可以提高溫度控制的響應速度。壓力與溫度的關係多為非線性關係,並且將隨著反應器內反應混合物的濃度變化而改變,故應用時這一方法亦受到限制。如果能夠得到壓力與溫度之間的數學關係,則可以通過壓力對溫度測量進行補償,這樣可能會得到更好的調節品質,如聚合反應器的壓力補償溫度控制系統。
當有某種組分在反應器內處於沸騰狀態時,反應熱可以通過該組分的氣化帶出反應器。這時可以不對反應器溫度進行直接控制,而是調節與沸點溫度有對應關係的反應器內的壓力,從而將反應溫度控制在這一組分的某一沸點上。
多個反應器串聯使用時,如串聯CSTR系列,第一個反應器的控制情況是後續設備控制難易程度的關鍵,從第二個反應器開始,可以將前一個反應器的溫度及出口物料的流量作為前饋信號 引入其控制系統中 陶成前饋—R饋複合調節系統。
當反應器中進行的是氣相反應,氧化反應,氫化反應或高壓聚合等反應過程時,常需對反應器內的壓力進行控制。此外,由於反應器的壓力與其溫度之間有一定的關係,為得到較好的溫度控制,有時也需要對反應器的壓力進行控制。
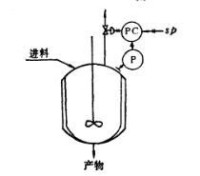
利用放空的反應器壓力控制
通過反應器後續設備,也能夠實現對反應器壓力的控制,如調節後續設備內的壓力,以影響反應器的出料量。顯然,這類調節的純滯后時間較大,使用中有一定的困難。壓力控制的典型例子是合成氨生產過程。在一般反應器中直接的壓力控制系統並不多見。
由予壓力過高可能會使反應器無法承受而發生爆炸,因而反應器應安裝必要的安全閥。
當化學反應涉及到鹼,酸等物質時,pH值往往是反應過程中的——個重要參數。由於能夠在線測量,所以pH值常常作為反應過程的質量指標加以控制。酸鹼中和過程的非線性程度很高,而且由於pH測量等原因使得過程有一定的純滯后時間,所以pH的控制通常被認為是比較困難的。
在進行pH控制系統的設計或改進時,首先應當對pH值測量裝置的選擇,安裝以及日常維護等給予足夠的重視,因為pH值測量的精度,測量滯后及由於採樣而帶來的純滯盾等因素對控制系統的調節品質影響很大。
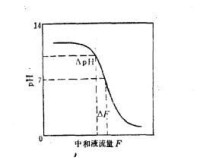
中和過程滴定曲線
由於化學反應過程的機理過於複雜,且化學反應器的操作往往涉及許多相互關聯的變數,所以在許多情況下都難以得到精確的反應過程的數學模型。由於反應過程具有高度的非線性特性,其中的某些參數,如傳熱係數。催化劑活性等具有時變特性,能夠得到的模型有時也難以求解,因而無法使用。由於這些原因,使得對模型要求很高的最優控制方法在反應過程中的應用受到很大限制。從這一點看,自整定和自適應控制方法的應用更為人們注意。
在線測量手段的缺乏是許多反應過程難以得到良好的控制的另一個原因。這也在控制方面向人們提出了如何利用狀態觀測器估計所需參數的問題。
在連續反應器中,除非原料與催化劑的接觸時間很長,加氫反應的主要以及次要產品都被連續地從體系中移出。接觸時間可以確保進料的完全轉化。因此,連續反應器中氮化物以及HS對催化劑的影響比間歇反應器中的小。並且,向體系中連續供應H可以準確地控制體系的壓力,同時控制HS與H的比值。當使用AR進料時,Gualda和Kasztelan觀察到間歇反應器中出現了與連續反應器中不同的催化劑失活類型。
連續操作條件下的固定床反應器可以做成包括微型反應器、實驗室裝置、中試裝置在內的各種尺寸。這些裝置的內徑不同,分別為10mm,20mm以及40mm左右,反應器直徑與催化劑顆粒直徑的比值分別約為7,13以及27。固定床反應器有下行床(即滴流床反應器)以及上行床反應器兩種操作模式。Bej等詳細討論了流體力學以及稀釋作用對兩種反應器操作模式的影響;A1-Dahhan等對高壓滴流床反應器進行了總結;Korsten和Hoffmann研究了對滴流床反應器動力學起關鍵作用的因素;Garcia和Pazos則著重於研究液滴滯留對於滴流床反應器的影響,他們發現液滴滯留的增加可以增大催化劑濕度,從而增加催化劑的利用率,在他們的研究中顆粒大小以及液體空速等動力學條件是重要的影響因素。
顯然,滴流床反應器比上行床反應器應用更廣。在滴流床反應器中,進料可以與催化劑很好地接觸。然後對於上行床反應器,可以通過固體床層的稀釋或者在催化劑床層的前後增加惰性固體層的方法來改善進料與催化劑的接觸問題。反應器尺寸的選擇是由研究目的決定的。例如,當研究目的是為了取得和工業操作相關的參數的時候,在中試裝置上能得到比實驗室裝置或微反裝置更可信的數據。選擇合適的反應器尺寸對於含金屬以及瀝青質的重油進料尤為重要。
內徑為10mm以及更小尺寸的反應器為微型反應器。使用這種反應器研究重油的加氫過程是有局限性的,尤其是對於減壓渣油和重油原油。因此,微反中催化劑的進料量低於1g。不過微型反應器直徑與催化劑顆粒直徑的比值可使催化劑顆粒直徑遠小於工業催化劑的1.5mm。因此,對於微反研究,需要將工業催化劑壓碎至直徑0.5mm以下。對於這樣的小顆粒,很難將重油進料加氨處理過程中的擴散現象進行正確的表徵,除非將更大體系中的測試結果對微反中的測試結果進行補充。反應初期由催化劑表面的快速積炭在微反裝置中就得到了好的表徵。同時,對於這樣小的顆粒,由堵塞或者壓降的增加導致的催化劑床層故障是不可避免的。當然,這個問題可以通過用惰性顆粒稀釋催化劑床層和,或用輕組分稀釋重油進料的方法來緩解。在催化劑床層的前後增加惰性固體層可以改善進料在催化劑中的分佈。Sie研究了將固定床反應器縮小到微反時的限制因素。對於更重的進料,其膠體穩定性隨溫度的升高而降低,這會使反應器壁面形成過多的沉積物而導致停工。因此,對於一些重油進料,很難在微反裝置或者更小尺寸的反應器中實現長周期運轉。使用重油進料(如減壓渣油)時微反裝置所變現出的這種局限性對於進料為輕質原料以及模型化合物時並不存在。對於輕質原料以及模型化合物,使用微反裝置可以得到加氫反應的有價值的數據。
實驗室規模的連續操作系統(內徑約20mm)已經成功用於重油加氫過程的各類研究。這類反應器中催化劑的體積可達100mL,是微反催化劑的20倍還多。在這種體系中,可以採用工業操作中使用的催化劑,因此也能得到更具有代表性、更可信的數據。從這種實驗室規模的反應器中得到的操作參數已經成功地與工業裝置上的操作參數相關聯。對於催化劑老化過程的研究要特別重視,這一數據對預測工業反應器內催化劑性能的模型非常重要。由於實驗室裝置中催化劑和原料的量較大,足以對待生劑和液體產物進行評價,而微反中的量很少,對於催化劑和產品的評價有局限性。
中試反應器的內徑和體積至少為實驗室裝置的2倍以及微反裝置的50倍,因此對於催化劑的大小和形狀沒有限制。同時也不需要稀釋重油原料來保證連續迸料。即使使用實驗室裝置可以對催化劑進行初步篩選,對於特定原料的催化劑的選擇最終需要在中試裝置上進行測試。在中試裝置上,即使對於減壓渣油以及重的拔頂原油,也可以進行很多天的長周期運轉。實踐表明,中試裝置可以得到用於工業裝置設計以及操作優化的大量數據。
具有不同大小及體積的連續攪拌釜反應器(CSTR)體系同樣可以用於重油加氫過程的研究,雖然應用的程度不如連續固定床反應器。Richardson等比較了在間歇反應器和CSTR上得到的Athabasca瀝青質渣油加氫動力學模型,得到的結果如圖4所示。使用CSTR來研究加氫反應的動力學模型具有一定的優勢,這是因為不存在最初的質量以及熱量梯度。另外,在CSTR中由於連續的攪拌可以避免在固定床反應器中存在的壓降問題。CSTR加氫過程的一種模式是液體以及H的連續再循環。反應器通過將催化劑裝入一個轉筐來運轉,或者採用靜止的催化劑筐,攪拌液體來運轉,也可以採用催化劑筐的多級串聯體系。在同一個反應器內,採用連續攪拌操作以及間歇操作兩種不同的方式研究了重質渣油的加氫脫金屬過程,得到的動力學存在顯著的差異:CSTR體系得到的動力學級數為1,而間歇操作體系中得到的動力學級數為1.5。
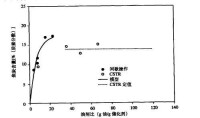
累集油劑對催化劑焦炭含量的影響
連續反應器應用於化學品、燃料和聚合物的大規模生產上。
其中M是進行聚合的單體,“n”是聚合物分子中單體單元數。例如,M可表示相對分子質量為28的乙烯單體(CH)。如果合成得到的聚乙烯的數均相對分子質量是200 000,n的值大約是7 000。聚烯烴如聚乙烯工業反應器如圖所示。
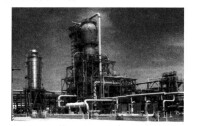
生產聚烯烴如聚乙烯和聚丙烯的Unipol反應器