東風汽車車輪有限公司
中國汽車車輪專業生產企業
東風汽車車輪有限公司,是我國規模最大的汽車車輪專業生產基地之一。公司由十堰本部、隨州車輪廠、襄樊車輪裝配廠和東風襄樊旋壓件有限公司等三個基地組成。
東風汽車車輪有限公司,是車輪和皮帶產品開發、生產、銷售為一體的大型企業,由十堰本部和隨州車輪廠兩個生產基地組成,企業綜合實力處於國內同行業領先地位。
企業規模領先。佔地面積283459平方米,其中工業建築面積141194平方米,固定資產凈值1.89億元,各類車輪生產能力300萬套。產品品種領先。覆蓋重、中、輕、微、農、特等七個系列200多個品種,形成車輪品種寬系列、多品種的格局。
技術水平領先。擁有成熟的板材衝壓、型鋼車輪成型、滾型車輪成型、旋壓等生產工藝;CAD、CAPP及三維有限無分析等先進技術廣泛應用於產品設計;產品檢測試驗達到國際先進水平。跨越世紀,東風車輪公司於時俱進,實現了歷史性的新跨越。
東風車輪公司改制五年來,面對來自行業和市場的雙中挑戰,不斷深化內部不改革,適時調整產品結構,加快發展建設步伐,有力地提升了企業的核心競爭力,創造了良好的生產經營業績。每年都全面超額完成總公司下達的各項經濟指標,累計實現利潤4100餘萬元。
拓市場、擴營銷,是公司創效益的首要工作。近幾年,公司以市場為導向,建立健全的產品開發個市場營銷體系,先後開發了40多種車輪和30餘種皮帶輪產品,公司的自銷收入連續3年達到8000萬元左右,自銷量由以往只佔銷售總額的5%升到25%以上。
謀求可持續發展,是公司興旺發達的保證。在發展問題,公司強調的是“可持續”,不因領導的變更而停滯,不因眼前的利益而搞短期的行為。一方面,抓緊改進、改造工作,突破制約生產能力的“瓶頸”,提高生產的柔性化,增強了多品種、小批量生產組織的應變能力。一方面,抓緊實施“雙高一優”及西班牙貸款建設無內胎項目,年內即可批量投產。
公司的前身第二汽車製造廠車輪廠,始建於1970年9月。1996年12月改製為東風汽車車輪有限公司。2003年融入東風日產合資合作體系。公司佔地面積29.64萬平方米,其中工業建築面積16.6萬平方米(十堰18.27、隨州7.7、襄樊3.67)。企業固定資產原值5.32億元,註冊資金14534萬元。公司擁有28條流水生產線,其中進口生產線5條。工藝設備937台,其中主要設備466台,進口設備61台。公司鋼輪生產能力700萬套,鋁輪生產能力100萬套。車輪產品100餘種,覆蓋重、中、輕、轎、微、特汽車車輪全系列。公司十堰工廠可生產直徑17.5″-32″、寬度5.25″-12″的各類卡車鋼製滾型車輪及直徑12″-18″、寬度3.5″-8″的各類輕轎鋼製滾型車輪及直徑16″-20″、寬度3.5″-8.5″的各類型鋼車輪。公司隨州工廠可生產直徑12″-17.5″、寬度3.5″-7″各類輕轎鋼製滾型車輪,直徑16″-20″、寬度5″-7.5″的各類型鋼車輪。東風襄樊旋壓件有限公司可生產各類旋壓皮帶輪,年產能力150萬隻。
05年市場份額:輕轎微滾型車輪佔13.5%,型鋼車輪佔11.57%。05年實現主營業務銷售收入(剔除輪胎)5.45億元,其中出口銷售收入3094萬元;06年1~8月實現銷售收入3.41億元,其中出口銷售收入3055萬元,完成息稅前利潤600萬元。
公司奉行的質量方針是:強化基礎,致力改進,追求精品,用戶滿意。1997年通過ISO9001質量體系認證;2000年通過QS9000質量體系認證,2005年通過ISO/TS16949質量體系認證;主要產品。
7.50V-20車輪合成2006年省級定期監督檢驗合格。公司奉行的環境/職業健康安全方針是:遵守安全環保法規,防治結合持續改進,節能降耗減污增效,安全健康規避風險,關愛員工保護環境,樹立東風日產品牌。2001年通過GB/T24001-1996環境認證,2005年通過GB/T24001-2004環境認證和GB/T28001-2001職業健康安全“一體化”管理體系認證。
企業戰略願景:中國汽車車輪製造行業“小型巨人”。
企業經營理念:質量對用戶負責,成本對市場負責。
主打廣告詞:東風車輪,讓世界轉起來。
2010年1-10月,東風車輪有限公司產銷車輪591.1萬套,超預算25.6%;主營業務銷售收入10.8億元,超預算58%,單月平均銷售收入超過1億元。
據介紹,東風車輪公司生產經營呈現出銷售收入遠超預算,完成挑戰目標的同時創歷史新高;規模效益凸現,盈利能力高於預算和同期;十堰、隨州、襄樊三地事業單元首次同時高產、全面盈利等經營亮點。
2010年以來,東風車輪公司圍繞“轉變運營加快發展提升優勢做強做大”的戰略思想,按照“效率提升年”的總體工作要求,以提升效率和績效為目標,以增強自我發展能力和綜合實力為主線。通過在主要生產線開展“效率提升改善”活動,採取狠抓現場管理、設備運行效率等有力措施,持續保持了平均日產超萬件的生產能力,型鋼車輪創16.02萬件的月份產量新高,滾型車輪創4.93萬件的月份產量新高;提高開發市場、適應市場的能力,抓住商用車旺銷的市場機遇,東風內市場銷售收入同比最大增幅達115%。卡滾車輪銷量同比增幅尤為顯著,銷量達到894%。
在外部市場,東風車輪公司加大與主機廠同步開發的步伐,確保獲得新產品份額,部分主機廠實現批量供貨,第三條輕轎滾型車輪生產線投產後,更大程度滿足了主機廠需求,擴大了市場競爭優勢,新增了穩定的銷售增長點,2010年1-10月累計實現新品銷售收入1.86億元,新品貢獻率達到20%,工藝改進實現技術降成本1574萬元,技術降成本率1.9%。
年產銷破500萬
2012年12月22日,伴隨著喜慶的鑼鼓和歡快的音樂,400餘名東風車輪公司幹部員工以舉行“激情跨越500萬”慶典的形式,共同見證該公司2012年第500萬隻乘用車車輪下線。
下線儀式上,東風啟辰車輪設計者李素雄從塗裝線上摘下2012年第500萬隻乘用車車輪,交給由30多名優秀員工代表、退休員工代表、部門負責人組成的梯隊,共同分享屬於東風車輪人成功跨越500萬隻的豪情。東風車輪公司總經理梁真最後將車輪放在第500萬隻車輪下線展示台上。
據了解,2012年,東風車輪公司全年乘用車車輪產量將達到524萬隻,同比增長11%;全年將實現金屬件銷售收入近4億元,同比增長10%,連續八年在乘用車OEM配套市場處於領跑地位。
梁真表示,東風車輪公司全體幹部員工要緊緊抓住乘用車車輪新製造基地建設啟動的機遇,充分發揮自身優勢,有效利用地方資源,堅持科學發展,著力提高管理水平,提升研發能力,優化物流水平,增強市場競爭、開拓創新能力,繼續追尋“乘用車車輪產能倍增1000萬隻,建設具有國際標桿水平的研發中心和製造基地”的新夢想。
2013首季破記錄
東風車輪有限公司2013年第一季度產銷乘用車車輪167萬隻,同比增長28%,預實比增長17%,刷新了乘用車車輪季度產銷量歷史新紀錄。其中,僅3月份乘用車車輪產銷就達到60.6萬隻,為該公司單月歷史最高產銷量。
東風車輪公司準確進行市場定位,根據市場形勢的風雲變幻,及時跟進調整乘用車車輪市場營銷策略,內部不斷強化能力建設、產品研發和效率提升工作,產銷量始終維持年均增長12%以上,領先於國內同行業。特別是該公司乘用車市場拓展行動——“亮劍新市場,決勝3+7”活動開展以來,產銷量大幅攀升,乘用車車輪不斷刷新班產、日產、月產和季產新紀錄,進一步提升了東風乘用車車輪市場的美譽度。
2010年12月17日,東風車輪有限公司在十堰工廠召開現場會,向十堰、襄樊、隨州三地全體員工發出動員令:採取一切必要的可行性措施,全力衝擊全年車輪產銷量730萬隻,主營業務銷售收入13億元的終極目標。
進入2010年四季度,東風車輪公司市場訂單和產銷量仍延續逐月攀升的態勢,並呈現出銷售大於產出的良好態勢。在大好的市場形勢下,東風車輪公司開足馬力,全力以赴挑戰目標。各部門緊盯當日生產計劃完成率,確保生產調度指令的落實;由製造管理科牽頭,對生產發交中的突出問題會同職能部門限時解決;將內外部物流與生產資源到貨周期統一集中管理,強化生產資源保障服務,減少生產等待,使各方面資源得以更有效的發揮。
據悉,截至2010年12月15日,東風車輪公司已累計產銷車輪突破670萬件;主營業務銷售收入突破12億元,同比增幅60%,均高於行業平均水平。
2010年11月11日,東風車輪有限公司召開全體幹部大會,宣布組織機構重組及各層面管理職能界定實施方案。隨後,東風車輪公司所屬十堰、隨州、襄樊三地事業單元職能部門及工廠正式按照管理層、經營管理單元、製造單元三個新的組織機構開始運作。至此,東風車輪醞釀8個月之久的組織機構重組工作正式完成。
據介紹,為適應新形勢下中長期戰略發展的需要,進一步優化公司體制機制,東風車輪公司多次召開專題研討會,在認真分析討論現有組織機構利弊的基礎上,提出了全新的組織機構設置構想,將分佈於三地的事業單元整合重組,採用公司———工廠制,管理組織機構設置遵循所有製造及相關單元從其他管理單元中剝離的原則,分別組成了公司總部、十堰工廠、隨州工廠和東風襄樊旋壓件子公司,工廠分別由工廠長負責,工廠長由公司副總經理兼任。公司本部管理部門統一稱為“部”,工廠業務部門統稱為“科”,工廠所有生產車間統稱為“車間”,對機構名稱進行相應變更,並對新的組織架構下相應的管理職能進行了明確界定,以有效的公司管理模式推進專業化分工,使組織效率得以提升。
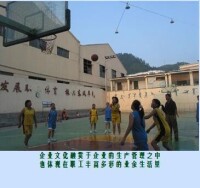
企業文化
早在九十年代初,東風公司就確立了自己的哲學和理念,即:“挑戰自我,視今天為落後”。東風有限在全面調查分析了產量、產值、利潤、人均收入等情況后,制定並啟動了具有挑戰性的中期事業計劃,其中包括東風和日產兩個大公司之間的相互學習和融合。這就要求東風有限必須建設適合開放融合創新特色的、具有強大活力的新的企業文化。這種新的企業文化的基礎,來自於東風35年來優良的文化積澱。這種新的企業文化的動力,來自於敢於正視並否定曾經引以為自豪的、但如今並不適應合資企業長遠發展的文化固習。因此,有必要重提“挑戰自我視今天為落後”。一個企業的挑戰目標,便是企業所希望實現的未來,它可以是成果目標,也可以是一種理想境界。
東風公司幾年前提出的企業目標是:引導、改善和改變人們行路難和物流落後狀態;創造優秀的產品和服務,最大限度地滿足市場需要,創建具有國際競爭力的企業。正是基於這樣的基礎,我們現在提出了讓全體員工認可的企業價值標準和價值取向,要把東風有限建成自主、開放、可持續發展,並具有國際競爭力的知名汽車公司;在人才價值觀上,採取專業崗位薪酬制度改革等措施,使東風公司倡導多年的“留住人才、用好人才”得到實實在的體現;在企業管理上,大力推進QCD改善活動,把企業現代化管理真正落實到每一天每一事的細微之處;我們現在每年確立必達目標與挑戰目標,把完成目標與工資獎勵持鉤,通過激勵員工的個人價值,來實現企業價值和發展目標。通過學習國外先進的管理經驗和管理理念,跳出過去的思維慣性和行為方式,達到真正意義上的開放和融合。
在過去東風“實現價值,挑戰未來”的企業精神基礎上,將東風有限企業精神表述為“面向世界,實現價值,挑戰未來”,這樣既可保持東風公司企業精神的一致性,又能準確地描述東風有限作為合資公司的定位與追求。
另外,東風有限文化融合必須堅持以“合”為貴。東風與日產合資的價值取向是合作雙贏。從合作開始,雙方都要著力營造具有共同目標的企業內部和外部的合作關係,通過對內部價值鏈進行整合,凝聚企業內部所有資源,形成既不易被對手模仿又能帶來超額利潤的自身核心競爭力。也只有內部價值鏈的整合與優化,才會對外部價值鏈具有強大的輻射與吸附作用。
建設中外合資企業文化,特別需要注意加強雙方的交流與融合,消除文化差異帶來的溝通困難,減少合作阻力與碰撞。東風與日產各有自己的民族文化傳統和自己的企業文化經驗,以積極的態度對話、交流與融合,對共同的文化進行篩選、甄別、借鑒與吸收,通過文化的溝通、交融與創新形成具有東風有限特色的企業文化。在文化融合與創新活動中,我們始終要有“視今天為落後”的心態,才能使我們的企業“日新,日日新,日又新”。
中國汽車車輪製造行業“小型巨人”。
質量對用戶負責,成本對市場負責。
東風車輪,讓世界轉起來。
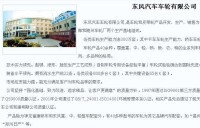
東風汽車車輪有限公司
一、工人培訓方面:
1、班組長培訓,每年舉辦2-3期培訓班,新任班組長必須100%進行培訓。
4、對輔助生產人員,如檢查工、電鉗維修工、機加工等工種進行專業理論和技能培訓,結合新設備、新工藝、新技術進行有針對性的培訓,提高他們的素質,以滿足生產的需要。
5、新工人培訓,凡進廠的新工人,都要進行入廠教育和專業理論、實際操作培訓,簽定師徒合同,嚴格堅持“先培訓、後上崗”的原則。
7、結合生產實際,大力開展技術練兵和技術比武活動,提高生產工人和技術工人的實際操作技能,培養一大批技術骨幹和工種帶頭人。
二、幹部培訓:
2、管理人員培訓,開展各種適應性培訓,做到普及與提高相結合。選派人員參加汽院、黨校及各系統舉辦的各類單科班和專題班進行培訓。搞好計算機的普及培訓,全部進行初級培訓,部分人員通過中級培訓。對計劃統計人員進行系統的有針對性的培訓,提高他們的專業技能。對各類管理人員加強繼續教育培訓,強化學分制管理,對完不成規定學分者進行考核。
3、科技人員培訓,隨時給科技人員進行充電,進行新知識的擴充,特別是產品設計和開發人員,不惜一切代價進行培訓,包括選送到大專院校進行深造或外聘專家到我公司講學。加強計算機和外語的普及與提高培訓,舉辦各類繼續教育專題班和單科班,工程技術人員必須加強計算機繪圖知識培訓,全部掌握計算機繪圖知識。
4、大中專畢業生培訓,首先進行入廠教育,然後下車間進行勞動實習,勞動實習合格轉入專業見習,專業見習合格正式止崗。
三、其它培訓:
1、根據各部門和系統的要求,搞好其它各種培訓,如黨員培訓、團干培訓、積極分子培訓、女工培訓、普法培訓等。
全員培訓面達90%以上,為公司的生產與發展墊定了基礎。
東風汽車車輪有限公司開發能力較強,先後開發出5.50F—16、7.00T—16、7.00T—20、7.50V—20等。5°滾型車輪是我們開發的重點產品,用自己編製的工藝、自己設計的模具開發出了“富康”轎車車輪。東風1.5T系列車的5°滾型車輪代表產品有4.00B×12、51/2J×14、51/2K×15車輪;15°滾型車輪有6.75×17.5、8.25×22.5、8.25×16.5等,15°滾型車輪既可以和東風系列車配套,又可出口創匯。
車輪及皮帶輪產品開發,採用CAD、CAPP輔助設計和有限元分析,大大提高了設計質量和設計水平。
東風汽車車輪有限公司現有型鋼車輪、滾型車輪、工程車輪等6大類40多種;10多種皮帶輪基本形成系列。
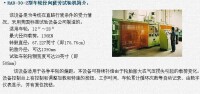
RAD-30-2型車輪徑向疲勞試驗機
1、RAD-30-2型車輪徑向疲勞試驗機簡介:
該設備是為考核在直路行駛條件的受力情況,採用美國標準試驗設備公司製造的。
適用車輪:12″~28″。
最大徑向載荷:136KN。
轉鼓直徑:67.227英寸(即170.76cm)。
輪胎外徑:可達1390mm。
試驗車輪輪輞寬度可達20英寸(即508mm)。
該設備適用於各種車輪的偏距。本設備可持續補償由於輪胎脹大或氣壓損失引起的載荷變化。設備控制台上有控制和調整載入和轉速的按鈕,工作時間、車輪累計循環次數等自動記錄、由數字儀錶顯示,並有複位按鈕。
2、RF30K車輪彎曲疲勞試驗機簡介:
該設備是為考核車輪在急轉彎情況下的受力情況,採用美國標準試驗設備公司製造的。
適用於車輪直徑:12″~28″。
最大負荷:40.68KN·m。
力臂:1.0668米。
轉速:435轉/分。
彎曲疲勞試驗機是一立式獨立的台架設備,適用於輕、重型、載貨汽車的彎曲疲勞試驗,在車輪旋轉的情況下同時長時間地對車輪施加一個同心的彎矩。
該設備裝備了必要的控制裝置和安全防護裝置,可進行無人看守試驗。為適應不同偏距、寬度的車輪,力臂在垂直方向上可上下調整;能持續給出試驗載荷的數字顯示信號;累積循環次數記錄,達到預定值時,試驗機自動停止工作,所有數字顯示可在控制面板上讀到。
3、Ⅲ311離心式彎曲疲勞試驗機簡介:
Ⅲ311離心式彎曲疲勞試驗機是一立式獨立台架式設備。適用於載貨汽車、客車、越野汽車和掛車的鋼製輻板式車輪的疲勞強度試驗。
該設備有一個水平工作中及8個“T”型槽與壓板配合將車輪夾緊,同時將車輪定心。車輪靜止不動,而在其載入軸下端承受一個旋轉的預定的彎矩。
適用於車輪:12″~24″。
電機最大轉速:1500轉/分。
最大負荷:20KNm。
4、MARK-1型彎曲疲勞試驗機簡介:
本機為輕、轎車輪的專用彎曲疲勞試驗設備,是我廠產品開發、質量控制和適應神龍公司對車輪生產廠家的質量控制要求的必備裝備。
本設備是在動態下測試汽車車輪疲勞壽命,車輪安裝面上承受一個已知彎矩,車輪在工作檯面上,並與工作台一起旋轉。在載入軸端施加一個力,此力在車輪上產生一個旋轉彎矩,並引起車輪的內部應力,這種應力是汽車車輪在“轉彎”中遇到的。
適用於車輪:12″~17″。
最大負荷:13000N·m。
寬度:3″~7″。
位移量:最大10mm。
5、ET86平衡機特點:
━一次啟動測量,可作卡車、轎車車輪平穩。
━微電腦數據處理中央系統。
━不平衡量可用g或ounee表示(顯示)。
━平衡轉速低。
━數據採集完畢自動制動。
━人工控制氣剎使轉軸定位。
━保護罩放下時自動啟動。
━面罩上附平衡塊盤。
━檯面上帶鐵鑽,用以修復平衡塊。
━12″單色綠點顯示屏,多種程序供選擇。
━平衡方式:標準雙面動平衡、單面靜平衡、鋁合金轎車、卡車車輪。
━通用程序:標定,自診斷。
━使用輔導程序。
━精度因子:卡車車輪10g,轎車車輪1g。
━卡車車輪範圍:
輪輞寬度:4″~20″。
輪輞直徑:12″~28″。
車輪—設備距離:400mm。
最大車輪重:200kg。
━轎車車輪範圍:
輪輞寬度:1.5″~20″。
輪輞直徑:8″~23″。
汽車車輪衝擊試驗機特點:
本試驗機用於評價轎車無內胎輕合金車輪軸向路同衝撞特性的試驗室試驗,也可用於評價無內胎鋼製轎車車輪的衝撞特性試驗。
ISOT141-1981(C)道路車輛——車輪——衝擊試驗規程。
設計原理:
1、車輛安裝的軸線方向與沖頭運動方向成13°±°角度;
2、沖頭衝撞輪胎接觸面的尺寸:長×寬=375mm×125mm;
3、車輪安裝支架撓性檢測:在垂直方向置1000kg;
質量於車架中心處測量其變形(撓度)應為7.5mm±10%
6、WE-300A液壓式萬有試驗機簡介:
本試驗機利用液壓加荷,液壓夾持試樣,操作方便,試驗讀數準確可靠,能做一般鋼材等金屬材料之拉伸、壓縮、彎曲及剪切試驗。
最大負荷:300千牛。
試樣夾持寬度:70mm。
拉伸鉗口間最大距離:550mm。
HG-1紅外碳硫分析儀說明:
主要參數:
分析範圍:碳0.002-6.0%。
硫0.0002-0.35%。
靈敏度:0.0001%。
電子天平感量:0.001g。
東風汽車車輪有限公司建立了以營銷為龍頭的生產經營運行機制,形成了“銷售、生產、科研、服務”四位一體的“大營銷”格局,組成了覆蓋22省38市的經銷網路,能夠通過完善營銷體系,服務在同行廠家之前,服務在客戶購貨之中,服務在用戶使用之後。本公司車輪產品的保修里程為50000公里,在三包期內對用戶實施“包修、包退、包換”服務,有專門機構負責賠償件的鑒定、賠償、解答顧客的各種疑義,實行優質服務,讓客戶對本公司產品質量滿意、品種滿意、價格滿意、服務滿意。

營銷網路
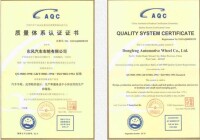
企業資質
1994年,公司開始接受GB/T19000族標準,對標準的基本知識開展了全員教育。1995年根據公司生產,經營的特點,公司決定在全面質量管理活動的基礎上逐步建立起符合94版ISO9001idtGB/T19001《質量體系設計、開發、生產、安裝和服務質量保證模式》,覆蓋公司輕、中、重車輪產品的文件化質量保證體系。1997年6月19日正式發布了公司第一版《質量保證手冊》,並形成了規範的四層次文件,文件化的質量體系開始運行。公司質量管理工作進一步系統化、規範化、制度化。

企業資質
為驗證、提高公司質量體系運行的符合性、有效性,公司每年按程序組織二次質量體系內部審核和一次管理評審。根據質量體系運行情況和審核結果不斷改進質量體系,1999年公司根據長遠發展需要,通過兩家認證機構的擴大認證和監督審核,把皮帶輪產品納入質量體系認證範圍。

東風汽車車輪有限公司
2005年市場份額:輕轎微滾型車輪佔13.5%,型鋼車輪佔11.57%。05年實現主營業務銷售收入(剔除輪胎)5.45億元,其中出口銷售收入3094萬元;06年1~8月實現銷售收入3.41億元,其中出口銷售收入3055萬元,完成息稅前利潤600萬元。
2010年1-10月,東風車輪有限公司產銷車輪591.1萬套,超預算25.6%;主營業務銷售收入10.8億元,超預算58%,單月平均銷售收入超過1億元。東風車輪公司生產經營呈現出銷售收入遠超預算,完成挑戰目標的同時創歷史新高;規模效益凸現,盈利能力高於預算和同期;十堰、隨州、襄樊三地事業單元首次同時高產、全面盈利等經營亮點。
2010年以來,東風車輪公司圍繞“轉變運營加快發展提升優勢做強做大”的戰略思想,按照“效率提升年”的總體工作要求,以提升效率和績效為目標,以增強自我發展能力和綜合實力為主線。通過在主要生產線開展“效率提升改善”活動,採取狠抓現場管理、設備運行效率等有力措施,持續保持了平均日產超萬件的生產能力,型鋼車輪創16.02萬件的月份產量新高,滾型車輪創4.93萬件的月份產量新高;提高開發市場、適應市場的能力,抓住商用車旺銷的市場機遇,東風內市場銷售收入同比最大增幅達115%。卡滾車輪銷量同比增幅尤為顯著,銷量達到894%。
在外部市場,東風車輪公司加大與主機廠同步開發的步伐,確保獲得新產品份額,部分主機廠實現批量供貨,第三條輕轎滾型車輪生產線投產後,更大程度滿足了主機廠需求,擴大了市場競爭優勢,新增了穩定的銷售增長點,2010年1-10月累計實現新品銷售收入1.86億元,新品貢獻率達到20%,工藝改進實現技術降成本1574萬元,技術降成本率1.9%。
2010年12月17日,東風車輪有限公司在十堰工廠召開現場會,向十堰、襄樊、隨州三地全體員工發出動員令:採取一切必要的可行性措施,全力衝擊全年車輪產銷量730萬隻,主營業務銷售收入13億元的終極目標。
進入2010年四季度,東風車輪公司市場訂單和產銷量仍延續逐月攀升的態勢,並呈現出銷售大於產出的良好態勢。在大好的市場形勢下,東風車輪公司開足馬力,全力以赴挑戰目標。各部門緊盯當日生產計劃完成率,確保生產調度指令的落實;由製造管理科牽頭,對生產發交中的突出問題會同職能部門限時解決;將內外部物流與生產資源到貨周期統一集中管理,強化生產資源保障服務,減少生產等待,使各方面資源得以更有效的發揮。
截至2010年12月15日,東風車輪公司已累計產銷車輪突破670萬件;主營業務銷售收入突破12億元,同比增幅60%,均高於行業平均水平。
公司奉行的質量方針是:強化基礎,致力改進,追求精品,用戶滿意。1997年通過ISO9001質量體系認證;2000年通過QS9000質量體系認證,2005年通過ISO/TS16949質量體系認證;
7.50V-20車輪合成2006年省級定期監督檢驗合格。公司奉行的環境/職業健康安全方針是:遵守安全環保法規,防治結合持續改進,節能降耗減污增效,安全健康規避風險,關愛員工保護環境,樹立東風日產品牌。2001年通過GB/T24001-1996環境認證,2005年通過GB/T24001-2004環境認證和GB/T28001-2001職業健康安全“一體化”管理體系認證。
2010年11月11日,東風車輪有限公司召開全體幹部大會,宣布組織機構重組及各層面管理職能界定實施方案。隨後,東風車輪公司所屬十堰、隨州、襄樊三地事業單元職能部門及工廠正式按照管理層、經營管理單元、製造單元三個新的組織機構開始運作。至此,東風車輪醞釀8個月之久的組織機構重組工作正式完成。
為適應新形勢下中長期戰略發展的需要,進一步優化公司體制機制,東風車輪公司多次召開專題研討會,在認真分析討論現有組織機構利弊的基礎上,提出了全新的組織機構設置構想,將分佈於三地的事業單元整合重組,採用公司———工廠制,管理組織機構設置遵循所有製造及相關單元從其他管理單元中剝離的原則,分別組成了公司總部、十堰工廠、隨州工廠和東風襄樊旋壓件子公司,工廠分別由工廠長負責,工廠長由公司副總經理兼任。公司本部管理部門統一稱為“部”,工廠業務部門統稱為“科”,工廠所有生產車間統稱為“車間”,對機構名稱進行相應變更,並對新的組織架構下相應的管理職能進行了明確界定,以有效的公司管理模式推進專業化分工,使組織效率得以提升。