熱軋
在再結晶溫度以上進行的軋制
熱軋(hot rolling)是相對於冷軋而言的,冷軋是在再結晶溫度以下進行的軋制,而熱軋就是在再結晶溫度以上進行的軋制。簡單來說,一塊鋼坯在加熱后經過幾道軋制,再切邊,矯正成為鋼板,這種叫熱軋。能顯著降低能耗,降低成本。熱軋時金屬塑性高,變形抗力低,大大減少了金屬變形的能量消耗。熱軋能改善金屬及合金的加工工藝性能,即將鑄造狀態的粗大晶粒破碎,顯著裂紋癒合,減少或消除鑄造缺陷,將鑄態組織轉變為變形組織,提高合金的加工性能。
熱軋是指在金屬再結晶溫度以上進行的軋制。
再結晶就是當退火溫度足夠高,時間足夠長時,在變形金屬或合金的纖維組織中產生無應變的新晶粒(再結晶核心),新晶粒不斷的長大,直至原來的變形組織完全消失,金屬或合金的性能也發生顯著變化,這一過程稱為再結晶,其中開始生成新晶粒的溫度稱為開始再結晶溫度,顯微組織全部被新晶粒所佔據的溫度稱為終了再結晶溫度,一般我們所稱的再結晶溫度就是開始再結晶溫度和終了再結晶溫度的算術平均值,一般再結晶溫度主要受合金成分、形變程度、原始晶粒度、退火溫度等因素的影響。
以上就是理論上的熱軋的簡單原理,在我們鋁加工行業的實際生產中主要的體現是,當鑄錠在加熱爐內加熱到一定的溫度,也就是再結晶溫度以上時,進行的軋制,而這一個溫度的確定主要依據是鋁合金的相圖,也就是最理想化的情況下,加熱溫度的確定為該合金在多元相圖中固相線80%處的溫度為依據,這就牽扯到了不同合金多元相圖的問題,加熱溫度的確定是以該合金固相線的80%為依據,在制度的執行中,根據實際的生產情況,根據設備的運行情況,多加修改所得到的適合該合金生產的溫度。
熱軋的特點:
1、能耗低,塑性加工良好,變形抗力低,加工硬化不明顯,易進行軋制,減少了金屬變形所需的能耗。
2、熱軋通常採用大鑄錠、大壓下量軋制,生產節奏快,產量大,這樣為規模化大生產創造了條件。
3、通過熱軋將鑄態組織轉變為加工組織,通過組織的轉變使材料的塑性大幅度的提高。
4、軋制方式的特性決定了軋后板材性能存在著各向異性,一是材料的縱向、橫向和高向有著明顯的性能差異,二是存在著變形織構和再結晶織構,在沖制性能上存在著明顯的方向性。
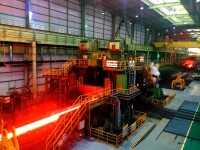
熱軋
帶鋼熱軋機由粗軋機和精軋機組成。粗軋機組分半連續式、3/4連續式和全連續式三種:①半連續式有一台破鱗(去掉氧化鐵皮)機架和 1台帶有立輥的可逆式機架;②3/4連續式則除上述機架外,還有2台串列連續布置機架;③全連續式由6~7台機架組成。精軋機組均由5~7台連續布置的機架和卷取機組成。帶鋼熱軋機按軋輥輥身長度命名,輥身長度在914毫米以上的稱為寬頻鋼軋機。精軋機工作輥輥身長度為1700毫米的,稱為1700毫米帶鋼熱軋機,這種軋機能生產1550毫米寬的帶鋼卷。
帶鋼熱軋按產品寬度和生產工藝有四種方式:寬頻鋼熱連軋、寬頻鋼可逆式熱軋、窄帶鋼熱連軋以及用行星軋機熱軋帶鋼。
1、軋制的理論:軋制是藉助旋轉軋輥的摩擦力將軋件拖入軋輥間,同時依靠軋輥施加的壓力使軋件在兩個軋輥或兩個以上的軋輥間發生壓縮變形的一種材料加工方法。
2、軋制參數:軋制變形過程,厚度方向的壓縮是主導變形。當軋件厚度方向受到軋輥壓縮時,將使金屬發生沿縱向和橫向的流動,但是縱向的延伸變形總是大大超過橫向的擴展量,這是因為輥面摩擦力對寬向流動的阻礙總是大於縱向,也就是說,相對縱向而言,橫向的寬展總是比較小,軋制時的變形指數主要為:
1)絕對壓下量:表示軋制前後軋件厚度絕對的變化量,便於生產操作上直接調整軋輥的輥縫值。
2)加工率:用於記錄近似變形程度。
3)寬展:生產現場用於表示寬展的絕對增加值。
3、軋制過程的建立:軋制過程總共經歷4個階段,分別為咬入階段,拽入階段,穩定軋制階段和軋制終了階段。
1)咬入階段:軋件開始接觸旋轉的軋輥,軋輥開始對軋件施加作用,將其拖入輥縫間,以便建立軋制過程。
2)拽入階段:一旦軋件被旋轉著的軋輥咬著后,軋輥對軋件的拖拽力增大,軋件逐漸充滿輥縫,直至軋件前端到達兩輥連心線位置為止。
3)穩定軋制階段:軋件前端從輥縫間出來后,繼續依靠旋轉軋輥摩擦力對軋件的作用,連續、穩定地通過輥縫,產生所需要的變形,厚度方向壓縮,縱向延伸。
4)軋制終了階段:從軋件後端進入輥縫間的變形區開始,直至軋件與軋輥完全脫離接觸為止。
4、實際軋制生產中會出現軋件不能順利被軋輥咬入,致使軋制過程停止,以及咬入角不合理引起板材塑性變形不均勻的情況,不僅降低了生產效率,而且產品易存在質量問題,這是因為咬入並軋制的過程是一個不穩定過程,當咬入的時候,變形區的幾何參數,運動學參數都是變化的,所以咬入角即軋輥與軋件接觸部分所夾的中心角是軋制過程中一個極其重要的影響因素,合理的咬入角應當在15度到20度之間,且當軋輥半徑相同時,咬入角隨壓下量呈拋物線形增長。
5、穩定軋制是軋制過程的主要階段,但是咬入過程卻是建立軋制過程的先決條件。
軋件在咬入的這一瞬間,軋件受到軋輥的正壓力N和切向摩擦力T的作用,根據摩擦定律,可以將N和T分解為同一方向上的兩個力,即垂直方向上和水平方向上,這樣就有了N和T兩個力的分力在兩個方向上的疊加,疊加后在垂直方向上讓軋件受到壓縮,產生塑性變形,而水平方向上的兩個力方向相反,即如果要順利的咬入的話,T 的水平方向上分力要大於N的水平方向上的分力,這樣就固定了一個指標即咬入角來判定咬入狀態。
6、穩定軋制時的咬入條件
軋件咬入后,軋制進入拽入階段,軋件與軋輥間的接觸面隨著軋件向輥縫間的充滿而增加,因此軋輥對軋件的作用力點的位置也向出輥方向移動,使輥間的力平衡狀態發生變化,經過公式計算得出α<2β為穩定軋制的臨界條件。
7、凡是減小軋輥咬入角和增大輥面對軋件摩擦係數的因素均有利於強化咬入和建立穩定軋制過程,通常採用的措施為:
1)減小軋輥咬入角,改善咬入的措施
採用大直徑軋輥,可減小接觸角,並有利於加大壓下量;
減小壓下量,雖可以減小咬入角,但降低壓下量反而要增加軋制道次;
軋件前端做成楔形或圓弧狀,以減小咬入角,可實行大壓下量軋制;
咬入時抬高輥縫以利於咬入,軋制時實行帶負荷壓下增大穩定軋制時的變形量。
2)增大輥面摩擦係數,改善咬入的措施
咬入時輥面不進行潤滑,增大輥面的摩擦;
低速咬入,告訴軋制,也可以增大咬入時的摩擦,改善咬入條件,同時對提高軋制生產效率也有利;
根據金屬摩擦與溫度的關係特性,通過適當改變軋制溫度來增大摩擦,對於大部分金屬,提高軋制溫度由於軋件表面氧化皮的存在,能增大摩擦等。
8、軋制時的金屬流動與變形
軋制時金屬在兩輥縫間發生塑性變形的區域稱為軋制變形區,該區域由軋件與軋輥的接觸弧,軋件進入軋輥垂直斷面和出口垂直斷面所圍成的區域,該區域主要牽涉到一個重要指標就是變形區長度,該長度直接影響著軋制時的金屬的流動。因為主要的變形發生在該區域,所以該區域牽涉到較多的數據,較多的變形。
9、這裡牽扯到另外兩個重要名詞是前滑和后滑,和我們的生產緊密相關
當金屬由軋前厚度H軋至軋后厚度h時,進入變形區的軋件厚度逐漸減薄,根據塑性變形的體積不變條件,則通過變形區內任意橫斷面的秒流量必然相等,則由於軋件越來越薄軋件運動的水平速度從入輥口速度到出輥口速度越來越高,其結果是前滑區軋件的前進速度高於輥麵線速,即軋件相對輥面向前滑動,反之,后滑區軋件的速度低於輥面速度,只有在中性面上二者的速度才相等。
10、軋件斷面上高向的流動和變形
大量的實驗研究和理論分析表明,軋制變形區內的流動和變形是不均勻的,其主要原因是接觸摩擦的影響所致,摩擦越大,水平流速便越不均勻,其中同橫截面上,相鄰不同高度的兩層面上質點間的流速差越大,則變形就越大。另外變形區的形狀係數對軋制斷面高向上的變形分佈情況影響很大,黨軋件相對較薄時,壓縮變形將深透到軋件中心,出現中心層變形比表層大的現象,當軋件相對較厚時,隨著變形區形狀係數的減小,外端對變形過程的影響變得突出,壓縮變形難以深入到軋件中心,只限於表層附近區域發生塑性變形,出現表層的變形比心部大的現象。當厚軋件軋制時,因為接觸摩擦的增高,某些合金的熱軋頭幾道次的變形量較小,加之摩擦大,容易出現粘輥,因而導致軋件頭部張嘴,嚴重時還會纏輥。
11、軋制時金屬除了高向壓縮和沿縱向的延伸外,也存在著沿橫向流動引起的橫向變形,稱之為寬展。根據金屬沿最小阻力方向流動流動的法則,由於摩擦阻力影響的不同,使得金屬沿水平截面的流動可以分為4個區域,如圖所示,變形區可以分為延伸區和寬展區兩部分,在區和區,橫向阻力大於縱向阻力,金屬質點幾乎全朝縱向流動,獲得延伸變形,在區和區,橫向阻力比縱向阻力小得多,金屬質點朝橫向流動產生寬展,可見,寬展主要產生在軋件邊部,而且后滑區比前滑區多。由於摩擦阻力從軋件邊部向中心越來越大,所以越靠近邊部的金屬質點橫向流動的趨勢越大,反之中心部位的金屬質點縱向流動的趨勢越來越大,即中心部位的金屬質點縱向流動快於邊部,這就是為什麼軋件頭部呈扇形,而尾部呈魚尾形的原因,如果中心與邊部流速差所引起邊部的附加拉應力超過了金屬的強度極限,將出現邊部裂紋。寬展其實是一個很複雜的過程,我們目前還沒有一個明確的計算寬展的方法,大多寬展的計算都是根據測量來的數據推斷出來的,要麼就是根據現場實際操作的經驗獲得的,所以這一方面研究的空間很大。
1、熱軋的方式很多,但是我們最常見的也最簡單的就是縱軋,也就是採用順著鑄錠長度方向進行軋制的方式,在軋制過程中主要是軋輥、軋件和乳液的三者之間相互作用的過程,另外還有輥縫外的立輥輥邊軋制、卷取張力控制等。
2、影響軋制的因素
1)軋輥的各項參數,這一因素中影響的主要參數為輥型和表面粗糙度,而這兩個參數的制定要根據實際的經驗才能夠確定出,根據軋機生產工藝要求而定,比如熱軋機的輥面粗糙度的選擇要求既要有利於咬入,防止軋制過程中打滑,也要防止因輥面粗糙而影響產品表面質量。表面粗糙度是指零件加工表面所具有的,較小間距和微小峰谷的微觀集合形狀不平度。雖然定義如此,但是包含著一種用特定的磨削工藝磨削出來的表面狀態。比如,同樣磨削一根粗糙度為1.0的工作輥,用80號的砂輪和用150號的砂輪磨出的效果就大不一樣,其他如不同的磨削液、不同的磨削工藝加工出來的效果也會不一樣。
2)熱軋溫度
這個熱軋溫度包括開軋溫度和終軋溫度,開軋溫度的確定主要是根據合金相圖中固相線溫度的80%左右,而終軋溫度的確定要根據合金的塑性圖確定,一般要求控制在合金的再結晶溫度以上。
3)軋制速度
一般情況下,為了提高生產效率,保證合理的終軋溫度,在設備允許的範圍內盡量採用高速軋制,而在實際的生產中應根據不同的軋制階段確定不同的軋制速度,比如開始軋制階段,平鋪階段,卷取階段等,不同的階段可採用不同的速度進行軋制。
4)熱軋壓下制度
熱軋壓下制度的確定主要包括熱軋總加工率和道次加工率的確定,而熱軋總加工率其確定原則是:
a)合金材料的性質,比如純鋁,高溫塑性範圍較寬,熱軋脆性小,變形抗力低,因而總加工率大,但是硬鋁合金,熱軋溫度範圍窄,熱脆性傾向大,其總加工率通常比軟鋁合金小。
b)滿足最終產品表面質量和性能的要求,比如供給冷軋的坯料,熱軋總加工率應留足冷變形量,以利於控制產品性能和獲得良好的冷軋表面質量。
c)軋機能力及設備條件,軋機最大工作開口度和最小軋制厚度差越大,鑄錠越厚,熱軋總加工率越大,但是鑄錠厚度受軋機開口度和輥道長度的限制。
熱軋道次加工率的確定原則:
制定道次加工率應考慮合金的高溫性能,咬入條件,產品質量要求及設備能力,不同軋制階段道次加工率確定原則是:
a)開始軋制階段,道次加工率較小,一般為2%-10%,因為前幾道次主要是變鑄造組織為加工組織,滿足咬入條件。
b)中間軋制階段,隨金屬加工性能的改善,如果設備條件允許,應該盡量加大道次變形量,對硬鋁合金道次加工率可達到45%以上,軟鋁合金可達50%,大壓下量的軋制將產生大的變形熱,補充帶材在軋制過程中的熱損耗,有利於維持正常軋制。
c)最後軋制階段,一般道次加工率減小,為防止熱軋製品產生粗大晶粒,熱軋最後道次的加工率應大於臨界變形量(15%-20%),熱軋最後兩道次溫度較低,變形抗力較大,其壓下量分配應該保持帶材良好的板形,厚度偏差以及表面質量。
2、用於冷軋、深沖產品。
3、製作汽車、拖拉機、工程起重機械、小型輕工民用機械的衝壓和結構件。
4、製作集裝箱及裸露金屬結構件。
5、焊管、鋼結構。
6、輸送石油天然氣用管線。
7、汽車大梁、橫樑。
8、汽車車輪專用鋼帶。
9、結構用防滑板、樓梯、天梯踏板等。
熱軋系列產品介紹:
產品牌號及標準
種類 | 寶鋼企業標準 | 相當國際標準 | 說明 | ||
標準號 | 牌號 | 標準號 | 牌號 | ||
熱軋低碳鋼 | Q/BQB 302 | SPHC | JIS G3131 | SPHC | 適用於製造冷成型加工的零件。 |
SPHD | SPHD | ||||
SPHE | SPHE | ||||
StW22 | DIN 1614 ( EN10111) | StW22 (DD11) | |||
StW23 | STW23 (DD12) | ||||
StW24 | StW24 (DD13) | ||||
一般結構用鋼 | Q/BQB 303 | SS 330 | JIS G3101 | SS 330 | 用於建築、橋樑、船舶、車輛等一般結構件。 |
SS 400 | SS 400 | ||||
SS 490 | SS 490 | ||||
SS 540 | SS 540 | ||||
St 33 | DIN 17100 ( EN10025) | St 33 (S185) | |||
St 37-2 | St 37-2 (S235JR) | ||||
St 37-3 | St 37-3 (S235JO) | ||||
St 44-2 | St 44-2 (S275JR) | ||||
St 50-2 | St 50-2 (E295) | ||||
St 52-3 | St 52-3 (S355JO) | ||||
焊接結構用鋼 | Q/BQB 303 | SM400A | JIS G3106 | SM400A | 用於建築、橋樑、船舶、車輛、石油罐、工程機械等要求焊接性能優良的結構件。 |
SM400B | SM400B | ||||
SM400C | SM400C | ||||
SM490A | SM490A | ||||
SM490B | SM490B | ||||
SM490C | SM490C | ||||
SM490YA | SM490YA | ||||
SM490YB | SM490YB | ||||
SM520B | SM520B | ||||
SM520C | SM520C | ||||
B520JJ | --- | --- | 混凝土攪拌車筒體用熱連軋鋼板。 | ||
Welten590RE | NSC | Welten590RE | 可焊高強度鋼板,用於壓力容器、油罐、工程機械、採礦機械、壓力水管等。 | ||
B590GJA B590GJB | --- | --- | |||
機械結構用鋼 | Q/BQB 303 | C22 | DIN 17200 | C22 | 用於經切削等加工並熱處理后使用的機械結構件。 |
C35 | JIS G4501 | C35 | |||
S20C | S20C | ||||
S35C | S35C | ||||
細晶粒結構鋼 | --- | StE255 | DIN 17102 | StE255 | 適用於焊接的細晶粒結構鋼。 |
StE355 | StE355 | ||||
鋼管用鋼帶鋼 | Q/BQB 303 | SPHT1 | JIS G3132 | SPHT1 | 用於焊接鋼管。 |
SPHT2 | SPHT2 | ||||
SPHT3 | SPHT3 | ||||
汽車結構用鋼 | Q/BQB 310 BZJ 311 BZJ 312 BZJ 313 BZJ 314 | SAPH 310 | JIS G3113 | SAPH 310 | 用於要求成形性加工性能的汽車構架、車輪等汽車結構件。 |
SAPH 370 | SAPH 370 | ||||
SAPH 400 | SAPH 400 | ||||
SAPH 440 | SAPH 440 | ||||
QStE 340TM | SEW 092 ( EN10149-2) | QStE 340TM (---) | 冷變形用熱軋粒鋼,用於要求良好冷成型性能並有較高或高強度要求的汽車大梁等結構件。 | ||
QStE 380TM | QStE 380TM (---) | ||||
QStE 420TM | QStE 420TM (S420MC) | ||||
QStE 460TM | QStE 460TM (S460MC) | ||||
QStE 500TM | QStE 500TM (S500MC) | ||||
B330CL | --- | --- | 有良好冷成型性能,用於汽車滾型車輪輪網及輪幅。 | ||
B380CL | |||||
B420CL | |||||
B440QZr | --- | --- | 製造汽車傳動軸管用。 | ||
B480QZR | |||||
B320L B550L | --- | --- | 汽車大梁、橫樑用。 | ||
B510L B420L | |||||
B510DL | |||||
鍋爐及壓力容器用鋼 | Q/BQB 320 | HII | DIN 17155 (EN10028-2) | HII (P265GH) | 除保證常溫性能外,還保證較高溫度下的力學性能,適用於蒸汽鍋爐設備,較高工作溫度的壓力容器及類似結構件。 |
19Mn6 | 19Mn6 (P355GH) | ||||
Q/BQB 320 | SB410 | JIS G3103 | SB410 | ||
Q/BQB 321 | B440HP | JIS G3116 | SG295 | 焊接氣瓶用鋼板。 | |
B490HP | SG325 | ||||
船體結構用鋼 | Q/BQB 330 | A | LR,BV | A | 可按各國船級社規範供貨。 |
B | GL,DNV及 | B | |||
D | ABS船規 | D | |||
耐大氣腐蝕鋼 | Q/BQB 340 | WTSt37-2 | SEW087 (EN10155) | WTSt37-2 (S235J2W) | 用於製造集裝箱、鐵道車輛、石油井架、工程機械等要求耐大氣腐蝕的結構件截流和燃料。 |
WTSt52-3 | WTSt52-3 (S355J2G1W) | ||||
NAW 400 | NSC | NAW 400 | |||
NAW 490 | NAW 490 | ||||
B460NQR | --- | --- | |||
B490NQR | |||||
耐硫酸腐蝕鋼 | S-ten2 | NSC | S-ten2 | 用於製造含硫化氫介質的容器等。 | |
耐海水腐蝕鋼 | Mariloy G41A | Mariloy G41A | 用於採油平台、船舶、海港建築等結構構件。 | ||
Mariloy S50A | Mariloy S50A | ||||
高耐候性 結構鋼 | BZJ342 | B480GNQR | --- | --- | 用於製造車輛、集裝、建築及 其它結構件。 |
厚度方向性能熱連軋鋼板 | Q/BQB 350 | Z15 | --- | --- | 鋼板厚度方向性能有良好的抗層狀撕裂性能,用於海上採油平台及其它要求厚度性能的結構件。 |
Z25 | |||||
Z35 | |||||
表面硬化鋼 | Q/BQB 360 | C10 | DIN 17210 | C10 | 高純凈低碳鋼,供進行表面滲碳或滲氮後進行淬火硬化製造表層高硬度、耐磨、芯部具高韌性的結構件。 |
C15 | C15 | ||||
S09CK | JIS G4051 | S09CK | |||
S15CK | S15CK | ||||
高韌性管線鋼 | BZJ 371 | X60RL | API 5L | X60 | 供螺旋焊生產石油輸送管用高韌性管線鋼熱軋寬頻鋼 |
X70RL | X70 | ||||
直縫焊接 套管用鋼 | BZJ 372 | J55 | API 5CT | J55 | 供製造直縫焊石油套管用 |
花紋鋼板 | BZJ 390 | BCP 270 | --- | --- | 扁豆型花紋鋼板 |
BCP 340 | |||||
BCP 400 | |||||
自行車用熱連軋寬頻鋼 | BZJ 304 | SPHT1Z,SPHT2Z | --- | --- | 用於製造自行車上、下、後接頭,前叉肩、前花盤、鏈條滾車把橫管,中軸等零件 |
SPHT3Z,SPHDZ | |||||
SM50BZ,SM53BZ | |||||
管線用 熱連軋卷 | GB 14164 | S205,S240 | API 5L | Grade A,B | 石油、天然氣輸送管用 |
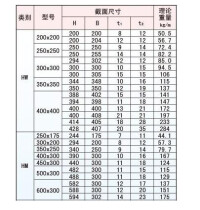
熱軋型鋼
(2)熱軋能改善金屬及合金的加工工藝性能,即將鑄造狀態的粗大晶粒破碎,顯著裂紋癒合,減少或消除鑄造缺陷,將鑄態組織轉變為變形組織,提高合金的加工性能。
(3)熱軋通常採用大鑄錠,大壓下量軋制,不僅提高了生產效率,而且為提高軋制速度、實現軋制過程的連續化和自動化創造了條件。
(1)經過熱軋之後,鋼材內部的非金屬夾雜物(主要是硫化物和氧化物,還有硅酸鹽)被壓成薄片,出現分層(夾層)現象。分層使鋼材沿厚度方向受拉的性能大大惡化,並且有可能在焊縫收縮時出現層間撕裂。焊縫收縮誘發的局部應變時常達到屈服點應變的數倍,比荷載引起的應變大得多。
(2)不均勻冷卻造成的殘餘應力。殘餘應力是在沒有外力作用下內部自相平衡的應力,各種截面的熱軋型鋼都有這類殘餘應力,一般型鋼截面尺寸越大,殘餘應力也越大。殘餘應力雖然是自相平衡的,但對鋼構件在外力作用下的性能還是有一定影響。如對變形、穩定性、抗疲勞等方面都可能產生不利的作用。
(4)熱軋產品厚度尺寸較難控制,控制精度相對較差;熱軋製品的表面較冷軋製品粗糙Ra值一般在0.5~1.5μm。因此,熱軋產品一般多作為冷軋加工的坯料。