薄鋼板
厚度在0.2~4mm之間的鋼板
薄鋼板是用熱軋或 冷軋方法生產的厚度在0.2~4mm之間的鋼板。薄鋼板的寬度在500 ~2500mm之間。根據不同的用途,薄鋼板有不同的材質:普通碳素鋼、優質碳素結構鋼、合金結構鋼、碳素工具鋼、不鏽鋼、彈簧鋼、電工用硅鋼等等。它們主要用於汽車工業、航空工業、搪瓷工業、電氣工業、機械工業等部門。薄鋼板有軋后直接交 貨的,還有經過酸洗的(酸洗薄鋼板)、鍍鋅或鍍錫的。
根據變形機理的不同,沖裁可以分為普通沖裁和精密沖裁兩類。
塑性彎曲乃是壓製成形工序中最為普遍的成形方法之一。彎曲成形的效果,表現為彎曲變形區曲率半徑R和角度x的變化(圖1)
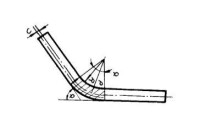
圖1
彈性彎曲時,切嚮應力為所以材料的變形程度與應力大小,完全取決於纖維至中性層的距離與中性層半徑的比值,而與彎曲角度α的大小無關。在彎曲變形區的內、外邊緣,應力應變最大。
對於厚度為t值的板料,當其彎曲半徑為R時,板料邊緣的應力與應變為
假定材料的屈服應力為,則彈性彎曲的條件是:
亦即
當 時,彎曲即開始由表及裡逐步進入塑性,變形。
拉深成型,是把平板凸緣拉入凹模孔內而形成直壁的加工方法。
凸緣的流入,隨著凹模孔輪廓形狀的變形狀態的不同,可分(a)壓縮凸緣流入、(b)平行凸緣流入、(c)伸長凸緣流入三類,(圖2)。
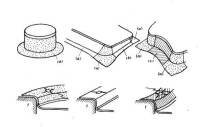
圖2
大批量生產中使用最多的就是冷軋鋼板。冷軋薄鋼板的厚度在0.15~3.2mm之間,汽車車身多採用0.6~0.8mm的薄板。這種薄鋼板尺寸精度非常高,表面光滑,具有良好的力學性能和加工性,主要用於車身側圍板、頂蓋、發動機蓋、翼子板、行李箱蓋、車門板和儀錶板等外覆蓋件,這些零件要求材料具有高的成形性能、良好的表面質量和焊接性能。
在無間隙原子鋼板(IF鋼)使用以前,汽車覆蓋件都用低碳沸騰鋼板(08F)和鋁鎮靜鋼(08AL)沖制。沸騰鋼由於衝壓成形性能差和容易失效等缺陷現已較少使用。而鋁鎮靜鋼板仍作為衝壓用鋼板大量應用,特別是對於成形要求不高的車身零件,採用鋁鎮靜鋼板仍然佔多數。
(1)鋁鎮靜鋼板(08AL)
a.碳。碳在一般鋼材中是主要元素,但是在深沖薄板中,它卻是有害元素。鋼中碳的質量分數增加,會使低碳鋼的強度提高而使成形性能降低。因此,我國的GB/T5213-2001中規定深衝壓用鋼的碳質量分數應低於0.08%。
b.錳。錳質量分數高時,使鋼板的強度升高,所以一般鋁鎮靜鋼的錳質量分數應低於0.4%。
c.硫。硫質量分數對薄鋼板的衝壓性能有不利影響,因此其質量分數越低越好。一般08AL鋼板規定的硫質量分數應低於0.025%。
e.硅。硅的作用主要是提高鋼板強度,但會惡化衝壓性能,所以其質量分數越低越好,硅質量分數應低於0. 030%。
f.鋁。鋁加入衝壓用冷軋鋼板中提高其衝壓性能,所以08AL規定鋁質量分數應在0. 02%~0.07%之間。
08AL鋼板屬於低碳鋼,有較好的塑性,合適的強度,具有一定的時效性,在3~6個月內使用時,不能破壞其衝壓性能。
鋁鎮靜鋼結相組織簡單,一般由鐵素體、遊離碳化鐵和少量非金屬夾雜物組成,遊離的碳化鐵和非金屬夾雜物對鋼板的衝壓性能影響很大,其中以方形夾雜物影響最大,圓形點狀夾雜物影響最小,在衝壓過程中會引起製件開裂。
鐵素體晶粒的大小和晶粒的均勻性對衝壓性能影響也很大,晶粒過小,強度升高而塑性降低,對衝壓性能不利;晶粒過大,衝壓后零件的表面差,會出現桔皮狀表面,晶粒度以7~8級最為理想。若晶粒不均勻,會引起零件整個變形的不均勻性,從而導致開裂。
在沖制複雜零件時,因零件各部位的變形量不同,會在零件表面出現滑移線,嚴重地降低零件的表面質量,這對於汽車的覆蓋件,這種現象是不允許出現的。一般要進行調質軋制處理,消除衝壓中出現的滑移現象。
綜上所述,08AL鋼板適合衝壓強度、表面質量要求不高的、變形均勻的一般零件。而對於深沖件和複雜零件,要慎用。
(2)無間隙原子鋼板(IF鋼板)汽車車身由衝壓件焊接組成。轎車車身的形狀為了減少空氣阻力和外形美觀而日趨複雜,對鋼板的衝壓性能要求日益提高,因此對影響衝壓成形性能的指標有一定要求,如高的塑性應變比、適當的應變硬化指數、高的伸長率、低的屈服強度,只有符合上述要求的鋼板才能衝出形狀複雜的零件。
以普通沸騰鋼為代表的第一代冷軋鋼板和以鋁鎮靜鋼為代表的第二代冷軋鋼板都難以完全滿足現代轎車衝壓件的要求。已能大規模生產的第三代冷軋無間隙原子鋼(IF鋼板)能滿足上述要求,由IF鋼衍生出的新型鋼板如IFBH鋼、IF高強度鋼、IF鍍層鋼等,再加上雙相鋼(DP鋼)和塑性變形誘導相變鋼(TRIP鋼),使汽車用冷軋鋼板達到了新的水平,基本上滿足了轎車生產的需要。
在低碳鋼中加入足夠數量的鈦后,鋼中的碳、氮間隙原子就完全被鈦固定,形成鈦碳化合物,此時鋼就成為無間隙原子鋼而具有優異的成形性能。因鈦價格昂貴,鋼的生產成本太高,因此無法大批量生產。20世紀60年代後期,真空脫氣技術的成功應用,使得鋼中的碳、氮含量大幅度降低,而減少了鈦的用量,從而降低了IF鋼的生產成本。到了70年代,鋼板生產採用連續退火機組,大大降低了生產成本,又出現了加鈮及複合添加鈦和鈮的IF鋼,擴大了IF鋼的生產和應用。
①IF鋼的化學成分。鋼的化學成分是其性能的基礎,對IF鋼而言,首先是降低對成形性能有害的碳和氮的質量分數,同時加入鈦和鈮。
IF鋼中碳、硅等元素的作用同08A1鋼,鈦和鈮是IF鋼中的重要元素,通過鈦和鈮的處理使固溶體中的間隙原子碳和氮得以清除,從而清除間隙原子的不利影響。工業生產中的超低碳鋼若不經過加鈦和鈮的處理消除間隙原子,其塑性應變比不高,成形性能不好。
工業生產的IF鋼有三種,即單一加Ti的Ti-IF鋼、單一加Nb的Nb-IF鋼和同時加Ti和Nb的複合Ti-Nb-IF鋼。
上述三種IF鋼的特點如下:
a.Ti-IF鋼。就工藝參數而言,低的加熱溫度、高的卷取溫度、高的退火溫度和大的冷軋壓下率有利於Ti-IF鋼成形性能的提高。合金成分對Ti-IF鋼延伸率的影響沒有Nb-IF鋼敏感,一般鈦穩定鋼延伸率較高。高的卷取溫度和退火溫度會得到粗大的TiC顆粒,因此強度級別低。對Ti-IF鋼性能產生重要影響的TiS和Ti4C2S2等析出物一般在加熱過程和熱軋初始階段就開始析出,所以工藝參數對Ti-IF鋼影響不是很敏感,工藝過程的可操作性強,性能穩定。但是這種成分體系的鋼平面各向異性大而且鍍層抗粉化能力較差,不適用於鍍鋅板。
b.Nb-IF鋼。與Ti-IF鋼相比,由於細小NbC粒子析出,可以提高鋼的強度,故Nb-IF鋼具更高的強度水平。Nb的添加,改善鋼的織組結構,各向異性值降低,提高了塑性應變比(r)平均值;Nb偏析到晶界,可防止冷加工脆性,提高可鍍性和抗粉化性能。但由於Nb-IF鋼的析出過程發生在熱軋冷卻階段或退火階段,力學性能對工藝參數比較敏感,而且Nb-IF鋼有較高的再結晶溫度,其力學性能不如Ti-IF鋼好。
c.( Nb +Ti) -IF鋼。鈮鈦穩定的IF鋼延伸率比Ti-IF鋼低,但r。值和r45 0值都比較高,具有較強的可成形性。鈮鈦穩定的IF鋼比鈦穩定鋼具有較好的塗層粘附性,具有良好的合金化及熱鍍鋅鋼板抗粉化,而且力學性能對工藝不敏感,整卷性能均勻,適合於在連續退火工藝下生產高強鋼及熱鍍鋅鋼,也是電鍍鋅IF鋼和熱鍍鋅IF鋼基板的最佳選擇。
②IF鋼板的特點。與廣泛使用的鋁鎮靜低碳深沖鋼比,IF鋼板在性能上最明顯的特點是優秀的成形性能和永不時效性。
a.優秀的成形性。
b.無時效性。一般鋼板都具有時效性。所謂時效性就是鋼板的屈服應力和延伸率隨時間的推移而變化,經過一段時間后鋼板的拉延性能曲線上會出現明顯的屈服平台,此時鋼板的成形性能下降。鋼板的這種時效性是由於鋼板中存在著碳、氮等間隙固溶原子造成的。儘管深沖鋼板使用了鋁鎮靜,其時效性已經不明顯了,但它的存在仍是一個客觀事實。所以,還仍然有這樣的規定,即軋制后的深沖鋼板的時效期為個3月,也就是說,軋制后的深沖鋼板必須在3個月內用完,否則成形性就會下降。
③IF鋼板的應用。由於IF鋼板具有優秀的成形性能和獨特的不時效性,所以在汽車工業特別是轎車工業中得到了廣泛的應用。其應用概括起來,有以下幾個方面。
a.用於形狀複雜的衝壓件。有些衝壓件形狀複雜,拉延較大,即使使用最好的鋁鎮靜深沖鋼也難以完全滿足要求。例如發動機的油底殼對鋼板的拉延性要求很高,過去一直使用進口的深拉延級鋼板,但效果不太理想。自從使用了國產的深沖IF鋼板之後,這個問題便迎刃而解。用國產Ⅲ鋼板取代進口的深沖鋼板生產一些形狀比較複雜的衝壓件,效果很好,值得進一步推廣。
b.用於製造高強度的汽車車身覆蓋件。為了節約能量和滿足日益嚴格的環保要求,高強度鋼板正在汽車工業中得到廣泛的應用。例如,轎車車身的許多外覆蓋件在原設計中就廣泛地採用了高強度鋼板,降低了鋼板的厚度,從而降低了車身的質量,降低了汽車燃油消耗,也降低了汽車的有害排放。
IF鋼板具有非常優秀的成形性。在此基礎上通過固溶強化等方式開發出來的高強度IF鋼板在獲得了較高強度的同時仍然保留著較高的成形性。
在強度級別相同的情況下,高強度IF鋼板的成形性指標的綜合水平要明顯優於傳統使用的高強度鋼板,加上這種IF鋼板不具有時效性,衝壓過程中不會在表面上出現影響板件外觀質量的滑移線,所以用這種鋼板生產汽車外覆蓋件非常適宜。
c.作為高性能鍍鋅鋼板的基板。鍍鋅鋼板在汽車上的應用越來越廣,如奧迪等歐洲車型和北美的一些車型中甚至整個車身都是用鍍鋅鋼板製成的。鍍鋅鋼板得到廣泛應用的原因一是北歐和北美等氣候寒冷的國家,冬日雪後路面噴灑鹽水對車身件腐蝕嚴重,二是為了提高汽車使用壽命,各國對汽車板材不發生鏽蝕的年限一再延長,一般裸鋼板不能滿足這些要求,所以鍍鋅鋼板受到了重視。
一般都採用深沖鋼板作為基板生產鍍鋅板,由於熱鍍鋅時需要加熱到500C左右的高溫,基板因發生嚴重時效而使成形性變壞,從而使鍍鋅板的應用產生了局限性,不能用於比較複雜的衝壓件。IF鋼板的問世成功地解決了這個問題。由於IF鋼板本身具有很高的成形性,加之沒有時效性,所以在熱浸鍍鋅后仍能保持著很好的成形性。表3.7是兩種以職鋼板為基板生產出來的鋼板的實測性能,我們從中可以看出這兩種鋼板基本上保持了它原板的特點,具有很好的成形性。
另外,由於用鈦作為微合金化的IF鋼板平面上各向異性較大,以此種鋼板為基板生產出來的鍍鋅鋼板在衝壓過程中,有可能因鋼板各個方向的應變程度不同而發生粉化。以鈮為微合金化元素時,情況要好得多,所以在實際生產中一般使用添加Nb或者Ti +Nb的IF鋼板作為鍍鋅板的原板。
為控制導致全球變暖的排放,汽車製造商以降低燃料消耗為目的,積極推進汽車車身輕量化的設計。20世紀90年代初,汽車車身使用高強鋼板的比例增加到30%,減輕了車重。90年代後期,出於碰撞安全性考慮,汽車車身增加了加強件的使用量,從而增加了車重。為確保車身碰撞安全性和輕量化,用於汽車車身的高強鋼板強度從440MPa級提高到590MPa級,車身結構件使用980MPa級超高強鋼板,使用比例也在40%以上。從提高車身緩蝕性能來看,合金化熱鍍鋅鋼板具有與冷軋鋼板相同的高強度特性。
汽車用高強度冷軋鋼板主要用於車身零部件,大致分為3類,即內外面板、結構件和加強件。表3-8列出了每一部件要求的鋼板強度和特性及需解決的問題。