鍛壓機床
金屬和機械冷加工用的設備
公元前二千多年出現的樹木車床是機床最早的雛形。工作時,腳踏繩索下端的套圈,利用樹枝的彈性使工件由繩索帶動旋轉,手拿貝殼或石片等作為刀具,沿板條移動工具切削工件。中世紀的彈性桿棒車床運用的仍是這一原理。
十五世紀由於製造鐘錶和武器的需要,出現了鐘錶匠用的螺紋車床和齒輪加工機床,以及水力驅動的炮筒鏜床。1500年左右,義大利人列奧納多·達芬奇曾繪製過車床、鏜床、螺紋加工機床和內圓磨床的構想草圖,其中已有曲柄、飛輪、項尖和軸承等新機構。中國明朝出版的《天工開物》中也載有磨床的結構,用腳踏的方法使鐵盤旋轉,加上沙子和水剖切玉石。
十八世紀的工業革命推動了機床的發展。1774年,英國人威爾金森發明了較精密的炮筒鏜床。次年,他用這台炮筒鏜床鏜出的汽缸,滿足了瓦特蒸汽機的要求。為了鏜制更大的汽缸,他又於1776年製造了一台水輪驅動的汽缸鏜床,促進了蒸汽機的發展。從此,機床開始用蒸汽機通過天軸驅動。
1797年,英國人莫茲利創製成的車床由絲杠傳動刀架,能實現機動進給和車削螺紋,這是機床結構的一次重大變革。莫茲利也因此被稱為“英國機床工業之父”。
19世紀,由於紡織、動力、交通運輸機械和軍火生產的推動,各種類型的機床相繼出現。1817年,英國人羅伯茨創製龍門刨床;1818年美國人惠特尼製成卧式銑床;1876年,美國製成萬能外圓磨床;1835和1897年又先後發明滾齒機和插齒機。
隨著電動機的發明,機床開始先採用電動機集中驅動,后又廣泛使用單獨電動機驅動。二十世紀初,為了加工精度更高的工件、夾具和螺紋加工工具,相繼創製出坐標鏜床和螺紋磨床。同時為了適應汽車和軸承等工業大量生產的需要,又研製出各種自動機床、仿形機床、組合機床和自動生產線。
隨著電子技術的發展,美國於1952年研製成第一台數字控制機床;1958年研製成能自動更換刀具,以進行多工序加工的加工中心。從此,隨著電子技術和計算機技術的發展和應用,使機床在驅動方式、控制系統和結構功能等方面都發生顯著的變革。
輥鍛式鍛壓機床
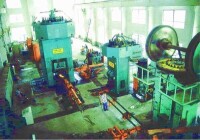
輥鍛式鍛壓機床
機械壓力式鍛壓機床
機械壓力鍛壓機床通過曲柄滑塊機構將電動機的旋轉運動轉換為滑塊的直線往複運動,對坯料進行成形加工的鍛壓機械。機械壓力機動作平穩,工作可靠,廣泛用於衝壓、擠壓、模鍛和粉末冶金等工藝。機械壓力機在數量上約佔各類鍛壓機械總數的一半以上。機械壓力機的規格用公稱工作力(千牛)表示,它是以滑塊運動到距行程的下止點約10~15毫米處(或從下止點算起曲柄轉角約為15°~30°時)為計算基點設計的最大工作力。
擠壓式鍛壓機床
熱擠壓鍛壓機床廣泛用於生產鋁、銅等有色金屬的管材和型材等,屬於冶金工業範圍。鋼的熱擠壓既用以生產特殊的管材和型材,也用以生產難以用冷擠壓或溫擠壓成形的實心和孔心(通孔或不通孔)的碳鋼和合金鋼零件,如具有粗大頭部的桿件、炮筒、容器等。冷擠壓鍛壓機床原來只用於生產鉛、鋅、錫、鋁、銅等的管材、型材,以及牙膏軟管(外麵包錫的鉛)、乾電池殼(鋅)、彈殼(銅)等製件。冷擠壓操作簡單,適用於大批量生產的較小製件。
螺旋式鍛壓機床
螺旋式鍛壓機床用螺桿、螺母作為傳動機構,並靠螺旋傳動將飛輪的正反向迴轉運動轉變為滑塊的上下往複運動的鍛壓機械。螺旋壓力機通常由電動機通過摩擦盤帶動飛輪輪緣而使飛輪旋轉,所以這種壓力機又稱摩擦壓力機,中國最大的摩擦壓力機為25兆牛。後來又出現用電機直接驅動飛輪的電動螺旋壓力機,它的結構緊湊,傳動環節少,由於換向頻繁,對控制電器要求較高,並需要特殊電機。
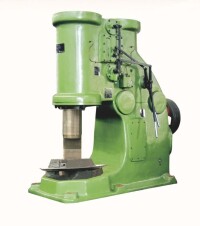
空氣錘
在鍛壓機床功能部件中,以其開發、生產和使用的成熟性而論,當首推機床壓力機用摩擦離合器-制動器。摩擦離合器-制動器是機床壓力機主傳動的重要部件,其性能優劣直接影響整機的使用性、安全性、可靠性以及設備的開動率和維修量。按摩擦離合器-制動器的結構形式分,有組合式摩擦離合器-制動器和分離式摩擦離合器-制動器;按摩擦副的工作狀態分,有乾式摩擦離合器-制動器和濕式摩擦離合器-制動器;按摩擦離合器-制動器的操縱系統分,有氣動摩擦離合器-制動器和液壓摩擦離合器-制動器。
光電安全保護裝置,在鍛壓機床的操作者與危險工作區之間的保護區域設置不可見紅外線光幕,一旦操作者某部位進入保護區遮斷光幕,控制系統則輸出信號至鍛壓機床安全執行機構,令鍛壓機床緊急停車,防止危險動作發生。可見,光電安全保護裝置自身並不能直接保護操作者,它僅僅是在可能發生安全事故之前,給機床發出停止危險動作的信號。因此,嚴格而言,光電安全保護裝置應稱為光電安全保護控制裝置。
光電安全保護裝置通常分為反射式與對射式兩種。反射式光電安全保護裝置由控制器、感測器和反射器3部分組成,光幕由感測器發出,經反射器再反射回感測器予以接收;對射式光電安全保護裝置由控制器、發射感測器和接收感測器3部分組成,光幕由發射感測器發出,由接收感測器予以接收。
凸輪控制器是機床壓力機電氣控制系統的重要組成部分。處理工作機構邏輯關係的方法,通常是將曲軸旋轉一周的360°進行分配,制定出機床壓力機的工作循環圖,對各工作機構的動作予以控制。凸輪控制器就是對曲軸旋轉角度進行分配的執行機構。凸輪控制器被安裝在與曲軸同步旋轉的軸上,工作機構依次產生規定的動作,完成機床壓力機的一個工作循環。國內有多家生產凸輪控制器的專業廠,產品質量一般都穩定可靠,主機廠辨取定向辨購的方式進行配套。
在鍛壓機床中有形形色色的自動送料裝置,此處指用於開式壓力機、閉式壓力機、多工位壓力機、高速壓力機等單機或衝壓自動線進行板料加工的自動送料裝置。自動送料裝置一般由料架及開卷校平機構、氣動鉗式送料機構、廢料收卷料架等3部分組成。料架及開卷校平機構有支撐卷料、開卷和校平3個功能,開卷機構將卷料少許鬆開並呈自由懸垂狀態,以減小送料機構在送料過程的拉力,有利於提高送料精度;校平機構以多滾輪對開卷后的卷料施力,使板材在衝壓前得到矯正,有利於提高製品精度。氣動鉗式送料機構以壓縮空氣為動力,控制夾鉗的開合與往複運動完成板料的送進,往複運動的行程無級可調以適應不同送料長度的要求。廢料收卷料架將衝壓后的廢帶料收卷,若衝壓時將廢帶料切斷回收,則不需要這一部分。
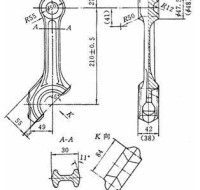
鍛壓機床工作原理
輥鍛變形的實質是坯料的軋制延伸,坯料部分截面變小而長度增加。當截面變形較大時,需要由幾道孔型經多次輥軋完成。其工藝設計主要是合理的決定各工步輥鍛的壓下量、展寬量和延伸變形量。它們取決於輥徑的大小、孔型的形狀尺寸、毛坯的溫度和冷卻潤滑等變形條件。有的雙支承輥鍛機在一端有輥軸伸出,這是懸臂式和雙支承式結合的複合型輥鍛機,它既能實現縱向輥鍛又能在懸臂端完成橫向展寬成形。在大批量輥鍛生產中,廣泛採用機械手傳送工件,實現生產過程的自動化,提高生產率,減輕勞動強度。
用凸模對放置在凹模中的坯料加壓,使之產生塑性流動,從而獲得相應於模具的型孔或凹凸模形狀的製件的鍛壓方法。擠壓時,坯料產生三向壓應力,即使是塑性較低的坯料,也可被擠壓成形。擠壓,特別是冷擠壓,材料利用率高,材料的組織和機械性能得到改善,操作簡單,生產率高,可製作長桿、深孔、薄壁、異型斷面零件,是重要的少無切削加工工藝。擠壓主要用於金屬的成形,也可用於塑料、橡膠、石墨和黏土坯料等非金屬的成形。
每個曲柄滑塊機構稱為一個“點”。最簡單的機械壓力機採用單點式,即只有一個曲柄滑塊機構。有的大工作面機械壓力機,為使滑塊底面受力均勻和運動平穩而採用雙點或四點的。
機械壓力機的載荷是衝擊性的,即在一個工作周期內鍛壓工作的時間很短。短時的最大功率比平均功率大十幾倍以上,因此在傳動系統中都設置有飛輪。按平均功率選用的電動機啟動后,飛輪運轉至額定轉速,積蓄動能。凸模接觸坯料開始鍛壓工作后,電動機的驅動功率小於載荷,轉速降低,飛輪釋放出積蓄的動能進行補償。鍛壓工作完成後,飛輪再次加速積蓄動能,以備下次使用。
機械壓力機上的離合器與制動器之間設有機械或電氣連鎖,以保證離合器接合前制動器一定鬆開,制動器制動前離合器一定脫開。機械壓力機的操作分為連續、單次行程和寸動(微動),大多數是通過控制離合器和制動器來實現的。滑塊的行程長度不變,但其底面與工作面之間的距離(稱為封密高度),可以通過螺桿調節。
生產中,有可能發生超過壓力機公稱工作力的現象。為保證設備安全,常在壓力機上裝設過載保護裝置。為了保證操作者人身安,壓力機上面裝有光電式或雙手操作式人身保護裝置。
1、操作者必須經過考試合格,並持有本設備的《設備操作證》方可操作本設備。
2、工作前認真做到:
(1)仔細閱讀交班記錄,了解上一班工作情況。
(2)檢查設備及工作場地是否清掃、擦試乾淨;設備床身、工作檯面、導軌以及其它主要滑動面上不得有障礙物、雜質和新的拉、研、碰傷。如有上述情況必須清除,並擦試乾淨設備;出現新的拉、研、碰傷應請設備員或班組長一起查看,並作好記錄。
(5)檢查潤滑部位(油池、油箱、油杯導軌以及其他滑動面)油量應充足,並按潤滑批示圖表加油。
(6)檢查各主要零、部件以及緊固件有無異常鬆動現象。
(8)進行空運轉試車,起動要寸動,檢查各操作裝置、安全保險裝置(制動、換向、聯鎖、限位、保險等)各指示裝置(指示儀錶、指示燈等)工作應靈敏、準確可靠;各部位動作應協調;供油應正常,潤滑應良好;機床運轉無異常聲音、振動、溫升、氣味、煙霧等現象。確認一切正常,方可開始工作。凡連班工作的設備,交班人員根據上述(8條)規定共同檢查進行交接班;凡隔班接班的設備,發現上一班有嚴重違犯操作規程現象,應請設備員或班組長一直查看,並記錄在案,否則發生設備問題以本班違犯操作規程論。設備經過調整或檢修后,操作者也必須按照上述(8條)要求和步驟對設備進行檢查,確認一切無誤,方可開始工作。
3、工作中認真做到:
(1)堅守工作崗位,精心操作設備,不做與工作無關的事。因事離開設備時要停機,並關閉電、氣(汽)源。
(2)按說明書規定的技術規範使用設備,不得超規範、超負荷使用設備。
(3)密切注意設備各部位潤滑情況,按潤滑指示圖表規定進行班中加油,保證設備各部位潤滑良好。
(4)密切注意設備各部位工作情況,如有不正常聲音、振動、溫升、異味、煙霧、動作不協調,失靈等現象,應立即停機檢查,排除后再繼續工作。
(5)調速、更換模具、刀具或擦試,檢修設備時,要事先停機,關閉電、氣(汽)源。
(6)在工作時,不得擅自拆卸安全防護裝置和打開配電箱(盒)、油池(箱)、變速箱的門蓋進行工作。
(7)設備發生事故必須立即停機,保護好現場,報告有關部門分析處理。
4、工作后認真做到:
(1)各操作裝置以及滑塊、榔頭、刀架等應按說明書規定放在非工作位置上;關閉電、氣(汽)源。
(2)整理工具、零件和工作場地。
(3)清掃工作場地和設備上的料頭、料邊、氧化皮、雜物等;擦試乾淨設備各部位,各滑動面加油保護。
(4)填寫交接班錄。
外部整體檢查
徹底清理鍛壓機床外部,檢查所有緊固螺釘是否鬆動,各零部件是否安全,有無開焊、裂紋或變形現象。機身上應有安全警告標誌,長度應不小於30厘米。
試運轉的檢查
鍛壓機床轉動后,檢查有無漏風現象,同時檢查機器有無異常振動,按要求進行全面潤滑。仔細觀察是否有碰撞、磨擦和卡滯現象。有無異常聲音。用動力機械帶動低速運轉,觀察各部分的運轉狀況。
輸入裝置的檢查
輸送鏈必須逐節檢查,如發現磨損嚴重、變形、裂紋應予更換。喂入鏈的緊張度應左右一致,以其鏈長的中部稍接觸底板為宜,輸送鏈的主、被動軸應平行,如傾斜,應查找原因予以排除。
離合裝置的檢查
安全離合器要在工作使用過程中進行調整,檢查波型齒的磨損程度,如齒高磨去1/3時應更換。
鍛壓部位檢查與調整