衝壓加工
產品零件的生產技術
衝壓加工是藉助於常規或專用衝壓設備的動力,使板料在模具里直接受到變形力並進行變形,從而獲得一定形狀,尺寸和性能的產品零件的生產技術。板料,模具和設備是衝壓加工的三要素。衝壓加工是一種金屬冷變形加工方法。所以,被稱之為冷衝壓或板料衝壓,簡稱衝壓。它是金屬塑性加工(或壓力加工)的主要方法之一,也隸屬於材料成型工程技術。
生產中為滿足衝壓零件形狀、尺寸、精度、批量、原材料性能等方面的要求,採用多種多樣的衝壓加工方法。概括起來衝壓加工可以分為分離工序與成形工序兩大類。
是在衝壓過程中使衝壓件與板料沿一定的輪廓線相互分離的工序。如下表所示:
工序名稱 | 簡 圖 | 工序特徵 | 應用範圍 |
落料 | 用模具沿封閉線沖切板料,衝下的部分為工件。 | 用於製造各種形狀的平板零件 | |
沖孔 | 用模具沿封閉線沖切板料,衝下的部分為廢料。 | 用於沖平板件或成形件上的孔 | |
切斷 | 用剪刀或模具切斷板料,切斷線不是封閉的。 | 多用於加工形狀簡單的平板零件 | |
切邊 | 用模具將工件邊緣多餘的材料沖切下來。 | 主要用於立體成形件 | |
沖槽 | 在板料上或成形件上沖切出窄而長的槽 | ||
剖切 | 把衝壓加工成的半成品切開成為兩個或數個零件。 | 多用於不對稱的成雙或成組衝壓之後 |
是毛坯在不被破壞的條件下產生塑性變形,形成所要求的形狀和尺寸精度的製件。如下表所示:
工序名稱 | 簡 圖 | 工序特徵 |
彎曲 | 用模具將板料彎曲成一定角度的零件,或將已彎件再彎。 | |
拉深 | 用模具將板料壓成任意形狀的空心件,或將空心件作進一步變形 | |
翻邊 | 用模具將板料上的孔或外緣翻成直壁 | |
脹形 | 用模具對空心件施加向外的徑向力,使局部直徑擴張。 | |
縮口 | 用模具對空心件口部施加由外向內的徑向壓力,使局部直徑縮小。 | |
擠壓 | 把毛坯放在模腔內,加壓使其從模具空隙中擠出,以成形空心或實心零件。 | |
卷圓 | 把板料端部捲成接近封閉的圓頭,用以加工類似鉸鏈的零件。 | |
擴口 | 在空心毛坯或管狀毛坯的某個部位上使其徑向尺寸擴大的變形方法。 | |
校形 | 將工件不平的表面壓平;將已彎曲或拉深的工件壓成正確的形狀 |
衝壓所使用的模具稱為衝壓模具,簡稱沖模。沖模是將材料(金屬或非金屬)批量加工成所需沖件的專用工具。沖模在衝壓中至關重要,沒有符合要求的沖模,批量衝壓生產就難以進行;沒有先進的沖模,先進的衝壓工藝就無法實現。衝壓工藝與模具、衝壓設備和衝壓材料構成衝壓加工的三要素,只有它們相互結合才能得出衝壓件。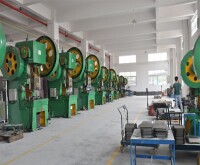
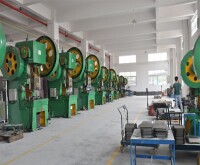
衝壓加工
(1)設計的衝壓件必須滿足產品使用和技術性能,並能便於組裝及修配。
(2)設計的衝壓件必須有利於提高金屬材料的利用率,減少材料的品種和規格,儘可能降低材料的消耗。在允許的情況下採用價格低廉的材料,儘可能使零件做到無廢料及少廢料沖裁。
(3)設計的衝壓件必須形狀簡單,結構合理,以有利於簡化模具結構、簡化工序數量,即用最少、最簡單的衝壓工序完成整個零件的加工,減少再用其他方法加工,並有利於衝壓操作,便於組織實現機械化與自動化生產,以提高勞動生產率。
(5)設計的衝壓件,應有利於儘可能使用現有設備、工藝裝備和工藝流程對其進行加工,並有利於沖模使用壽命的延長。
與機械加工及塑性加工的其它方法相比,衝壓加工無論在技術方面還是經濟方面都具有許多獨特的優點。主要表現如下。
(1)衝壓加工的生產效率高,且操作方便,易於實現機械化與自動化。這是因為衝壓是依靠沖模和衝壓設備來完成加工,普通壓力機的行程次數為每分鐘可達幾十次,高速壓力要每分鐘可達數百次甚至千次以上,而且每次衝壓行程就可能得到一個沖件。
(2)衝壓時由於模具保證了衝壓件的尺寸與形狀精度,且一般不破壞衝壓件的表面質量,而模具的壽命一般較長,所以衝壓的質量穩定,互換性好,具有“一模一樣”的特徵。
(3)衝壓可加工出尺寸範圍較大、形狀較複雜的零件,如小到鐘錶的秒錶,大到汽車縱梁、覆蓋件等,加上衝壓時材料的冷變形硬化效應,衝壓的強度和剛度均較高。
(4)衝壓一般沒有切屑碎料生成,材料的消耗較少,且不需其它加熱設備,因而是一種省料,節能的加工方法,衝壓件的成本較低。
最新技術
複合衝壓
本文所涉及的複合衝壓,並不是指落料、拉伸、沖孔等衝壓工序的複合,而是指衝壓工藝同其他加工工藝的複合,譬如說衝壓與電磁成形的複合,衝壓與冷鍛的結合,衝壓與機械加工複合等。
衝壓與電磁成形的複合工藝
電磁成形是高速成形,而高速成形不但可使鋁合金成形範圍得到擴展,並且還可以使其成形性能得到提高。用複合衝壓的方法成形鋁合金覆蓋件的具體方法是:用一套凸凹模在鋁合金覆蓋件尖角處和難成形的輪廓處裝上電磁線圈,用電磁方法予以成形,再用一對模具在壓力機上成形覆蓋件易成形的部分,然後將預成形件再用電磁線圈進行高速變形來完最終成形。事實證明,用這樣複合成形方法可以獲得用單一衝壓方法難以得到的鋁合金覆蓋件。
最新研究表明鎂合金是一種比強度高、剛度好、電磁界面防護性能強的金屬,其在電子、汽車等行業中應用前景十分看好,大有取代傳統的鐵合金、鋁合金、甚至塑膠材料的趨勢。目前汽車上採用的鎂合金製件有儀錶底板、座椅架、發動機蓋等,鎂合金管類件還廣泛應用於飛機、導彈和宇宙飛船等尖端工業領域。但鎂合金的密排六方晶格結構決定了其在常溫下無法衝壓成形。現在人們研製了一種集加熱與成形一起的模具來衝壓成形鎂合金產品。該產品成形過程為:在沖床滑塊下降過程中,上模與下模夾緊對材料進行加熱,然後再以適當運動模式進行成形。
此種方法也適用於在沖床內進行成形品的聯結及各種產品的複合成形。許多難成形的材料,例如鎂合金、鈦合金等產品,都可用該種方法衝壓成形。由於這種衝壓要求沖床滑塊在下降過程中具有停頓的功能,以便對材料加熱提供時間,故人們研製一種全新概念的沖床———數控曲軸式伺服馬達沖床,利用該沖床還可在衝壓模具內實現包括攻螺紋、鉚接等工序的複合加工,從而有力地拓展了衝壓加工範圍,為鎂合金在塑性加工業廣泛應用奠定了堅實的基礎。
衝壓與冷鍛的結合
一般板料衝壓僅能成形等壁厚的零件,用變薄拉伸的方法最多能獲得厚底薄壁零件,衝壓成形局限性限制了其應用範圍。而在汽車零件生產中常遇到一些薄壁但卻不等厚的零件,用單一的衝壓與冷鍛相結合的複合塑性成形方法加以成形,顯得很容易,因此,用衝壓與冷鍛相結合的方法就能擴展板料加工範圍。其方法是先用衝壓方法預成形,再用冷鍛方法終成形。用衝壓冷鍛複合塑性成形,其優點為:一是原材料容易廉價採購,可以降低生產成本;二是降低單一冷鍛所需的大成形力,有利於提高模具壽命。
現在所談論的微細加工指的是微零件加工技術。微零件的界定通常指的是至少有某一方向的尺寸小於100μm,它比常規的製造技術有著無可比擬的應用前景。用該技術製作的微型機器人、微型飛機、微型衛星、衛星陀螺、微型泵、微型儀器儀錶、微型感測器、集成電路等等,在現代科學技術許多領都有著出色的應用,他能給許多領域帶來新的拓展和突破,無疑將對中國未來的科技和國防事業有著深遠的影響,對世界科技發展的推動作用也是難以估量的。譬如微型機器人可完成光導纖維的引線、粘接、對接等複雜操作和細小管道、電路的檢測,還可以進行集成晶元生產、裝配等等,僅此就不難窺見微細加工誘人的魅力。
發達工業國家對微細加工的研究開發十分重視,投入了大量的人力、物力、財力,一些有遠見的著名大學和公司也加入了這一行列。中國在這方面也做了大量的研究工作,有理由認為在21世紀,微細加工一定會像微電子技術一樣,給整個世界帶來巨大的變化和深刻的影響。
對於模具工業,由於衝壓零件的微型化及精度要求的不斷提高,給模具技術提出了更高的要求。原因是微零件比傳統的零件成形要困難得多,其理由是:①零件越小,表面積與體積比迅速增大;②工件與工具間的粘著力,表面張力等顯著增大;③晶粒尺度的影響顯著,不再是各向同性的均勻連續體;④工件表面存儲潤滑劑相對困難。微細衝壓的一個重要方面是沖小孔,譬如微型機械、微型儀器儀錶中就有很多需要衝壓的小孔。故研究小孔衝壓應是微細衝壓的一個極其重要的問題。沖小孔的研究著重於:一是如何減小沖床尺寸;二是如何增大微小凸模的強度和剛度(這方面除了涉及到製作的材料及加工的技術外,最常用的便是增加微小凸模的導向及保護等)。儘管在沖小孔上需要研究的問題還很多,但也取得了不少可喜的成績。有資料表明國外已經開發的微衝壓機床長111mm,寬62mm,高170mm,裝有一個交流伺服電機,可產生3kN的壓力。該壓力機床裝有連續衝壓模,能實現沖裁和彎曲等。
日本東京大學利用一種WFDG技術製作了微衝壓加工的沖頭與沖模,利用該模具進行微細衝壓,可在50μm厚的聚醯胺塑料板上衝出寬為40μm的非圓截面微孔。在超薄壁金屬筒形件拉深方面,清華大學有了良好的開端。超薄壁拉深技術的關鍵是要有高精度的成形機。他們在壁厚為0。001mm~0。1mm的超薄壁金屬圓筒成形中,研製出一台有微機控制功能的精密成形試驗機,使沖頭與凹模在加工過程中對中精度達到1μm,有效地解決了超薄壁拉深中易出現起皺與斷裂而不能正常操作的難題。利用該機對初始壁厚為0。3mm的黃銅和純鋁進行一系列變薄拉深加工,加工出內徑為16mm,壁厚為0。015mm~0。08mm,長度為30mm的一系列超薄壁金屬圓筒。經檢測,成形后的超薄壁筒壁厚差小於2μm,表面粗糙度Ra0。057μm,從而大大地提升了應用該超薄壁圓筒儀器儀錶的精度,相應地也提升了安裝該儀器儀錶整機的性能。
智能化衝壓
板料衝壓從手工操作到半機械化、機械化、自動化操作,均是衝壓發展到每個階段的標誌,而今板料衝壓又進入到了智能化階段,因此,可以說智能化衝壓是板料衝壓技術發展的必然趨勢。板料成形智能化研究起源於20世紀80年代初的美國,繼后,日本塑性加工界也開始板料智能化研究。該項技術研究之初的十餘年間,全部力量集中於彎曲回彈的成形控制,直至1990年後該項技術的研究才擴展到筒形零件的拉深變形,進而再擴展至汽車覆蓋件成形、級進模智能成形等。所謂智能化衝壓,乃是控制論、資訊理論、數理邏輯、優化理論、計算機科學與板料成形理論有機相結合而產生的綜合性技術。板料智能化是衝壓成形過程自動化及柔性化加工系統等新技術的更高階段。其令人讚歎之處是能根據被加工對象的特性,利用易於監控的物理量,在線識別材料的性能參數和預測最優的工藝參數,並自動以最優的工藝參數完成板料的衝壓。這就是典型的板料成形智能化控制的四要素:實時監控、在線識別、在線預測、實時控制加工。智能衝壓從某種意義上說,其實是人們對衝壓本質認識的一次革命。它避開了過去那種對衝壓原理的無止境探求,轉而模擬人腦來處理那些在衝壓中實實在在發生的事情。它不是從基本原理出發,而是以事實和數據作為依據,來實現對過程的優化控制。智能化控制的當然是最優的工藝參數,故最優的工藝參數確定是智能化控制的關鍵所在。所謂最優工藝參數,就是在滿足各種臨界條件的前提下所能夠採用的最為合理的工藝參數。要實現最優的工藝參數的在線預測,就必須對成形過程的各種臨界條件有明確的認識,並能夠給出定量的準確描述,在此基礎上才能夠確定智能化的控制。而定量描述的精度又決定著智能化系統的識別精度和預測精度。這就表明系統的識別精度、預測精度和控制精度均依賴於定量描述精度的提高,故要不斷予以修改、提高。且檢測精度、識別精度、預測精度和監控精度系統本身也要不斷完善提高。這樣,智能化衝壓才能達到應有的水平。有關研究表明在拉深過程的智能化控制中,最優工藝參數的預測最終歸結為壓邊力變化規律的確定,而壓邊力的控制又基於壓邊力的預測研究。預測拉深成形壓邊力的傳統方法主要有兩種:實驗法和理論計演演算法。近年來又把人工神經網路和模糊論等人工智慧理論引入壓邊力最佳控制曲線的預測研究中,目前變壓邊力控制技術已成為學術界和工業界的一個研究熱點。而壓邊力變化規律的理論根據就是確定起皺或破裂的臨界條件,可見拉深中法蘭起皺和破裂的臨界條件的正確確定不可不重視。進一步研究還表明,對錐形件拉深而言,法蘭起皺區幾乎被側壁起皺區所包圍,故克服了側壁起皺同時也就克服了法蘭起皺,所以對錐形件拉深來說,其主要矛盾集中於工件破裂和側壁起皺。故其壓邊力大小範圍要控制在側壁不起皺(最小極限)和側壁不破裂最大極限)之間。
綠色衝壓
綠色製造是一個綜合考慮環境影響與資源效率的現代製造模式,而綠色衝壓亦是如此,實質上就是人類可持續發展戰略在現代衝壓中的具體體現。它應包括在模具設計,製造、維修及生產應用等各個方面。
1、綠色設計所謂綠色設計即在模具設計階段就將環境保護和減小資源消耗等措施納入產品設計中,將可拆卸性、可回收性、可製造性等作為設計目標并行考慮並保證產品功能、質量壽命和經濟性。隨著模具工業的發展,對金屬板料成形質量和模具設計效率要求越來越高,傳統的基於經驗的設計方法已無法適應現代工業的發展。近年來,用有限元法對板料成形過程進行計算機數值模擬,是模具設計領域的一場革命。用計算機數值模擬能獲得成形過程中工件的位移、應力和應變分佈。通過觀察位移后工件變形形狀能預測可能發生的起皺;根椐離散點上的主應變值在板料成形極限曲線上的位置或利用損傷力學模型進行分析,可以預測成形過程中可能發生的破裂;將工件所受外力或被切除部分的約束力解除,可對回彈過程進行模擬,得到工件回彈后的形狀和殘餘應力的分佈。這一切,就為優化衝壓工藝和模具設計提供了科學依據,是真正意義上的綠色模具設計。
2綠色製造在模具製造中,應採用綠色製造。現在有一種激光再製造技術,它是以適當的合金粉末為材料,在具有零件原形CAD/CAM軟體支持下,採用計算機控制激光頭修復模具。具體過程是當送粉機和加工機床按指定空間軌跡運動,光束輻射與粉末輸送同步,使修復部位逐步熔敷,最後生成與原形零件近似的三維體,且其性能可以達到甚至超過原基材水平,這種方法在沖模修復尤其是在覆蓋件沖模修復中用途最廣。由於該項技術不以消耗大量自然資源為目標,故稱為綠色製造。此外,在衝壓生產中應盡量減少衝壓工藝廢料及結構廢料,最大限度地利用材料和最低限度地產生廢棄物。減少工藝廢料,就是通過優化排樣來解決,例如採用對排、交叉排樣等方法,還可以採用少無廢料排樣方法,以大幅度提高材料利用率。所謂優化排樣就是要解決兩個問題:一是如何將它表示成數學模型;二是如何根據數學模型儘快求出最優解,其關鍵就是演演算法問題。現代優化技術已發展到智能優化演演算法,主要包括人工神經網路、遺傳演演算法、模擬退火、禁忌搜索等。可以相信優化排樣將會有一個突破性進展,對結構廢料多的工件可採用套裁方法,從而能達到廢物利用,變廢為寶。
此外,還可以通過改產品結構的方法來加以解決也不是完全不可能的。對於套裁,人人皆知的有大墊片套裁中墊片,中墊片再套裁小墊片等。
高強度鋼衝壓
當今高強鋼、超高強鋼很好的實現了車輛的輕量化,提高了車輛的碰撞強度和安全性能,因此成為車用鋼材的重要發展方向。但隨著板料強度的提高,傳統的冷衝壓工藝在成型過程中容易產生破裂現象,無法滿足高強度鋼板的加工工藝要求。在無法滿足成型條件的情況下,目前國際上逐漸研究超高強度鋼板的熱衝壓成形技術。該技術是綜合了成形、傳熱以及組織相變的一種新工藝,主要是利用高溫奧氏體狀態下,板料的塑性增加,屈服強度降低的特點,通過模具進行成形的工藝。但是熱成型需要對工藝條件、金屬相變、CAE分析技術進行深入研究,目前該技術被國外廠商壟斷,國內發展緩慢。
當材料被衝壓成形時,會變硬。不同的鋼材,變硬的程度不同,一般高強度低合金鋼只略有3KSI增加,不到10%。注意:雙相鋼的屈服強度有20KSI增加,增加了40%多!金屬在成形過程中,會變得完全不同,完全不像衝壓加工開始之前。這些鋼材在受力后,屈服強度增加很多。材料較高的屈服應力加上加工硬化,等於流動應力的大大增加。----這會引起需要更多的噸位來製作部件----它會使金屬的變形溫度增加(可能會燃燒或破壞不恰當的潤滑劑),硬點會增加模具磨損----塗層可能會於事無補或無法持續到和預期的時間一樣長。綜上所述,高強鋼成形的高壓力要求、回彈的增加、加工硬度的增加、高成型溫度下的操作對模具及潤滑都提出了挑戰。
過去在生產深沖或者重沖工件,大家都認為耐壓型(EP)潤滑油是保護模具的最好選擇。硫和氯EP添加劑被混合到純油中來提高模具壽命已經有很長的歷史了。但是隨著新金屬--高強度鋼的出現,環保要求的嚴格,EP油基潤滑油的價值已經減少,甚至失去市場。
在高溫下高強度鋼的成型,EP油基潤滑油失去了它的性能,無法在極溫應用中提供物理的模具保護隔膜。而極溫型的IRMCO高固體聚合物潤滑劑則可以提供必要的保護。隨著金屬在衝壓模具中變形,溫度不斷升高,EP油基潤滑油都會變薄,有些情況下會達到閃點或者燒著(冒煙)。IRMCO高分子聚合物潤滑劑一般開始噴上去時稠度低得多。隨著成形過程中溫度的上升,會變得更稠更堅韌。實際上高分子聚合物極溫潤滑劑都有“熱尋性”而且會粘到金屬上,形成一個可以降低摩擦的隔膜。這個保護屏障可以允許工件延展,在最高要求的工件成型時沒有破裂和粘接,以此來控制摩擦和金屬流動。有效的保護了模具,延長了模具使用壽命,提高了衝壓的強度。
主要應用
由於衝壓具有如此優越性,衝壓加工在國民經濟各個領域應用範圍相當廣泛。例如,在宇航,航空,軍工,機械,農機,電子,信息,鐵道,郵電,交通,化工,醫療器具,日用電器及輕工等部門裡都有衝壓加工。不但整個產業界都用到它,而且每個人都直接與衝壓產品發生聯繫。像飛機,火車,汽車,拖拉機上就有許多大,中,小型衝壓件。小轎車的車身,車架及車圈等零部件都是衝壓加工出來的。據有關調查統計,自行車,縫紉機,手錶里有80%是衝壓件;電視機,收錄機,攝像機里有90%是衝壓件;還有食品金屬罐殼,鋼精鍋爐,搪瓷盆碗及不鏽鋼餐具,全都是使用模具的衝壓加工產品;就連電腦的硬體中也缺少不了衝壓件。
但是,衝壓加工所使用的模具一般具有專用性,有時一個複雜零件需要數套模具才能加工成形,且模具製造的精度高,技術要求高,是技術密集形產品。所以,只有在衝壓件生產批量較大的情況下,衝壓加工的優點才能充分體現,從而獲得較好的經濟效益的。
當然,衝壓加工也存在著一些問題和缺點。主要表現在衝壓加工時產生的噪音和振動兩種公害,而且操作者的安全事故時有發生。不過,這些問題並不完全是由於衝壓加工工藝及模具本身帶來的,而主要是由於傳統的衝壓設備及落後的手工操作造成的。隨著科學技術的進步,特別是計算機技術的發展,隨著機電一體化技術的進步,這些問題一定會儘快得到完善的解決。