分子蒸餾
在高真空下操作的蒸餾方法
分子蒸餾是一種在高真空下操作的蒸餾方法,這時蒸氣分子的平均自由程大於蒸發表面與冷凝表面之間的距離,從而可利用料液中各組分蒸發速率的差異,對液體混合物進行分離。
在一定溫度下,壓力越低,氣體分子的平均自由程越大。當蒸發空間的壓力很低(10~10mmHg),且使冷凝表面靠近蒸發表面,其間的垂直距離小於氣體分子的平均自由程時,從蒸發表面汽化的蒸氣分子,可以不與其他分子碰撞,直接到達冷凝表面而冷凝。
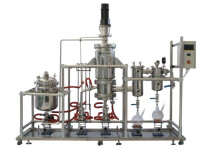
分子蒸餾
當液體混合物沿加熱板流動並被加熱,輕、重分子會逸出液面而進入氣相,由於輕、重分子的自由程不同,因此,不同物質的分子從液面逸出后移動距離不同,若能恰當地設置一塊冷凝板,則輕分子達到冷凝板被冷凝排出,而重分子達不到冷凝板沿混合液排出。這樣,達到物質分離的目的。在沸騰的薄膜和冷凝面之間的壓差是蒸汽流向的驅動力,對於微小的壓力降就會引起蒸汽的流動。在1mbar下運行要求在沸騰面和冷凝面之間非常短的距離,基於這個原理製作的蒸餾器稱為短程蒸餾器。短程蒸餾器(分子蒸餾)有一個內置冷凝器在加熱面的對面,並使操作壓力降到0.001mbar。
短程蒸餾器是一個工作在1~0.001mbar壓力下熱分離技術過程,它較低的沸騰溫度,非常適合熱敏性、高沸點物。其基本構成:帶有加熱夾套的圓柱型筒體,轉子和內置冷凝器;在轉子的固定架上精確裝有刮膜器和防飛濺裝置。內置冷凝器位於蒸發器的中心,轉子在圓柱型筒體和冷凝器之間旋轉。
短程蒸餾器由外加熱的垂直圓筒體、位於它的中心冷凝器及在蒸餾器和冷凝器之間旋轉的刮膜器組成。
蒸餾過程是:物料從蒸發器的頂部加入,經轉子上的料液分佈器將其連續均勻地分佈在加熱面上,隨即刮膜器將料液刮成一層極薄、呈湍流狀的液膜,並以螺旋狀向下推進。在此過程中,從加熱面上逸出的輕分子,經過短的路線和幾乎未經碰撞就到內置冷凝器上冷凝成液,並沿冷凝器管流下,通過位於蒸發器底部的出料管排出;殘液即重分子在加熱區下的圓形通道中收集,再通過側面的出料管中流出。
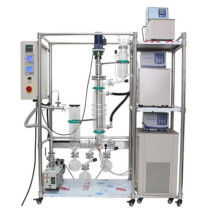
分子蒸餾
分子從液相主體向蒸發表面擴散
通常,液相中的擴散速度是控制分子蒸餾速度的主要因素,所以應盡量減薄液層厚度及強化液層的流動。
分子在液層表面上的自由蒸發
蒸發速度隨著溫度的升高而上升,但分離因素有時卻隨著溫度的升高而降低,所以,應以被加工物質的熱穩定性為前提,選擇經濟合理的蒸餾溫度。
分子從蒸發表面向冷凝面飛射
蒸氣分子從蒸發麵向冷凝面飛射的過程中,可能彼此相互碰撞,也可能和殘存於兩面之間的空氣分子發生碰撞。由於蒸發分子遠重於空氣分子,且大都具有相同的運動方向,所以它們自身碰撞對飛射方向和蒸發速度影響不大。而殘氣分子在兩面間呈雜亂無章的熱運動狀態,故殘氣分子數目的多少是影響飛射方向和蒸發速度的主要因素。
分子在冷凝面上冷凝
只要保證冷熱兩面間有足夠的溫度差(一般為70~100℃),冷凝表面的形式合理且光滑則認為冷凝步驟可以在瞬間完成,所以選擇合理冷凝器的形式相當重要。
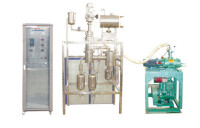
分子蒸餾
2、在飽和壓力下,蒸汽分子的平均自由程長度必須與蒸發器和冷凝器表面之間距離具有相同的數量級。在這此理想的條件下,蒸發在沒有任何障礙的情況下從殘餘氣體分子中發生。所有蒸汽分子在沒有遇到其它分子和返回到液體過程中到達冷凝器表面。蒸發速度在所處的溫度下達到可能的最大值。蒸發速度與壓力成正比,因而,分子蒸餾的餾出液量相對比較小。
在大中型短程蒸餾中,冷凝器和加熱表面之間的距離約為20~50mm,殘餘氣體的壓力為10-3mbar時,殘餘氣體分子的平均自由程長度約為2倍長。短程蒸餾器完全能滿足分子蒸餾的所有必要條件。
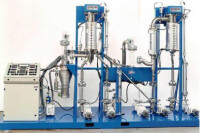
分子蒸餾
2、普通蒸餾是蒸發與冷凝的可逆過程,液相和氣相間可以形成相平衡狀態;而分子蒸餾過程中,從蒸發表面逸出的分子直接飛射到冷凝面上,中間不與其它分子發生碰撞,理論上沒有返回蒸發麵的可能性,所以,分子蒸餾過程是不可逆的。
3、普通蒸餾有鼓泡、沸騰現象;分子蒸餾過程是液層表面上的自由蒸發,沒有鼓泡現象。
4、表示普通蒸餾分離能力的分離因素與組元的蒸汽壓之比有關,表示分子蒸餾分離能力的分離因素則與組元的蒸汽壓和分子量之比有關,並可由相對蒸發速度求出。

分子蒸餾
2.蒸餾真空度高,分子蒸餾裝置其內部可以獲得很高的真空度,通常分子蒸餾在很低的壓強下進行操作,因此物料不易氧化受損。
3.蒸餾液膜薄,傳熱效率高。
4.物料受熱時間短,受加熱的液面與加冷凝面之間的距離小於輕分子的平均自由程,所以由液面逸出的輕分子幾乎未經碰撞就達到冷凝面。因此,蒸餾物料受熱時間短,在蒸餾溫度下停留時間一般幾秒至幾十秒之間,減少了物料熱分解的機會。
5.分離程度更高,分子蒸餾能分離常規不易分開的物質
6.沒有沸騰鼓泡現象,分子蒸餾是液層表面上的自由蒸發,在低壓力下進行,液體中無溶解的空氣,因此在蒸餾過程中不能使整個液體沸騰,沒有鼓泡現象。
7.無毒、無害、無污染、無殘留,可得到純凈安全的產物,且操作工藝簡單,設備少。分子蒸餾技術能分離常規蒸餾不易分離的物質。
8.分子蒸餾設備價格昂貴,分子蒸餾裝置必須保證體系壓力達到的高真空度,對材料密封要求較高,且蒸發麵和冷凝面之間的距離要適中,設備加工難度大,造價高。
9.產品耗能小,由於分子蒸餾整個分離過熱損失少,且由於分子蒸餾裝置獨特的結構形式,內部壓強極低,內部阻力遠比常規蒸餾小,因而可大大節省能耗。
從分子蒸餾技術以上的特點可知,它在實際工業化的應用中比常規蒸餾技術具有以下明顯的優勢:
(1)對於高沸點、熱敏及易氧化物料的分離,分子蒸餾提供了最佳分離方法。因為分子蒸餾在遠低於物料沸點的溫度下操作,而且物料停留時間短;
(2)分子蒸餾可極有效地脫除液體中的物質如有機溶劑、臭味等,這對於採用溶劑萃取后液體的脫溶是非常有效的方法;
(3)分子蒸餾可有選擇地蒸出目的產物,去除其它雜質,通過多級分離可同時分離2種以上的物質;
(4)分子蒸餾的分餾過程是物理過程,因而可很好地保護被分離物質不受污染和侵害。
一套完整的分子蒸餾設備主要包括:分子蒸發器、脫氣系統、進料系統、加熱系統、冷卻真空系統和控制系統。分子蒸餾裝置的核心部分是分子蒸發器,其種類主要有3種:(1)降膜式:為早期形式,結構簡單,但由於液膜厚,效率差,當今世界各國很少採用;(2)刮膜式:形成的液膜薄,分離效率高,但較降膜式結構複雜;(3)離心式:離心力成膜,膜薄,蒸發效率高,但結構複雜,真空密封較難,設備的製造成本高。為提高分離效率,往往需要採用多級串聯使用而實現不同物質的多級分離。
降膜式分子蒸餾器
為早期形式,結構簡單,但由於液膜厚,效率差,當今世界各國很少採用。該裝置是採取重力使蒸發麵上的物料變為液膜降下的方式。將物料加熱,蒸發物就可在相對方向的冷凝面上凝縮。降膜式裝置為早期形式,結構簡單,在蒸發麵上形成的液膜較厚,效率差,現在各國很少採用。
刮膜式分子蒸餾裝置
我國在80年代末才開展刮膜式分子蒸餾裝置和工藝應用研究。該裝置形成的液膜薄,分離效率高,但較降膜式結構複雜。它採取重力使蒸發麵上的物料變為液膜降下的方式,但為了使蒸發麵上的液膜厚度小且分佈均勻,在蒸餾器中設置了一硬碳或聚四氟乙烯制的轉動刮板。該刮板不但可以使下流液層得到充分攪拌,還可以加快蒸發麵液層的更新,從而強化了物料的傳熱和傳質過程。其優點是:液膜厚度小,並且沿蒸發表面流動;被蒸餾物料在操作溫度下停留時間短,熱分解的危險性較小,蒸餾過程可以連續進行,生產能力大。缺點是:液體分配裝置難以完善,很難保證所有的蒸發表面都被液膜均勻覆蓋;液體流動時常發生翻滾現象,所產生的霧沫也常濺到冷凝面上。但由於該裝置結構相對簡單,價格相對低廉,現在的實驗室及工業生產中,大部分都採用該裝置。
刮板式分子蒸餾裝置
(Wiped-FilmMolecular Still)
刮板式技術(Wiped-Film Style)採用的是Smith式45°對角斜槽刮板,這些斜槽會促使物料圍繞蒸餾器壁向下運動,通過可控的刮板轉動就能夠提供一個程度很高的薄膜混合,使物料產生有效的微小的活躍運動,(而非被動地將物料滾輾在蒸餾器壁上,)這樣就實現了最短的而且可控的物料駐留時間,和可控的薄膜厚度,從而能夠達到最佳的熱能傳導、物質傳輸和分離效率。刮板式分子蒸餾設備通過一個平緩的過程,進料液體流經一個被加熱的圓柱形真空室,利用進料液體薄膜的刮擦作用,將易揮發的成分從不易揮發的成分中分離出來。進料液體暴露給加熱壁的時間非常短暫(僅幾秒鐘),這部分歸因於帶縫隙的刮板設計,它迫使液體向下運動,並且滯留時間、薄膜厚度和流動特性都受到嚴格的控制,非常適合熱敏性物質的分離應用。另外,這種帶斜槽的刮板不會將物料甩離蒸餾器壁,污染已被分離出來的輕組分。與傳統的柱式蒸餾設備、降膜式蒸餾設備、旋轉蒸發器和其他分離設備比較,刮板式蒸餾設備被公認為要出色得多。
離心式分子蒸餾裝置
離心式分子蒸餾裝置離心力成膜,膜薄,蒸發效率高。但結構複雜,製造及操作難度大。該裝置將物料送到高速旋轉的轉盤中央,並在旋轉面擴展形成薄膜,同時加熱蒸發,使之與對面的冷凝面凝縮,該裝置是目前較為理想的分子蒸餾裝置。但與其它兩種裝置相比,要求有高速旋轉的轉盤,又需要較高的真空密封技術。離心式分子蒸餾器與刮膜式分子蒸餾器相比具有以下優點:由於轉盤高速旋轉,可得到極薄的液膜且液膜分佈更均勻,蒸發速率和分離效率更好;物料在蒸發麵上的受熱時間更短,降低了熱敏物質熱分解的危險;物料的處理量更大,更適合工業上的連續生產。
1.北京新特科技發展公司分子蒸餾設備,北京新特科技發展公司是由北京化工大學創辦的全資高科技公司,成立十幾年來,所開發的分子蒸餾(短程蒸餾)技術及工業化裝置得到了迅猛發展,該項目於1998年獲國家石化局(原化工部)科技進步一等獎,同年被國家科技部列為全國重點推廣項目,另外完成“863”國家項目一項,並獲得2001年度國家科技進步二等獎。被專家們譽為“國內領先、國際先進,是產、學、研相結合的典範”。
2.美國POPE科學公司成立於1963年,(前身是AUTHOR SMITH公司,世界最早的從事分子蒸餾技術開發和設備製造的先驅)。是專業從事蒸餾、精餾設備的製造廠家,產品涵蓋實驗室、中試和工業生產用設備。Pope採用的刮板式工藝(Wiped-Film Style)的特點是:短暫的進料液體滯留時間、憑藉高真空性能的充分降溫、最佳的混合效率,以及最佳的物質和熱傳導。這種高效的熱分離技術的結果是:最小的產品降解和最高的產品質量。物料暴露給加熱壁的時間非常短(僅幾秒鐘),這部分歸因於帶縫隙的刮板設計,它迫使進料液體向下運動,並且滯留時間、薄膜厚度和流動特性都受到嚴格控制。
3.德國NGW公司分子蒸餾設備,又稱短程蒸餾,英文名稱為:short-pathevaporator,其操作壓力範圍為:0.001-1000mbar。採用兩級回收瓶,真空的密封性能更好。在蒸餾的同時,重相和輕相組份均能連續取樣進行檢測,取樣次數可以達到10次以上。在0.001mar的真空條件下進行的薄膜蒸發過程稱為短程蒸發過程,蒸發器中部保證集成冷凝器,在小於或等於0.001mbar的真空條件下進行的薄膜蒸發過程統稱為分子蒸餾。分子蒸餾能達到0.001mbar的超低真空度,這是因為蒸發麵和冷凝面的距離小於或等於被分離物料的分子平均自由程,而這是傳統類型的蒸餾無法達到的。
4.德國威帝恩公司為真空蒸餾設備的專業生產廠家,提供刮膜蒸發和短程/分子蒸餾設備。產品從小試,中試,到大型生產設備。世界上最大的短程蒸餾設備即為VTA提供。這些設備專門用於熱敏物質和高沸點物質的蒸餾分離和提純,短程蒸餾真空度可達0.001毫巴,使物質的沸點降低,蒸餾的持續時間縮短,避免對蒸餾產品的破壞。
5.德國UIC公司成立於1950年,UIC公司專攻於蒸餾設備的設計和交鑰匙工程,為客戶的各種需求提供最佳解決方案,並且有世界上最小的實驗研究用的短程蒸餾設備。採用上部進料,物料從進料管進入后加到物料分配盤上,物料盤旋轉離心分配物料到蒸發器四周側壁,不會出現結焦現象。全加熱型蒸發器為模塊化設計,具有三個獨立的加熱區域(蒸發區域、重組分出料區域、餾分出料區域和內置冷凝器)以保證物料在整個蒸餾過程中具有良好的流動性。UIC設備具有一次離心成膜+一次機械成膜,膜更均勻,真空度可達0.001毫巴。
食品工業
1、單甘酯的生產
分子蒸餾技術廣泛應用於食品工業,主要用於混合油脂的分離。可得到w(單脂肪酸甘油酯)>90%的高純度產品。從蒸餾液面上將單甘酯分子蒸發出來后立即進行冷卻,實現分離。利用分子蒸餾可將未反應的甘油、單甘酯依次分離出來。單甘酯即甘油一酸酯,它是重要的食品乳化劑。單甘酯的用量目前占食品乳化劑用量的三分之二。在商品中它可起到乳化、起酥、蓬鬆、保鮮等作用,可作為餅乾、麵包、糕點、糖果等專用食品添加劑。單甘酯可採用脂肪酸與甘油的酯化反應和油脂與甘油的醇解反應兩種工藝製取,其原料為各種油脂、脂肪酸和甘油。採用酯化反應或醇解反應合成的單甘酯,通常都含有一定數量的雙甘酯和三甘酯,通常w(單甘酯)=40%~50%,採用分子蒸餾技術可以得到w(單甘酯)>90%的高純度產品。此法是目前工業上高純度單甘酯生產方法中最常用和最有效的方法,所得到的單甘酯達到食品級要求。分子蒸餾單甘酯產品以質取勝,逐漸代替了純度低、色澤深的普通單甘酯,市場前景樂觀,開發分子蒸餾單甘酯可為企業帶來豐厚的利潤。
2、魚油的精製
從動物中提取天然產物,也廣泛採取分子蒸餾技術,如精製魚油等[8]。魚油中富含全順式高度不飽和脂肪酸二十碳五烯酸(簡稱EPA)和二十二碳六烯酸(簡稱DHA),此成分具有很好的生理活性,不僅具有降血脂、降血壓、抑制血小板凝集、降低血液黏度等作用,而且還具有抗炎、抗癌、提高免疫能力等作用,被認為是很有潛力的天然藥物和功能食品。EPA、DHA主要從海產魚油中提取,傳統分離方法是採用尿素包合沉澱法[9]和冷凍法[10]。運用尿素包合沉澱法可以有效地脫除產品中飽和的及低不飽和的脂肪酸組分,提高產品中DHA和EPA的含量,但由於很難將其他高不飽和脂肪酸與DHA和EPA分離,只能使w(DHA+EPA)<80%。而且產品色澤重,腥味大,過氧化值高,還需進一步脫色除臭后才能製成產品,回收率僅為16%;由於物料中的雜質脂肪酸的平均自由程同EPA、DHA乙酯相近,分子蒸餾法儘管只能使w(EPA+DHA)=725%,但回收率可達到70%,產品的色澤好、氣味純正、過氧化值低,而且可以將混合物分割成DHA與EPA不同含量比例的產品。因此分子蒸餾法不失為分離純化EPA、DHA一種有效方法。
3、油脂脫酸
在油脂的生產過程中,由於從油料中提取的毛油中含有一定量的遊離脂肪酸,從而影響油脂的色澤和風味以及保質期。傳統工業生產中化學鹼煉或物理蒸餾的脫酸方法有一定的局限性。由於油品酸值高,化學鹼煉工藝中添加的鹼量大,鹼在與遊離脂肪酸的中和過程中,也皂化了大量中性油使得精鍊得率偏低;物理精鍊用水蒸氣氣提脫酸,油脂需要在較長時間的高溫下處理,影響油脂的品質,一些有效成分會隨水蒸氣溢出,從而會降低保健營養價值。
馬傳國等在對高酸值花椒籽油脫酸的研究中,利用分子蒸餾對不同酸值的花椒籽油進行脫酸,能獲得比較高的輕(脂肪酸)、重(油脂)餾分得率,這是目前化學鹼煉或物理蒸餾等工藝所不能達到的。對酸值為28mgKOH/g和412mgKOH/g的高酸值油脂用分子蒸餾法脫酸后,油脂的酸值分別下降到26mgKOH/g和38mgKOH/g,油脂的得率分別為86%和809%,中性油脂基本沒有損失。所以利用分子蒸餾技術對高酸值油脂脫酸具有良好的效果,具有廣闊的應用前景。
4、高碳醇的精製
高碳脂肪醇是指二十碳以上的直鏈飽和醇,具有多種生理活性。目前最受關注的是二十八烷醇和三十烷醇,它們具有抗疲勞、降血脂、護肝、美容等功效,可做營養保健劑的添加劑,某些國家也作為降血脂藥物,發展前景看好。
精製高碳醇,其工藝十分複雜,需要經過醇相皂化,多種及多次溶劑浸提,然後用多次柱層析分離,最後還要採用溶劑結晶才能得到一定純度的產品。日本採用蠟脂皂化、溶劑提取、真空分餾的方法得到w(高碳醇)=10%~30%的產品。而劉元法等對米糠蠟中二十八烷醇精製研究中得出,經多級分子蒸餾后,可得到w(高碳醇)=80%的產品。張相年等利用富含二十八烷醇的長鏈脂肪酸高碳醇酯,還原得到二十八烷醇。即以蟲蠟為原料,在乙醚中加氫化鋁鋰(AlLiH4),在70~80℃還原25h得到高碳醇混合物,經分子蒸餾純化,高碳醇純度達到w(高碳醇)=96%,其中w(二十八烷醇)=167%。利用分子蒸餾技術精製高碳醇,工藝簡單,操作安全可靠,產品質量高。
在精細化工中的應用
(二)在精細化工中的應用
分子蒸餾技術在精細化工行業中可用於碳氫化合物、原油及類似物的分離;表面活性劑的提純及化工中間體的製備;羊毛脂及其衍生物的脫臭、脫色;塑料增塑劑、穩定劑的精製以及硅油、石蠟油、高級潤滑油的精製等。在天然產物的分離上,許多芳香油的精製提純,都應用分子蒸餾而獲得高品質精油。
1、芳香油的提純
隨著日用化工、輕工、製藥等行業和對外貿易的迅速發展,對天然精油的需求量不斷增加。精油來自芳香植物,從芳香植物中提取精油的方法有:水蒸氣蒸餾法、浸提法、壓榨法和吸附法。精油的主要成分大都是醛、酮、醇類。且大部分都是萜類,這些化合物沸點高,屬熱敏性物質,受熱時很不穩定。因此,在傳統的蒸餾過程中,因長時間受熱會使分子結構發生改變而使油的品質下降。
陸韓濤等用分子蒸餾的方法對山蒼子油、姜樟油、廣藿香油等幾種芳香油進行了提純,結果見表3。結果表明,分子蒸餾技術是提純精油的一種有效的方法,可將芳香油中的某一主要成分進行濃縮,併除去異臭和帶色雜質,提高其純度。由於此過程是在高真空和較低溫度下進行,物料受熱時間極短,因此保證了精油的質量,尤其是對高沸點和熱敏性成分的芳香油,更顯示了其優越性。
此外,利用分子蒸餾技術分離毛葉木姜子果油中的檸檬醛可得到w(檸檬醛)=95%,產率53%的產品;對乾薑的有效成分的分離中,通過調節不同的蒸餾溫度和真空度可得到不同的有效成分種類及其相對含量,調節適宜的蒸餾溫度和真空度可獲得相對含量較高的有效成分。
2、高聚物中間體的純化
在由單體合成聚合物的過程中,總會殘留過量的單體物質,併產生一些不需要的小分子聚合體,這些雜質嚴重影響產品的質量。傳統清除單體物質及小分子聚合體的方法是採用真空蒸餾,這種方法操作溫度較高。由於高聚物一般都是熱敏性物質,因此溫度一高,高聚物就容易歧化、縮合或分解。例如,對聚醯胺樹脂中的二聚體進行純化,採用常規蒸餾方法只能使w(二聚體聚醯胺樹脂)=75%~87%,採用分子蒸餾技術則可以使w(二聚體聚醯胺樹脂)=90%~95%。在對酚醛樹脂和聚氨酯的純化中,採用分子蒸餾的方法可以使酚醛樹脂中的單體酚含量脫除到w(單體酚)<0.01%,使w(二異氰酸酯單體)<0.1%。分子蒸餾技術能極好地保護高聚物產品的品質,提高產品純度,簡化工藝,降低成本。
3、羊毛脂的提取
羊毛脂及其衍生物廣泛應用於化妝品。羊毛脂成分複雜,主要含酯、遊離醇、遊離酸和烴。這些組分相對分子質量較大,沸點高,具熱敏性。用分子蒸餾技術將各組分進行分離,對不同成分進行物理和化學方法改性,可得到聚氧乙烯羊毛脂、乙醯羊毛脂、羊毛酸、異丙酯及羊毛聚氧乙烯脂等性能優良的羊毛脂系列產品。
醫藥工業
利用分子蒸餾技術,在醫藥工業中可提取天然維生素A、維生素E;製取氨基酸及葡萄糖的衍生物;以及胡蘿蔔和類胡蘿蔔素等。現以維生素E為例:天然維生素E在自然界中廣泛存在於植物油種子中,特別是大豆、玉米胚芽、棉籽、菜籽、葵花籽、米胚芽中含有大量的維生素E。由於維生素E是脂溶性維生素,因此在油料取油過程中它隨油一起被提取出來。脫臭是油脂精練過程中的一道重要工序,餾出物是脫臭工序的副產品,主要成分是遊離脂肪酸和甘油以及由它們的氧化產物分解得到的揮發性醛、酮碳氫類化合物,維生素E等。從脫臭餾出物中提取維生素E,就是要將餾出物中非維生素E成分分離出去,以提高餾出物中維生素E的含量。曹國峰等將脫臭餾出物先進行甲脂化,經冷凍、過濾後分離出甾醇,經減壓真空蒸餾后再在220~240℃、壓力為10-3~10-1Pa的高真空條件下進行分子蒸餾,可得到w(天然維生素E)=50%~70%的產品。採取色譜法、離子交換、溶劑萃取等可對其進一步精製。此外,在分子生物學領域中,可以將分子蒸餾技術作為生物研究的一種前處理技術,以保存原有組織的生物活性和製備生物樣品等。
綜上所述,分子蒸餾技術作為一種特殊的新型分離技術,主要應用於高沸點、熱敏性物料的提純分離。實踐證明,此技術不但科技含量高,而且應用範圍廣,是一項工業化應用前景十分廣闊的高新技術。它在天然藥物活性成分及單體提取和純化過程的應用還剛剛開始,尚有很多問題需要進一步探索和研究。